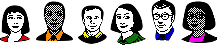
Metal finishing Q&As since 1989
-----
Obtaining long salt spray hours for Zinc Plating and Chromating
Q. I have a part that I am processing to a Zinc Clear, Chromate that requires a 600 hour salt spray to red rust. When I test the parts, I get to around 450 hours and the parts have red rust.
I have asked my customer for assistance on the sealer that is used to achieve the 600 hours, and had no response.
Does anyone have a name of a sealer that would get to 600 hours to red rust.
Thank you,
shop with plating line - Wyandotte, Michigan
February 26, 2009
![]() |
A. Amy, - Great Neck, New York February 28, 2009 March 1, 2009 A. Ms. Amy Kolodziej ![]() Asif Nurie [deceased] - New Delhi, India With deep regret we sadly advise that Asif passed away on Jan 24, 2016 ---- March 2, 2009 A. This is a good and interesting question and I believe you will get good responses from various suppliers connected with the www.finishing.com website. I would like to add two more parameters that will also affect your corrosion protection... - Budapest, Hungary March 4, 2009 A. Mr, Amy, ![]() P. Gurumoorthi electroplating process chemicals - Chennai, Tamilnadu, India |
July 2, 2009
Hello,
Thank you for all your great advise. Just to clarify, this is barrel plated, to a .00015 Min Zinc Clear Chromate.
The part is also a rivet, 3/8 body with a truss head.
- Wyandotte, Michigan, USA
"Zinc Plating"
by Herb Geduld
on
AbeBooks
or
Amazon
(affil links)
A. Hi Amy. 0.00015" zinc doesn't meet any standard anywhere that I'm aware of :-( Some people call it "commercial zinc" but I think that's just a euphemism for "the lowest thickness we can apply without excessive rejects". The good advice you've received here included a plating thickness of 35 to 40 microns if you stick with regular zinc plating or 25 microns of zinc-nickel. As a compromise, it sounds like you could try tripling or quadrupling your plating thickness, and then see where you stand. Good luck.
Regards,
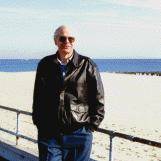
Ted Mooney, P.E.
Striving to live Aloha
finishing.com - Pine Beach, New Jersey
Salt spray hours for white chromate process
Q. I need clarification for clear white chromating process and salt spray test procedure as per MIL std.
Can anyone give the clear information to me!
- Chennai, India
March 27, 2012
A. Hi cousin Bharathi. Unfortunately, a prerequisite for a clear answer is a very clear question :-)
Can we assume the parts in question are made of steel? Steel can't be directly chromated, but several types of electroplating can be chromated. Is the item in question zinc plated? In most cases, this type of electroplating receives a chromate post treatment to deter "white rust".
No chromates that I know of are actually "white", but there are "clear" chromates, where the color of the metal will show through.
"MIL std." means U.S. Military Standard, and there are thousands of them. You need to describe what you want to do, then an applicable MIL spec / Mil std. can be selected. Many MIL standards will specify how many hours of salt spray testing the finish must survive, and most MIL standards will require that the salt spray test be conducted in accordance with ASTM B117, rather than a MIL spec salt spray test. Good luck; and get back to us, if you can, with several paragraphs clarifying your situation -- then we'll probably be able to guide your through it.
Regards,
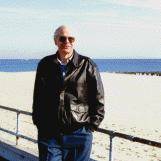
Ted Mooney, P.E.
Striving to live Aloha
finishing.com - Pine Beach, New Jersey
March 27, 2012
How many microns of zinc plating for 280 hours salt spray resistance?
Q.
Trying to find out how many microns of zinc is needed to obtain a 280 hour salt spray rating when tested to ASTM B117 test for red rust?
specification - huntington beach, California usa
June 20, 2013
A. Hi Ron. We appended your inquiry to a thread which should give you plenty of food for thought about the chromating and sealing being as or more important than the zinc plating thickness.
Still ... since, we all know that salt spray hours do not really correlate to real life and that customers are actually concerned about real life, and since the spec is for reasonably high hours rather than 48 or 96 or 192, I personally don't think .00015-.0002" is what they're really looking for. I expect they might be looking for, say, 8 micron (0.00032", 'moderate exposure') or 12-13 micron (0.0005", 'severe exposure') plating even if they don't exactly know it yet :-)
So, if you are the one doing the specifying, or are in an influential enough position to talk to the customer about clarifying the spec, you might be able to suggest that the requirement be 8 microns minimum, as well as the 280 hours. Good luck.
Regards,
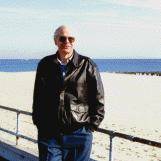
Ted Mooney, P.E.
Striving to live Aloha
finishing.com - Pine Beach, New Jersey
June 29, 2013
Zinc plating gets red rust in 24-hour salt spray test
Q. We'd requested our supplier to coat our bolts with Fe/Zn5A. The supposed minimum coating thickness is 5 micron. However, upon measuring the coating thickness, most of them were in the ranges of 1 - 5 microns. Since, our customer requires the bolts to withstand 48 hours of salt spray testing, we opted for the use of sealant. However, once the bolts were salt spray tested, it could not even withstand red rust for 24 hours. Is there anyone who could help to explain why?
Al Fauzi- Johor, Malaysia
February 1, 2019
A. Hi Al. Although I don't know what spec you are referring to, if you have 1/5 of the 5 microns zinc thickness considered adequate for 'mild' exposure you can't expect much if any corrosion resistance. The bigger question is: if the spec was 5 microns, why did they plate it to 1-5, and why are you accepting it?
Regards,
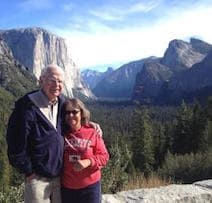
Ted Mooney, P.E. RET
Striving to live Aloha
finishing.com - Pine Beach, New Jersey
February 2019
Thanks, Ted. Anyway, the spec is ASTM F1941/F1941M-16. We actually just discovered that the thickness is below the requirement. Since, the part was an old stock, we thought of salvaging the stock by using sealant. But, from the results of salt spray testing, apparently that didn't work.
- Johor, Malaysia
February 7, 2019
Q, A, or Comment on THIS thread -or- Start a NEW Thread