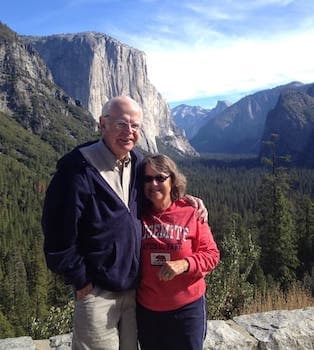
Ted Mooney, P.E. RET
- Pine Beach, NJ
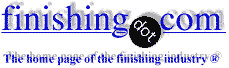
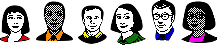
The authoritative public forum
for Metal Finishing since 1989
-----
Setting up a passivation station in our shop
November 18, 2009
we are a small job shop and are interested in setting a small passivation station.
The materials we're looking to passivate are the following:
316 s.s., 303 s.s., 17-4PH Condition H900 & Nitronic 60 30% Cold Worked
The part size is: .246 dia. x .050 thick with a .040 I.D.
We want to passivate against: ASTM
ASTM A967
Using: Nitric Acid. (We realize under this specification citric acid can be used)
We want to know the following:
1)what do we need to set up this station
2)handling nitric and disposal
3)testing: checking the nitric acid level. (we plan to use a 50/50 solution)
4)testing: making sure we remove traces of iron
5)ventilation
6)etc.....
- Chicago, Illinois
November 19, 2009
Greetings,
Nitric passivation tanks are relatively easy to maintain (we run our at 20% rather than 50%). You have four basic steps: clean, rinse, passivate, rinse.
We use a hot alkaline cleaner to ensure that the parts are oil/grease free. Our cleaner is hot, so we use a stainless tank for this step. Follow your suppliers' instructions for maintaining the cleaner concentration.
We use a dual tank (poly works) flowing rinse post-cleaning, and discharge the rinse water to the sewer.
Poly tanks will work fine for the passivation tanks. If you order the nitric in the concentration you want, it makes your life easier and the nitric can be stored in drums. I know I sound like a lawyer, but you'll have to check local regulations to see what quantities would require you to have secondary containment in the event of a drum leak.
One detail that is important regarding the list of materials you want to passivate is that 303 stainless requires passivation in a mixture of nitric acid and sodium dichromate (we use 20% and 2% respectively). Without the sodium dichromate, you can turn a lot of
303 into scrap pretty quickly.
Check nitric concentration weekly (titrate with sodium hydroxide). Check sodium dichromate weekly (titrate with sodium thiosulphate
⇦this on
eBay
or
Amazon [affil links]
).
Spray the parts over a catch tank to remove most of the drag out from the passivation tanks. Because of the sodium dichromate, you'll need to be especially careful to catch all of the rinse water. You can allow water in this tank to evaporate. Once it is full, it'll have to ship as chromate waste unless you have the capacity to treat it in house. If you have this capacity, you can neutralize the contents of this tank and remove the chromate. The leftovers can go to the sewer.
Next you'll want an immersion rinse tank. Check the pH in this tank daily (keep it between 6 and 8). We are usually able to discharge this tanks contents to the sewer, but we check the metal content
(especially chromium) before changing out the tank.
As far as keeping the nitric fresh, a periodic change out of 10% -
25% of the bath is a good idea. The frequency depends on the volume of parts you process.
Keep the tanks covered when not in use.
We don't need to ventilate our tanks, and we don't run any post-passivation QC on the parts. Our customers don't require any, and we've never had a complaint about a passivated part failing in the field (over 10 years running the line).
Enjoy the new process!
Engineer - Grand Junction, Colorado
Nitric is of course a perfectly valid method of passivation, but I would be remiss if I didn't mention that it comes with many issues such as safety, disposal, and ventilation, and these issues are very much lessened by using citric acid instead. Many small shops are only now starting to do passivation because the citric allows them to do it without the hazards and costs associated with the nitric. But if you are comfortable with everything that having a nitric acid line will entail, then by all means, carry on.
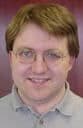
Ray Kremer
Stellar Solutions, Inc.

McHenry, Illinois
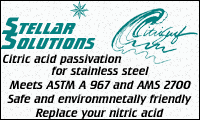
December 7, 2009

this text gets replaced with bannerText
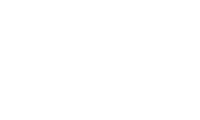
Q, A, or Comment on THIS thread -or- Start a NEW Thread