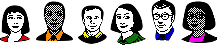
Metal finishing Q&As since 1989
-----
Masking electroless nickel for hardcoating
Q. I've printed this question before, and not had any response. I know there simply HAS to be a masking product out there that will adhere to Electroless Nickel plating well enough to withstand a 2 mil hardcoat process...will someone please point me in the right direction? I've tried many different products, along with different preparation techniques, and had failure, after failure..someone please help me before I commit harry-carry!
p.s. Most tapes will not be an option due to the complexity of the part design
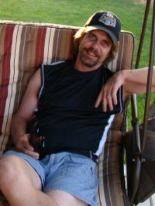
Marc Green
anodizer - Boise, Idaho
2001
A. OK this should be non-commercial but I cannot say the product without saying where it comes from - sorry.
T5145 lacquer fron Turco
We have had a lot of success with this product.
Try application by dip 3 - 4 coats.
To stop it going where you don't want it paint a mixture of zinc oxide
[affil links] and glycerine.
Allow to cure and cut back with a new razor sharp scalpel.
pumice [on
eBay or
Amazon] the areas to be treated to get a good water break free surface (hope you don't have to do thousands).
The best bit is the removal - thick coats are peelable.
Try a sample it should work well.
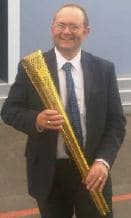
Martin Trigg-Hogarth
surface treatment shop - Stroud, Glos, England
A. The best that I found was Super XP 2000 from Pyramid Plastics in Hope, AR. This requires a low temp "bake" to cross-link it. Use the recommended temp or it is slow to cure(low)or it is tough as alligator skin (high). They were working on an acrylic latex that had to be cross linked at a higher temp, but it eliminated the solvents.
Remove by soaking in boiling water for a few minutes and peel it off.(Makes it pliable) Don't use it of rough surfaces like sand castings or you will never get it all off, even with solvents.
- Navarre, Florida
2001
A. Depending upon the configuration of your part and the area to mask,(I.D/O.D) , heat- shrink tubing(polyolefin) has worked for me in the past.
Richard Newman- Frankfort, Illinois
2001
Q. Martin and James,
Thanks for replying, and giving me advice. James ... I have tried the Super XP 2000 product, and didn't have much luck..perhaps there is a special preparation technique to the EN plating prior to applying the maskant? If you have a moment, please explain the phrase "cross linked". I did not bake the product. I just let it cure naturally over a 24 hr period of time. The stuff peeled off so readily after curing overnight, that I didn't even bother trying to put it through the anodizing process. Today I will try curing it in the oven, and see if I have better success.
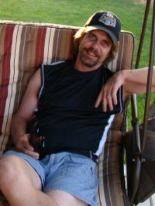
Marc Green
anodizer - Boise, Idaho
2001
A. Try Henco blue spray mask. I use it on electroless nickel, black oxide.
Will Sanders- Santa Monica, California
2001
A. In the process of phasing out my wax tanks, I came across product called Microstop from Tolber Corporation as stop-off lacquer. It worked for me.
Balaji Mandulapalli- Miami, Florida
2001
A. I have also had good luck with the Super XP 2000. On critical jobs we have found that putting numerous very thin coats with ample drying time in between coats helps. If possible try bead blasting the surface you want masked with a very fine glass bead. This will roughen the surface very slightly for some mechanical bond.
Rick Richardson, MSFDayton, Ohio
2001
![]() |
Regards, ![]() Ted Mooney, P.E. RET Striving to live Aloha finishing.com - Pine Beach, New Jersey February 2019 |
Multiple threads merged: please forgive chronology errors :-)
RFQ. We are in need of getting both anodize and electroless nickel operations performed on the same piece, so it will require a good deal of masking. The finish on the electroless nickel area will be critical.
Teddy M [last name deleted for privacy by Editor]- Blacksburg, Virginia
January 14, 2012
Ed. note: Sorry, this RFQ is old & outdated, so contact info is no longer available. However, if you feel that something technical should be said in reply, please post it; no public commercial suggestions please ( huh? why?)
Q. I'm designing aluminum parts where I require some areas to be anodized and others to be Ni plated. These parts have rather complex geometry but are small (approx. 1"-3" size). The purpose of the anodization is cosmetic and environmental protection, the Ni is electrically conductive and provides a good wear surface for threads and a sealing surface (the threads are used repeatedly during service)
Previously parts have been made like this with anodizing and electroless Ni. This was very expensive apparently requiring two different difficult masking steps. I'm looking for an alternative. I can't change the anodizing, the Ni could change if something better exists, we have tried replacing it with Alodine but it didn't stand up to repeated matings of the threads well.
My first thought was to replace the electroless Ni with electrolytic Ni. The anodizing could be done first with the Ni areas masked then with the masks removed the electroplating would only occur in the bare metal areas. This saves the most difficult masking step but I'm not sure if it is practical.
Any thoughts are appreciated
- Madison
November 16, 2012
A. If the threads getting worn are your main problem here, my suggestion would be to use a STI tap, Alodine/anodize (have your coater mask the threads), and then install the appropriate size helicoil insert AFTER anodizing. An insert would give you much better thread life, plus could be replaced should the need arise.
Plating/anodizing threads typically is not a good idea, especially aluminum ones.
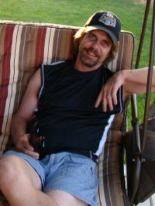
Marc Green
anodizer - Boise, Idaho
November 21, 2012
Q. Thanks but I should have mentioned. The threads in question are ~0.75" non standard acme threads so I really can't use a helicoil. I could perhaps make my part out of two pieces I'm not certain the added cost/ complexity would compensate for the reduced masking required.
M. Martin- Madison, Wisconsin
November 21, 2012
Q. My challenge is we are nickel plating, using [a product mentioned above] to mask off a certain area. My challenge is this stuff is MEK based, costs a lot and costs a lot to dispose of.
My question-is there something out there comparable to this that is NOT MEK based?
Thanks for any relies.
- Plymouth, Michigan, USA
December 6, 2012
Is anodize and nickel plating possible on the same part?
Q. We have an order for some prototype parts that will be made from aluminum, (probably 7075-T73), which the customer wants anodized red (no problem so far) ... but then one face of the part needs to be nickel plated. Can anyone help me out here?
Thanks,
Ralph
R&D Scientist - Milford, Connecticut, USA
January 8, 2016
Hi Ralph. The semi-conductor machinery industry employs parts that are partially anodized and partially electroless nickel, so it's widely done, and I've seen such parts. But lacking hands-on experience with it, I'll let someone else suggest the most practical masking sequence and process sequence to get there :-)
Regards,
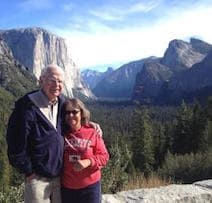
Ted Mooney, P.E. RET
Striving to live Aloha
finishing.com - Pine Beach, New Jersey
January 2016
A. Hi,
I've seen one of those too. Aluminum spools for gold wires.
First, the inside measurement of the spools were machined to size, the outside to be machined later. Electroless nickel plate the whole spool ... then machine to size the outside of the spool leaving the inside electroless nickel plated.
Mechanical seal the inside of the spool leaving the outside bare aluminum to be anodized.
End product is an aluminum spool electroless nickel plated on the inside and color anodized on the outside.
- Penang Malaysia
January 13, 2016
A. Ted is correct, this is quite common on components used in the semiconductor industry, Typically, the part will be anodized with the area to be nickel plated masked. After anodizing, the masked area will be selective Ni plated.
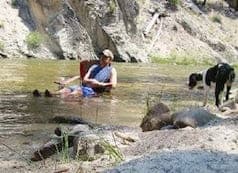
Marc Green
anodizer - Boise, Idaho
January 16, 2016
Q. What is the best approach and process to put a hard anodized finish on an aluminum as well as e-nickel plating? We have complex parts we need both finishes on and need to be able to control the masking process in house. We are not sure in what order to do the process as well as which type of masking application would be best. Thank you.
TJ Swope- Lexington, Kentucky, United States
April 19, 2018
A. First mask area to be electroless nickel plated with [peelable maskant material with high temperature resistance]. Anodize the part, strip the maskant in acetone
[on
eBay or
Amazon], than apply [peelable maskant material with high temperature resistance] over anodized surface and plate electroless nickel.
Be sure to chemfilm the whole part prior to any masking.
This works every time
Danco EN - Ontario, California USA
February 25, 2019
----
Ed. note: Thanks for the instructions, Vijay. Readers, we no longer post recommendations of specific brands & sources (why?)
Problems masking for anodizing plus electroless nickel
July 12, 2019Q. I am new working with ENP, I am a masker, and today a job came back because of "paint" on edges. This is a VERY porous aluminum small part that has 3 masks. Green stop off is the mask I use.
Step 1).
Chem film
Step 2).
Green paint and then type1? Anodize
Step 3).
Mask two ends w/ green tape, dip several coats paint,
Cut out both ends, paint touch up to edges, black light check. TWICE, then ENP
Then put in a stripper to remove paint.
..,........
It is NOT paint from my masking, but dark streaks near edges, that are present. It cleans off on some areas, not on others I was thinking to try a Sonic toothbrush, to see if it can clean out pores.
I'm prepping them to be blasted and worked again.
I'd love to not HAVE to do that!
Does anyone recognize this description?
Thank you
Masker for ENP - Phoenix Arizona
A. Jennifer, it may help to solve this issue if you post a pic of the "paint streaks".
That being said, I believe you have this process backwards. Generally anodizing is performed before conversion chem films (i.e. Alodine) are applied. This may be part of your problem. Additionally, the electroless nickel solution is a high temperature application (180-200 °F) that could be in appropriate for the masking used.
To strip the anodic coating usually a highly caustic mixture is used and mid- or high-phos EN does not do well in highly alkaline environments.
Im sorry I don't have a better answer then that, but those are the things going through my head with the limited amount of supplied info. Any additional pics, pretreatment processes, operating parameters of each step, and masking used help in this troubleshooting process.
Technical Sales Rep - Cleveland, Ohio
July 30, 2019
A. I'm going to add to Isaac's statement here. In most cases, the chem-film process is generally done prior to anodizing, and it serves as an excellent adhesion base for the "Green" paint masking. And also, if the print allows/requires chem film on areas without anodizing, you don't have to mess with trying to chem film on anodized part.
As Isaac mentioned, a picture would be really helpful here.
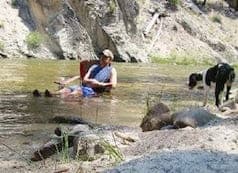
Marc Green
anodizer - Boise, Idaho
August 3, 2019
Q. Hi folks,
I'm trying to determine if you can electroless nickel plate directly over anodized aluminum. I have an application that requires a part to be half anodized and half nickel plated, and I'm wondering if I can simply anodize the whole part and then nickel plate over the anodize in the required area. I'm worried if I have to strip the anodize it will leave a seam that could promote corrosion.
I know electroplating requires a conductive surface and would be incompatible, but if electroless can be applied to plastics, is there any reason it can't be applied over an existing anodized surface?
I would prefer to use a low or mid phosphorus mixture because I need the nickel coating to be magnetic.
Thanks.
Aerospace - Wichita, Kansas, USA
September 4, 2019
A.
I'm not aware of an instance where nickel has been deposited on a anodized surface. Yes, nickel is often plated over non-conductive plastics, but that process was developed many years ago, and it was not simple.
It would be a development project of unknown complexity.
Why you cannot use masking and selective plating/anodizing, I don't understand.
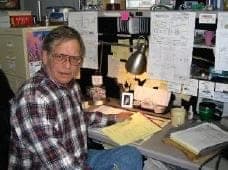
Jeffrey Holmes, CEF
Spartanburg, South Carolina
September 8, 2019
A. Thanks Jeffrey! I don't think Joshua is opposed to conventional methods; we appended his inquiry to this discussion, and he probably wasn't quite aware of how the issue is conventionally handled.
Regards,
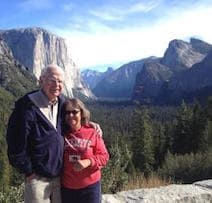
Ted Mooney, P.E. RET
Striving to live Aloha
finishing.com - Pine Beach, New Jersey
September 2019
A. Not sure if it would work but as far as I know nickel plating on plastic is done by filling the pores* with palladium and then using those spots (of palladium) to begin the plating process.
If you don't seal the anodizing layer maybe you could fill the pores* with palladium and plate from there?
To be clear - I'm just theorycrafting -- have no idea if it would work.
Think it's a very interesting topic! please come back if you find a solution!
*I'm not 100% on the english term for micro holes in an anodizing layer.
Also this is my first post, hopefully I didn't violate any rule.
Provexa AB - Gothenburg, Sweden
October 3, 2019
Thanks Eric, and welcome.
We like to think that by the time people use the site a while and fully understand how it actually works, they will feel no pressure of "rules" other than common sense -- but if you get a different vibe, let us know and we'll try to fix it :-)
Regards,
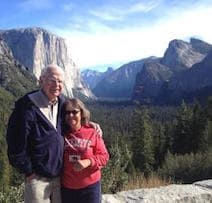
Ted Mooney, P.E. RET
Striving to live Aloha
finishing.com - Pine Beach, New Jersey
October 2019
finishing.com is possible thanks to our supporting advertisers, including:
Q, A, or Comment on THIS thread -or- Start a NEW Thread