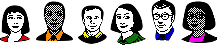
Metal finishing Q&As since 1989
-----
Chrome Plating of rotogravure cylinders: Problems & Solutions
Q. Hi, During rotogravure cylinder plating I am getting partial chrome plated cylinders in circumference. and every time on the same place of the bath.
I am using the Datwyler machine with a current density of 120 Amp/dm2; chromic acid content of the solution is 300 g/lt and sulphate content is 3 g/lt. The area of the cylinder is 3 sqm. Please suggest what should I have to do?
Kartikey Singh- G Noida, India
March 12, 2023
⇩ Related postings, oldest first ⇩
by Robert K. Guffie
on AbeBooks
or Amazon
(currently UTL on eBay)
(affil links)
Q. Morning Gentlemen,
I am new to this experts-exchange & hope to get find the right advice towards fixing my current problem.
Issue:- 'White streaks on the "2 ends" of the rotogravure cylinder'
Current Setup:-
- Chrome Type : Hard chrome Tank (1500 mm x 300 mm x 300 mm)
- Acid Used - Atotech Chromic Acid (liquid)
- Suppressant - Atotech Suppressant
- Anode - Lead/Nickellead-tin
- Temperature - 50 °C
Things I have done to address this:-
- Checked the acid density -> Found it to be appropriate
- Cylinder edges -> The cylinder edges are clean & do not have any copper residue prior to the chrome plating process
- Anode -> Still fresh with no yellow shade
- Since this is a 1500 mm x 300 mm x 300 mm, ensure there is enough anode coverage "end to end"
- Tried chrome plating multiple cylinders at one go -> not a fix
This did not fix my issue. How do you think I can address the streak issue ?
Looking forward to your feedback &/or suggestions ...
- Chennai, India [returning]
February 13, 2012
A. Hello,
This is called burning and you need to review your bath chemical parameters to your physical parameters.
Kind regards,
- Melbourne, VIC, Australia
![]() |
Q. Thank you for your response! - India A. This is clear burning : - France |
A. I am a strong proponent of conforming anodes where the anode cathode distance would be about 2 cm and the anode would be trimmed on the end until the burning stopped. Increased distance yields lower tank efficiency.
With tank anodes, a common fix would be to either use robbers or to use shields on the end to reduce the excessively high current density and get a normal bright plate. Some people use both.
Conforming anodes uses a close distance and gets a fantastically high plate rate that is bright. It does not burn on the end because trimming the ends of the anode increases the throw distance and uses the amperage where you want it to plate. Is it easy on large rolls-NO, but it is great after you develop the techniques. It uses a mesh mat anode so you get lots of solution flow.
- Navarre, Florida
A. My friend, did you say anode: LEAD/NICKEL? I think that was a typo error...should have been lead/tin?
Anyways, I would go with my friend Dominik.
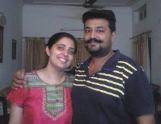
Vikram Dogra
Irusha India - Chandigarh, India
Thank you Francois, James & Vikram for your inputs.
Francois - I will try and correct the cathode/anode distance to be at 10 cms and let you know the results.
Vikram - Thank you for highlighting this! Yes, it's lead/tin and not Nickel :)
Q. James - Could you please elaborate on the term "robbers" & "shields"? I would like to understand and try them out if it's giving good results.
David Jose
- Chennai, India
A. Hi David,
Please let me know your cylinder data (face length and circumference) and as well which current and voltage is in use. Also, which method are you using (vertical or horizontal) for the chrome plating?
I would appreciate if you give us some more information about your bath specifications and analysis results.
Thanks,
Dominik
- Melbourne, VIC, Australia
A. Hi David,
Me again. I just have seen that you try to chrome plate at 50 degrees. If your chemical balance is given (min. 270g/l CrO3 & 0.9% H2SO4) then I would suggest you increase your temperature to 58 degrees. I do not recommend to increase your distance to the anode by now since it can cause higher resistivity and therefore reducing your amperage which then will result in a poor coverage of engraved cells in the middle of the cylinder and causing possible printing problems (shorter run times, poor ink release to substrate, etc).
Good Luck,
Dominik
- Melbourne, VIC, Australia
A. David,
On the picture there is the part burned to the right, but the 2 grey streaks are, I believe, coming from the material when they machine the part and weld it.
Regards
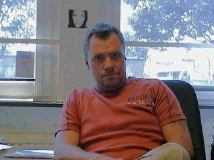
Anders Sundman
4th Generation Surface Engineering
Consultant - Arvika,
Sweden
A. Anders raises a good point. I am not sure that the part has been machined, but I agree the photograph is misleading. Assuming the streaks referred to in the original question are (is) the one at the end of the gravure, I would go along with the idea it is "burning" caused by a high current density that would be expected to be seen in such an array. I would suggest using a robber to reduce the effective current density at the ends of the gravure.
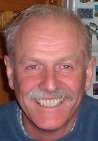
Trevor Crichton
R&D practical scientist
Chesham, Bucks, UK
A. Add in 25 KG of chromic acid with 3 liters of additive HEEF 25As. Increase your temperature to 60 degrees.
Ahmad HTT- Malaysia
October 19, 2023
Q. I have a related question to ask about Chrome 6 plating.
Recently, our current setting is fluctuating during plating. The difference is -40 to +40 Amperes from setting that we want to plate. The outcome is whitish and burned chrome plating layer and sometimes yellowish or not plated with chrome at all.
Is it related to sulphate content or other additive which is not in balance in the bath?
How about the mechanical factor like wiring, cable, connector and rectifier itself?
We have tried changing rectifier, controller, doing some dilution and adding in some additive, but still not effective. Please give some idea?
For your information, recently we have changed all the tin lead anodes for this bath.
- Malaysia
April 26, 2012
A. Hi Nordin,
Need more info on your process. Chromic acid concentration, sulfuric acid concentration, operating temperature, current density used. New setup having problem or old line which having been running fine before? The last question needs to be asked because hexavalent chromium plating needs low-ripple rectification.
- Penang, Malaysia
info: Hi Mr.Cheah,
Regarding your question --
chromic acid concentration is 245 g/l, sulphate 1.4g/l,
operating temperature 39-40° C., current density use depends on part shape/character -- normally between CD 4-CD 8 with plating time 2.5 to 3.0 minutes.
- Malaysia
![]() |
A. Hi. - Penang, Malaysia A. Dear Norudin, - Ajman UAE |
Q. We have a problem with plating chrome over copper in rotogravure cylinder. After the cylinder is going to press and after 1 ton or less the chrome is going weak and the doctor blade makes scratches on the cylinder surface.
We use current density of 65 A/dm2
plating shop employee - SA
May 5, 2012
A. Please first check hardness you are getting is looks like you're getting below 800 vickers. Are you using conventional bath or organic catalyst bath?
Qutubuddin Saify- Ajman UAE
![]() |
A. I work in ASI for chrome, so 65 ASD = about 650 ASF which = about 4 ASI. Normally this would be good, but if you are using stick anodes with a long distance from the part to the anode, You are generating a huge amount of heat. The 4 ASI would normally take in the low efficiency of the tank, but that depends hugely on the highest temp for the run. - Navarre, Florida A. Try to lower your current density since you have a greater build up on radius of cylinders and edges of cells. If you have a chemical imbalance, your throwing power will suffer and leads to lower lifetime of cylinders. Also, micro-cracks which usually will provide the lubrication during the print will be greatly reduced. How's you temperature and chemical parameters? - Melbourne, VIC |

Q, A, or Comment on THIS thread -or- Start a NEW Thread