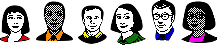
Metal finishing Q&As since 1989
-----
Designing a rinsing plan for Zinc Phosphate line
Q. Hello, we are a military sub contractor using a zinc phosphate dip process to prep our cold rolled parts for paint. We use seven 1000 gallon tanks that have: Parco cleaner 131, rinse, Fixodine Z, zinc phosphate, DI rinse, parcolene 99x, DI rinse, in that order. We just received a new contract that calls for a large increase in parts run through the tanks per day. I am trying to find out what is the best way to set up my rinse tanks to extend tank life and minimize drag out.
We would set up a countercurrent rinse system and the issue would be solved, but we don't have room to add any more tanks. A spray system is also not an option due to intricate nature of the parts.
Our only option is to do a constant overflow of DI water on each tank. I'm trying to figure out if I can do a cross flow from tank #7 to Tank #5 to save some water or run separate over flows at each tank. Our drag out is quite high, due to the shape of the parts, does anyone have any suggestions on how much water I should move per tank? Also I'm assuming that I should install the inlet at the top and the outlet on the opposite side bottom of the tank?
Any suggestions would be great. Thank you
- Berthoud, Colorado, USA
October 1, 2012
A. Hi Marcin. I wouldn't do that for DI rinses. Rather, I would recirculate each of the two DI rinses through its own deionizer. I suppose it actually could be a single de-ionizer for the two tanks, but the central point is "recirculate" not once through. That way you will have very clean water, a good flow rate, no worries about cross contamination. Then you can concentrate on the best regeneration/backwash protocol to minimize the actual water flow to your wastewater treatment system and drain. Good luck.
Regards,
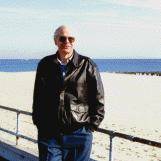
Ted Mooney, P.E.
Striving to live Aloha
finishing.com - Pine Beach, New Jersey
October 2, 2012
A. I agree with Ted. We have recycled many DI rinses after iron phosphating and zinc phosphating, since it is usually much cheaper than once through DI water use. The only concerns are the concentration of dissolved solids and adequate pre-filtration to remove suspended solids.
But, each situation is different and must be evaluated on its own merits.n
consultant - Cleveland Heights, Ohio
October 5, 2012
Q. Hello, my name is Artur Blahut and I work in an electroplating plant in the Czech Republic. For some time we have had a problem with our deionized water. We have a phosphating line with barrels. For rinsing first we have one bath with regular water and next a bath with deionized water, which runs through a closed circuit and passes an ion exchange column. Normally the water stays pretty clean (conductivity under 20 microSiemens and pH about 5, which is okay for us) for about a month, then we regenerate the column. In the last time, the conductivity rose quickly and we had to perform the regeneration every week to two weeks, which is a bit too much and there should be no reason for this. The resin is also not that old.
Has anyone had any similar experiences and what did you do?
- Brno, Czech Republic
November 14, 2019
A. Hi Artur. Since the resin is not old, odds are strong that the rinse rate in that 1st rinse was reduced, such that it's concentration is higher ... and/or that the drain time has been reduced. If twice as much salt is dragged into the D.I. rinse as previously, its life will be cut in half.
Regards,
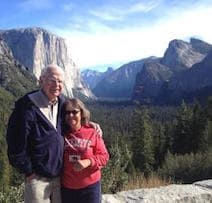
Ted Mooney, P.E. RET
Striving to live Aloha
finishing.com - Pine Beach, New Jersey
November 2019
Q, A, or Comment on THIS thread -or- Start a NEW Thread