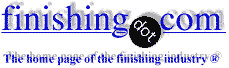
-----
Passivating carbon steel / when to / how to

this text gets replaced with bannerText
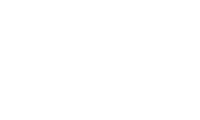
(added to provide context, hopefully helping readers more quickly understand the Q&A's)
This thread about 'passivating carbon steel' opens with the semantic problem of people not agreeing about the meaning of the word passivating or passivation, and therefore whether carbon steel can even be 'passivated' in the the first place :-)
Those readers who are most versed with the processes used to passivate stainless steel note that the electrochemical activity series & corrosion tables always make a clear distinction between 'active' stainless steel and 'passive' stainless steel whereas there is no such distinction for carbon steel. They also note that there are recognized Standards & Specifications for the processes used to passivate stainless steel, including ASTM A380 , ASTM A967, ASTM B912, and AMS2700) whereas no such passivation standards for carbon steel. They attribute a narrow meaning to the term and say that carbon steel can't be passivated.
But those readers who work with steam boilers and other equipment which requires treatment regimens & careful control of operating conditions to limit corrosion know that their measures make the carbon steel more passive, and are confident that their methods are passivating carbon steel.
In the end, slang can't be controlled, and the meaning of 'passivating' will depend on who is doing the slinging -- such that nearly anything can be 'passivated': zinc and electroless nickel surfaces are sometimes said to be 'passivated' with chromate conversion chemistry; steel surfaces are said to be 'passivated' with phosphatization; and that phosphatization in turn is said to be 'passivated' with a final chrome rinse. Thus, there probably is little to be gained from arguing the meaning of the word. But don't attempt a 'nitric acid passivation' of carbon steel -- it can evolve toxic quantities of NOx.
Q. I am having trouble convincing a customer (computer hardware manufacturer) that you only passivate stainless steel and not normal carbon or alloy steels. How can I proceed to verify this with them. Is there an exact specification I can go to. This is all about having some tools clean enough for a computer clean room environment.
Herb Earl- Phoenix, Arizona
2001
A. Your customer may be confusing "passivating" with "passive". Many times a steel part needs to be activated for plating or finishing because it has become passive. Passivating for stainless means to remove the iron from the surface and create a nickel and chrome- rich surface layer that is not as subject to rust (only iron "rusts"). Let your customer know that a steel part will always have a propensity to rust - even if it has become passive, because the iron is always exposed to the atmosphere. Hope this helps.
Dan Brewerchemical process supplier - Gurnee, Illinois
A. Herb:
You cannot "passivate" carbon steel. Passivation is removing the free iron and other exogenous materials from the surface so that a good passive layer can be formed. In the case of carbon steel, this is not possible. After cleaning with a good cleaner, there are a variety of coatings that can be used for carbon steel to provide a corrosion resistant layer, but passivation is not the correct process.
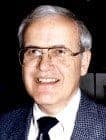

Lee Kremer
Stellar Solutions, Inc.

McHenry, Illinois
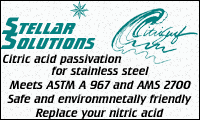
A. Passivating carbon steel. If carbon steel could not be passivated then there would be no boilers made of carbon steel. Boiler steel passivation occurs by the Schikorr reaction at about 300 °C or 30 bar pressure. A protective "passivating" magnetite layer, a few microns thick forms by a reaction between clean, pickled steel and water. The reaction lowers the pH of the boiler water. In practice, newly pickled boilers are subjected to controlled passivation using very small quantities of chemicals to control pH and prevent re-dissolution of new magnetite. The thickness of this magnetite layer will continue to grow at a decreasing rate until it hinders heat transfer. The boiler is then again chemically cleaned.
The chemical cleaning itself, by pickling, strips oxide layers from the boiler surface, leaving the steel active and prone to immediate oxidation (rusting).
To stop this "flash-rust" disturbing the Schikorr reaction, the pickled boiler receives an initial "temporary passivation". This involves dissolution of the flash rust in citric acid, followed by raising the pH to the range 8.8-9.5 using ammonia, which keeps sequestered iron in solution. Once the pH is correct, an oxidizing agent, for example sodium nitrite is introduced. This reacts with the iron in the steel to produce a very thin (40-100 Angstrom) layer of Fe2O3, which, when formed under these circumstances, inhibits flow of ions through it, thereby passivating the steel. This passivity is easily destroyed and is therefore temporary in nature (unlike passive oxides formed on stainless steel).
For carbon steel items to be used for everyday use, coatings are indeed usually applied. Some coatings involve chemical reactions in which iron from the steel plays a part (such as zinc phosphating), while other, usually more durable coatings physically attach themselves to the steel, for example paint. It is common that physically adherent coatings are applied to steel that has been temporarily passivated by, for example the formation of iron phosphate. Such phosphates are formed by dipping pickled steel into hot dilute phosphoric acid solutions followed by exposing them to air to complete the process. An example of such a process is phosphating and painting of car body parts.
For tools to be used in clean-room environments preference should be given to quality stainless steel implements.
Trevor Tipton- Singapore
A. I think Trevor has confused conversion coatings with passivation. To begin with, carbon steel boilers don't rust because the pH of the water is kept above the oxidizing point of steel which is about 8.2 - 8.3. The magnetite coating is a chemically induced conversion coating (also called black oxide), that if left in a pH environment below 8.2 will start to rust. If proper boiler chemistries and and periodic blowdown schedules are followed, there should be no buildup requiring chemical stripping of the boiler tubes. I have seen boilers that have been online for 10 years and more without needing a chemical strip.
Parts that receive a phosphate treatment likewise are not immune to rust and cannot be considered passivated. This is another example of a conversion coating.
To close, passivation is accepted as being a theoretically permanent condition. Passive means to not be active enough for the next finishing step.
Dan Brewer- Gurnee, Illinois
Q. Dear Trevor Tipton & Dan Brewer:
I liked your responses and would like to ask what is a good reference to read about the passivation of Boiler interiors?
And is it possible to obtain magnetite based solely on NaOH/Na3PO4 and ammonia
⇦ on
eBay or
Amazon [affil links] dosing for surfaces below & above 180 °C and pressures above 100 bar?
Best regards,
- galabovo, Bulgaria
2007
A. Passivation is subjected to lot of conditions. Say when you talk about a boiler, carbon steel tubes in generating section will have a reduced oxide in a state of magnetite. it remains intact only when you treat the water and chemically condition the same. Demineralised water, free from oxygen and chloride, pH elevated to 9.0 to 9.5, free from caustic, etc.; it is non impervious to ionic intrusion.
Whereas if it is gamma ferric oxide, it will remain intact and it's P.B ratio is above 1.0 it is impervious due to structural integrity, and natural oxide growth rate during regular operation is retarded and beneficial in all respects.
- Chennai, Tamil Nadu, India
March 27, 2009
Q. I have heard a lot about stainless steel passivation using various chemicals. But is it possible to passivate carbon steel piping using sodium hydroxide, hydrochloric acid, soda ash, Rodine-213 (corrosion inhibitor) and glassy sodium meta phosphate?
Can you suggest alternative for the same.
Regards,
consultant - New Delhi, India.
August 27, 2009
A. Passivation is a state wherein we protect it from re-oxidation.
A chemically active surface is more prone to attack due to its active state after immediate chemical cleaning. It is important to make the metal passive to prevent the re-oxidation and thereby prevent further corrosion
Normally the medium is switched to an alkaline state after an acidic reaction with an oxidising agent to get the passivation layer on to the surface.
- baroda, Gujarat, India
A. Carbon Steel can be passivated using .25% NaH2PO4, .25% Na2PO4 and .5% NaNO2 @ 150 degrees. Makes a passive phosphate layer.
Bart Snow- Ponte Vedra Beach, Florida
Q. Hi Bart Snow.
I will be grateful if you post your references. Also explain that passivating process.
Student - Isfahan, Iran
October 30, 2021
Q. Is it possible to passivate BI pipes? If it's possible, what is the recommended acid for passivation? Is phosphoric acid applicable? Thank you.
Liz Bargola- Philippines
January 1, 2013
A. Hi Liz. It is certainly possible to treat rusty steel with phosphoric acid to convert the fluffy red rust to the more stable black rust. Whether this should be called 'passivation' is a semantics argument over the use of that word rather than a technical issue. Some people consider the word 'passivation' to have a very specific meaning that applies only to the processes used on stainless steel.
Regards,
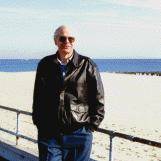
Ted Mooney, P.E.
Striving to live Aloha
finishing.com - Pine Beach, New Jersey
Q. I've seen lots of conjecture about passivating metals.
If anyone has good information I would like to know:
General Question: What is a good global definition of passivating and passive?
Specific question: Is it possible to passivate carbon steel in aqua ammonia to prevent further corrosion at ambient temperatures.
Thanks.
- Denver, Colorado, USA
July 10, 2013
![]() |
A. It is possible but that is an old fashioned way, and other methods such as Parkerizing would be better. If it's a prototype you can try it. If the application does not contain an aggressive environment or a lot of H2O then you might get away with bluing or using the method you mentioned,; it won't hurt, it will help a little to use an alkali solution. ![]() Blake Kneedler Feather Hollow Eng. - Stockton, California A. My thought is that it would be a neutralizing rather than passivation step. - Navarre, Florida |
A. Hi M. As this page notes, "passivation" has a good definition when it is applied to stainless steel; ASTM & AMS and other specs provide the careful definitions that you seek. But the word is also used in slang fashion for many other situations and there is no way anyone can limit slang; that is just the way the world is :-)
We can say that a "tank" is an armored fighting vehicle and write careful definitions for how thick the armor must be and what specifications it must meet before it can properly be called "a tank" according to those specifications ... but that won't stop people from calling their aquariums, hot water heaters, propane cylinders, and gasoline reservoirs "tanks". And even if we add all those terms & more to the dictionary, it won't stop teenagers from calling their parents' old station wagon "a tank". Thus it probably will remain with 'passivation' :-)
Regards,
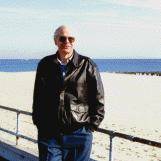
Ted Mooney, P.E.
Striving to live Aloha
finishing.com - Pine Beach, New Jersey
A. M.,
Passive is actually a chemist's term, it is the opposite of active. Active refers to atoms or molecules that "want" to react with something. Taking metals as a pertinent example, metal as we think of it has an electron valence of zero, which is to say the number of electrons in orbit is equal to the number of protons in the nucleus. However most atoms, including metals, "prefer" to have a different number of electrons, in the case of metals they want to give some away and become a positive ion in solution or become bonded to the atom that it gave its electrons to. Surface oxidation is the most common route to this, for instance if you cut a block of aluminum in half you can see the slight color change across the fresh surface as oxygen gas swoops in and quickly forms a layer of aluminum oxide. The new oxide layer is "passive" because it is happy and no longer want to react to anything, and as a bonus it seals off the zero valence aluminum underneath from being able to react with anything.
This is all fine and good for the majority of nonferrous metals, but when iron forms iron oxide it is not a nice and pretty layer, it turns to rust and falls off, exposing new iron to new oxidation. Common methods to combat this are coatings of another material, such as paint, powder coat, zinc (galvanizing), a chromate conversion coating, etc. There are also stainless steels, which use chromium to form a chromium oxide layer over the iron, protecting it the same way the aluminum oxide prevents further reaction in the underlying aluminum metal.
Anything that renders your surface less likely to chemically react with materials in the environment can legitimately be called "passivating".
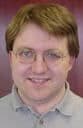
Ray Kremer
Stellar Solutions, Inc.

McHenry, Illinois
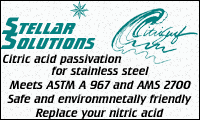
What is "sequestered iron"?
Q. Hi.
What is "sequestered iron"?
Iron II and III in complex with citric acid is "sequestered iron"?
After the pickling phase, the steel surface will be very reactive and oxygen will cause flash rust to form.
What is flash rust? Fe2O3?
If flash rust is Fe2O3, why must we remove flash rust before "temporary passivation"? wWe create Fe2O3 in temporary passivation.
power plant - mashhad, khorasan, Iran
July 20, 2014
A. Hi Hasan. I am not a chemist, and hope to be corrected if I'm seeing it wrong, but your question is partially technical and partially semantics. According to Wikipedia, sequestration and chelation are much the same thing, but others might use "sequestration" in a looser sense where the iron is tied up or complexed in ways that may not meet the actual definition of chelation -- for example, iron can be complexed with cyanide ("Prussian blue") and it is probably proper to say that the iron is sequestered.
I think any condition which keeps more iron in solution than the pH and alkalinity alone would dictate probably represents sequestration.
Flash rust is red, so I'd say it is Fe2O3. I believe the idea in pretreatment is to remove the rust and then get on with the treatment process immediately rather than letting flash rust form.
Regards,
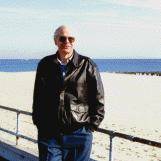
Ted Mooney, P.E.
Striving to live Aloha
finishing.com - Pine Beach, New Jersey
A. Indeed, "sequestered" isn't really the preferred term by chemists but I'm pretty sure as a colloquial it means the same thing as "chelated". Wikipedia seems to agree.
There are a few different varieties of iron oxide, depending on the oxidation state of the iron atoms, or the ratio of iron atoms to oxygen atoms present. I always forget which is which, but black iron oxide tends to be pretty stable while red iron oxide is the rust that eventually leads to progressive deterioration of the metal.
I have heard of "temporary passivation" of carbon steel in regards to boilers -- I'm not overly familiar with the process but in general any coating that prevents oxygen molecules from contacting zero valence iron is getting you what you need, for as long at it's intact.
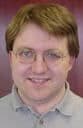
Ray Kremer
Stellar Solutions, Inc.

McHenry, Illinois
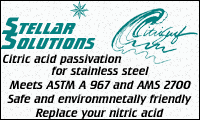
A. Hi hasan eghbali,
The difference between flash rust and temporary passivation is simply that the temporary layer is gamma Fe2O3 which is gamma hematite, but the flash rust is normal hematite (I think is alphaa hematite). the Gamma Hematite is produced at higher pH and enriched oxygen content (presence of strong oxidizing agent).
- Sydney, Australia
January 7, 2019
Q. Dear All,
I just have gone through with interest the arguments put forward by the august participants in the Q & A column. It is not clear why it is said that carbon steel does not need passivation. All the water tubes of sub-critical boilers are of carbon steel and all the top notch manufacturers of such boilers recommend chemical cleaning of the boiler tubes by alkali boil out to remove oil, grease, loose debris etc, then rinsing, thereafter acid pickling to remove rust, mill scale etc. This is followed by DM Water rinsing, then citric acid pickling and thereafter, neutralization by raising pH with sodium nitrate
⇦ on
Amazon [affil link]
solution in a sequential manner. After this, passivation of the nascent iron surface is effected by ammonia and hydrazine solution having pH 10. This helps in the formation of a passive Magnetite (Fe3O4) layer which prevents re-rusting of the tube internal surfaces. This magnetite layer can be maintained if the pH of the Boiler water is maintained between 8.5-9.5.
My understanding is that the alkali boil out procedure alone cannot remove the rust, mill scale, etc. from the tubes and form the passivated layer.
I would be thankful if someone can inform that alkali boil out alone can remove rust, mill scale and form the passivation layer. Also I would welcome an explanation how the Tri-sodium phosphate and Sodium Hydroxide are instrumental in forming the passivation layer.
Thanking you all,
November 4, 2014
- CALCUTTA, WEST BENGAL, INDIA
Hi Dhruba. I don't think anyone claimed that carbon steel "does not need" corrosion-proofing. I think what they claimed is that carbon steel does not use or benefit from the processes that are used to passivate stainless steel, and that some people reserve their use of the word 'passivation' to refer to those carefully defined and specified processes for stainless steel.
Sorry, I am not familiar with the protocol for preparing boiler tubes for service beyond what you read on this page.
Regards,
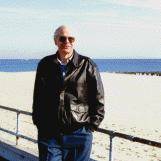
Ted Mooney, P.E.
Striving to live Aloha
finishing.com - Pine Beach, New Jersey
Q. Is it possible to use Gaseous Oxygen as the oxidizing agent post mill scale removal with citric acid ? The short answer of just "NO" or "YES" is not what I am looking for, but rather why you cannot or can. Traditionally it has been a "NO" and to just use Sodium Nitrite to solution, never an explanation of why you cannot use gaseous oxygen.
Aaron Rook- Jacksonville, Florida USA
June 24, 2015
A. Aaron,
I may be missing some context to your question. What metal and for what purpose do you need oxidation? Gaseous oxygen, or just plain air since there's plenty of gaseous oxygen in there, is splendid for converting active zero valence metal atoms into metal oxides. It does vary a little depending on the metal, for instance if you are talking about iron it helps to have some moisture involved. If you are talking about converting zero valence metal atoms into metal ions via oxidation, you will need an aqueous solution containing an oxidizing agent, which can be but is not limited to acids.
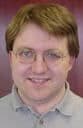
Ray Kremer
Stellar Solutions, Inc.

McHenry, Illinois
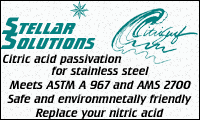
Q. Hey guys,
I'm working on a research program with AISI 4340 steel and the workpiece goes through a few baths of a protective (Bonderite Prevox 7400), I wonder if it is possible that this protective forms a passive layer on the surface that could influence negatively on a plasma nitriding process. We've been having to do some rework on nitriding and are trying to figure out why.
Any opinions about this??
July 22, 2015
- Curitiba, Paran, Brazil
Q. Can anyone tell me if there is any acid that I can introduce to my old iron water pipes to remove rust build up?
Bob Brinkman- Los Gatos, California USA
October 1, 2015
A. The way it is professionally done is with hydrochloric acid that is strongly inhibited. This is the same as what metal finishers call 'pickling.' The acid attacks the metal underneath, lifting the rust, and the inhibitor coats the metal, largely preventing further attack by the acid.
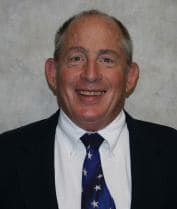
Tom Rochester
CTO - Jackson, Michigan, USA
Plating Systems & Technologies, Inc.

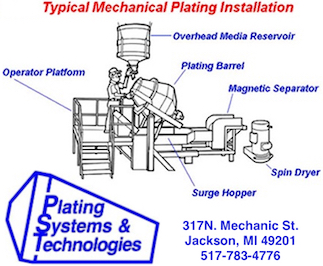
Q. After chemical cleaning with acid I use sodium nitrite as passivator. Is this enough for passivation or I should use another chemical instead of sodium nitrite?
moataz elmasryengineering solutions - portsaid, egypt
January 17, 2016
A. Moataz,
As per the usual here, please read the thread above for comments that may have already answered your question.
The answer to "is it enough" is always "it depends". If your item is going to live in a cool and dry environment, hardly any protection is needed at all. If your item is going to live at the water's edge along an ocean coastline, you need a lot of protection.
Possibly you will want to run some kind of performance test, like an ASTM B117 salt spray.
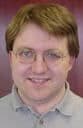
Ray Kremer
Stellar Solutions, Inc.

McHenry, Illinois
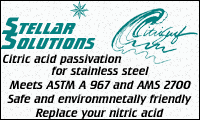
Passivation of mild steel boiler tubes
Q. I have done descaling of water tube boiler made of mild steel, and also I have done passivation with phosphates and caustic aqueous solutions; but by that treatment I have not taken good results. So I want a suggestion about chemicals as passivators. Please suggest chemical name for passivator for mild steel.
Thanks.
Regards,
water treatment company - Mohali, Punjab, India
August 22, 2016
A. Carbon Steel can be passive. Iron in its natural stage is almost never stable, it needs to bond with oxygen and form Iron oxide to be passive. Same happens with Stainless steel, difference is you form Chromium oxide (mrs stable) instead of Iron oxide (less stable) Pickling or descaling is not passivation, but the process to remove foreign matter from the metal surface. Once the metal surface is free of scales, then passivation can take place. For Stainless steel it is promoted with highly oxidative Acids In carbon steel is promoted with other oxidizers, being Sodium Nitrite the most common.
EDUARDO CORTESCESCO, (chemical cleaning experts) - Cuautitln, Estado de Mexico, MEXICO
Q. Hi!
First of all, excuse my English.
I have a problem: deionized water running through a carbon steel pipe, not recirculating. The line is already significantly corroded. As I understand it, diluted CO2 promotes the dissociation of Oxygen, increasing its mobility. On the other hand, another pipe of the same material is not suffering any corrosion at all; that is, I believe, because the pipe had years of "regular" sodium rich water running, effectively coating it.
At this time changing the piping is not an option. Would passivation/coating be an option? I am looking for at least a temporary solution to extend the operating life of the line. I fear that cleaning (pickling) the line with acid may compromise its thickness and even if that is not true it could be a waste in a pipe that should be changed in the near future. Is there any reaction that would stabilize the already formed rust, as was mentioned before? Also, the line carries a considerable pressure; I don't know if this can affect the passive coating, should it form.
Thank you in advance, interesting forum.
- La Plata, Buenos Aires, Argentina
November 14, 2017
A. Hello Alfredo!
Can you take off this piping for treating? Which size is it? Is it pressurized?
If you have running DI water through this pipe, you should have the pipe coated from the inside with some coating to maintain your pipe without corrosion and your water without minerals! Really, steel passivating is not very effective for this use as DI water will corrode your pipe again. If it were stainless, you could pickle and re-passivate, but carbon steel can't be permanently passivated as stainless.
If you can't take your pipe out and can't replace it, I would suggest chemical cleaning and soft protection (hydrochloric acid, rinse, then some steel protection as sodium nitrite and rinse with DI water), then paint your pipe from the outside. But this won't last, as carbon steel is not the material you want to work with DI water.
Best of luck amigo!
TEL - N FERRARIS - Cañuelas, Buenos Aires, Argentina
Q. I am a chemist working for an oil services company. We manufacture a product that removes H2S from natural gas. The problem is that we are seeing high corrosion rates downstream of our product from the remaining wet, CO2 laden gas. It seems the H2S was forming a protective "passivation layer" that kept the CO2 from eating the carbon steel. Is there any way to passivate the carbon steel to reduce the effect of wet, CO2 laden gas?
William BrundickGas Processing - St. Louis, Missouri USA
January 8, 2019
Q, A, or Comment on THIS thread -or- Start a NEW Thread