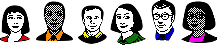
world gathers for metal finishing
Q&As since 1989
-----
Substituting copper plating for nickel plating
After striking a Tin/Lead or zinc alloy in a decorative rack plating operation we have been plating bright nickel for 30-45 minutes before flashing with gold. This has visibly been quite acceptable. Someone suggested that since we have an empty tank in the line that splitting the time between acid copper and nickel would provide just as bright a nickel base at less of a cost. What are the plating characteristics of acid copper and Brite nickel and is this concept one worth exploring.
Ken Fefferman- Harwood Heights, Illinois
1996
Hi, Ken. In many shops labor is the costliest part of production. Add to this the extra rinse water required when copper plating, and the cost of treating it. Then the increased rejects that are implicit in a cycle of more steps. I think you would find that substituting copper for half of the nickel might raise, rather than lower, the product cost--which is probably why few OEM bumper plating shops use copper anymore.
However, if you are "tank bound" in the nickel tank, such that you could double production by halving the nickel plating time, it certainly would be worth thinking about. I believe that you would see no decline in brightness, and that the nickel would still be thick enough to prevent diffusion of copper into the gold. But this is an educated guess, not a professional opinion.
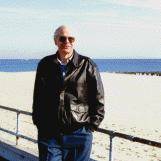
Ted Mooney, P.E.
Striving to live Aloha
finishing.com - Pine Beach, New Jersey
Hi, I see your line of reasoning about labor and dragout vs material cost. Is there any plating characteristic which would motivate having both baths in a decorative zinc or tin/lead operation. Does acid copper cover porosity better or plate faster or anything else. Thanks,
Ken Fefferman- Harwood Heights, Illinois
1996
Hi, again. I see only two things that would suggest plating an underlayer of copper: a need to buff to fill scratches, and as a guard against nickel shortages. They say that history is written by the victor, but perhaps it's actually written by the bystanders. Here is the history I saw, with no guarantee that I saw it accurately: Years ago there was no such thing as self-leveling bright nickel, so decorative work was copper plated, buffed, then nickel plated. Perhaps out of habit, perhaps due to occasional need to buff, decorative work continued to be copper plated then nickel plated for some years. 25 years ago or so, there was a prolonged period, 2 or 3 years, where nickel rationing was in effect and the best you could hope for was to be allowed the amount you had used the year before. In this climate, nobody was likely to say: "Hey, I've got it, let's eliminate copper and just use twice as much nickel!"
But in the past 15 or 20 years, most decorative shops I know of have eliminated the copper underlayer, and even when nickel went to $7+ per pound a few years ago, there was no major move back to a copper underlayer. And such references as MFSA's Quality Guides do not suggest copper underlayers or claim that they offer any corrosion resistance advantages.
But you will encounter old-timers who think it is advantageous without being able to prove any specific advantage, and also those who claim (I believe correctly) that the result is higher reflectivity via the buffing
I think it will be cheaper to apply nickel than copper plus nickel, as noted previously. If it were possible to apply only copper, that would probably be less expensive than nickel, but I don't think that is a possibility in your case where you are going to gold plate.
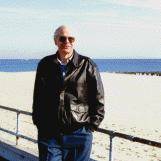
Ted Mooney, P.E.
Striving to live Aloha
finishing.com - Pine Beach, New Jersey
Ted's comments are true and the expense of introducing an acid copper step between the strike and the bright Ni wouldn't be worth the trouble. Also, the Cu bath would have to be maintained at least as a semi-bright for the finished product to have the same degree of luster. A much simpler and probably more efficient approach would be to fill the empty tank with a semi-bright nickel formulation. You will be killing three birds with one stone: 1. No intermediate rinsing between the semi-bright and bright Ni baths would be required, so, no extra rinsing steps will be involved; 2 Semi-bright Ni is more noble in corrosion terms than bright Ni, therefore, a combination (duplex) semi-bright-bright layer of nickel can be reduced in thickness by about 30% with no loss of corrosion resistance. Moreover, the semi-bright Ni is substantially less porous than the bright, so your gains could be even higher; 3. The semi-bright bath would also serve as a barrier to dragout contamination for the bright Ni bath, improving it's performance. I've done such a conversion myself with excellent results. Good luck to all from PlaterB
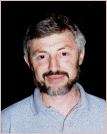

"PlaterB" Berl Stein
NiCoForm, Inc.

Rochester, New York
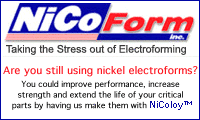
1996
Q, A, or Comment on THIS thread -or- Start a NEW Thread