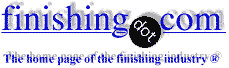
-----
Solutions to Problems in nickel barrel plating
DEAR SIR.
I HAVE A PROBLEM WITH NICKEL BRIGHT PLATING IN ZINC DIE CASTING.
WE GIVE NICKEL BRIGHT TO ZINC DIE CASTING PULL AND WE GET A DARK NICKEL FINISHING THEN WE GIVE NICKEL BRIGHT TO STEEL SCREW AND WE GET A BEAUTIFUL FINISH. (FOR INSTANCE WE GIVE COPPER PLATING TO ZINC PULL BEFORE GIVE NICKEL PLATING.)
WE WISH TO KNOW IF THE SAME SOLUTIONS CAN BE USED IN BOTH PROCESS OR WE NEED TO PREPARE A SPECIAL BATH FOR ZINC DIE CASTING ?
BEST REGARDS
locks and hardware - Monterrey, Mexico
1996
As you say, Ricardo, zinc die-castings require copper plating in a copper cyanide solution before plating with nickel. But after the zinc is covered with copper you should be able to plate it with the same nickel bath you use for plating onto steel.
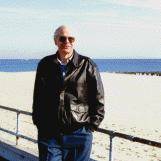
Ted Mooney, P.E.
Striving to live Aloha
(Ted can offer longterm or instant help)
finishing.com - Pine Beach, New Jersey
Although zinc die castings can be plated out of the same nickel bath as other substrates, isn't it recommended to take precautions (low current dummying of the bath) to avoid a build-up of zinc metal? Parts with a complicated geometry will still have exposed zinc where the copper does not throw.
Keith Rosenblumplating shop - St. Paul, Minnesota
1996
After copper plating and rinsing you should go back through your activation acid solution and closely observe your parts for any gassing. If you see gassing you need to deposit additional copper prior to nickel plating.
Paul D. Peterson- Rock Hill, South Carolina
1996
DEAR SIR.
IN MARCH I SENT A QUESTION ABOUT OF NICKEL BRIGHT PLATING IN A ZINC DIE CASTING PULL AND KNOB. WE HAVE A PROBLEM BECAUSE THE PIECES ARE LIKE A BURN AND HAS BUBBLE IN THE NICKEL PLATING.
FIRST OF ALL I AM GOING TO EXPLAIN OUR PROCESS: THE FIRST STEP WE GIVE A ALKALINE COPPER PLATING FOR THE PIECES IN A BARREL PLATING. AND THE WE GIVE A WATER RINSE VERY WELL AND THE WE GIVE NICKEL PLATING IN THE SAME BARREL AND WHEN FINISH THIS STEP THE PIECES LOOKING LIKE BURN.
I WAS TALKING WITH SOME PERSONS AND THEY TOLD ME THAT THE PROBLEM IS THAT WE CAN NOT GIVE THE NICKEL PLATING IN BARREL. WHAT IS YOUR OPINION ABOUT THIS ? OR WE NNED TO GIVE ACID COPPER PLATING AFTER ALKALINE COPPER ?
BEST REGARDS
locks and hardware - Monterrey, Mexico
1996
Nickel plating can be done in a barrel; and I don't think that acid copper is required. Beyond that, I don't know why you are getting burning, nor what exactly is being done wrong that is causing the nickel to blister.
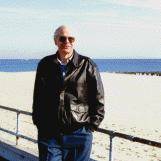
Ted Mooney, P.E.
Striving to live Aloha
(Ted can offer longterm or instant help)
finishing.com - Pine Beach, New Jersey
Burning of nickel is caused by high ph,low metal content in solution,low temperature,chromium contamination and low type I brightener.
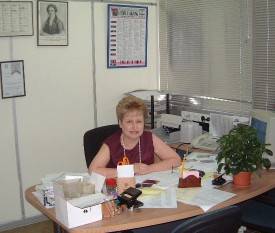

Sara Michaeli
Tel-Aviv-Yafo, Israel
1996
For Zinc Die Cast pieces:
1. Apply Alkaline Copper Plating for a period of 1 to 3 minutes. Free Cyanide should be in a range of 10 to 18 gr/L at 45 °C.
2. Neutralize the alkalinity of the piece using 10% Sulfuric Acid.
All the pieces coming out of this bath should result with a beautiful bright copper, ready for bright nickel plating.
Good luck!,
- Honduras
1996
1996
1. The same nickel bath can be used for any other base material after plating on zinc die castings with good plating practices.
2. Cyanide Copper has excellent throw and the problem of exposed zinc is never in low current density area but rather on the edges where peening or rubbing action in the barrel will break through the copper plate. As a rule, the smaller and lighter the part, the less copper required (.0002" thick) The heavier the part the more copper needed in some cases .001" thick. Just get every principle of rack plating out of your mind for zinc die castings.
3. You cannot go to an acid copper unless you have the required copper from an alkaline bath. Acid copper is more aggressive than a nickel bath.
4. Blistering can be of two types, casting or plating. Although not visible, the zinc surface first formed in casting is composed of zinc carbonate and zinc hydroxide. The movement of the molten zinc tends to laminate these salts during plating the stresses caused by the formation of the intermetallic zinc copper layer tends to loosen the lament and causes a blister. One can test for the cause by cutting and rolling over the blister and observing the back side under 20X mag. If the back side is crystalline and bright, it is from the casting. On the other hand, if is gray, smooth and dark, it is from plating and your copper strike should be checked.
Our company barrel plates 60 loads of zinc die cast with copper & nickel per day. We have never dummied our nickel plating baths for contaminants. Low levels of zinc and copper tend to be plated out during the process with no ill effects on the plate as long as these contaminates are low leveled. We do, however, carbon treat our tanks and do general maintenance on regular schedules.
Sincerely,
NEW BRUNSWICK PLATING

New Brunswick, New Jersey
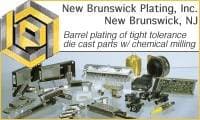
Nobody has said anything about cleaning prior to copper plating. We have found that cleaning in a hot immersion cleaner with the work in a stainless steel baskets is best for our operation. We also use oblique barrels with rheostats to control the speed of the barrels; this way the work does not bang around. We also change barrels from copper to nickel.You do not need acid copper. As for the burning, I would check your amperage and voltage. It is hard to make a call without seeing what you call burning. Again, cleaning is usually the problem for blistering.
Good luck,
- Rhode Island
1996
Ricardo,
Besides better or proper cleaning, Cyanide copper plating, Acid dipping etc recommended in previous letters, you should reduce the Barrel speed (revolutions per minute) in Copper plating and all rinses/acid dips prior to Nickel plating.
Copper is rather soft as well Zinc. If you rotate the barrel too fast (over 4 RPM) you abrade the corners and edges of the articles you plate, thus having exposed Zinc at that locations. Nickel will not plate there. It even may etch into the Zinc, causing burn-like black-grey appearance at surrounding areas. In case this areas are very small, they may be over-plated with nickel, but later blisters become visible.
regards,
- Hong Kong
1996
Dear Ricardo
We also experience blackening of low CD areas on the insides of our D connector hoods we also try barrel plating and no matter how much copper we lay down first the acid nickel always eats away the low cd ares and the high points on our castings . We will now modify our casting so that they don't have sharp edges in the low cd areas and we will ask the electro platers to start the current at a lower figure on the first lay down of copper so as to provide a harder copper surface before the acid nickel.
If you get brown blue gold discoloration in the nickel finish your electro plater is not cleaning out the nickel baths and they are contaminated with zinc and magnesium We are also lost for a solution
Best Regards
- Corby (City) Northampton (County)
1999
Q, A, or Comment on THIS thread -or- Start a NEW Thread