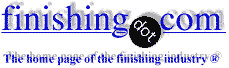
-----
Yellow Dichromate vs. Yellow Chromate?
(to help readers better understand the Q&A's)
This topic starts with the fairly elementary question of what is the difference between 'dichromate' and 'chromate'. The correct answer which you would get from a chemistry professor is 'chromate' is CrO4-- and dichromate is Cr2O7--. But there is little practical difference between them, and merely changing the pH of the solution can change the ratio of the two species in solution. But we quickly encounter the issue that the slang used by most platers doesn't match that careful definition :-)
Backing up a little, things are often zinc electroplated because it's an inexpensive, thin, reliable corrosion fighting coating for steel parts. But zinc plating itself has a strong tendency to quickly get 'white rust'. To prevent that, zinc plating nearly always receives a 'chromate conversion coating'. This involves a dip in a solution containing chromates and/or dichromates which may be optimized to impart a yellow color or to remain clear (other colors like olive or black are less common). But whether the species in the tank is CrO4 or Cr2O7 is not particularly interesting to the plater so he may use the terms interchangeably; or maybe he'll call the clear version chromate and the yellow version dichromate even though not strictly true.
Then we move on to a discussion of RoHS (a European Parliament directive regarding 'Reduction of Hazardous Substances', and questions of whether the performance of compliant products meets the old standards -- which is very confusing because it is a moving target and things have changed so dramatically from 2000 to today :-)
In the old days (before the early 2000's) there were two general types of chromates used: hexavalent chromate, the workhorse offering great corrosion resistance and usually imparting a yellow color, although sometimes clear; and trivalent chromates, the poor sister in terms of corrosion resistance (12 hours salt spray resistance compared to 96), and usually clear.
Enter RoHS, with hexavalent chromates forbidden, but at about the same time comes new trivalent chromate technology with corrosion resistance approximately equal to the hexavalent coatings. So you'll see correct claims in 2000 that trivalent coatings are patently inferior, and claims in the 2010's that their corrosion resistance is essentially the same.
Q. Hello, my name is Mark Thomas. I am an engineer for an OEM that uses a wide variety of plated products. Recently, a question has camp as to the difference between yellow dichromate and yellow/gold chromate. I have seen references to both. What is the difference between the two processes(e.g. salt-spray resistance when paired with zinc electroplate, appearance, application, bath chemistry, etc.).
In addition, is one process used in certain applications while thither is not? Specifically, this question is in reference to zinc electroplated fasteners and similar hardware, however any general information would be appreciated.
Finally, I would like to know what is the best way to note what won't on a part print. Currently, we use a note that says something like,"Zinc and yellow dichromate per ASTM B633, Type II, Fe/Zn 12." What is the best way to relay what I want to the plater? Any information would be greatly appreciated. Thanks.
- Oshkosh, Wisconsin, USA
2000
A. Hi Mark, I'm an engineer for a Tier I supplier. The two terms are the same thing. Yellow chrome is yellow chrome. Just ask for "zinc yellow" plating from your plater, give them copies of the correct specifications, and make sure the plating you will get will meet the spec.
By the way, if your application is for model-year 2003 or later,then you can't use yellow chrome. All zinc and zinc-alloy platings used currently also use some form of chrome on top of the plating.This chrome is of the hexavalent variety, and is on your company's restricted substances list. (Go check!) You can specify a TRIVALENT chrome system with a topcoat/sealer which will meet the new material regulations.
We have found that even though specialized groups within the OEMs are aware and dealing with the hex chrome situation, many of the engineers directly working on projects have not yet been informed of these new requirements. So, you are not alone, and you should spread the word to your co-workers. If you would like any further information, I would be happy to help you.
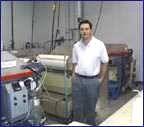
Tim Neveau
Rochester Hills, Michigan
2000
Q. Thanks Tim; I appreciate your response. However, I am still little bit confused. If yellow dichromate and yellow chromate are the same thing, then why is the distinction "yellow dichromate" made as opposed to say "clear chromate." Why not simply refer to all as chromate. Please feel free to go into detail. It is important that Understand what exactly the process is. Thanks again.
Mark Thomas- Oshkosh, Wisconsin USA
2000
A. There are different types of hexavalent chromates. Dichromate and chromate refer to the same hexavalent chrome conversion coating.Yellow and gold are about the same too.
However, there are a variety of chromates out there. There are yellow, bronze, clear, olive drab, and other colors out there. Yellow is stronger than clear. Bronze is stronger than yellow. Sometimes the only difference in these chromates is the thickness. Sometimes the chromate bath composition is different, but right now all currently specified chromates are based on hex chrome.
I just saw ASTM B633 this morning while discussing plating specs with a co-worker. Yes, "Zinc and yellow dichromate per ASTM B633,Type II, Fe/Zn 12" is a good way to specify plating on a part print.Type II is for colored chromates like zinc yellow. If you were specifying zinc with clear chromate, you would have to specify Type I.
I suggest that you ask your plater and/or the plater's chemical vendor about trivalent chrome passivation. I also suggest you ask someone in your corporate materials group about the European Union restrictions on hexavalent chrome. This topic is a big issue in fastener groups too, and you might also be able to get internal information there too.
I have had meetings with GM, Ford, and Daimler Chrysler, and all three are working on phasing out the types of chromates you are asking about! You maybe have one more year in which you can continue to specify this type of plating.
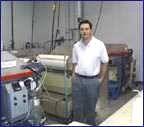
Tim Neveau
Rochester Hills, Michigan
2000
Q. I am the Quality Manager at a spring manufacturer. We have a few customers who want their product plated with yellow dichromate or clear Zinc plating. I am looking for information concerning the plating process so that I have a better understanding when discussing issues with our vendors. Any information will be greatly appreciated. Bill Nelson
William L. Nelson- Adel, Iowa, USA
2002
A. In brief, Mr. Nelson, things are zinc plated because it is an inexpensive, corrosion resistant, reasonably attractive finish which offers cathodic protection to steel (it dissolves preferentially to steel, thus protecting the steel, even if scratched).
However, zinc itself corrodes fairly quickly and the corrosion products are unsightly, sticky, white salts. Chromate conversion coatings on the zinc plating are very thin protective coatings that keep the zinc shiny and corrosion free for a time.
Traditionally, clear chromates have usually had a mix of hex and trivalent chromium while yellow chromates have been hexavalent based. The yellow chromates offered substantially better corrosion resistance.
There has been worldwide pressure to eliminate the use of hexavalent chromates for a while because of their toxicity and, in some cases, carcinogeneity. Recently, the European Union issued a directive that autos can have no (or essentially no) hexavalent chromium in them. This greatly intensified the pressure, and most people are trying to eliminate hexavalent chromates from their products; alternatives have recently been developed and improved, but are not as reliable or inexpensive as hexavalent chromates yet.
As for "chromate" vs. "dichromate", this is a semantics/language issue. Although to a chemistry professor chromate is CrO4 and dichromate is Cr2O7, to a plater either there is no difference or they may think of chromates as clear and dichromates as yellow, but it has little basis in fact. Further, as Tim says, all such chromate conversion coatings will soon use trivalent chromium rather than hexavalent anyway and the term trivalent chromate is an oxymoron anyway (CrO4, i.e. 'chromate', can't be trivalent).
I hope this answered your question.
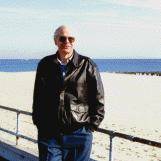
Ted Mooney, P.E.
Striving to live Aloha
finishing.com - Pine Beach, New Jersey
(Ted is also available for instant or long
term paid consultation and assistance)
2002
A. If anyone is looking for the relevant law on the (zinc) hexavalent chromate issue take at look at the European Union ELV (End of Life Vehicle) Directive 2000/53/EC Article 4 Section 2. (a) Prevention and Annex II Exemptions.
The Directive is available online: europa.eu.int
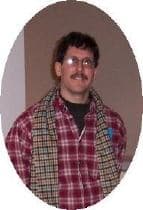
Sean McDermott
- Ramsey, New Jersey
2005
Q. Tim, I am also struggling with the Hex Chromate issue. Do all Chromate finishes (blue, black, clear, etc..) contain Hex Chromium? My understanding was, only Yellow contains the Hex Chromium. Also, my understanding is with the trivalent Chromium, you don't need a clear coating. It provides the same 96 hrs of salt spray protection. Is this correct? Your clarification will be greatly appreciated.
Rita Mohant- Stoughton, Massachusetts
2005
Q. In regards to the Trivalent coating....is this RoHS compliant?
Gene Crevier- Grand Rapids, Michigan
2005
A. This letter goes back pretty far in time and there have been huge investments and consequent improvements in trivalent chromating in the last few years. So, as an update --
Trivalent chromates have existed for decades but were rarely used because their corrosion resistance was so inferior to hexavalent chromates. But with RoHS regulations and other pressures to remove hexavalent chromium from products, new trivalent chromate processes have been introduced that can (depending on who you listen to) match or exceed the performance of hexavalent chromate, while conforming to RoHS requirements. All of these are highly proprietary; some involve a clear post treatment after the chromate whereas some involve a thick film of chromate. None are as easy as hexavalent chromating, nor as cheap, and they are usually not as reliable. Further they often don't work well where they must be painted, or survive further processing steps -- but elimination of hexavalent chromate finishes is important and it presently appears that it can be done, although imperfectly.
But RoHS (European Parliament Reduction of Hazardous Substances) does not concern itself solely with chromates, so simply specifying trivalent chromate is not a guarantee of compliance. As a simple example, cadmium plating with trivalent chromate would not be RoHS compliant.
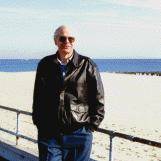
Ted Mooney, P.E.
Striving to live Aloha
finishing.com - Pine Beach, New Jersey
(Ted is also available for instant or long
term paid consultation and assistance)
2005
A. Hexavalent chrome is required in ASTM B633 Type II. However, according to your answer, trivalent chrome seems to be allowed in ASTM B633 Type II because of safety reasons. And we do not use hexavalent chrome because it is toxic. Is there any description in the latest version of ASTM B633 that allows trivalent chrome? Or is there any RoHs requirement that prohibits use of hexavalent chrome in products that conforms to ASTM B633?
If you have any question, please feel free to ask me.
- Yokohama Japan
October 14, 2010
----
Ed. note: ASTM B633 has been updated to include non-hexavalent chromating.
Q. I want to know if "YELLOW DICHROMATE" is supposed to be also used for metal nuts, and bolts and what is it's purpose? Is it safe to use in an enclosed area?
Efrain VeraDept. Of Aging and Disability - Richmond, Texas
February 11, 2013
A. Hi Efrain. The overwhelming majority of the world's nuts and bolts are zinc plated then chromated/dichromated and have been for many decades. Without zinc plating, nuts and bolts rust away quickly. Without chromate/dichromate post-treatment, the zinc plating forms voluminous gummy corrosion products that jam them up and ruin their function.
So, yes, whether the chromate/dichromate is clear or yellow, that's what it's for, and all zinc plated nuts and bolts have it, and it's perfectly safe to use in an enclosed area, although licking the hardware may not be perfectly safe. There is worldwide movement away from hexavalent yellow chromate to trivalent yellow chromate, so some portion of new hardware is trivalent chromated, but up to this point I don't know of anyone anywhere who has gone back and replaced any hexavalent chromated hardware.
Regards,
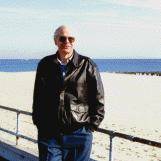
Ted Mooney, P.E.
Striving to live Aloha
finishing.com - Pine Beach, New Jersey
(Ted is also available for instant or long
term paid consultation and assistance)
February 13, 2013
Thank You Mr. Mooney.
I work with people who are mentally challenged, and some are allergic to some chemicals. I appreciate your answer and it gives me an idea of what it is used for and its purpose. I will post this so my co-workers can be aware, and what precautions to use. Example: Gloves, face masks, Protection glasses and cleaning supplies.
Again, Thank You!!
Regards:
Efrain Vera
Dept. Of Aging and Disability - Richmond, Texas
February 14, 2013
Q. 1) Some manufacturers call the yellow passivation as 'bichromate Passivation' or 'dichromate passivation'. Are these two the same?
2) What are the types of chromate conversion coatings for Zn passivation
electronics - Bangalore, Karnataka, India
June 10, 2014
A. Hi Roopa. Bichromate and dichromate are the same, and according to chemistry nomenclature they mean Cr2O7. From a plater's point of view, chromate, CrO4, isn't much different either.
But the salient point is that even through we may still call the conversion coatings on zinc "chromate" or "bichromate" or "dichromate" that's not what the newer RoHS-compatible ones actually are; rather, the chromium ion is trivalent (Cr+3) or perhaps partially divalent, but it is not hexavalent (Cr+6). Good luck.
Regards,
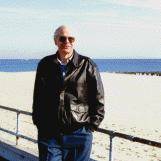
Ted Mooney, P.E.
Striving to live Aloha
finishing.com - Pine Beach, New Jersey
(Ted is also available for instant or long
term paid consultation and assistance)
June 2014
What is the difference between Zinc Dichromate And Zinc Bichromate
Q.
Dear sir
1. What is the difference between Zinc Di chromate And Zinc Bi Chromate. This both are equivalent to Zinc Chromate with trivalent as per ASTM B633 standard specification?
2. One of our customers is asking for this surface finish from us. We need to supply carbon steel or low alloy steel bolting as Zinc bi-chromated /Di chromated treated (ISO 4042 - 12 C Fe or ASTM F871M-98
[withdrawn]
and ASTM B633 - Fe Zn 12 Sc3). We request you to check whether you can supply Fasteners meeting all these three standards indicated in the above statement.
fasteners - Bangalore India
July 30, 2014
A. Hi cousin Basavaraj. That situation has been the topic of this thread, so I think if you slowly study the thread you will clearly understand the issues. But for the auto industry in total, and many other industries in part, and essentially all parts shipped to Europe, the chromate conversion layer on the zinc plating MUST be trivalent, not dichromate/bichromate as hexavalent chromate is not allowed. You must write this requirement into your spec/purchase order either explicitly or by specifying a correct (non-hexavalent) class of coating in ASTM B633. Best of luck.
Regards,
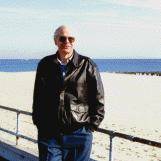
Ted Mooney, P.E.
Striving to live Aloha
finishing.com - Pine Beach, New Jersey
(Ted is also available for instant or long
term paid consultation and assistance)
July 2014
June 20, 2016
! Oh, hypocrisy of the modern world.
To save environment hexavalent chrome is banished.
Yet using trivalent chromium instead results in losing additional millions of tons of steel to rust - steel which would survive if coated properly and disappears as iron oxide, never again to be recovered.
So additional ore has to be mined (you ever been to iron mine? now THAT'S environmental destruction) and additional steel has to be processed (you ever been to a smelter?)
It is NOT the hexavalent chromium film on finished products that harms environment. It is the electroplating process which -- if performed by irresponsible electroplating facilities -- contaminates water.
Why not concentrate on properly treating hexavalent waste?
Don't throw the baby out with the bathwater -
in this case maybe treat the bathwater and keep the baby.
Standard Plating - Vancouver, Canada
Hi Joanna.
Unfortunately, that ship sailed decades ago. In the USA, when the EPA was established, taking over the job of environmental protection from the Department of the Interior, the very first thing they did was to aggressively target electroplating, a small industry dedicated to improving sustainability :-(
And around the world today, lo these many decades later, environmental protection agencies are *STILL* focused on reducing the discharge of zinc from plating shops and phosphates from painting shops, despite watching as the life of steel outdoor goods like patio furniture and garden equipment plummeted from 20+ years to 3 years or less. So we re-mine, re-ship, re-smelt, re-ship, re-fabricate, re-paint, re-package, re-ship, re-stock, re-sell, and re-landfill a ton of steel 5 times over for each pound of phosphate we 'saved' :-)
The axiom "penny wise and pound foolish" was never ever more aptly used than to describe these aggressive 'environmental protection' efforts directed against the exact industries which protect goods from corrosion and enable a sustainable future. Hopefully, we'll start to learn one of these days, but 50 years (and my whole career) later and with so few plating shops left, I've seen absolutely zero evidence that we've learned even the first thing from this debacle yet. I guess we'll have to wait for Silent Spring 2point0 to learn anything :-)
Regards,
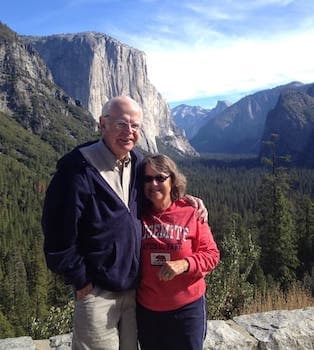
Ted Mooney, P.E. RET
Striving to live Aloha
finishing.com - Pine Beach, New Jersey
(Ted is also available for instant or long
term paid consultation and assistance)
Q, A, or Comment on THIS thread -or- Start a NEW Thread