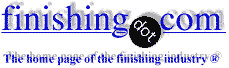
-----
Microsection vs. XRF Method for Plating Specification
ACRONYMS:
XRF = X-Ray Fluorescence
Q. I have a plating problem determining the thickness of copper plating and tin plating over a brass base material. My supplier has evaluated the platings via XRF and say they are in specification. I have evaluated the platings via microsections on a microscope per ASTM B487. My readings show the platings not to specification. My question is what technique has the better accuracy and precision? I believe the microsection technique is more accurate and precise. I do not believe that the XRF technique is capable of giving accurate and precise readings and since it is non destructive, no one will be able to see the plating layers to ensure that all the plating is within specification. I would appreciate a response and any references that I could look up to either support or not support my position.
Larry Akre-Minneapolis, Minnesota
2001
A. Microsection is the referee method in all cases of plating thicknesses within the resolution of the light microscope, very thin layers, say 0.00010" or so, may need electron microscopy. You don't have to argue the calculation or theory, when you have a photograph in front of you. I assume that you are talking about plating thickness when you say "specification". Minimum plating thickness is easier to argue, since you tend to overestimate the thickness if the section is not perpendicular to the plating.
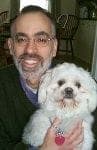

Tom Pullizzi
Falls Township, Pennsylvania
2001
A. I agree that microsection is the referee method, but I must emphasize that the technique is important. In cases of dispute, it would be normal to have the sections prepared by a disinterested third party.
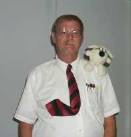
James Totter, CEF
- Tallahassee, Florida
2001
A. Larry,
The misreading from the XFR measurement could be a calibration problem with XRF machine.
1) Is the Base material used for calibration the same as plated sample?
2) What reading accuracy are you controlling at ± 10 to 20% between Cross section to XRF?
Jim Goo- Singapore
2001
2002
ACRONYMS:
PCB = printed circuit board
I come from a PCB fabrication background and in my experience a well prepared microsection gives an almost gospel account of the specimen problems and potential problems that even a well calibrated XRF may never detect. Having said that, poorly prepared microsection specimens can also give false information, e.g., signs of delamination, cracking and smearing can also be signs of poorly prepared specimens as well as potential real problems. Try mico-etching the microsection specimen; this will show the different plating processes under the microscope and, using a well calibrated VMS measurement system connected to the scope, measurement of all layers is possible and thus accurate readings are possible.
Graeme Cooperwaite- Sunderland, England
All the different types of thickness measurement machines
Q. Please send the details of various type of coating thickness measuring machine along with the quotation.
Zaki Ahmad- Pune, India
A. I recommend FISCHERSCOPE using the X-Ray Fluorescence test Method.
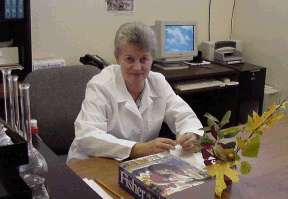
Benigna Skorobogatiene
electrical components mfgr. - San Jose, California
A. Hi Zaki. There are dozens of measurement techniques other than XRF, ranging from calipers, to magnetic "banana" gauges, to eddy current, to coulometric types which measure the time to electrochemically dissolve the coating. Thickness measurement machines can be of destructive or non-destructive type; they can be for use on magnetic or non magnetic substrates, and conductive or non-conductive substrates; the coatings can be magnetic or non-magnetic, and conductive or non-conductive. Very thick coatings can be measured with a micrometer whereas thin coatings cannot. Some methods work on pinhead size areas or smaller, some work only on relatively large flat surfaces; and of course the cost can range from the better part of a hundred thousand dollars down to promotional give-away items.
If you can tell us the particulars of the proposed application, people can probably provide two or three reasonable alternatives for you to consider. But a generic answer to a forum posting will not be sufficient to turn me into a thickness measurement expert, able to select the most appropriate method for every possible case, nor you either. Good luck.
Regards,
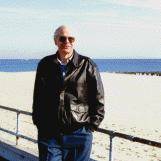
Ted Mooney, P.E.
Striving to live Aloha
finishing.com - Pine Beach, New Jersey
December 2013
X-ray thickness measurement of copper-nickel diffusion layer
Q. I have been asked to assist a plating company with a problem concerning measurement of multiple coating layer thicknesses - Bright Nickel over Bright Acid Copper over steel panels. The panels are formed from steel sheet approximately .062" thick. The plating call-out is minimum .0001" thickness for both copper and nickel, no maximum specified. Plating thicknesses are held as close as possible to minimum however, to preclude assembly problems.
The problem being experienced is: X-ray measurement gives a large variation in readings, while sectioning shows no distinct boundary between the copper and nickel coatings. The total thickness of the coatings exceeds the .0002" minimum.
Can X-ray read coatings this thin accurately? Is there a diffusion layer that can cause erroneous readings? Does anyone know of literature covering this subject?
Alan Cooper- Dallas, Texas
ACRONYMS:
ROI = region of interest,
FP = fundamental parameters
A. If the x-ray you're using is a older ROI based machine, there might be some problems but if it is a FP based machine the application is simple even that thin. Depending on your x-ray, there will be a limit to the thicknesses you can measure. If the Ni reaches about 500 - 600 µin, a simultaneous dual measurement might not be possible.
Jeff Vernier- McKinney, Texas
A. With your coatings being thin, you should also check your XRF device to see if it has mechanical filtering available as well as numerical filtering. Since you are trying to measure two elements with overlapping spectra you need to effectively separate the Ni from the Cu. The mechanical filter will minimize the effects of the underlying Cu. Then the numerical filter, through peak deconvolution will add back in the counts hidden in the overlapping areas to insure an accurate measurement. I would be wary of systems that are numerical filtering only for this application.
Chris Horvath- Chicago, Illinois, U.S.A.
Q. Whether XRF technique can measure plating thickness if base is Brass (70-30)coated with Pure Copper (0.2microns)? I understand XRF has limitations in case base and the layer has same major element.
- Secaucus, New Jersey, USA
August 8, 2016
Q. With Fischer XRF XDLM-237
Why is it necessary to calibrate with Ag & Cu before calibrating with Ni & Cr sample. My end interest is to investigate Chrome plating over nickel plating over steel substrate.
What's the logic behind this.
Does EMF series play some role for Ag & Cu as a master sample? If yes then why not Au?
Does mass attenuation coefficient has its part?
UET Lahore - Lahore, Pakistan
January 4, 2017
Q, A, or Comment on THIS thread -or- Start a NEW Thread