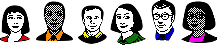
Metal finishing Q&As since 1989
-----
Anodizing Cast Aluminum

Q. I want to anodize (type II) die casting aluminium (AC4CH) part having silicon content about 7.5 %. My question is what type of etching and Desmutting chemical should I use so it removes silicon contained on surface of part.
Shubham Rajput- Pune, INDIA
March 6, 2022
A. Hi Shubham. We have about a dozen threads in this forum about anodizing castings and their high silicon content, so we attached your inquiry to one of several which seem to answer your questions well...
It is best to not etch (although some knowledgable readers say you can if you must), then you must use a nitric acid plus aluminum bifluoride desmut as described by Robert Probert.
And don't have high expectations for aesthetics :-)
Luck & Regards,
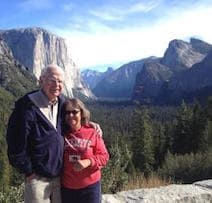
Ted Mooney, P.E. RET
Striving to live Aloha
finishing.com - Pine Beach, New Jersey
⇩ Related postings, oldest first ⇩
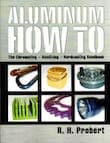
"Chromating - Anodizing - Hardcoating"
by Robert Probert
You'll love this book. Finishing.com has sold 880 copies over the years without ever a single return request :-)
Q. I came across this website doing a search on Anodizing. Very Impressive I must say, but still at a loss for what I'm looking for. Just about all the technical information on here is way over my head, definitely not my field.
From what I understand: Aluminum can be anodized but not Cast aluminum and get the same quality as the before mentioned.
My application is for automotive use and there are a few pieces that I need to get plated, ceramic coated or something other than spray paint. I am looking for a finish that's just about identical to the "purple" Maglite flashlights, and be able to withstand normal operating temperatures associated with car engines.
Any leads would be greatly appreciated. Please feel free to contact me either by phone or e-mail.
All I'm looking for is to get some custom work done for my engine rebuild the way I want it to look, and I know there is a way ... just having trouble finding the right path you might say. Thank you,
CRAIG SKILES- Atlanta, Georgia
2000
Ed. note: Sorry, this RFQ is old & outdated, so contact info is no longer available. However, if you feel that something technical should be said in reply, please post it; no public commercial suggestions please ( huh? why?)
Treatment &
Finishing of
Aluminium and
Its Alloys"
by Wernick, Pinner
& Sheasby
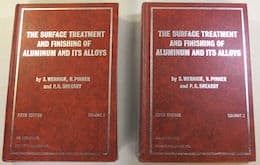
on AbeBooks
or eBay or
Amazon
(affil links)
A. You are very probably looking for "two step anodizing". I doubt if regular dyed anodizing will have the fade resistance you are looking for. Find a job shop that does that type of work. There are not many, but there are several. Cost is a fair bit higher. Wrought alloy anodizes beautifully, extrusions are from good to bad and castings are from fair to very bad.
James Watts- Navarre, Florida
A. Powder coating may be an option. If the parts can be brought to a high luster, the powder coat can be applied with a translucent effect that is very attractive and this can be done in a large variety of colors.
Bill Miller- Shinnston, West Virginia
A. Hi, Craig and readers.
The internet is a gigantic one-room schoolhouse; so sometimes it's hard to find the information you're looking for at the level you wish. But here's a quick explanation about why it's hard to anodize certain types of aluminum: only the aluminum per se can be anodized, not the other stuff that may be in an alloy or casting like the silicon, copper, zinc, magnesium, etc.
Some grades of aluminum (and all castings) have a lot of that other stuff. That other stuff doesn't etch away easily, doesn't get converted to glassy looking aluminum oxide, but just turns into a gray to black smut which may be porous or speckled, won't be bright or smooth, and won't dye to the colors you'd like. So the more of that other stuff, the less satisfactory the anodizing, and that's just a lot of that garbage in castings.
The next point, that James Watts mentioned, is that even if you do dye it, most dyes are organic and subject to degradation from high heat. So you probably need a special inorganic coloring for an under-hood application. Those inorganic dyes, which are also used for architectural anodizing are applied by methods called "integral color anodizing" or "two step anodizing" but tend to be champagne to bronze to brown in color. Purple sounds unlikely for an inorganic dye; before the days of synthetic inorganic dyes, purple was so rare and difficult that it was reserved for royalty :-)
So, an attractive "purple mag lite" anodized finish for an under-hood application on cast aluminum doesn't sound very do-able to me, and would be a development project rather than something a consumer purchases. I think a a purple ceramic sounds like a more promising approach. Good luck!
Regards,
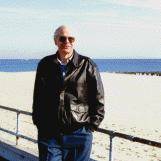
Ted Mooney, P.E.
Striving to live Aloha
finishing.com - Pine Beach, New Jersey
Plating or anodizing a Webasto aluminum heater
Q. I have my hands on a Webasto thermo engine heater, it's basically a mini buddy heater that uses diesel fuel to heat up an all aluminum body heat exchanger. On the other end of the heat exchanger the vehicles coolant passes through and is pumped throughout the engine. I had the unit sand blasted to bare metal to remove all built up dirt and soot. What I'm wondering is, what would be the best suitable method of ensuring it doesn't build up particulate as easily. I was suggested to have it anodized or plated, bear in mind it will see temperatures upwards of 200 °F, with contact with diesel fuel and engine coolant. Any advice is much appreciated.
Sam.
- Winnipeg, Manitoba, Canada
October 31, 2015
A. Hi Sam. I'm not sure if you're speaking of anodizing/plating the innards or the outside surface but the innards may not be possible considering the way those processes work.
Luck & Regards,
Ted Mooney, P.E. RET
Striving to live Aloha
finishing.com - Pine Beach, New Jersey
Q. Hi everyone
I'm anodising motorcycle parts and some cast aluminium like brake calipers and engine cases. When finished being anodised they are very dark grey.
It makes it impossible to dye them anything but black.
What's going on here?
- Brisbane, Queensland, Australia
December 8, 2018
A. Hi Tom. We appended your inquiry to one of our prior threads on this subject. Cast aluminum contains a lot of garbage that isn't aluminum and will not anodize. You can slightly improve the situation by de-smutting before anodizing, with acids tailored to the specific contaminants (like nitric acid for the copper, fluoride-bearing acids for the silicon), but you're unlikely to get good aesthetics from anodized cast aluminum.
Regards,
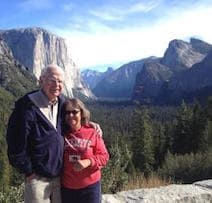
Ted Mooney, P.E. RET
Striving to live Aloha
finishing.com - Pine Beach, New Jersey
A. Hi Tom,
In addition to Ted's comment which is of course spot on, what is your temperature during anodizing? If it is low enough to approach Type III / Hardcoat range, that also will darken your end result.
The best you can do with a gnarly casting IMO (our standard protocol here) is hot caustic etch the part, deox/desmut it very well, using a bath that has both Nitric acid and Sulfuric Acid with ferric chloride [on
eBay or
Amazon] and LOTS of bubbles, and maintain your Type II temperature range at 70 °F +/- 2. And then cross your fingers and hope it comes out marginally attractive ... That bit doesn't show up in the routers ;)
Black dyed parts aren't the worst thing to ever happen. But make sure you are using a black dye that will stand up to engine temperatures, fluid leaks/spills, and UV exposure over time.
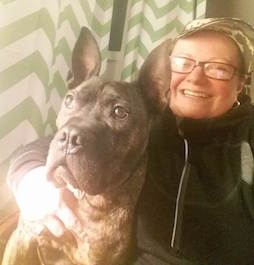
Rachel Mackintosh
- Greenfield, Vermont
A. Both of above are right, but I take difference on alkaline etching. caustic soda [affil links] etching removes aluminum and exposes more silicon - exactly opposite of what you really want, so stay out of the alkaline etch. After non-etch soak cleaning, then 100% Nitric acid with 2#/gallon ammonium bifluoride, the parts will turn "frothy white" in about 15 seconds, take them out, rinse two times hurriedly, do not stop to look, anodize - that is the best you can get with that particular casting. After a few runs it will take more than 15 seconds. The above is for sand cast, some of those motorcycle parts are die cast in which case you can use only 50% nitric with one #/gal ammonium bifluoride. Anodize the castings at about 22 volts.
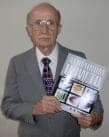
Robert H Probert
Robert H Probert Technical Services

Garner, North Carolina
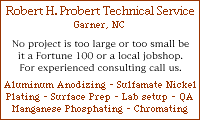
Are Honda motorcycle parts clear coated or anodized?
Q. Hi, I will restore a motorcycle and is named sand cast (CB 750 Honda), and want to refinish the parts to aluminum color. I am not an expert but I once put an aluminum cover into a battery acid
[affil links] bath and it turned white, and is still white since 5 years.
The wheel hubs, control levers, brake pump & caliper, and engine covers all look like different alloys.
I can't find the process used by Honda in the 1970's but they look polished with a clear coat. I think in anodizing but after reading your expert advice, ask if the experts know the best finishing option for motorcycle aluminum parts? I am ready to learn. Thanks.
motorcycle and outboard mechanic - Mexicali Baja California Mexico
January 7, 2019
A. In my experience, many automotive parts are clear coated. This includes motorcycle engines, and especially polished mag wheels. Do a scratch test in an inconspicuous area and see if it flakes.
Evan ParentPersonal - Wilmington, Delaware
Not question or comment, total experimental, but got pics of crescent wrenches used on some cast aluminium parts that I cleaned first with wire brush then beat with crescent wrenches then lightly lightly beat after big crescent long story 96 third irs knuckles going to be anodized, doing some small cast aluminium.
Pretty close to finished part:
- St. George utah
November 30, 2019
Q. question now is porosity if all aluminium will electrical charge go skiwhompos or will it do like smooth surface
- St george utah
December 31, 2019
A. Hi Mike. Very nice pictures, thanks. But I have to apologize that I have little idea what your questions & comments refer to. It seems like you are saying you did a bright hammer finish on some aluminum castings (and that's what it looks like). Now I'm guessing you want to anodize them? But as people have said previously, it's not very promising; if you want to preserve the look, a clear coat seems like a much better idea. Good luck.
Regards,
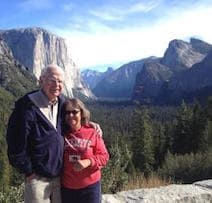
Ted Mooney, P.E. RET
Striving to live Aloha
finishing.com - Pine Beach, New Jersey
Been hammered and diced and sliced sorta like ball peened thinking about flash heating surface to smooth out ripples and to level surface more should take but was just wondering about porosity that seems to be most of problems (in discussions that I've read) with cast aluminum in and by products in the cast. Thanks for the reply, your reply is like mine should just clear coat much easier.
- St george utah
January 4, 2020
Can we anodize cast aluminum car wheels
Q. We know that anodizing pure Aluminum is very easy and gives very good appearance.
But most car wheels are made from Aluminum alloy -- I think it's Aluminum-silicon alloy and Aluminum -zinc alloy.
So can we do anodizing on it?
- jordan amman
October 26, 2020
A. Hi Qwee. I think you will find that it anodizes far too gray and irregularly to please you. But you could cut a cast aluminum wheel into a bunch of pieces and experiment with them, or just accept Robert Probert's advice on the best approach.
Luck & Regards,
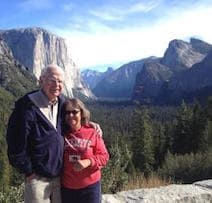
Ted Mooney, P.E. RET
Striving to live Aloha
finishing.com - Pine Beach, New Jersey
Q. Hi, we struggle getting a great finish on our cast aluminum parts. The parts are sand blasted before finishing.
We would like to get clear dull aluminum coating, ideally similar in color to clear anodizing on machined aluminum.
We would like to avoid paint, due to cost and masking issues.
We tried electroless nickel and clear anodizing, but the color is not very even and darker/yellower than desired.
Would it be possible to apply an aluminum flash on the casting before clear anodizing to get a more uniform and "whiter" finish?
Any other insight to obtain the desired clear aluminum finish on our cast parts?
- Montreal Quebec
March 2, 2021
A. Hi Ben. We added your inquiry to one of several threads on anodizing of cast aluminum. I think you already understand that the basic problem is that aluminum castings have a high percentage of non-aluminum material in them. and only the aluminum portion anodizes -- so discoloration and blotchiness is inescapable. It is possible to anodize an outer layer of aluminum plating, provided it's thick enough, but aluminum plating is a difficult proposition with (to my knowledge) only one shop in America offering it.
Luck & Regards,
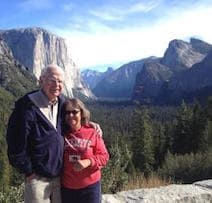
Ted Mooney, P.E. RET
Striving to live Aloha
finishing.com - Pine Beach, New Jersey
A. The best "white" finish you can get depends on the alloy quality of the casting and the surface preparation. Do NOT alkaline etch. Dip in 100% commercial nitric acid with 2#/gal ammonium bifluoride for the approx. 15 seconds it takes to get "frothy white" all over, rinse twice and anodize, and that is the best you can get with that particular casting. The fumes eat holes in the air sacs of your lungs.
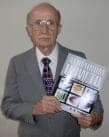
Robert H Probert
Robert H Probert Technical Services

Garner, North Carolina
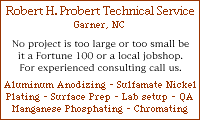
Q. Hello everybody,
I've got a piece of AlSi9Cu3 alloy to anodize. It is a steering cover.
I red here in the blog that die cast aluminium should not be dip in caustic etching. The problem is that if I do not that, then not enough current passes through the piece and it will not sufficiently anodize. On the other hand, if I dip it into the caustic etch, the piece comes out of the hot sealing tank with a black powder on all the surface.
Here in the plant I've got the possibility to acid etchthe piece (30% sulfuric acid) before anodizing it. Do you think that it is possible to anodize die ast aluminium in a right way with that sulfuric etching before anodizing? If yes, how much time do you think that I have to stay into the acid etching tank before the anodization?
Or do you think that the only way to anodize this alloy is dipping in nitric acid before the anodization?
Thank you so much in advance.
- Vicenza Veneto Italia
June 21, 2021
A. If you alkaline etch die castings alloy you decrease the exposed aluminum and increase the exposure of non-anodizable silicon. This is opposite of what you need to do. Do not alkaline etch castings. For die castings, deox in 50% commercial nitric acid with 1 pound per gallon ammonium bifluoride, takes about 20 seconds, rinse twice and go to anodizing quickly. ONLY fluoride will remove all or part of the exposed silicon and show more aluminum area. You anodize "aluminum", you only darken the silicon that is on the surface.
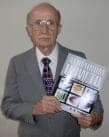
Robert H Probert
Robert H Probert Technical Services

Garner, North Carolina
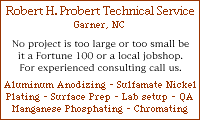
Q. Thank you so much Mr. Probert.
Certainly, in future, I will make a new tank with nitric acid and ammonium bifluoride as you suggested me. Unfortunately, for the moment, I can not etch the parts in that way.
My die cast piece has not got aesthetic requirements. I have only to functional anodize them (≤10 µ
m).
This morning I tried to acid etch one of them with 30% sulfuric acid and a bit of oxygen peroxide, before the anodization.
The black powder disappeared and I found also a good oxide thickness.
Do you think that this acid etching is useful for the anodization or is useless?
If I do not etch with nitric acid and ammonium fluoride could I have problems on the functional oxide properties or it is just a matter of aesthetic?
Thank you so much in advance.
- Vicenza, Veneto, Italia
A. Hi Riccardo. With Robert's wide experience, hopefully he can predict.
But for the benefit of other readers trying to better understand metal finishing I should take the time to not mislead them by noting that, while our subject is science-based, it relies very greatly on empirical knowledge. Questions like: "what will be the corrosion resistance of AlSi9Cu3 aluminum subjected to a sulfuric acid + peroxide dip before 10 µm anodizing" cannot be answered by 'first principles' at the current state of the art, but only by conjecture based on similar experience. And where there is not significant prior experience there is not a lot of empirical knowledge :-(
Luck & Regards,
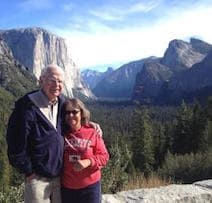
Ted Mooney, P.E. RET
Striving to live Aloha
finishing.com - Pine Beach, New Jersey
Q. You mentioned being able to anodize cast aluminum in a 2 step process in champagne to bronze color. I have cast aluminum engine parts I would like anodized in a bright copper color. Do you think it is possible to get a nice finish on cast with a 2 step copper color? THANKS.
Robert Wong- Westminster
October 2, 2021
by Runge & Kaufman
on AbeBooks
or eBay or
Amazon
(affil links)
A. Hi Robert. That's not exactly what we said, or at least it's not what we were trying to say :-)
The '2-step process' (actually just slang) refers to a method of dyeing (usually reserved for architectural work) which, instead of using organic dyes, 'implants' metals into the anodizing pores to give colors with exceptional fade resistance and UV resistance. If it could give a good copper color it's still not going to resolve the issue of the unsuitability of castings for decorative, aesthetic, anodizing which is a problem related to the impurities and general crudiness inherent in castings. Your headers will probably not look good if anodized and dyed a copper color whether with organic dyes or a two-step inorganic dyeing process.
You could copper plate the headers but I don't know how you would prevent oxidation and keep them looking good. I think high-temperature paint in more promising.
Luck & Regards,
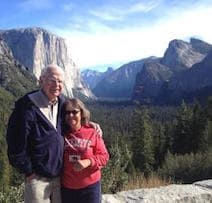
Ted Mooney, P.E. RET
Striving to live Aloha
finishing.com - Pine Beach, New Jersey
I have been floating around this forum for years, and it never ceases to amaze me at the level of knowledge and willingness of people to impart their knowledge onto the 'dumb' (HA - for want of a better term).
Comments from the likes of Ted and Robert (and others) are always interesting to read and the recipients of the knowledge of these people need to add Ted and Robert (and others) onto their Christmas card list - HA.
I am not a professional finisher, but do dabble in it for my own projects and hence enjoy reading about the problems and solutions. CHEERS from AUSTRALIA.
Lawyer and car, motorcycle and piston engine aircraft nut - Melbourne, Australia
January 8, 2023
Hi Bill. Thank you the kind thoughts :-)
Regards,
Ted Mooney, P.E. RET
Striving to live Aloha
finishing.com - Pine Beach, New Jersey
Q, A, or Comment on THIS thread -or- Start a NEW Thread