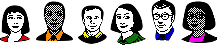
Metal finishing Q&As since 1989
-----
Powder Coat as a Corrosion Inhibitor for Automotive Product ?
2001
I am a small manufacturer of custom aftermarket automotive products. I have a problem with corrosion on a part that I manufacture.
Basically, I have carbon steel tubes welded to an automotive transmission pan. The pan seems to have a Zinc coating as delivered from the factory.
I have used a simple Hi-Heat anti-rust aerosol paint to coat this assembly -- after the welding process. The surface is sandblasted and cleaned PRIOR to the welding. The pans seem to NOT rust, in mild climates where Road Salts are not used.
But ... My Eastern customers are seeing a fair amount of rust -- both at the welds AND on the steel tubes. BOTH the welds and the tubes are coated with the aerosol Anti-Rust product.
I have been told by one local plating shop to consider Thermoset Powder coats -- with a Zinc Chromate under coat.
The coated surface of the pans will be subject to 200 F degree continuous with a brief exposure to 275 F degree on an intermittent basis. Road salts are frequently splashed onto the heated pan surface in the winter months.
I would greatly appreciate feedback from those experienced in coatings/methods to suggest a process for coating this product to minimize corrosion ?
Bob Weiland- Tucson, Arizona, USA
We use powder coatings on the road salt spreaders we manufacture and have yet to have any coating failure complaints on our powder coated products. Steel shot or sand blasting followed by a iron phosphate wash and rinse typically gives us 750+ hours of salt spray with vitually no creep.
Good Luck.
Chuck Stairs- Rockford, Illinois, USA
2001
I agree that blast, iron phosphate and powder will give good results. For enhanced salt spray, try blasting, zinc phosphate and cathodic electrodeposition as a primer and then topcoat with the powder.
Scott Whitehurst- Holland, Michigan, US
2001
Q, A, or Comment on THIS thread -or- Start a NEW Thread