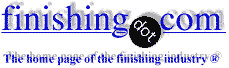
-----
What is "black rust" on steel?
Q. I am a law student working for a law firm and we have a document from a client which refers to "black rust" on steel. I don't know much about rusting, but I didn't realize that rust could come in different colors. Does anyone know anything about "black rust" and what distinguishes it from any other colors of rust? I've searched everywhere I could think of on the web, but nothing I've tried seems to distinguish colors of rust.
The firm is expecting me to be able to jump on the web and find an answer to this, so any help would be greatly appreciated.
- Valparaiso, Indiana
2001
A. A wild guess--They might be referring to the black "mill scale" that is an oxide on steel, when it is quite hot and exposed to air.
James Watts- Navarre, Florida
2001
A. I ran across this web page in reference to "Black Rust". www.nacecorrosionnetwork.com/archive/9812/0257.html This page refers to converting Red Rust Fe2O3 to Black Rust Fe3O4.
Bill Boatright- Raleigh, North Carolina
2001
A. Not to further add to the confusion but... could you be describing the actions of a rust "converter/remover"? (rust converter ⇦ on eBay or Amazon [affil links] ) These products will convert/dissolve red rust and leave behind a "passive" surface. In heavily rusted areas the rusted area once converted will appear black.
Richard Newman- Frankfort, Illinois
2001
A. The common chemical name for rust is Iron Oxide(s). It can actually be separated into different chemicals. The three most common are:
a) FeO = ferrous oxide
b) Fe2O3 = ferric oxide, hematite, and red iron oxide
c) Fe3O4 = ferrous ferric oxide, magnetite, and black iron oxide
They are widely used in the cosmetic and pharmaceutical industries as colorants. The shade ranges from a dull yellow through various oranges and reds to a deep black. Magnetite, or black iron oxide is also used to make recording media:audio and video tapes, floppy and hard disks, etc.
I'm not aware that "black rust" has any significantly different properties chemically than any of the other forms of Iron Oxides.
cosmetic pencil manufacturing - Bohemia, New York
2001
Not much progress! Some context from the original document would be helpful. That might indicate whether we're looking for a processing byproduct or a weathering/corrosion product or a deliberately applied coating or whatever.
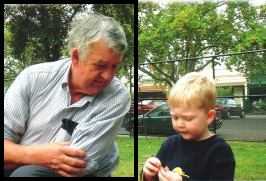
Bill Reynolds [deceased]
consultant metallurgist - Ballarat, Victoria, Australia
We sadly relate the news that Bill passed away on Jan. 29, 2010.
2001
A. I assume you have probably already attained the answer you were looking for, but if not here is some more information for you.
The "rust" converter concept does exist, but there is another possibility. In thermal processing of metal there is a process called blackening. This is a high temperature process used on (in my specific case) steel. The process promotes the "rusting" of the metal. The oxidizing of iron initially goes to FeO it then further oxides to Fe2O3 (your red rust). Another possibility is to hinder the formation of Fe2O3 and promote further oxidization to Fe3O4. This skips the layering effect. I mean red oxide (Fe2O3) which is then oxidized to Fe3O4 (black oxide). Instead you are attempting to have a larger % of FeO going to Fe3O4 than Fe2O3. Why is this important? Well Fe3O4 is more adherent and it has nice magnetic properties (very good for TV tubes). It also then inhibits red rust. So it is a "good" rust.
Regards,
- Lancaster, Pennsylvania
2001
The black rust could possibly be a coating, which is a form of rust. There is black rust which is good, and red/brown rust which is bad! The black rust is applied through a process of heat treatment (sort of a controlled rust)...its purpose is to reduce corrosion rate and its also a form of lubrication...its used in aviation parts as a break-in period.
San [surname deleted for privacy by Editor]- Norm, Oklahoma
2002
Q. The context in which you have encountered the term "black rust" would be helpful.
But I have also encountered the term recently as it relates to the a black, marbleized discoloration on corrugated metal roof panels that have been galvanized with zinc. It appears that the panels were stored outside for a period of time, and some water got in between the stacked corrugated sheets. The prolonged exposure to the water (so the theory goes) created the discoloration as the water could not evaporate quickly. In my case, both the terms "black rust" and "white rust" have been used to describe this condition. It is unclear whether this discoloration is merely aesthetic or whether it has impaired the rust-inhibiting properties of the zinc galvanization. A prior posting in this chain referred to "white rust" as the result of oxidized zinc. Does anyone know whether this condition impairs the zinc coating or the underlying steel?
Robert Dunn- Farmington, Connecticut
2002
A. Hi, Robert. "White rust" is the corrosion product of zinc, not the underlying steel. However, it is often associated with poor storage conditions. In use, galvanized coatings "see" carbon dioxide in the air and form a more stable corrosion product; but when stacked and stored wet, they suffer this "white rust" wet storage stain.
Regards,
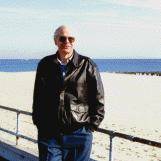
Ted Mooney, P.E.
Striving to live Aloha
finishing.com - Pine Beach, New Jersey
I would like to add my own experience.
My understanding of the term "Black Rust" is the corrosion products that form when iron or steel corrodes under conditions of limited oxygen availability. It is a sticky material that rapidly turns to the more conventional red/brown rust if it encounters a more oxygen rich environment.
Such black rust might be encountered on steel or cast iron under layers of aquatic growth or marine fouling, or on reinforcing steel in concrete immersed in sea-water. It may also be present on the surface of pipelines underneath disbonded but otherwise impermeable coatings. I suspect that black rust forms at the anode of macro corrosion cells in oxygen poor environments, and therefore does not encounter the cathode reaction products which under more normal conditions would allow the formation of conventional rust, Fe2O3.H20.
I am not sure of the composition of this black rust, but suspect that when it forms on steel immersed in sea-water it is a colloidal mixture of FeO (black) and FeCl2 since it sometimes has a greenish hue to it.
Since corrosion of steel to form black rust does not produce a crystalline material, it will occupy voids in concrete or other available spaces in concrete without exerting expansive pressures on the surrounding material, and therefore has the ability to dissolve substantial amounts of reinforcing steel without the concrete cracking and spalling. This can result in gross underestimation of the severity of corrosion and the weakening of RC structures.
I have heard of failures in the UK involving prestressed concrete beams due to black rust, but I do not have any more details. I would also welcome more information about black rust.
- Sydney, NSW, Australia
2002
A. Dear Sir,
Black rust is the ferric tannate formed by the reaction of tannic acid
⇦ on
eBay
or
Amazon [affil links] with iron. All forms of rust are converted to the ferric salt and passivated. It is also the classical ink which lasts very long.
Bye,
- Chennai, India
2002
A. I live in an area where road salts are used a lot and rust is a constant problem. I have done a bit of research on rust prevention and will answer your question about BLACK RUST.
Black Rust on steel or Iron is Fe3O4. The red rust you normally see is Fe2O3. Black Rust is protective in nature as it's molecules are not as large as Red Rust. Black rust will coat the iron/steel and prevent oxygen from reaching the underlying metal. Red Rust on the other hand puffs up because of it needs more room than in it's previous unoxidized state. This expansion exposes bare metal to oxygen and causes the Red Rust to spread.
There are many products on the market that will convert Fe2O3 (red) to Fe3O4 (black). The resulting Black Rust will protect the metal and can be painted but does not offer a smooth surface. It's not too practical for auto body but for the underbody, inside wheel wells, etc it's perfect. Black Rust conversion is also perfect for marine applications, steel fences, towers, or anything else outside that has rusted and does not require a smooth finish.
- London, Ontario, Canada
2003
A. Hello, perhaps I would be able to answer this question since I majored in Chemistry. First off, as was already explained, rust as you probably are familiar with it is an iron oxide. The red/brown stuff is Fe2O3, or Iron III Oxide with a +3 charge on the iron. However, being a transition metal, iron may also exist with a +2 charge. Oxygen under ordinary conditions only exists with a -2 charge. This means that you can have FeO or Fe2O3. In certain mineral structures you can also have Fe3O4 (This is also an Iron III Oxide.) FeO and Fe3O4 are usually black. Unfortunately, this is not the whole story. Sometimes, molecules of the same chemical can be arranged in different ways or in different structures. Usually one of a few of these forms will predominate, however atoms arranged in different ways will effect light in different ways. For example, you are probably familiar with diamonds and graphite. Technically, they are both made of nothing but carbon atoms. But most people would rather wear a diamond on their finger than a chunk of graphite. Actually, Fe2O3 can exist in a black state, the structure known as Black Alaskan diamond. If I am not mistaken it also plays a role in giving color to other precious gems but since these gem structures involve more than a single type of molecule I will avoid further discussion. If you want to know if you have FeO or Fe3O4, you can try to put a flame to it. FeO should become rust like you know it if it is forced to react with more Oxygen. Fe3O4 on the other hand already has given up all the electrons it can and actually there is something else going on with it that I will not explain. Suffice it to say that 2 of the irons in Fe3O4 are +3 while one is +2, but due to something called resonance the charge is distributed.
Hope this answers your question.
- Iowa City, Iowa
2003
I hope this will help. I found it posted online on the MadSci Network: Chemistry site hope it helps.
"When iron rusts quickly and is kept wet, the first product is usually Fe3O4, the mineral with this formula is called Magnetite. It is magnetic, colored grey to brownish-black. When finely divided it is black."
(Posted By: Charlie Crutchfield, Retired)
- Sooke, BC, Canada
2004
Hi - I am doing some R&D; but just for interest
-
Circ 1700 Guns were made - then they discovered brown rust
(red rust) protected the metals - as used on guns like the brown bess a thin coating usually polished and oiled protected the surface from further rusting -
Circ 1900 the gun trade discovered that if you boil in water the brown rust - you ended up with a nice black rust - known as blacking / blueing - hence blacking of steel -process is still used today .
- Kent, UK
2005
2005
Fe3O4 is Black Magnetite
a black colored corrosion product
This came off of:
METHODS OF CONSERVING ARCHAEOLOGICAL MATERIAL FROM UNDERWATER SITES
The primary anodic reaction of electrochemical corrosion of iron is the production of ferrous ions. The secondary stage, the oxidation of the ferrous ion compounds to a ferric state, is modified in anaerobic environments. Intermediate oxidation products of ferrous hydroxide, such as hydrated magnetite and black magnetite, are formed (Potter
1956:236-237; Evans 1963:28-29, 75):
6Fe(OH)2 + O2 >> 4 H2O +
2Fe3O4 . H2O
(green hydrated magnetite)
Fe3O4 . H2O >> H2O
+ Fe3O4
(black magnetite)
Depending on the environment, the corrosion products can take on a variety states of division and hydration, as well as a variety of physical forms. It is common to find corroded iron from marine sites with an outer layer of hydrated ferric hydroxide (common rust), which has restricted the supply of oxygen to the ferrous hydroxide briefly formed at the surface of the metal. Laminated corrosion layers consisting of an inner layer of black magnetite, a thin layer of hydrated magnetite, and an outer layer of hydrated ferric hydroxide are formed:
Fe3O4 /2 Fe3O4 . H2O or 2 Fe2O3 . H2O
- East Hampton, Connecticut
A. Black rust forms during high temperatures in a reducing atmosphere.
Tristan pope- Coventry, England
2005
A. I am in Year 9 at School, and I make Chainmail. We mailsmiths use lemon juice or a similar acid to turn galvanized iron or steel darker.
I don't know if this is any help.
student, high school - Sydney, NSW, Australia
2005
A. Fe3O4 is not black magnetite. Fe3O4. H2O is black magnetite. The difference is marked, and the two should not be confused.
In any event, Fe3O4 occurs in low moisture environments when iron is heated substantially. As far as I know,
black rust does not occur naturally. Fe2O3 (the bad kind) occurs when iron hydrides are formed during the partial oxidization of iron.
Fe2O3 flakes off and exposes more of your metallic crystal iron/steel to be oxidized. Fe3O4 does not.
- Odessa, Texas
2005
A. Daniel et al.,
Sorry that I did not see this posting earlier. There is a quite excellent article on anhydrous (5 types) and hydrated (10 types) of iron oxide authored by Mr. Douglas Godfrey. It appears (pages 33-37) in the February 1999 edition of Lubrication Engineering Magazine (a.k.a. The Journal of the Society of Tribologists and Lubrication Engineers).
Three of the anhydrous types are black. All other types are red-yellow-brown.
- Saxonburg, Pennsylvania
2006
A. In the coil coating industry, black rust is the oxide that forms on zincalume coated steel. It is the product of wet storage similar to white rust formed on galvanized coating. It is esthetically displeasing and if allowed to continue to be exposed to moisture will eventually result in perforation of the steel substrate
(iron oxide will begin).
For more information visit galvinfo.com.
- Kalama, Washington
2006
A. You refer to a what seems to be a coating on metal.
There is not enough information in your request to confirm that conclusion
Perhaps the reference in the document does not mean a coating...
Black rust is a component in manufacturing thermite:
from wikipedia:thermite entry:
Black or blue iron oxide (Fe3O4), produced by oxidizing iron in an oxygen-rich environment under high heat, is the most commonly used thermite oxidizing agent because it is inexpensive and easily produced.
- Lubbock, Texas
2006
Red rust is the oxidation of iron with water
Blue rust is the oxidation that occurs after you burn iron (light a match and hold to some 0000 steel wool
⇦ on
eBay or
Amazon [affil links] , be careful I'm not responsible if you burn your hand off!)
Black rust occurs when you run electricity through steel wool hook a - and a + current up to it and after it sorta burns it leaves behind black rust
Black rust is much more explosive
I don't know much about blue rust, and red rust is a much better oxidizing agent which is why it's used in thermite.
- Pville, Iowa
2006
I'm curious about the reason that black rust is the preferred rust for thermite. Is it the extra oxygen atom? I made black rust quite by accident when I was trying to get red. I simply put some fine #00 steel wool ⇦ on eBay or Amazon [affil links] in a small amount of water and let the capillary action pull the moisture up into the rest of the "wool". It all turned into very fine black rust, no other chemicals were added.
John Wagner- Bonham, Texas
August 12, 2008
I came across it as I was researching for a project. The "black rust" you mentioned may be caused by the solution that the steel came into contact with. Sulfur, sulfide, and sulfamic acid (used in construction to dissolve concrete) contain Sulfur, Hydrogen, Oxygen, and Nitrogen, all of which react with the steel to create a rust which is black in color. I am unsure of its official name, however I also know that it is common with Sulfamic acid and occurs at low pH. There are probably other instances where the "black rust" can occur, but this is the one I am familiar with.
John Reddings- Sacramento, California
2006
I'm 13 years old and I'm working on a science fair project. I encountered that "Black Rust" on mild steel which was immersed in Coca Cola, Gatorade and vinegar ⇦in bulk on eBay or Amazon [affil links] . I did some research on it. I think it's some kind of residue or salts of something. And about that lest post about the sulfur, its called "mackinawite" .
Nikki C [surname deleted for privacy by Editor]- Abbotsford, British Columbia, Canada
2007
April 8, 2008
I believe that the original question was referring to corrosion in buildings (or other structures) which is detrimental to that structure. It seems most of the replies have been hung-up on the colour, the chemical formulae, and methods of creating same.
I agree with Fred Salome as what Fred described is exactly what I found recently in an ocean-side block of home units (apartments).
As well as the marine atmosphere, this particular building had floors that were topped with "magnesite:, a fibrous topping that is self-leveling and provides a degree of sound dampening. It is a good product until water, from any source, reaches the topping. The chloride salts are leached from the magnesite and seep into the underlying concrete. At that time, the protective patina (Fe2O3) on the steel rebar is dissolved and corrosion begins.
This building has several sources of water ingress - leaking windows and doors, leaking water heaters and bathroom showers.
We identified the 'black rust' by stains (aka 'blooms') on the magnesite and then later on the concrete top surface after removing the magnesite.
When the steel bars were exposed, we fond exactly what Fred had described. The outer surface of the steel was dark gray to black, and the core was a black hard jelly like substance. All quickly turned to red rust after exposure to the air.
The bars were 12 and 16 diameter (1/2" and 3/4"). Typically the 12 diameter bars had only about a 1 mm annulus around their periphery, while the 16 diameters bars had 1.5 - 2.0 mm annuluses. That is, effectively no structural capacity remaining.
Structural Engineer - Sydney, Australia
Black Rust, without discussing the chemistry, has been a common phenomenon with bridge painters for at least a few centuries. The common terms in this industry is; Red Rust (surface rust red/orange in color). Black Rust- commonly called Pack Rust (Black/ grey/yellow in color and stratifying- Layers). You can find this phenomenon on older bridges in the North Eastern US. Common terminology Ferric Oxide -red surface rust and Ferrous Hydroxide black stratifying rust. Contact NACE International; www.nace.org and ask for a CIP level 3 instructor for more detailed information.
John Brown PE- Luanda, Angola
August 18, 2008
On a current archaeological dig in Ottawa, Ontario, many of the iron items dug have had a bright blue rust just like the toolbar & browser frame on this pc computer.
Ted Stewart- Rideau Lakes, Ontario, Canada
September 6, 2008
Black rust isn't rust but a phosphoric reaction so look that up.
William Nefr- San Diego, California
October 19, 2008
First of all this has mostly been answered correctly, "Black Rust" is not rust as most people would think, it is formed at high temperatures and is not significantly damaging to the bulk material, however it is not Fe3O4, but rather FeO. Fe3O4 is a common term denoting the what you have is not pure "black rust" but rather a combination of Fe2O3 (red rust) and FeO. Fe2O3+FeO=Fe3O4, technically inaccurate, but not all that important. What is important is knowing how much of the "black rust" is actually "red rust". Also, for the person I saw asking about thermite, FeO is better because it unstable at low (room) temperature, so it reacts better.
David McDonald- Pullman, Washington
October 30, 2009
Black rust on steel reinforcing bars in reinforced concrete structures is a sign of the onset of pitting corrosion which is very damaging. The UK Design Manual for Roads and Bridges, published by the Highways Agency describes what is happening (see BA34/90):
4.5.2 Penetration of concrete by chloride ions from de-icing salts and marine environments is the primary cause of reinforcement corrosion in highway structures. The minuscule and highly mobile free chloride ion is able to penetrate concrete through the water present in the pore structure. The passive layer surrounding the reinforcement is locally broken down, causing the anode of an electrochemical cell to form and anodic pitting corrosion to develop. The cathode may be an adjacent area of steel, or other layers of reinforcement. Once corrosion is initiated the rate of corrosion is determined by the availability of oxygen and moisture and the resistivity of the concrete, but pitting corrosion is rapid and severe local loss of section can occur. Corrosion will be accelerated in damp concrete with a high water/cement ratio and low electrical resistivity. The products of pitting corrosion may initially be black with no external visual clues to their existence. Where sufficient oxygen is available the black corrosion product turns to red rust which is expansive and can lead to cracking of the cover concrete.
The DMRB is available online, free of charge:
www.standardsforhighways.co.uk/dmrb/vol3/section3/ba3590.pdf
bridge engineer - Frome, Somerset, UK
December 2, 2009
You can also have sulfides form - but this depends on the conditions. I think more details about the composition of the metal and the conditions it is in are important. The term "iron" may be used but it might be a alloy of some sort that contains other metals.
We get 00 steel wool
⇦ on
eBay or
Amazon [affil links] to turn black in a marine environment - but it is coated with bacteria and assorted organic stuff - we know this because we've looked at it under an electron microscope and did some analysis. If someone looked at it with the naked eye they might say it was rust or black rust - and they would be wrong.
- Valdosta, Georgia
January 31, 2010
YOU GUYS NEED TO STOP AND THINK ABOUT IT. YOU'RE ALL WAY TOO SMART FOR THIS QUESTION . YOU CAN ASK ANY WELDER OUT THERE WHO HAS A SHOP -- AND THE TERM "BLACK RUST " COMES FROM THE SLANG OF SAYING . . . "USE THE OLD MATERIAL OUT THERE IN THE PILE! IT'S BLACK IRON THAT'S RUSTY! DON'T USE THE GOOD STUFF FIRST !" AND RUST ISN'T BLACK ! IT'S ORANGE / RED DEPENDING HOW LONG IT'S BEEN WEATHERED !
JOEY AJERO- VALLEJO, California
March 15, 2010
Hi, Joey. That's an interesting take on it; thanks. But the meaning of phrases actually depends on their context.
If you tell the driver of a heating oil truck that a tank is an armored fighting vehicle, he won't agree, and he will follow his delivery instructions and pump 200 gallons into a tank anyway; if you tell an infantryman that a tank is a thin sheet metal container for holding heating oil, he won't agree, and he will fire his bazooka at it if it has enemy markings :-)
So it is with "black rust". All of these helpful individuals are right about what black rust means to them ... but there simply is no stopping people from using the slang they want to use, and they'll call something "black rust" if it's a handy shorthand for them, and that's that.
Regards,
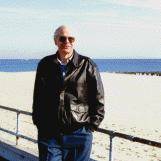
Ted Mooney, P.E.
Striving to live Aloha
finishing.com - Pine Beach, New Jersey
March 15, 2010
It is explained in electro-chemistry. The chemical composition of rust is Fe2O3. The way rust begins is when iron is exposed to air and water. as Fe2+ is exposed to water, it begins to form Fe2O3. I won't get into too much detail but the reason that it varies in color is because of the amount of H2O present during the rusting. It varies from SHADES of red, brown, yellow and black.
Andrew Lukonin- Vancouver, BC, Canada
June 1, 2010
While black rust is good for protecting steel, it is very tough and non-conductive which is disastrous to a railroad signal system.
There are usually three stages of rust. Simple Iron oxide is yellow in color, forms very quickly and is fluffy. The orange rust is a little harder. Both types are easy for rail wheels to penetrate so they make contact to the rails and "shunt" between them. This is necessary to activate signal systems and, hopefully, prevent drivers from running into trains or vice versa.
The black rust forms more slowly. I'm not sure why it forms on rails while it doesn't normally occur on other steel. The constant current flowing due to the signal detection circuits combined with the massive hammering of the steel wheels which have 20 tons of pressure on each wheel might have something to do with it. In any case, the black rust can be hard enough and non-conductive enough to "lose" trains, which can cause warning devices to fail to operate. Periodically, rail grinder need to be used in areas where there is insufficient rail traffic to keep the rails clean.
Black rust is a savior to some, but a real problem for a railroad signalman.
MCCORD ENGINEERING, INC. - OMAHA, Nebraska, USA
January 19, 2011
... Sam is interviewing for railroad signalman, and told that he & his family will live a hundred miles from civilization in a house near the tracks, where he'll maintain the switches. He is harassed by his team of interviewers:
"What will you do if the L.A.-to-Chicago and the Chicago-to-L.A. are roaring towards each other at 100 MPH each, and a switch sticks, putting them on the same rail?""Yes, but suppose sunspots block the radio transmissions?"
No matter what he says the interviewers relentlessly badger him with another
"Yes, but what if... What if ... What if ..."
"What will that fix, Sam?"
Regards,
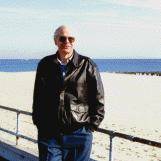
Ted Mooney, P.E.
Striving to live Aloha
finishing.com - Pine Beach, New Jersey
Hi - nice to find a site on the internet where contributors don't feel the need to be rude to each other! Very interesting thread.
Anyway, my input: I collect swords (c1750-2000) and rust is, naturally, a major enemy. Blades from this period are, of course, steel (of differing qualities) and the rust which attacks them is, to a chemical layman like me, reddish brown (usually) or, occasionally, black. In my area of interest I see them in this way: red rust is aggressive, and needs stabilising/clearing quickly, but is usually confined to the surface; but where I find "black" rust it tends to be associated with smaller, localised areas, and often causes/has caused pitting which can be quite deep, when compared with the nearby "bright" areas of the blade. Careful polishing can remove both types of rust to an extent, but black rust seems to leave cloudier/deeper damage, and lurks menacingly in the pitting where I cannot get at it. This seems to contradict the idea that it is a stable, benign form, although this may simply be because the damage has already been done, or it just looks "black" to me?
So, given the thread above (including references to heat, not present in my case), can black rust be a natural progression from untreated red rust, or are we talking about different circumstances/steels attracting different types? (The black rust and consequent pitting I am currently treating is on the blade of an early C20th British Army Highland Officer's Broadsword, which has been stored inside its wood lined leather scabbard).
Sorry if I'm not adding much, but I am interested. Best wishes.
- Derbyshire, England, United Kingdom
June 22, 2012
Q. I also have interests in swords. In this forum thread: www.vikingsword.com/vb/showthread.php?t=14263&page=3&pp=30
I found discussion of "reactivation of the ferric oxide in the carbon environment"
The photos show the metal in the white, with all corrosion transformed or removed.
Can someone explain how this is accomplished?
- Kingston, Ontario, Canada
November 8, 2012
A. A good friend sent me this D-I-Y method
www.atocha1622.com/electrolytic_reduction_process.htm
- Kingston, Ontario, Canada
November 9, 2012
Q. Hi,
Has anyone been able to remove black rust from sheet metal?
Thanks!
- Victoria Texas USA
January 21, 2013
A. Hi Katherine. Certainly it can be sand blasted or sanded away ... but I'm not sure that I'm really understanding your question.
Regards,
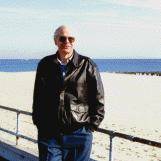
Ted Mooney, P.E.
Striving to live Aloha
finishing.com - Pine Beach, New Jersey
January 23, 2013
Q. My concern is with the color of stain on asphalt shingle roofing. I had a roof with 4 angle iron supports mounting a baked finish chimney surround, topped with a rusted cap. Said roof developed a significant black stain, which everyone in these parts attributed to the old, extremely inefficient oil burner (<50%!): unburned hydrocarbons. I replaced the burner with a high efficiency unit, and had the roof re-shingled several years later. Within 10 days of the new shingles going on, a reddish orange stain appeared, roughly, but hardly exactly in the same area as the previous stain. I attribute this stain to the angle-irons and inadequate flashing, or the cap. The baked-finish metal was and remains visually intact, inside and out.
Thoughts?
- Rockport, Massachusetts, USA
January 23, 2013
A. Hi Jeff, based on your description of the condition and the parts of the chimney, I would suspect that the rusted cap is doing just that, rusting. If the material is predominantly iron (Fe) on the cap, any moisture will continue to contribute to the rusting of the iron until it no longer exists. When the moisture stops, that's when the rust will stop. Exposed edges of the painted sheet metal will also corrode once the galvanized coating is consumed since the galvanized coating is on steel (mostly iron) substrate. If the cap is in fact steel, getting the rust off of it and painting it will most likely correct the staining for a while (that may need to be done annually). Also paint the edges and any exposed fasteners and brackets.
Gary Preisendorfer- Birmingham, Alabama, USA
October 4, 2013
!! People don't realize that rust exists in two basic forms, Free and Reactive. In the Free state it is easily removed by sanding or rust conversion products; but in its reactive state rust has achieved an electrochemical bond with the metal surface. In extreme cases black rust is formed. Black rust (magnetite) can be a thick hard scale which usually forms in a harsh chemical environment where high concentrations of chlorides, sulphates, and nitrates are present. Removing rust in its free state usually involves simple sanding or the use of rust converter ⇦ on eBay or Amazon [affil links] s, but in its reactive state more extreme measures are required. When reactive rust changes into black rust, high pressure sandblasting is the only removal method available. In any case, after removing reactive rust a wash down using various chemical detergents is needed to remove chemical residue, or premature paint failure will occur.
Jim Deardorff- Chillicothe, Missouri
March 19, 2014
Q. I also wish for an explanation of black rust.
I had a 97 Toyota Tacoma that was bought back by Toyota and sent to the crusher. These trucks were prone to severe frame rust in northern (salt using) states. I found a picture on the internet of a Toyota truck that broke in half when placed on a lift.
Before turning the truck in, I had it inspected by a frame restoration shop. While beating on the frame with a hammer, they knocked a piece out of the frame. It was 1" x 2", had factory finish on both sides, and was only slightly thicker than original steel, perhaps 50% thicker. (standard steel corrosion is supposed to expand like 8 to 10x) The piece had converted to black corrosion, and could be snapped with my fingers. The corroded piece was solid and did not have layering. Interestingly, someone on the web posted that Toyota literature at the time boasted of enhanced corrosion resistance.
I am currently attempting to repair my wife's 2000 Camry. The steel in a couple spots under the windshield corroded into black corrosion. The increase in thickness caused the windshield to break. The stuff is a dense thick layer that requires quite a bit of grinding to remove. It appears that this corrosion product wicks moisture and causes the corrosion product to advance under the paint. I don't now what causes this steel to corrode this way but sure would be interested in an explanation.
It would appear that steel that corrodes this way is insidiously dangerous when used in structural components.
- Columbus Ohio USA
April 26, 2014
December 12, 2014
Q. Came upon this thread while researching black corrosion in a Pontiac engine cylinder. The engine sat about 10 years in a "dry" garage (humidity would be present). 7 cylinders had "typical" red surface rust where the cylinder wall was exposed - this came off with light 320 grit sanding - when the crankshaft was rotated/piston moved in cylinder, the bore was smooth with no rust where the piston had been covering it for 10 years.
One cylinder was different. From the top of where it had been positioned in the bore, and down about 2" (in a rough upside-down triangle pattern) was black corrosion. I assume some liquid was on the top of that cylinder, leaked down past the rings, and caused the corrosion. The corrosion is fairly soft, similar to red rust, and leaves heavy black deposits (no red at all) on the sandpaper - it seems thicker than the red surface rust. It also seems to have stained the cast iron - at edges, I can sand it until smooth, but black remains. I assume antifreeze was on top of the cylinder, leaked past rings, and caused this - there could also be some sulfur content (maybe?) or other contamination/elements from oil/carbon deposits on top of the piston. A major point is it wasn't exposed to much oxygen/humidity below the piston because other cylinders were still shiny metal below piston tops (I think reduced oxygen is required to produce Fe3O4).
So far I've read: this could be FeO or Fe3O4 - I can tell difference by hitting it with a flame: FeO will turn red (I'd do this with sanded particles away from the oily engine block). The only way to get rid of Fe3O4 is to bead/sand blast it.
Questions:
1) does this sound like Fe3O4?
2) can it "soak" deep into the metal?
3) will acid dissolve it (or really do need to blast it)?
4) will it be hard enough to run (not break down as time goes on) in the engine even though it stains the iron?
Any other info/input is appreciated. Very interesting topic.
- St. Louis, Missouri USA
A. FeO isn't likely to form in such conditions. Normally FeO only forms at high temperature (about 800C if I remember right) in air. Most commonly this is called "mill scale" from the steel hot rolling process.
Fe3O4 is more normally found in nature as iron ores in mining and sometimes as sand on beaches, where its black sand with high Fe content.
I suspect your "black rust" is some other compound containing more than just Fe and O. Possibly C, or Mn ?
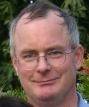
Geoff Crowley
Crithwood Ltd.
Westfield, Scotland, UK
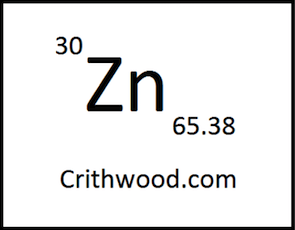
December 12, 2014
Q. Thanks Geoff. So it's not FeO (maybe FeO is the black powder that gets on hands when handling hot rolled steel).
Not sure what other elements would be in the black cylinder corrosion -- carbon on piston was present. Other elements would be those found on top of piston (whatever's in burned motor oil, unburned hydrocarbons from gasoline, etc.) and in antifreeze (generally drains/sets on piston when cylinder head is removed [maybe is why I had a gut feeling to clean this out of cylinder]).
1) Do you think muriatic acid would dissolve the corrosion to metal?
2) Do you know if the black stain would affect the integrity of the cylinder (assuming the acid or blasting removes the deposit)?
3) Then, if acid cleans it, is there a danger of the acid seeping into "microcracks" (causing other problem, if these are reason for staining that doesn't sand off) which would be less affected by blasting (microcracks remain but don't matter during engine operation)? Of course the acid would be neutralized with baking soda [in bulk on
eBay
or
Amazon [affil links]
solution, but acid may soak in further than alkali solution(?).
- St. Louis, Missouri USA
December 13, 2014
A. Hi Chris. Whatever it is, mechanical removal (grinding/sanding/blasting/buffing/honing) sounds more promising than chemical removal. Using hydrochloric acid, which corrodes metal (and can be dangerous) on some black material of unknown composition, may corrode the cylinder while being harmless to the stain anyway.
Sorry, I don't have any worthwhile guesses of what it might be.
Regards,
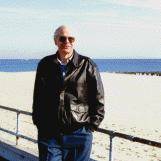
Ted Mooney, P.E.
Striving to live Aloha
finishing.com - Pine Beach, New Jersey
December 2014
I came upon this forum while trying to find a solid method of removing what is definitely rust, definitely black, and definitely a huge pain in my backside. Our victim is the roof structure (rail) of a 1974 Dodge Challenger. This is above the area where the drip rail or trough is spot-welded to the structure; the roof panel itself is welded to the drip rail. The area shown is never seen on a car unless the roof panel has been cut off, but it does not contact the roof panel. There's a slight air gap.
This is a Montgomery, Alabama car its whole life. It has not been exposed to road salt or life by the sea. Other than being part of the chassis and therefore the ground plane for the electrical system, it has seen no current. It was painted black but I highly doubt even the AL sun got it hot enough to catalyze it. This corrosion is severe, and 125 PSI of air pressure pushing crushed coal slag is having very little effect on it.
For the average Joe, as the original poster's subject most-likely was, this is what "black rust" means.
Pierre Payant- Kingsford Michigan USA
March 29, 2015
! I'm fairly sure that I have black rust on the 1st steel sword that I bought
about 8 yrs ago. As for how, I believe it was due to the citric acid that got onto my blade, when my friends, & I used to pitch lemons to each other, and cut them in 1/2 with our swords. I was the only 1 with a steel sword, so sword maintenance was never taught to me. Well, I had my fun with it, cutting lemons in 1/2, clearing pathways with it, & testing its edge. Eventually, I put it in its scabbard, & let it be. Then about 3 yrs ago I found a website in the U.S. that sells Filipino swords. All of them have real Filipino Ironwood handles, & full tang blades, made with steel blends of 5160 and D2. Anyways, it took me awhile, but I finally know how to keep my swords from rusting. Still, I might have my sharpener take a look at it. If the rust is only on the surface, maybe he can clean it up for me.
- El Cajon
May 4, 2016
A. Black rust is necessary for an effective brass iron battery. It will have a life span of about 30 years and performance of an Edison or a lead battery.
John scheel- Ontario, Canada
April 25, 2017
May 6, 2017
Q. Good day.
I have read all the questions and answers in this topic of "black rust" and have found it all most interesting!
I have a particular problem.
I recently purchased a 1960 VW Karmann Ghia, with a badly rusted roof. Part of the area is what I would agree as being "black rust".
I have done the usual sanding with a wire brush (on a drill), and have tried various rust and paint removers, but with no luck!
As the rusting is pretty severe, I don't want to grind down to clean metal, as I'm sure that the roof will be weakened to the point of no return.
If at all possible, I want to chemically remove the black rust and preserve as much metal as possible.
I therefore have two questions for this illustrious panel of experts to please answer:
1. What chemical compound will I have best results with to remove the black rust?
2. Will I be able to effectively prime, fill and paint the roof, if there is still a black appearance?
Responses will be most helpful.
Retired engineer. - Johannesburg, South Africa.
Hi Barney. Questions about priming, filling, and painting classic cars have drifted pretty far from the topic of "What is 'black rust'", and probably a number of the 60,000 threads on this site are closer to the mark, but we'll see if other enthusiasts follow the same path you did to get to this thread, and whether they have advice for you. Good luck.
Regards,
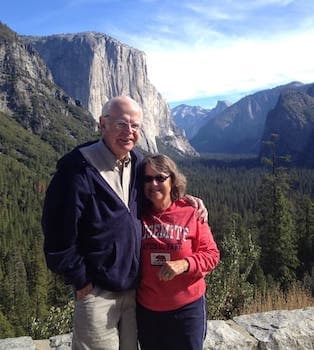
Ted Mooney, P.E. RET
Striving to live Aloha
finishing.com - Pine Beach, New Jersey
May 2017
What is black patina on old woodplane?
Q. I'm restoring hand planes. In the process of wooling one off with 0000, there was this beautiful black patina that the wool didn't remove. The same happened on the iron, which is tool steel (non stainless). I usually sand them down to bare metal and try to achieve as new as possible of a look because of all the ones I bought, the aged look they had looked more like an abused thing than patina. I was very happy with my progress restoring them to look as new as possible. But this one quickly became my favorite as it almost looked like someone lovingly cared for it and the patina so it would all be evenly spread like a coating. It is very thin. It did have a build up which was sticky feeling with the wool but as I cut through that thin layer of very tough dark greyish blackish patina surfaced. With some 3-in-1 oil applied it gave it a little shine and it is just gorgeous. And I can tell it is durable and no rust will ever form there. I would like to know how long it takes to get this naturally and what conditions would bring on this oxide rather than the harmful red orangish stuff that always pits if not caught soon enough.
Chuck Panno- Menifee California USA
April 14, 2018
A. Hi Chuck. My feeling is that this is not a 'natural' patina; rather that the manufacturer 'black oxided' the parts back when they were manufactured. You can see this on many drill bits, hacksaw and jigsaw blades, allen wrenches, socket sets, gears & sprockets, power transmission chain, etc., as well as on gun barrels. We have a dozen or more threads about the black oxide process if you use the search engine, but basically the parts are immersed in a vat of boiling hot caustic and nitrates which build that extremely thin black finishing on them
I think you are right that the parts won't rust, but only if you keep them oiled.
Regards,
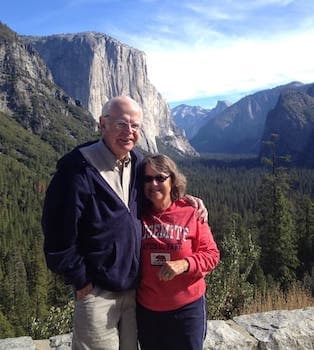
Ted Mooney, P.E. RET
Striving to live Aloha
finishing.com - Pine Beach, New Jersey
April 2018
Q, A, or Comment on THIS thread -or- Start a NEW Thread