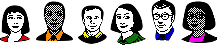
Metal finishing Q&As since 1989
-----
Stainless Steel Pretreatments before Powder Coating
Q. We are about to powder coat some stainless steel sheets of which will be 4 x 10 and range from a little less than 1/2" to 5/8" thick. What is the recommended way[s] to pretreat these panels. These panels will be used on an exterior of a building.
John KentileSalesman - Ashland, Virginia
April 10, 2009
A. Where to begin? I've been a powder coat process engineer for 20 years and I find this question to be absolutely incredible unless you are only talking about a panel or two. "Break" the surface tension of the stainless with an abrasive so that the powder has something to stick to then spray away.
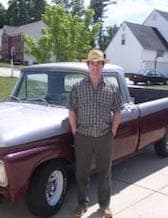
Sheldon Taylor
supply chain electronics
Wake Forest, North Carolina
A. As SS is one of the most difficult to obtain adhesion with PC, evaluate a product called "TWO Pack Etch Primer". The acid content will help with adhesion and the anti corrosive pigment content with weathering. Purchase from your local Auto supply stores or local auto body shop.
Terry HicklingBirmingham, United Kingdom
Q. Terry, do you think etch primers can withstand temperatures as high as 180 - 220 degrees. Will the bonding be the same and will it pass the impact test and bend test? Kindly reply, I am anxious to know this.
Shankar Omprakash Khandelwal- Coimbatore, India
April 25, 2009
A. You can either air-dry or bake the primer at 180-200 °C. This primer was originally formulated by the US Navy in 1940's and is a universally recognised formula. It has excellent adhesion to most metals and therefore improves the adhesion properties of most following coatings, liquid and powder, with the additional benefit of preventing some corrosion creep. However, it use has declined (but as far as I am aware not banned) due to the fact that it contains chromate pigments and an environmentally non-friendly solvent blend of low flash solvents. If you do wish to evaluate this material make sure you purchase the two pack variety and only apply a very thin coat (but still wet) otherwise you may lose adhesion. As with any new process you must carry out trials to satisfy you and your client that the system meets all requirements... maybe include the additional process suggest by Sheldon.
Terry HicklingBirmingham, United Kingdom
A. Because of high flexibility and surface tension, coating on stainless steel is often avoided, Stainless steel generally is aesthetically pleasing so I wonder why anybody would want to coat it, And if somebody wants to coat it any way why not go in for Mild steel (Ms steel) which is generally 5-6x times cheaper (or even aluminum) rather than stainless steel...Why do you think its called STAIN-LESS steel
Karan B- Bangalore India
Hi Karan, I would guess that Stainless Steel (SS) is powder coated because the client wants a more aesthetic feel to the item than that produced by SS. Maybe they also understand that if/when the to coating becomes damaged then the SS substrate will remain STAIN-LESS. Unfortunately, if/when powder coated Mild steel (MS) items if/are damaged then the MS steel substrate will become affected, this is called RUST (Iron oxide). Maybe that is why it is called Mild steel, it only has MILD resistance to attack from the elements :-)
Terry HicklingBirmingham, United Kingdom
A. We have occasionally over passivated/etched 304 stainless in our passivating tanks prior to powder coating.
Cliff Kuschelectropolishing shop - North Vancouver, British Columbia, Canada
Q. Hi,
I would like to know if there is a recommendation for cleaning parts before applying powder coating. We have 2 types of material that we are applying powder to, one is aluminum substrate with chem film applied on it. The other one is a 303 Stainless steel with a passivate process before powder. What do you recommend for cleaning or treating these parts before powder coating?
Engineer - Tijuana, B.C. Mexico
February 5, 2013
Ed. note re. Slang:
"Chem-film" is a colloquial term often used over here in the Americas meaning MIL-DTL-5541
[on DLA] Chromate Conversion Coating of Aluminum.
A. To meaningfully assist you any one of us would require more detail.
A chem film on Aluminium is not particularly enlightening as to the process?
303 is not a particularly spectacular performer in the corrosion stakes.
What performances are you looking for?
Please advise.
Regards,
Bill
Trainer - Salamander Bay, Australia
A. I feel sure this response will draw critics but note that no-one else has contributed to your enquiry to date so I advance my modest advice:
With Aluminium there has been no significant advance over a true chromate conversion coating of which I am aware especially with regard to "self healing properties".
With your passivated Stainless although it is an inferior corrosion resistant grade of Stainless you are face with a quandary.
Is the Powder grade you intend to apply a sufficient Corrosion Barrier? if so blast the passivate off, provide a key and apply the powder.
If not, leave the passivate on and apply the lower grade powder.
Hope this helps,
Regards,
Bill
Trainer - Salamander Bay, Australia
A. I'm a passivation guy, not a powder coating guy, but I have had the question put to me a few times, and I suspect that powder coating on stainless has more to do with the surface finish (roughness) than it does whether or not the part has been passivated. As such, if there are adhesion problems, I would see if a sandblasting/bead blasting operation improves the situation. If yes, they should move the passivation step to after the blasting or just skip it, since passivating before blasting is pointless.
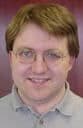
Ray Kremer
Stellar Solutions, Inc.

McHenry, Illinois
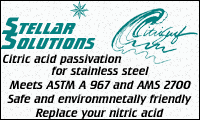
March 11, 2013
A. My self Prabhakar Deshpande, I am in Sheet metal fabrication field since last 40 years. I totally agree with Mr Kremer's views on pretreatment for Stainless steel. Basically Stainless steel is powder coated only to ensure better life for the product, if at all powder coating fails.
The only effective solution for Pretreatment prior to powder coating/painting on stainless steel is sand blasting or glass beading. One has to be careful while blasting as Stainless steel tends to distort as it is a bad conductor of heat.
- Pune India
September 8, 2022
Painting of stainless after passivation
Q. Hello,
I think this is a straight-forward question but I could not find an answer in any of the specs I've looked at. I was hoping someone could give me an answer.
15-5ph stainless - How long after passivation (nitric and sodium dichromate) can I proceed to paint.
I usually allow my parts to sit undisturbed after passivation for 24 hours to prevent contamination and allow the passive layer to form. Is it necessary to sit that long if you are applying paint?
Sincerely and Thank-you in Advance,
- Rincon, Georgia USA
March 28, 2016
Micheline,
24 hours is usually overkill, 2-3 hours is generally plenty for the passive oxide layer to form. However, as you say, since you are painting it almost becomes a moot point. Paint is one of the options for corrosion protection on carbon steel, the corrosion protection inherent to stainless becomes superfluous when you are covering it over.
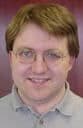
Ray Kremer
Stellar Solutions, Inc.

McHenry, Illinois
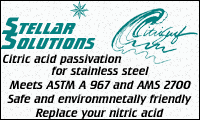
Q, A, or Comment on THIS thread -or- Start a NEW Thread