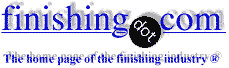
-----
Is ASTM B633 still the viable spec. when calling out trivalent chromium?
2005Q. We design and manufacture CATV power supplies and outdoor enclosures (3R, 4 and 4X). We have been specifying clear and bronze chromium conversion coatings over zinc plated CRS per ASTM B633 for some time, and are just now realizing these coatings are hexavalent and are rapidly being phased out (RoHS, etc). We are researching trivalent chromium coatings and our local plating vendors' capabilities with this. It seems we will be able to make the switch without major issues. Reading the many posts on this issue here in finishing.com has been a tremendous help in increasing my knowledge.
My main concern is creating new internal specs/drawing notes to specify trivalent chromium. Example: One current spec. we have is: "Zinc plate (0.0010" thick) plus bronze chromate conversion per ASTM B633-98: Type 2 bronze, FE/ZN 25, (very severe environments)". Questions I have:
How would I call this out for trivalent chromium?
Do I continue referencing ASTM B633, even though it was written for hexavalent chromium?
Are there new accepted ways of specifying trivalent chromium?
What if I want to keep the native clear/blue trivalent (instead of dyeing yellow) and have high corrosion protection (which is possible now)? Do I then have to customize my note since type 3 is clear (but low corrosion protection) and type 2 is colored (but high corrosion protection)? i.e. call out salt spray hours?
Thanks for your time. Any information will be appreciated.
Mechanical Designer, Power Supply Industry - Bellingham, Washington, USA
A. I would be interested in other people's take on this inquiry, too, John. My feeling is that there is nothing that prevents you from saying "except . . ." or "but . . .", and thus you can say "except that chromate conversion coating must be trivalent in accord with RoHS standards, and must achieve xx hours to white rust".
But spec writers don't like their specifications used in this fashion unless your spec is "tougher" than the more generic case. They try to prevent you from "diluting" the spec. Here is an extract addressing that (this extract is from ASTM A480 and I don't know offhand which specs have and don't have such a statement) --
Several different technologies are in play in this rapidly changing, highly competitive, proprietary field, including at least one naturally yellow trivalent chromate. Some of these trivalent chromates use top coats for increased corrosion protection, and that may be no problem in some applications; but if you need conductivity, or paint adhesion, etc., your "except" list may also have to prohibit such top coats or allow only certain types, etc.
You are probably right that there may be some problems with B-633 in this age of proprietary trivalent chromates for RoHS standards, but it is a far better starting point than a blank sheet :-)
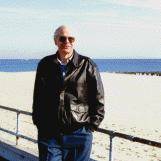
Ted Mooney, P.E.
Striving to live Aloha
finishing.com - Pine Beach, New Jersey
2005
2005
A. It's my opinion that referring to ASTM B633 leads to more confusion than clarity; the automotive industry uses much more of Zinc Alloy plating and Trivalent Chromate and without referrals available, its easier to use relevant automotive standards as a guide or starting point.
The reason being, Trivalent chromates don't deliver similar results as Hexavalent; I have had twenty enquiries last year with customers asking for Trivalent Passivations with Hexavalent Plus performance and its not actually happening on plating shop floors despite fancy literature and fancy prices.
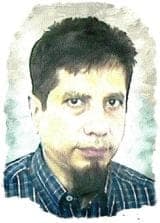
Khozem Vahaanwala
Saify Ind

Bengaluru, Karnataka, India
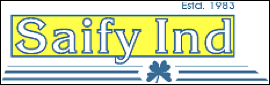
A. So much to say and yet I don't know where to start.
1. Trivalent provides ALMOST the same corrosion protection as hexavalent. We have done many, many salt spray tests with several different suppliers of trivalent products (not all trivalent products yield the same results) and we just can't seem to get the same corrosion protection as with hexavalent. Again, it is very close but not equivalent. Trivalent is still the best/closest/cost effective replacement in our opinion.
2.We still use ASTM B633 and do exactly as Ted has stated. We state on our drawings that the parts must be RoHS compliant and for the passivation over our zinc plating to be Trivalent "clear to light blue" in color. We do call for type II and allow no red rust for the 96-hour test on either the primary surface or edges of our sheet metal piece parts. We also have a standard calling for no white rust on the primary surface up to 12 hours. No more than 10% white rust on the primary surface for 96 hours. White rust on the edges is acceptable. I do agree that ASTM needs to help out with this situation by modifying B633 but for now it's all we can go with.
3. Our manufacturing plants are keying off of the "clear to light blue color" and will be scrapping any existing sheet metal that is yellowish in color after a certain date next year in order to become RoHS complaint.
- North Canton, Ohio
2005
A. Just who is this ASTM and who do they think they are leaving industry up in the air like this? I can answer that as I am an ASTM volunteer on Committee B08 that works on issuing new and revising existing ASTM specifications on Metallic and Inorganic Coatings. ASTM B633 is one of those specs. Unfortunately, as with all too many technical organizations, corporations aren't so willing to support such organizations and persons aren't so willing to give up their time so organizations suffer from too much work to be done by too few people. This is just the case with ASTM's Committee B08 on coatings! It needs dedicated people from firms willing to support this necessary effort to keep specifications current and technically up to date. If you're willing to support this necessary cause, visit the ASTM web site and check out joining the committee.
As an ASTM insider, check out the ASTM guidance document on terminology and you'll discover that "chromating is a chemical conversion process using chromium compounds." When they wrote this, they didn't differentiate between hex or tri so Type II ASTM B633 could be either tri or hex. Regardless of this, anyone ordering a RoHS compliant coating should clearly specify that they're looking for such. Our firm has 7 electroless nickel combinations, some of which are lead-free / cad-free and some not - to heighten the cases that a RoHS compliant coating is achieved, it's always best to let your finisher know.
Lastly, we're using a clear, blue-bright tri-chrome conversion coating that gives wonderfully bright clear and when a yellow dye is added to it, looks amazingly close to conventional hex chrome yellow zinc. The clear, trivalent product OUT PERFORMS any clear hex product we've ever used and the yellow is nearly identical in corrosion performance.

Milt Stevenson, Jr.
Syracuse, New York
2005
Q. Please help me to find the ASTM B633 (downloading) for zinc electroplating.
Thanks & regards
employee - ludhiana,Punjab, India
December 1, 2009
A. Hi, Baljit. We've linked your inquiry to a source for the spec; there are other specification clearing houses, or you can download it from www.astm.org. In any case, as Milt says, it is a lot of work to put these standards together ... so they are internationally copyrighted and you must pay about $40 - $50 for the download. Good luck.
Regards,
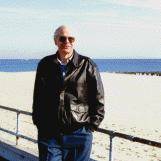
Ted Mooney, P.E.
Striving to live Aloha
finishing.com - Pine Beach, New Jersey
December 1, 2009
Q. Perusing the text of ASTM B633 -07, I see that they specifically define passivate as "a conversion coating on zinc shall not contain hexavalent chromium." To me, this incorporates trivalent chromate. Since types V and VI are defined as passivation, this would therefore make the trivalent chromate B663 types V or VI, colorless or colored respectively.
Anyone have any information regarding the conductivity of trivalent vs. hexavalent chromates on zinc? Is it possible to create a non-conductive chromate on zinc as can be done with aluminum?
- Meriden, Connecticut, USA
August 13, 2010
August 15, 2010
A. Hi, Ken.
I could be in error, but I don't think the conductivity of a chromate for aluminum (or zinc for that matter) is a go/no-go affair. Rather, I believe that the thin clear chromates simply impose lower resistance than when the same or similar chromate is applied thicker. I think what you are hunting for -- an insulative chromate -- won't be found.
Regards,
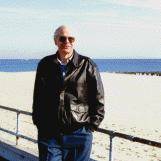
Ted Mooney, P.E.
Striving to live Aloha
finishing.com - Pine Beach, New Jersey
Q. Hi Ted,
I had assumed along the lines of what you mentioned (more resistive than non-conductive), but don't see a reference in the ASTM B633 nor ASTM B201-80 regarding chromate application and increased electrical resistance as is seen for aluminum in MIL-DTL-5541.
- Meriden, Connecticut, USA
August 17, 2010
Q. We are reviewing all documentation to make sure our products are RoHS compliant. (Our medical devices will shortly lose RoHS exemption).
Our standard Finish note (for many years) was:
ZINC PLATE PER ASTM B633 -98 Fe/Zn5 SC1 MILD, THEN CLEAR CHROMATE
How can we modify this note to make sure finishes are RoHS-compliant?
Component Engineer - Pittsburgh, Pennsylvania
January 26, 2013
Q. I have a requirement that zinc finish must be a Minimum of .0005 which would be 13 µm, in order for this product and finish to be compliant to their standards; we must also state which of the standards applies. I have checked the ASTM B633 standard, and ASTM along with ISO only show as 12 µm at a minimum. Is there any standards organization that covers Fe/Zn13 that I'm missing?
Dallas M. Dworak- Corona, Ca. U.S.A.
September 13, 2013
A. Hi Dallas. I suspect that your customer simply works in English rather than metric units, so they want a round number of .0005" to use with their inspectors and documentation, rather than wanting to specify an over-precise thickness of .00047244". I'd probably want to simply plate the parts to .0005" and certify them as complying with ASTM B633, 13 micron (.0005" thick).
Regards,
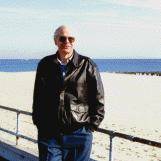
Ted Mooney, P.E.
Striving to live Aloha
finishing.com - Pine Beach, New Jersey
September 17, 2013
A. ASTM B633 covers 2 types of RoHS compliant (Hex Chromium free) plating, types V (colorless trivalent) & VI (colored trivalent). It also covers 4 standard services classes of thickness (SC 1 = 5 µm, 2 = 8 µm, 3 = 12 µm, 4 = 25 µm). The selection of V would be used when needed for a base coat under paint or powdercoat and VI for standalone plating.
For Reference: The service class is based on the expected wear and lifetime of the product. (i.e, indoor with no movement/wear = SC 1, outdoor/humid environment with movement/wear = SC 4). This is determined based on an educated decision.
- Pittsburgh, Pennsylvania, USA
October 3, 2014
ASTM B633 - Conversion Coating vs. Passivate
Q. Table II of ASTM B633, mentions "passivates" Types V & VI in addition to "chromate conversion coatings", Types II & III.
What are the "passivate", Type V & VI coatings?
Are the "passivate" coatings really just a chromic or nitric acid bright dip?
If it is a chromic acid bright dip, is the chromic acid concentration usually just 5-10 volume percent?
- Lakehurst, New Jersey, USA
December 30, 2015
A. Hi Rade. We appended your inquiry to a thread on the subject which may lend clarity. In the old days of 15 years ago, almost all chromates were hexavalent; the available trivalent chromates offered very little corrosion resistance. Then, in response to RoHS requirements, more capable trivalent chromates were developed, supposedly approximately equal in corrosion resistance to the hexavalent chromates.
After this, ASTM B633 was updated to acknowledge the existence of these trivalent or non-chromate coatings. Type V & VI are intended to be free of hexavalent chromium, so a dip in chromic acid would surely not comply. A nitric acid may brighten a zinc plated surface, but I don't think it affords any corrosion resistance or 'passivation' at all.
Type V & VI are hexavalent chromium free coatings, and to comply you would generally obtain a proprietary trivalent chrome conversion coating process from a vendor of such processes. Good luck.
Regards,
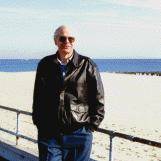
Ted Mooney, P.E.
Striving to live Aloha
finishing.com - Pine Beach, New Jersey
December 2015
January 6, 2016
! I believe that it would be worthwhile to refine a discussion such as this by defining the terms used. Some people may disagree with my definitions, and it would be worthwhile for them to describe why they disagree; finishing.com is a great forum for this kind of discussion.
As a chemist, I think that 'chromate' should refer only hexavalent chromium-containing coatings. But industry practice is to use 'chromate' for both hexavalent and trivalent post-plate finishes. Conversion Chemical, the first company devoted to chromate conversion coatings, used the term 'chromate' for the trivalent passivates developed by Ken Bellinger, and the misnomer has stuck. (I worked for the successors to Conversion Chemical in Rockville, Connecticut for a number of years.) So now we have 'trivalent chromates', a terminology that all chemists would consider internally contradictive. Others, seeing this contradiction, started calling these 'trivalent passivates,' which in my opinion is a good use of our language. I think that everyone can agree that 'hexavalent' is +6. And that 'trivalent' is +3.
What is a passivate?
In my opinion a passivate is a coating or process that passivates the surface -- in other words it makes the coating less reactive with the environment. So a traditional hexavalent chromate is a passivate. So is a trivalent conversion coating, which generates hexavalent chromium to passivate the metal.
Anodizing is clearly a passivating process. So are the oxidizing treatments commonly applied to stainless steel, which, like anodizing, make the surface passive by increasing the thickness of the oxide layer. This does not exhaust the list of passivates in any way.
So what is a conversion coating?
A conversion coating is a coating that converts the surface to another (hopefully better) coating. A zinc (or any other metal) phosphate is a conversion coating, converting iron to a mixture of zinc and iron phosphates on the surface of a ferrous material. All conventional chromates are conversion coatings, converting zinc (or any other active metal) to a mixture of hexavalent, trivalent and other compounds on the surface of the metal being treated. Again, this discussion of conversion coatings is not exhaustive.
There are a few no-rinse hexavalent chromium-based coatings that protect zinc or other active metals without conversion (Dacromet 150, Hyperguard 1.0; there may be others). So these are passivates but not conversion coatings. Similarly there are a few no-rinse trivalent passivates (Hyperguard 3.0, Tri-Top) that are trivalent passivates but not conversion coatings because they do not react with the surface. It is common to apply silicates or silicated polymers to the surfaces of active metals. Quite a few suppliers offer such coatings. These are generally not considered conversion coatings (although the is a limited reaction between the silicates or silicated polymers and the substrate), but rather passivates or topically applied inhibitive coatings.
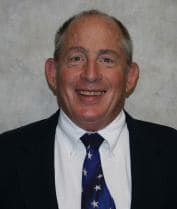
Tom Rochester
CTO - Jackson, Michigan, USA
Plating Systems & Technologies, Inc.

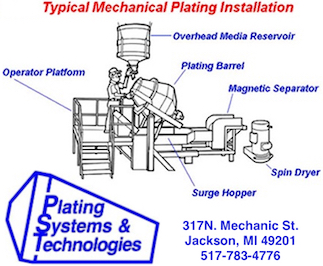
February 2016
Thanks Tom. I appreciate your explanations of these surface treatments.
My own feeling from handling tens of thousands of inquiries here over the past couple of decades, though, is that we can't successfully delimit loose words or phrases like "passivate" with definitions like those, much as we may want to, because people adopt shorthand and slang which is helpful and comfortable for them. For example, we constantly debate (see letter 11822 for example) whether carbon steel can be "passivated" but "passivation" will continue to mean one thing to stainless steel processors and another thing to people who offer boiler treatment chemistry :-)
You can tell the stainless steel processors that "passivation" is not limited to meaning treating stainless steel with nitric or citric acid to remove ferrous ions and thicken the oxide layer, and that other people are entitled to use the word, but that would force them to substitute long-winded and exacting specification numbers into their discussions in lieu of the short word "passivate", so they're not going to do that. Similarly, the boiler treatment people want to use the word "passivate" in lieu of long explanations about the Schikorr reaction and phosphate treatment, etc. So I think the answer to the continually repeated question of "Can carbon steel be passivated?" is not yes or no, it is "It spends on what 'passivation' means to you".
Regards,
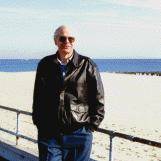
Ted Mooney, P.E.
Striving to live Aloha
finishing.com - Pine Beach, New Jersey
February 1, 2016
A. Ted:
Yes, it's all very context-sensitive. Highly technical people come up with these words that mean specific things, and then they escape into the industry where less technical people dwell, and take on new and slightly different meanings.
If I wanted to be precise about it, I would point out that all "passivation" of a carbon steel substrate involves some type of coating, because the steel itself inherently cannot be passivated. If I wanted to be extremely precise, I would point out that the passivation of stainless steel shouldn't really even be called that, because the passive surface layer has been removed of its iron and no longer has the composition of stainless steel, it is a chromium oxide layer OVER stainless steel.
In the end, as long as the parts don't corrode within expected operational parameters, the end user doesn't care what it's called. Though within our own little technical circles, using additional words as needed to better establish context does tend to be helpful.
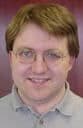
Ray Kremer
Stellar Solutions, Inc.

McHenry, Illinois
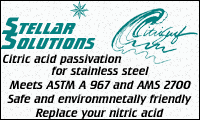
Q, A, or Comment on THIS thread -or- Start a NEW Thread