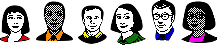
Metal finishing Q&As since 1989
-----
Best finish and substrate for my situation?
Current question and answers:
November 15, 2020Q. Hi all
What base/substrate material for gold plated electrodes?
I should preface by saying that I'm very new to the science & art of metal finishing, so please excuse any mistakes.
I'll first describe the application that I'm trying to find a solution for. I'm building a test cell that has metal cylinders as electrodes to measure an electrical property of liquids. These liquids will be mostly organics and hydrocarbons (fuels, oils etc). I need to finish the electrodes and the case to be corrosion resistant.
** My current setup:
I have the test cell case made from anodised aluminium. The cylindrical electrodes are made from aluminium and electroless plated with Gold.
** Thermal Requirements:
I need a base metal that has high thermal diffusivity and hence one reason why aluminium was chosen (and ease of machining). Other suitable metals could be copper and brass.
** Issues with the current setup:
We've noticed that the gold plating on the aluminium has started flaking with some green-tinted corrosion. We suspect this is because the gold plating was breached or scratched.
** Points to note:
1. Some of the electrodes have threads which are screwed on a central support mandrel.
2. The cell is thermally cycled within a range of -40 °C up to 80 °C
3. Chemicals often used are fossil fuels, aviation fuel, alcohols, some other organic materials. We don't use any highly corrosive acids, but some of the aviation fuels could have sulfur and chlorine compounds in trace amounts.
** Questions
1. Is gold-plating aluminium generally a robust solution? It feels like since aluminium is relatively soft, and that might not help.
2. Gold plating copper vs gold plating brass vs gold plating aluminium --- which coating is more resistant to failure?
3. I understand hard gold coating might help with resistance to scratches or dents. I'm wondering if the presence of non-noble metals could cause oxidation and worsen chemical resistance?
4. Since anodised aluminium has adhesive bonding properties, does that mean I can't screw two pieces of anodised aluminium together if they would bond together?
5. If certain parts are made from brass and some with aluminium, does that cause any galvanic corrosion?
6. When gold plating brass, is there usually a zinc/nickel plating intermediate? I think currently, the scratches/pores on the gold plating exposes the zinc beneath and this is what is corroding, rather than the base aluminium.
** My proposed solution
Continue using anodised aluminium as the test cell case. Use brass that is gold plated for the electrodes. I would prefer to use the same metal, but if I use brass as the case, I suspect that means I would have to gold plate that as well.
Does gold plating brass prevent the migration of zinc away from the base metal? I read that brass could degrade through the loss of zinc. If this is the case does using gold plated copper make more sense.
I'm leaning away from copper as copper does corrode with relatively long exposure to Jet Fuels.
So there we go, what do you guys think?
Hatim
- Chertsey, UK
A. Hi Hatim. If anodized aluminum is causing you no grief for the case, don't change it.
For the electrodes, electrolytically pure copper offers the highest electrical conductivity and thermal conductivity, and easy plateability, so I think it's a good choice. Brass is okay but most people think that it ought to be copper plated before proceeding, so copper sounds simpler. The alternative, electroplating onto aluminum, can be done but always involves an intermediate step of immersion plating with zinc which does not offer the same reliable adhesion strength as electroplating (and you are doing thermal cycling that will try to attack that weakness). You should have a diffusion barrier of nickel plating between the copper and the gold plating. If everything is done reasonably well, I wouldn't expect any problems.
Luck & Regards,
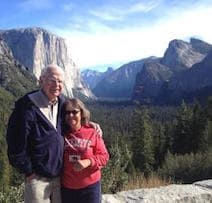
Ted Mooney, P.E. RET
Striving to live Aloha
finishing.com - Pine Beach, New Jersey
November 2020
⇩ Related postings, oldest first ⇩
Q. Hello to all the finishing experts as well as the regular slobs such as myself! My company produces breakaway socket anchors for roadside sign installation. The sockets are hot-rolled steel plate welded to standard angle iron, which we the dip-coat in an oil base red oxide primer paint. We use a tapered wedge to secure square or round signposts inside the socket. The wedge is formed from zinc plated steel tubing that we cut to 4" lengths. It is hammered into the socket to secure the posts. When a sign post is struck and damaged, the wedge is removed with a slide hammer and a new post and wedge are installed.
PROBLEM: Customers replacing posts after a period of time are having difficulty in removing the wedges due to corrosion. Functionality requires a tight fit to begin with, so I don't want my customers also fighting with metal rusted together! What is the toughest, most economical finish for these two surfaces (wedge and socket) to avoid corrosion in a roadside environment? Thanks in advance for any and all thoughts on this!
Production Supervisor - Brown Deer, Wisconsin
March 12, 2010
A. How about just keeping the parts physically separated by sliding a piece of plastic between the two components during installation? I am thinking something like a piece of a cut-up soda bottle (usually made from PET in the USA) ought to do the job. At 5 cents per bottle, this is probably your lowest cost solution.
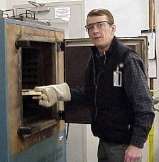
Thomas Hanlon, Materials Engineer
aerospace finishing - East Hartford, Connecticut, USA
March 18, 2010
Self-Etching Primer
on
Amazon
(affil links)
A. Hi Rich. Zinc plating is known for voluminous and sticky corrosion products (which causes this jamming), whereas cadmium plating is very similar in corrosion prevention but offers lubricity and far less voluminous and sticky corrosion products. In critical aerospace, military, and life safety applications cadmium plating is often still the answer. But cadmium is a biocumulative poison we're working hard to get out of the environment. On the other hand the news periodically shows us repeatedly that some of our jewelry, even children's jewelry, from China will be cadmium, ni-cad batteries are a commonplace, and some brake discs are still advertised as cadmium plated).
So I'll just present the situation as I see it and let others, perhaps state highway commissions, decide whether cadmium plating should be considered or ruled out.
But I think it would not hurt to dip those 4" long wedges into primer as well, maybe aluminum colored. Although some of the paint will be scraped off during the hammering, it will provide at least some paint coverage to significantly slow down the steel corrosion and the development of zinc corrosion products.
Luck & Regards,
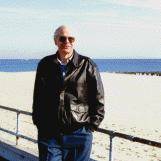
Ted Mooney, P.E.
Striving to live Aloha
finishing.com - Pine Beach, New Jersey
Q, A, or Comment on THIS thread -or- Start a NEW Thread