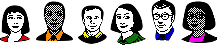
Metal finishing Q&As since 1989
-----
Corrosion of gold plated 316 stainless steel garter springs at the weld point
June 5, 2014
Q. I have a garter spring made of 316 stainless steel and gold plated (using a nickel strike). I am submerging samples of this spring in brine solution (seawater per ASTM D1131) that is at temperature (160 ° and 212 °F). Almost all the samples corrode. Corrosion generally appears in various sections of the spring but the first section to corrode is the weld point in all cases. I am wondering if I could get some advice regarding possible solutions.
Additional information:
a. I have tested samples of the same spring but unplated. These other samples do NOT corrode.
b. I have tested samples of the same spring but with nickel strikes and gold layers having increased thicknesses. The plating that worked the best had corrosion at the weld point only. I am hesitant to keep increasing the thicknesses of the nickel strike and gold. The garter spring is stressed in operation, and a stiff plating is undesirable (it could crack and also affect the mechanical properties of the spring).
c. I have tested samples of the same spring but without a nickel strike but an acid gold strike instead, maintaining the original thickness of the gold layer. The performance is similar to the performance of the plating that worked the best referred to in b. above, that is, I see corrosion at the weld point only.
Next steps:
- At this point I am considering changing the base material. I am coiling inconel, hastelloy, MP35N and 316L wire. I will make garter springs with these other materials and plate them normally, that is, with the original plating, and test them.
- I am also quoting a special gold plating technology which, among other things, includes a sealant on top of the gold layer. This gold plating technology includes nickel strikes as well.
Specific questions:
A part from looking for advice, I have the following specific questions. I will greatly appreciate having them answered.
1. When plating stainless steel, the first step is to activate it. My question is: does it remain activated after plating? I do think it does, because the chromium oxide layer is prevented from being formed, however, I have no experience in this field and I would like to confirm this.
2. I am trying to find possible ways to plate weld seams successfully. This may give me some insight to the problem I am trying to solve. Do you know of any case or reference I can consult?
Thank you very much in advance for your help.
- Foothill Ranch, California, USA
June 11, 2014
A. Hello Pere,
I had this same problem years ago. We found that the parts were not sand blasted at the weld joint in a proper manner. Is blasting possible on these parts? The oxide present at the weld joint had to be clean before we went into our pre-clean, activation and strike. Ni plating will become passive if the top coat is not applied in a timely fashion. I like to go into the final plate within 45 seconds to a minute after Ni plate. A Ni activator can be used to insure good adhesion. Hope this helps you.
Process Engineer - Malone, New York USA
June 12, 2014
Hello Mark,
Thank you very much for your input. I think we cannot sand blast the parts, they are spring rings with an OD of 0.205 inches, so the weld point is a very small region. However, I may be completely wrong, so I have asked our Processing Department if we can actually do it. I will update you with their response.
In line with this possible solution, just for your information, I am having yet another set of springs plated with the plating that performed best in the past (referred to in my previous post) but, prior to plating, we first electropolish the parts, the purpose of electropolishing being the same as sand blasting, that is, smoothen the surface of the weld. The only downside is that we electropolish not only the weld but also the rest of the spring. But I expect this not to be an issue.
Finally, I am also working with our welders to see if we can improve the weld in order to improve its surface condition without having to do a post-process such as electropolishing/sand blasting.
Regarding the Nickel activation, I am not sure about the time that passes between its activation and the application of the next layer. I will ask our plating supplier.
Again, thank you very much for your input, Mark. It does help.
- Foothill Ranch, California, USA
A. It's not surprising that you are seeing the most corrosion along the weld areas, that's where stainless always fails first if it is not passivated after welding. Of course in this case you shouldn't really want to passivate since you have to do the opposite to do your electroplating.
"When plating stainless steel, the first step is to activate it. My question is: does it remain activated after plating? I do think it does, because the chromium oxide layer is prevented from being formed, however, I have no experience in this field and I would like to confirm this."
If a passive stainless surface is composed of mostly chromium oxide, nickel oxide, and very little iron, and an active stainless surface is composed of a lot of iron and some zero valence chromium and nickel, then I would say yes, underneath the gold layer the stainless is still "active". It technically shouldn't matter because if there's a coating over the top of everything (your gold) then there's no way for anything to react with the iron that's there. I'm guessing that your gold layer is too thin to really be a coating that prevents corrosion (e.g. when carbon steel is painted or chromed) and perhaps some diffusion of iron is taking place through the gold layer to the surface where it is able to form rust.
I think ultimately your decision to test a different substrate may be the best thing. The entire nature of stainless kind of goes against plating it with something else.
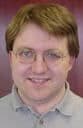
Ray Kremer
Stellar Solutions, Inc.

McHenry, Illinois
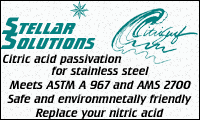
June 12, 2014
June 13, 2014
Ray,
I agree with your conclusion, which is that there is diffusion of iron. Also, the tests I have performed so far confirm that having a nickel strike on top of a stainless steel substrate is counter productive: the nickel strike is supposed to act as a diffusion barrier but yet is more reactive than the base. Hopefully changing the base material will work. I am glad to hear that you agree with this approach.
Thank you very much for your input.
Pere
- Foothill Ranch, California, USA
Q, A, or Comment on THIS thread -or- Start a NEW Thread