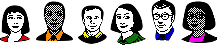
world gathers for metal finishing
Q&As since 1989
-----
What's the best finishing process for exterior steel railing?
January 28, 2017
Q. Hello,
The more I read on different threads, the more confused I am getting. That's why I wanted to just start a new thread and get your input.
The product in question is exterior steel railing. One inch square tubing top and bottom horizontal rail 6 feet long, 0.63 inch square tubing for vertical rails welded top and bottom to the horizontal top and bottom rail. Spacing for vertical rails is 4.5 inches. Total height 34 inches.
Since there is welding involved, I will not be using galvanized tubing. I need to provide 15 year limited warranty for this product. Product needs to be in black and hammered bronze finish. Once again this is exterior deck railing.
So now, to achieve this,
1) Do I need galvanizing?
2) If yes, then do I hot dip galvanize or electro galvanize?
3) What process do I use for the final finish? Pre treatment requirements for this finishing?
4) Is cathodic electro deposition a option? If I do this, should I still get it galvanized first?
5) Any other process that I might not know of?
Appreciate all the help.
Thanks.
Manny
Designer - Des Moines, Iowa, USA
A. Hi Manny. It's not clear to me whether you will be mass producing such railings or making just one. If mass producing, you really should hire a finishing consultant to clearly detail the process, assist you with test runs, salt spray testing, etc.
If you are making just one, you won't be able to afford to do that, and no matter what process you choose you will have to accept some risk of the railing failing within 15 years and having to repair/replace it. That being the case, I would not galvanize it because there is too much chance of adhesion problems on a one-off piece. I would have it zinc phosphatized, electrocoated, and powder coated. And I would include warnings/disclaimers about keeping de-icing salt and lawn fertilizers away from it. Good luck.
Regards,
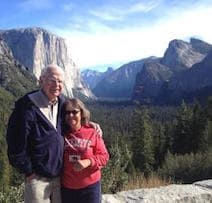
Ted Mooney, P.E. RET
Striving to live Aloha
finishing.com - Pine Beach, New Jersey
January 2017
Q. Hello Ted,
Appreciate the response. I won't be mass producing these. I build houses and have a machine shop. I figured I can make the railing myself. I will be making enough of these where I want to make sure I make a good product, but can't really afford a consultant.
There were a couple of threads where they discussed powder coating over galvanized steel and that if the pre treatment is done properly should work. Currently I am thinking electro galvanizing, pre-treatment and then baked on powder coat.
Are there any serious concerns about my line of thought? What are some of the things to watch out for when you are powder coating electro-galvanized steel?
Thanks.
Manny
- Des Moines, Iowa, USA
January 28, 2017
A. Hi Manny. I told you what I would do if I were you, and I implied why I wouldn't do what you are envisioning. For one thing, I think there is a very substantial chance of adhesion problems with what you would like to do. Plus, finishing of items made from hollow tubing is fraught with issues because you don't want to make airtight welds, but if you don't, you'll have unfinished surfaces that don't get plated, and will collect moisture both during processing and during use. I'd plan on drainage holes for good drainage of the inside of the tubing, and go for phosphatizing and electrocoating before powder coating.
Regards,
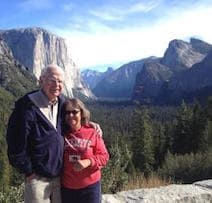
Ted Mooney, P.E. RET
Striving to live Aloha
finishing.com - Pine Beach, New Jersey
January 2017
January 30, 2017
A. Well there are several issues which need to be addressed here:
HDG of this fabrication would be a disaster as there would be insufficient drainage opportunities.
The same issue exists with E-coat.
Why not use pre-galvanised tubes and fabricate with Si-Br wire?
The fabrication difficulties so addressed then a fair-dinkum Zn Phosphate system should be used as a pre-treatment.
Then we come to the final problem.
Most commercially available Powders are good for 7 years.
To achieve 15 you would need to use a warranty approved powdercoater using a true architectural grade powder.
Of course all the foregoing is dependent upon the application being in an environmentally friendly locale.
If the locale is hostile (seaside close to coal fired powerplant et al) my recommendation would be to go for an Aluminium fabrication using marine grade tubem a chromate conversion coat, and then warranty grade powder.
Hope this helps,
Regards,
Bill
Trainer - Newcastle Australia
Q, A, or Comment on THIS thread -or- Start a NEW Thread