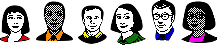
Metal finishing Q&As since 1989
-----
Pretreatment for Copper Infiltrated Powdered Metal Parts
May 26, 2015
Q. Hello All,
I am trying to determine the appropriate pretreatment for Copper Infiltrated Powdered Steel Parts that will have a TGIC coating applied. Currently, a zinc phosphate pretreatment is being considered. My current concern is two fold. First, I am concerned with how the copper will effect the coating that the part receives. Will the reaction process be accelerated due to the copper and how will this effect the corrosion resistance, paint ability, and surface finish? Secondly, I am concerned that the copper in the part will contaminate the zinc-phosphate bath and cause problems with future parts. In the ASM handbook it discusses 0.5% copper being a limiting amount in steel alloys for phosphate pretreatments as it causes surface checking of steel during hot rolling. However, I have not been able to find references for how this effects the phosphate bath or the conversion coating. Any advice on what the appropriate pretreatment would be (primarily looking for corrosion resistance and TGIC adhesion) or how this effects the bath is greatly appreciated.
Thank you in advance for your consideration.
With warm regards,
Todd
- Newberg, Oregon, USA
May 26, 2015
Q. Hello All,
A couple of details that I missed in the original post that I wanted to clarify:
- This is a powdered metal part
- The part is 10%+ copper and heat treated
Thank you in advance for your advice.
With warm regards,
Todd
- Newberg, Oregon, USA
October 28, 2015
A. Todd,
That is an interesting challenge. A couple ideas that have worked on somewhat similar projects: 1. Light grit blast. 2. Bake out.
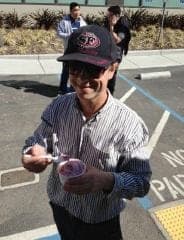
Blake Kneedler
Feather Hollow Eng. - Stockton, California
Q, A, or Comment on THIS thread -or- Start a NEW Thread