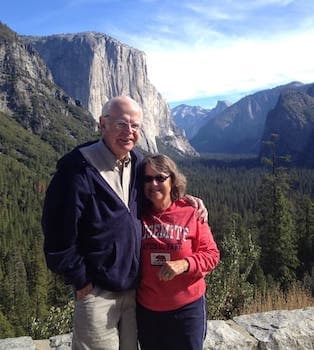
Curated with aloha by
Ted Mooney, P.E. RET
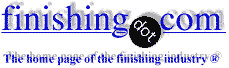
Finishing of Magnesium
Thomas J. Pullizzi, Bayside Electrical Testing, Inc., Beach Haven, NJ
Magnesium is usually treated with chromate conversion coatings or an anodize finish prior to the application of organic finishes.
Review of early prepaint cleaning and activation of magnesium --
Groshart1 states that magnesium must be passivated before painting. He recommends Dow 17 or HAE anodize (Mil-M-45202 Type I Class A) and Type I Class C, respectively, or Conversion coating (DOW 7 (Mil-M-3171 Type III or VIII) or or DOW 19 (Mil-M-3171 Type VI).
Weed2 recommends:
- Vinyl and epoxy resins for organic coatings since the corrosion products of magnesium are highly alkaline in nature, thus acting as a stripper for many commonly used organic primers and enamels.
- To minimize the corrosion potential between magnesium and dissimilar metals, the area of the magnesium should be large compared to the area of the dissimilar metal.
- The quality and thickness of organic coatings is most important in mating areas of dissimilar metals.
- Avoid sharp corners during design of the component.
- Allow for dimensional growth in protective coatings for magnesium except for dichromate or chrome pickle treatments.
- Select compatible aluminum alloys such as 5052 and 6061, for attachments and tin plated steel in preference to cadmium or zinc plating. If cadmium or zinc must be used, chemically treat with a chromate or a phosphate coating.
Published procedures and formulas for the finishing of magnesium --
Janssen3 studied thermal reflectance of AZ31B and HK31A magnesium samples and reports the use of the following solutions:
Electropolish:
HCl | 100 ml: ethylene glycol - 900 ml |
Temperature | Below 10 °C |
Time | 10 minutes |
Current Density | 20 amperes/square foot |
Preclean:
- degrease in trichloroethylene
- clean with inhibited alkaline cleaner (Oakite 61A/45 g/l), for five minutes at 93 °C followed by cold water rinse.
HAE process
The chemicals were dissolved in the order given, then the bath was dummied with 1 square foot per gallon of magnesium
Solution:
KOH | 163 g/l |
Al (metal) | 9.25 g/l |
Na3PO4 | 3.33 g/l |
KMnO4 | 18.3 g/l |
Temperature | 20 °C |
Current Density | 20 amperes per square foot ac |
For tan coatings the voltage was terminated at 64 VAC, for thick brown coatings the voltage was terminated at 85 VAC.
Dow 17 Process
Solution:
NH4HF2 | 237 g/l |
Na2Cr2O7.2H2O | 98 g/l |
H3PO4 (85%) | 85 ml/l |
Temperature | 71 °C |
Current Density | 20 amperes per square foot AC |
- Half the water was heated to 71 °C and NH4HF2 was slowly added. The other ingredients were added and the solution was heated to 82 °C.
- For light green coatings the voltage was terminated at 64 VAC, for thick green coatings the voltage was terminated at 90 VAC.
- These coatings were not sealed.
Sharma4 reports the use of the following solutions for preplating of electroless nickel and gold on AZ31B magnesium alloy (3% aluminum, 1% zinc, 0.2% manganese by weight):
(Water rinse after each step)
- ultrasonic degreasing in isopropanol for 5-10 minutes
- alkaline cleaning in NaOH, 50 g/l and Na3PO4.12H2O (TSP, trisodium orthophosphate), 10 g/l at 55-65 °C for 6-10 minutes.
- Acid pickle in CrO3, 500 g/l at 20-30 °C
- Immersion zincate: ZnSO4.7H2O, 50 g/l
- Na4P2O7.10H2O, 200 g/l, NaF, 7 g/l, and Na2CO3 5 g/l, pH 10.2-10.4 at 80-85 °C for 5-7 minutes.
To prepare the zincate: zinc sulphate ⇦ on eBay or Amazon [affil link] was first dissolved in water, then heated to 65-75 °C. Sodium pyrophosphate was slowly added to it while stirring. While the sodium pyrophosphate was added, a white precipitate formed that later dissolved, giving a clear solution. Sodium fluoride was then added to this clear solution, and finally the pH of the solution was adjusted with the addition of sodium carbonate ⇦ on eBay or Amazon] .
References
1. Groshart, E.A., Metal Finishing 83 (1), January 1985, "Organic Finishing, Part I - Design Concepts and Surface Preparation".
2. Weed, E.I., 47th Annual Technical Proceedings American Electroplaters' Society, 1960, "Magnesium Corrosion", pp. 66-67.
3. Janssen, J., et al., 49th Annual Technical Proceedings American Electroplaters' Society, 1962, "Thermal Reflectance of Anodized Metals for Spacecraft", pp. 126-132.
4. Sharma, A.K., et al., Metal Finishing, 91(3), March, 1993, "Gold Plating on Magnesium for Space Applications", pp. 34 - 40.
Ion exchange of chromate bearing rinse water solutions
- Ion exchange (IX) columns of cationic and anionic resins are available from several suppliers to cycle the rinse water from a static rinse through the resin beds to remove chromate.
- Use a small pilot plant to learn the chemistry, the vendors do not always have the expertise to provide mistake proof startups. You can estimate dragout from the parts, and, knowing the concentration of the hexchrome, you can determine how long your resins will last.
- Filter to remove particulates and send the rinsewater through the resin beds. A 20 " wound filter cartridge is a good size for up to a 1000 gallon rinse tank.
Typical processing data for MIL-M-3171C, Type VIII (proprietary chromate) Iridite#15
- Chemical (chromate) treatment for magnesium.
- Protective coating and/or a paint base to MIL-M-3171C, Type VIII.
- The coating should be non-powdery, of uniform yellow to brown color, depending on the magnesium alloy involved. There is no appreciable difference in corrosion resistance from light or dark coatings so variations in the finish due to slight differences in surface chemistry is acceptable. If color matching is imperative, additional surface conditioning may be useful. HF acid pickle and/or liquid honing will improve color matching but is difficult or impossible with some alloys.
Brush application
- Touch up of abraded, damaged, or reworked areas previously coated with a chemical treatment such as Dow #7, or anodize is acceptable. Approval for reworking should be made on a part by part basis by the quality control department, and should be included in the processing specifications for each part number or family of part numbers. For instance, threads which have been reworked can often be repaired with a suitable cleaning and brush application of chromating solution.
Processing New Castings
- New castings should be sand or grit blasted and then sulfuric acid pickled for 10 - 15 seconds or until 50 µm (0.002 " or inches) have been removed if dimensional tolerances permit.
Equipment and Materials
- Tank construction
- chromic acid pickle - lead lined or stainless steel.
- sulfuric acid pickle - plastic or lead lined.
- hydrofluoric acid - lead lined or plastic lined.
- Chemical chromate solutions - plastic, (Poly Vinyl Chloride (PVC), polyethylene, etc.)
- Work rods shall be electrically insulated from the tanks.
- Racks and hooks - PVC coated steel for racks, hooks, and baskets
Cleaning
- Parts may be cleaned in a commercial steel cleaner with the pH maintained above 11 except use alkaline cleaners with less than 2 percent caustic for ZK60A, ZK60B, and some magnesium - lithium alloys to prevent etching and dimensional change.
Chromic acid pickle
- Makeup: 180 g/l
- Operating conditions:
- Temperature 190-202 °F
- Keep chlorides, sulphates, and fluorides to a minimum, Test bath occasionally with a scrap piece of magnesium for any etching.
Sulfuric acid pickle
- Makeup: 4 fl.oz. /gal
- temperature: 70-90 °F
- hydrofluoric acid solution
- Makeup: HF (60%) 38 fl.oz./gal
- Operating conditions:
- HF 10 - 20 %
- temperature 70 -90 °F
Chemical chromate treatment for magnesium alloys with more than 1% aluminum
- proprietary chromate compound 5 opg
- HCl (concentrated) 7.5 fl.oz./g
- proprietary detergent 1 ml/gal
- temperature 75-100
- pH range 0.2 to 0.6
Chemical chromate treatment for magnesium alloys with less than 1% aluminum
- proprietary chromate (Note 2) compound 5 opg
- HCl (concentrated) 2 fl.oz./gallon
- proprietary detergent (Note 2) 1 ml/gal
- temperature 75-100
- pH range 0.6 to 1.0
General cleaning
- Immersion in alkaline cleaner until parts are chemically clean and free from waterbreaks.
- Corroded parts: Corrosion products and discoloration shall be removed by immersion in the chromic acid pickle for 1 to 15 minutes or until they are clean.
- Chemical finishes: Previously applied chemical finishes shall be removed by alternate immersion in the alkaline cleaner and the chromic acid pickle until the old finish is removed.
HF pre treatment (optional)
- Immerse the parts in the hydrofluoric acid solution for only as long as it takes the initial gassing to subside and no longer. Remove the part from the HF and rinse throughly to prevent the drag-in of fluorides into other processing solutions.
Chemical (chromate) treatment
- 2 - 3 minutes in the appropriate solution, depending upon the alloy.
- Rinse throughly in counterflowed rinses, immerse in hot water and dry. Drying by circulating air at 160 - 200 °F will produce a dark brown coating of increased hardness and reduced solubility.
Operating information
- Failure to form chemical chromate coatings: pH too high, solution too cold; metal not properly cleaned, ratio of acid to compound too low.
- Non-adherent powdery coatings: Alloy treated in wrong solution; pH too low; metal not properly cleaned; ratio of acid to compound too high.
- Parts with dissimilar inserts may be treated by this process except for aluminum inserts which may not be given the HF treatment, and copper inserts which will be etched by the chromic acid pickle.
Notes
1. conversion from English inches to metric µm (micrometres):
1 mil (0.001 inches) x 1 inch/1000 mils x 2.54 centimeters / inch x 1 metre/100 centimeters x 1,000,000 µm (micrometers) / metre = 25.4 µm
so 0.001" (inches) = 25.4 µm (micrometres)
2. Proprietary chromate compounds and detergents are available from chemical supply houses serving the finishing industry.
Process - Pickling of magnesium alloy castings.
Used for surface inspection (Type I) or to remove casting skin contamination (Type II)
sulfuric acid solution
- Makeup - 3 - 7 fl.oz./gal
- Temperature 70 - 90 ° F
- Tank corrosion resistant plastic
hydrofluoric acid solution
- Makeup - hydrofluoric acid 1 part
- Water - 4 parts
- Temperature 70-90F
- Tank - corrosion resistant plastic
Procedure
- Clean the casting of any oil in a suitable alkaline cleaner
- Immerse in the sulfuric acid solution for the following time, as applicable
Type I - 10-20 seconds
Type II - 1-5 minutes - Rinse throughly in cold water
Any smut may be removed by immersing for 10-30 seconds in the hydrofluoric acid solution. - Rinse throughly in cold water, then hot water, and dry.
The pickling of magnesium castings is done under Type I to detect surface flaws, defects, sand holes, and evidences of welding, and under Type II to remove the casting skin and other surface contamination that may affect subsequent chemical treatments.
The removal of casting skin and other contamination removes 25 to 50 µm of material from the casting.
Chrome pickle treatment (Dow #1) treatment of magnesium alloys (MIL-M-3171C, Type I)
Type I - Treatment for Wrought Material
Type II - Treatment for castings
The treatment of this process will produce a variable colored coating, depending upon the age of the solution, the alloy, and heat treatment condition of the alloy. The best paint base is a matte grey to yellow-red, iridescent color. Bright, brassy coatings are unsatisfactory for a paint base.
Chromic acid pickle
- Makeup: 180 g/l
- Operating conditions:
- Temperature 190-202 °F
- Keep chlorides, sulphates, and fluorides to a minimum, Test bath occasionally with a scrap piece of magnesium for any etching.
sulfuric acid pickle
- Makeup: 4 fl.oz. /gal
- temperature: 70-90 °F
Type I Chrome for treatment for wrought material: Pickle solution
- sodium dichromate (.2H2O) 24 opg
- nitric acid (1.42) 24 fl.oz./gal
- temperature 70-110
Type II Chrome for treatment for castings: Pickle solution
- sodium dichromate (.2H2O) 24 opg
- nitric acid (1.42) 24 fl.oz./gal
- potassium or ammonium acid fluoride 2 opg
- temperature 70-140 °F
Processing
- Blasting Post-treatment
- Castings subjected to blasting operations shall be pickled in the sulfuric acid pickle for 10-15 seconds or until 50 µm of the surface has been removed if dimensional tolerances permit.
- Cleaning: Parts shall be immersed in a commercial steel electrocleaner with the pH maintained above 11.
- Corrosion products and discoloration shall be removed from the parts by immersion in the chromic acid pickle for 1 to 15 minutes or until they are clean.
- Previously applied chemical finishes shall be removed by alternate immersion in the alkaline cleaner and the chromic acid pickle until the old finish is removed.
Dow #1 treatment
Type I, agitate the parts in the chrome pickle solution for 30 seconds to 2 minutes, with a 5 second drip time to develop color and reduce dragout. Rinse and dry.
For Type II, immerse the parts in hot (180F) water for 15 - 30 seconds followed immediately by immersion in the chrome pickle for 10 seconds to 2 minutes, with a 5 second drip time. Rinse and dry.
Brush application
Brush application with approval by the quality control department, is acceptable for repairs or for special parts too large for immersion in tanks.
Maintenance of Dow #1 solutions
30-40 replenishments. See Mil-M 3171C
Trouble shooting summary For Dow#1 processing
Brown, non-adherent, powdery coating - the part was in the air too long before rinsing; ratio of acid concentration to sodium dichromate too high; solution too hot; parts not clean; solution replenished too many times.
Grey, non-adherent, powdery coating on castings - immersed in bath too long; used Type I solution instead of Type II for castings.
Dichromate Treatment (Dow #7)
Dichromate solution
- sodium dichromate 20 oz/gal
- calcium or magnesium fluoride 1/3 opg
Operating conditions
- sodium dichromate 16 -24 opg
- temperature: boiling
- pH 4.1 - 5.6
- Immerse in the HF acid solution for 5 minutes, except that parts made of AZ31B shall be immersed for 30 seconds only. Rinse throughly.
- Immerse in the dichromate solution for 30 minutes. Rinse throughly in cold water, then hot water, then dry.
Dichromate solution maintenance
A 10 % solution of chromic acid is used to adjust pH. the calcium or magnesium fluoride content is maintained by the continuous immersion of a cloth bag containing one of these compounds: cloth made of vinylidene chloride or acrylonitrile fiber is recommended.
Troubleshooting information
Abnormally heavy and loose powdery deposits - HF acid concentration low; pH of dichromate low; corroded or contaminated surfaces; contact between work and tank;prolonged treatment in the dichromate solution.
Failure to coat or nonuniform coatings - pH of dichromate solution too high; dichromate concentration low; surface contamination because of insufficient cleaning or contaminated after cleaning; temperature of dichromate solution;improper rinsing after HF acid.
Notes on Dow #7
- The dichromate treatment provides an excellent paint base and protective coating on all standard magnesium alloys except EK30A, EK41A, HM31A, HM21A, HK31A, La141A and M1A. No coatings form on these alloys.
- Castings containing bearings, studs, and inserts of brass, bronze, cadmium plate and steel may be treated. Aluminum is rapidly attacked by the HF acid. Do not use the chromic acid pickle on parts containing copper based inserts.
- Use alkaline cleaners containing less than 2 % caustic for ZK60A, ZK60B and some Magnesium Lithium alloys, as dimensional losses due to etching may occur.
Anodic treatment of magnesium alloys
MIL-M-45202A, Anodic treatment of Magnesium Alloys
Class
Type I - Dow#17 Process
Type II - HAE Process
Class A - Thin Coating
Class B - Heavy Coating
All castings, before machining, shall be sand or grit blasted and acid pickled with:
- sulfuric acid - 3-7 fl.oz./gal
- Temperature 70-90 °F
- Tank - ceramic, rubber-lined, lead or equivalent
- Time - sufficient to remove 50 µm (200 µinches)
Note: Any smut formed after pickling may be removed by dipping in 10-15% HF acid solution.
Color
- Type I - Class A - Light Grey to light, yellowish green
- Type I - Class B - Dark Green
- Type II - Class A- Tan
- Type II - Class B - Dark Brown
Dimensional Change
(Minimum, Maximum, Typical)
- Type I - Class A - 0.1, 0.5, 0.3
- Type I - Class B - 1.5, 2.7, 1.9
- Type II - Class A - 0.1, 0.3, 0.2
- Type II - Class B - 0.6, 1.1, 0.8
Post Treatment for Type II (HAE) coatings
Unless otherwise specified, Class A coatings shall be given a chromate post treatment per Type I, Class A, Grade 2 or MIL_M_45202A and the Class B Coatings shall be given a bifluoride-dichromate post treatment as per Type II, Class A, Grade 3 of MIL-M-45202A.
Notes:
- Dissimilar metal inserts must be installed after anodizing.- The Heavy coatings have better corrosion resistance.
- Type I Class B coatings on castings have a tendency to spall (poor adhesion to itself) Class A coatings have good corrosion resistance in comparison to the chemical treatments for magnesium, but they have the limitations of no dissimilar metal inserts during treatment, and a slight dimensional change.
- Do not use these coatings on parts which are subject to flexing in service.
- For the best corrosion protection cover these coatings with one coat of zinc dust by brush, stipple or dab. There need not be a requirement that the paint coating match the color of the anodized coating. An additional coating of a approved paint may then be used to match the color of the anodize if necessary.
Impregnation of Castings
Applicable Documents
MIL-STD-276, Impregnation of Porous Non-Ferrous Metal Castings
MIL-I-6869, Impregnants for Aluminum Alloy and Magnesium Alloy
Castings.
Impregnation of castings requires the use of an aqueous detergent tank and hot and cold water rinse tanks for the detergent and uncured impregnating resin. Wastewater treatment of this rinsewater may be complicated by toxic organics present in the uncured resin, if so formulated.
Fluorescent Penetrant Inspection
Parts are to be etched prior to inspection.
Applicable Documents - MILITARY SPECIFICATIONS
MIL-I-6866 Inspection, Penetrant Method of
MIL-F-38762 Fluorescent Penetrant, Inspection Units
MIL-I-25135 Inspection Materials, Penetrant
MIL-P-47158 Penetrant Inspection, Soundness Requirements for Materials, Parts and Weldments
MIL-STD-410 Non-Destructive Testing Personnel, Qualification and Certification
Magnetic Particle (Magnaflux) Inspection
Applicable Documents - MILITARY SPECIFICATIONS
MIL-M-6867 Magnetic Inspection Units
MIL-I-6868 Inspection Process, Magnetic Particle
MIL-STD-410 Qualification of Inspection Personnel ( Magnetic Particle and Penetrant)
--------------------------------------------------------------------
copyright © 2000, Bayside Electrical Testing, Inc. 27 W. Rhode Island Avenue, Beach Haven, NJ 08008, USA, all rights reserved worldwide.
An Update on Magnesium Treatments
Following up on Tom Pullizzi's highly detailed and well-researched report from 2000 ...
With the ever increasing consumer demand for small, light, and portable electronic devices like cell phones and stylus-operated computers, magnesium and its surface treatment have become increasingly important.
At the same time, environmental pressures have made many of the older surface treatments undesirable and in some cases have even forbidden their use in some countries and on some applications.
Newer alternatives are available to supplant the older and more toxic treatments based on fluoride processes, silanes, cerium-based processes, micro-arc oxidation, electroplating, and electroless nickel plating. These newer processes are often either retained as trade secrets or covered by active (rather than expired) patents and thus are only available from the patent holders.
The major suppliers of proprietary plating processes offer these proprietary magnesium treatments and should be consulted for these replacement technologies.