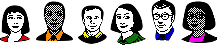
Metal finishing Q&As since 1989
-----
Can pretreating of aluminum for epoxy bonding be done on a small scale?
Q. We need to create a strong bond between aluminum parts with epoxy adhesive [on eBay or Amazon]. Henkel have advised phosphoric acid etching of the surfaces to be bonded. As this must be done shortly before bonding, can this process be performed by a small company and are the chemicals readily available in small quantities? Thanks for any advice!
Martin Hughesproduct designer - Albany, NY, USA
June 29, 2009
![]() |
"adhesive Bonding of Aluminum Alloys" A. For adhesive bonding I recommend to anodise the parts in phosphoric acid (BOEING method) 10% phosphoric acid, 10°C, 10 - 12 V for 20 - 25 min; became 400 to 600nm layer. Franz R Wagner- Blumenau SC Brazil July 6, 2009 A. If Henkel are referring to Phosphoric acid anodise the chemical are pretty much phosphoric acid and water so you can manage to just buy in from a chemical supplier and make up your own tanks.Also you do need a de-oxidise stage prior to anodise. You can also do this with a Phosphoric acid electrolytic deoxidise. Aerospace - South Wales, UK July 6, 2009 |
Q. My understanding from Henkel was just that I should use a phosphoric acid wash to remove oxidation and create an etching of the surface. They didn't say I should anodize the surface after etching, but they did say that bonding should be done within 4 hours of cleaning to prevent the formation of new oxides on the aluminum surface. This job is a one off so I don't want to get involved in a more complicated process than I need, if just etching will work sufficiently well enough. I was thinking about Alumiprep 33 [on eBay or Amazon] or similar for the wash.
Martin Hughes [returning],product designer - East Greenbush, New York USA
July 9, 2009
July 14, 2009
"adhesive Bonding"
by L.H. Lee
on
AbeBooks
or
Amazon
(affil links)
What Henkel are telling you sounds like the first stage of a surface treatment and much of the details will be be surrounding your exact definition of "strong bond". Myself and the earlier poster have taken that to mean structural. To prepare aluminium for bonding it is normal to remove any natural oxides and then regrow a porous oxide coating on the surface. A thick porous coating provides micro-roughness and a good mechanical key for the adhesive to adhere to.
If you don't do this you will end up with and adhesive failure mechanism where the adhesive will simply not bond to the substrate. This is exacerbated by heat and humidity. Without the oxide layer cracks will migrate to the metal surface and cause the aluminium to oxidise, The addition of the oxide layer actually increases stress at the crack tip and it runs along the adhesive/metal interface.
These coatings are also subject to degradation so there is often a time limit after the oxide has been applied. (4 hours is, by the way, the normal time limit after anodising).
Depending on how strong (and durable) you need the bond depends on how much effort you need to apply. If the bond is going to be indoors and not subject to high loads then you may be able to get away with some of the small scale manual operations. Deoxidise with phosphoric acid and touch up Alodine. If however your component is likely to be subject to loads, heat and or humid conditions you will need to improve your level of surface preparation.
As you are saying this is a one off I would seriously look at the Boe-gel/AC-130 process. It is designed for repair and is therefore good as a one off (kit form). There is little in terms of a hazardous waste stream and to be quite honest it is the easiest process to complete. If you can sand and paint you can already do it.
Aerospace - South Wales, UK
Q, A, or Comment on THIS thread -or- Start a NEW Thread