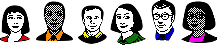
Metal finishing Q&As since 1989
-----
How To Remove Oxide Film on Titanium Alloy?
Q. Hi experts,
My trouble is quite specific, but I rely anyway on your help!
Try to imagine a complex shape part made in Titanium alloy (6Al-4V, B348 gr.5). It has an extremely polished surface, very very smooth, in spite of its complex geometry. Due to a previous electrochemical process (no way to modify it), it results anodized. Its color ranges light brown to golden brown.
Hard to believe: I need to remove most of this anodic film, restoring Titanium to its original silver appearance! Obviously, I need to avoid any damaging/modification (both morphological and chemical) of the polished surface; That's why any mechanical approach (tumbling, brushing, sanding and similar) appears to be unfeasible.
Are we dealing with science fiction?
Thanks in advance,
Giovanni Righini- Italy
2001
A. Giovanni,
You can use solution: Chromium oxide (CrO3) - 100g/l Hydrofluoric Acid 40% - 20ml/l. Rinse in this solution until stains disappear. You can also try electropolishing titanium in salty solution. For more information contact Dan Weaver at Global Stainless in Georgia.
Good luck.
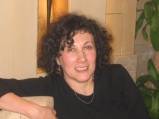
Anna Berkovich
Russamer Lab

Pittsburgh, Pennsylvania
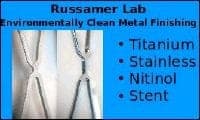
2001
A. What if you etch your part carefully, I mean etch it just enough to strip the oxide film off? Do you think your part will loose the shine?
Mark Camilleri- Malta
2001
A. I think that a room temperature dip in nitric-HF acid will do quite nicely. Time and concentrations are important. Ratio needs to be about 14 to 1 and not lower than 10-1 or it will eventually pit, possibly from tramp ions.
James Watts- Navarre, Florida
2001
Q. Dear friends,
Many thanks to all of you for your help. I really appreciated it. At the moment I'm testing an acid mixture HNO3-HF characterized by a very very low ratio, about 60 to 1, otherwise the brightness of the polished surface is lost (etching of the surface, resulting in a "butter finish" appearance). This ratio seems to be promising, also if time is still a critical parameter.
Thanks again,
Giovanni Righini [returning]- Italy
2001
A. The time is not so critical, but for us one minute was sure enough.
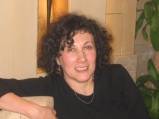
Anna Berkovich
Russamer Lab

Pittsburgh, Pennsylvania
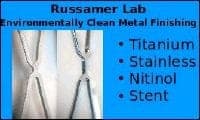
2001
Q. Hello,
This question may seem out of left field, but I can't find anyone in physics or electronics that has any experience in this kind of etching! I am attempting to etch off the thin film of titanium dioxide that has formed on small samples of titanium coated glass. The titanium has been deposited on the glass using a sputtering technique, and is only 1 micrometer thick. We've annealed the samples up to high temperatures (700 °C) in air, but this significantly increases the thickness of the titanium dioxide layer (maybe 100 nanometers thick?).
I need to find a way to remove or decrease the thickness of this oxide layer WITHOUT damaging the titanium film underneath. I've tried using HF solutions, but no matter the concentration, the etchant just seems to eat holes right through the whole titanium film, and not uniformly remove the titanium dioxide.
Any suggestions for etchants would be greatly appreciated!
Thanks,
Mark
student - Vancouver, British Columbia, Canada
June 1, 2011
Q. Hello,
I am working on hot salt stress corrosion cracking of Ti-64. During high temperature exposure (450 C) in presence of salt, it forms titanium oxide layer which contains salt also. I unable to clean this layer on fracture surface which I need it for fractographic analysis.As per literature I could able to clean it for lower temperature exposure (say up to 400 C) by using boiling nitric acid but for higher temperature I failed to clean. It will be great if you can give me the remedy for this.
Thanks & Regards
- Bombay, India
March 13, 2012
A. I've removed Oxide from Titanium in a High Vacuum oven at 500 °C for 30 mins.
Mike Jansen- Clarence, New York
November 18, 2012
Q. Hi
We poured a Ti-45%Al intermetallic in a VAR Furnace. After that we homogenized our alloy in a tube furnace for 16 hours with Argon atmosphere (99.999% purity) at 1100 °C. But a dark black layer was produced on the surface after homogenization that is probably Ti oxide. What should we do for removing this layer? By grinding it can be removed but it takes time. Any solution?
PhD Student of Material science - Tehran, Iran
September 6, 2017
December 17, 2017
Q. I was given the following volumetric formula of a solution for oxide removal from titanium:
25% DI water
25% Sulfuric acid
50% Nitric acid
120 g/L Ammonium bifluoride
It cleans and whitens the titanium beautifully, but (as the first question in this discussion asked) how do I know it doesn't damage/modify (both morphological and chemical) the surface?
Does anyone used/read/heard about such a composition?
- Petach Tikva, Israel
Q, A, or Comment on THIS thread -or- Start a NEW Thread