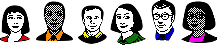
world gathers for metal finishing
Q&As since 1989
-----
Galvanizing flux: Ammonium chloride requirements and analysis

Q. I am a chemical engineer from Ethiopia and I was trying to understand galvanizing flux using Zinc ammonium chloride. My question is can someone dictate to me the step by step process, please?
Regards,
- Ethiopia
February 10, 2024
A. Hi Abreham,
I am not quite sure what your actual question is, whether it's how to make galvanizing flux, how to analyze and control it, or how it is used, etc.
But I think Dr. Cook's article "LOWER ZINC IN HOT DIP GALVANIZING" might be what you are looking for :-)
Luck & Regards,
Ted Mooney, P.E. RET
Striving to live Aloha
finishing.com - Pine Beach, New Jersey
A. So called "Zinc ammonium chloride" is a mixture of zinc chloride and ammonium chloride. It is mixed in various ratios of the two components, mainly double salt (2:1 NH4Cl to ZNCl2), and triple salt. (3:1).
It is used as an aqueous solution of typically double salt 450 g/L and triple salt 300 g/L (but this varies according to local practice).
The purpose of the ZnCL2 is to prevent rusting between the flux tank and the zinc tank. The NH4Cl is involved in a series of reactions at the interface between the steel and the zinc.
Buy the pre-mixed powder, or liquid, and dilute to required strength. The steel to be galvanized, after cleaning in a pretreatment regime gets dipped in that aqueous solution before immersing in zinc.
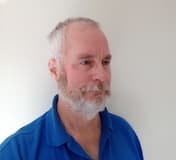
Geoff Crowley
Crithwood Ltd.

Bathgate, Scotland, UK
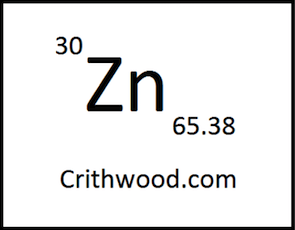
February 18, 2024
⇩ Closely related postings, oldest first ⇩
Q. Hi
I'm a chemical engineer in a new galvanizing plant in Egypt, a want to make a flux tank control but I cannot determine the concentration of ammonium chloride in the tank, in fact the flux tank ph = 3 and I think that value is low, so I want to know the ammonium chloride content to increase it, by the way what is the suitable amount of ammonium chloride should be added to increase the ph by 1 degree per m3?
Thanks,
chemical eng - Cairo, Egypt
July 7, 2008
"Practical Inductively Coupled Plasma Spectroscopy"
on
AbeBooks
or
eBay
or
Amazon
(affil links)
A. Measuring the pH of flux is difficult, and often misleading. Most of the usual techniques do not work.
ICP [on
eBay
affil links]
is one way to measure the ammonium chloride concentration.
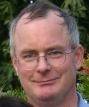
Geoff Crowley
Crithwood Ltd.
Westfield, Scotland, UK
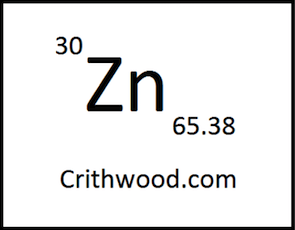
A. Sirs:
Until about 1985 I did ammonium chloride in flux using Kjeldahl distillation and published the method in the magazine,
METAL FINISHING. Now I use a self-developed heat of solution method which is extremely simple. This method takes advantage of the fact that when zinc chloride is dissolved in water the solution gets hot, whereas when ammonium chloride is dissolved in water the solution gets cold. Under the conditions that I use there is about a 35 °C differential. I have taught this method to many galvanizers who use it once or twice a month.
In another of my publications in METAL FINISHING, I sent out 13 samples all from the same batch of flux made up here in my lab with an ACN of 1.00 (ACN = ammonium chloride/zinc chloride; e.g., equal amounts of ammonium chloride and zinc chloride, this is between the double and triple salts). All 13 labs failed to provide a usable result even though most of these labs are "certified" by the US government and charge a few hundred dollars/test.
It is true that a newly dissolved flux solution has a pH near 3. The best operating pH for flux is 4.2. "pH" is pH not "ph." This is the negative log base ten of the hydrogen ion concentration (e.g., when the pH changes by one unit the hydrogen ion concentration changes ten-fold, "pH" is actually a mathematical term applied to chemistry.) Ammonium chloride is NOT what to add to change the pH! pH is NOT measured in degrees.
Geoff, I am not familiar with using ICP (inductively coupled plasma) [on
eBay
affil links]
for measuring ammonium chloride in flux solution. I am under the impression that ICP is used like AA or AE except that it is more sensitive because the temperature is hotter. AA or AE is used for 30 or 40 metals that have electrons much further from the nucleus and more easily promoted to outer shells to emit energy upon return. Actually it doesn't really matter because the folks with ICP are very reluctant to run samples with zinc in them because of the memory effect.
Regards,
Galvanizing Consultant - Hot Springs, South Dakota, USA
Q. Thanks sirs for your support.
So there is an analytical method to measure the amm. chloride conc.; actually I use a raw liquid flux solution with (800 g/l). By analysis I found that the zinc chloride conc. is 545 g/l
Then I dilute the sample (1 liter water and 1 liter raw flux) so I expect that the conc. of zinc chloride will be 272.5 g/l, but I found it 331 g/l by analysis; please tell me where is the problem (the analysis done by EDTA AND PERMANGANATE)
Second, the flux tank conditions are: (temp=50 °C , baumé=30, pH=3.0); if I dilute it to reach a pH=4.2, then baumé will be = 13-14, so (I think that it is low ), I cannot find the optimum conditions.
chemical eng - Cairo, Egypt
August 10, 2008
A. Sir:
It is possible that your local fertilizer company may have a way to test for NH4Cl. The method would likely be Kjeldahl distillation or total nitrogen. I personally would not trust the result however. If the total (ZnC2 plus NH4Cl is 800 g/liter and the ZnCl2 alone is 545 g/liter then the NH4Cl alone is 255 grams/liter (800-545). This would be an "ACN" of only 0.47 (255/545). This ACN corresponds to the mono salt which is commonly used at high concentration for continuous sheet galvanizing. It would NOT be a good flux for general galvanizing.
EDTA [on
eBay or
Amazon]
is the proper titrant for zinc +2 ion. There would be no use for permanganate in this titration (except to oxidize iron+2 to iron+3). This is a very messy way to determine zinc because the orange sludge formed from iron +3 would contain liquid that would also still contain zinc.
For approximate zinc chloride the density in baumé does quite well if the NH4Cl is fairly well known. I have full tables for this.
Could you explain a bit more about your operation, especially the type of galvanizing that you do.
Regards,
Galvanizing Consultant - Hot Springs, South Dakota, USA
A. I would determine Zn via an EDTA titration, and the ammonium chloride via an ion selective electrode.
If I/my employer was too cheap to buy the probe, I'd distill off the NH3, with the Kjeldahl method, then titrate the distillate with 0.02 N H2SO4.
You might have luck using Nessler's reagent [on
Amazon]
for the ammonia determination, if you prepared the proper matrix matched standards. Lots of set up time, but possibly quicker than the above two methods, after the initial work of making the standard curve is done.
I also don't see how ICP could be used for NH3.
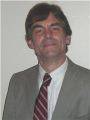
Dave Wichern
Consultant - The Bronx, New York
August 22, 2008
Q. Sir
thanks for your support.
Actually I have a concentrated flux solution with 800 g/l, 89% zinc chloride and 11% ammonium chloride
I put the concentrated flux sol. with water into the flux tank to adjust the baumé to 30, now the pH BECOME = 2.0
I want to:
1- increase the pH to 4.2
2- determine the ammonium chloride to try to adjust the components percentages ( please list the procedures of the process of heat of solution)
3- the other procedure to make a full control on the flux solution
I want to tell you some facts
1- the process is hot dip galvanizing
2- I have two rinse tanks before flux
3- the flux temp. =50 c
4- I have a flux regeneration unit by peroxide and ammonia (I will work at Jan 2009)
5- the work started from 10 months only
6- I work to prepare an acidic degreaser before the pickling process by hydrochloric acid (I'm sorry to late the reply)
Thanks sir.
chemical eng - Cairo, Egypt
Q. Kind Sirs:
Greetings! I understand that Dr. Cook is saying he has a quick and simple way to determine the ammonium chloride number in the flux solution via heat of solution (or temperature difference?) however, in all honesty I cannot seem to follow through the method. Guesstimates for actual ACN can be deduced from pH and baumé but still has to be based on the initial flux formulation and will take experience. For a newbie, this will be tedious. Inasmuch as Dr. Cook mentioned that he has already taught the method to galvanizers in the past, I am asking if the kind Doctor can give us the details of the procedure in this thread.
Thank you very much and more power!
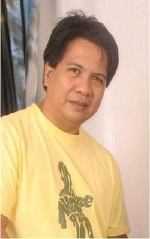
Barlow Campano
galvanizing chemist - Jeddah, KSA
May 18, 2011
A. Sir:
The "bake and shake" method of testing flux does NOT yield ACN. It gives ACNV which is the correct way to control the volatile (ammonium chloride) and the non-volatile components (zinc chloride, ferrous chloride, and sulphate) of hot dip galvanizing flux. As I previously mentioned on this thread this method is based on the fact that ammonium chloride is endothermic (gets cold) when it is being dissolved in water and zinc chloride and iron (+2) are both exothermic (gets hot) when dissolved in water. Also ammonium chloride contributes little to baumé, whereas zinc chloride and iron chloride give high baumé solutions when dissolved. The method depends on a series of known ACNV's and equipment that is calibrated. It is not possible for me to give the methods or calibrations on a web site.
Regards,
Galvanizing Consultant - Hot Springs, South Dakota, USA
for Shops, Specifiers & Engineers
"Hot Dip Galvanizing of Steel Structures" by Kuklik & Kudlacek (2016)
avail from eBay, AbeBooks, or Amazon
"Handbook of Hot Dip Galvanization" by Maass & Peissker (2011)
avail from eBay, AbeBooks, or Amazon
"Galvanized Steel Reinforcement in Concrete" by Stephen Yeomans (2004)
avail from eBay, AbeBooks, or Amazon
"Hot Dip Galvanizing -- A Guide to Process Selection & Galvanizing Practice" by M. J. Hornsby (1995)
avail from eBay, AbeBooks, or Amazon
"Faults in Hot-Dip Galvanizing" by Dietrich Horstmann (in English, French & German)
avail from Amazon
"User's Guide to Hot Dip Galvanizing for Corrosion Protection in Atmospheric Service" by NACE (1997 only rarely avail.)
avail from AbeBooks, or Amazon
(as an Amazon Associate & eBay Partner, finishing.com earns from qualifying purchases)
Q. Sir:
It seems to me that your quick method suits best in determining (estimating) the ACN value of an undissolved flux salt such as for quality check of bulk order in lieu of the individual analyses of ammonia, zinc, and chloride. However, pH and baumé are good gauges when it comes to controlling the ACN in a flux solution. As to the differential temperature procedure, I will find time to perform it in the lab, thank you anyways. Nevertheless, Barlow is just fine for me sir.
Best regards.
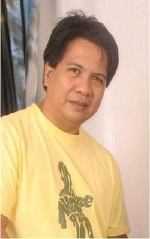
Barlow Campano
galvanizing chemist - Jeddah, KSA
May 21, 2011
Barlow:
My "bake and shake method" is not quick but it is simple once it is properly set up. It gives ACNV (ACNV = ammonium chloride/(zinc chloride + iron (+2)chloride) NOT ACN. The ACNV value is quite accurate and extremely useful in controlling flux. ACN is NOT useful in the presence of high iron(+2) chloride. pH and baumé do NOT control ACN and in fact are not even related to ACN.
Regards,
Galvanizing Consultant - Hot Springs, South Dakota, USA
Q. Dear Dr. Cook:
Sir, I use both pH and baumé (and recently % HCl by weight) as indicators of ammonium chloride and zinc chloride balance in the flux solution depending on the initial formulation.
I make use of the fact that zinc chloride dissociates to form the HCl needed to remove the remaining iron oxides in the fluxed steel and aqueous zinc oxide that aids in providing a protective layer. It is the zinc chloride number that pulls the pH down due to the above reaction rather than the ammonium chloride number that remains as is in the solution (however, a small portion is believe to be dissociated to ammonium hydroxide). The ammonium chloride provides most of the oily protective layer that sublimes to ammonia and again HCl in the zinc bath but recombines at lower temperature forming the white smoke. This is how the ACN or ZCN becomes related with pH.
Given that zinc chloride is almost twice as heavy as ammonium chloride, this is being used as gauge to determine the need to add more zinc ammonium chloride or just ammonium hydroxide alone to convert the HCl and/or FeCl2 carryover in the flux to more ammonium chloride. As you have advised, it's not good to make use of straight ammonium chloride as pre-flux because the galvanized steel would become so clean that it can detect entrapped dross or ash in the form of pimples. Replacing the lost zinc chloride (or zinc oxide rather) is then necessary to add texture to the zinc coating and thus avoid the concern. % HCl in the flux solution is also being correlated with the amount of zinc chloride.
Nevertheless, there is no substitute to an accurate volumetric or spectrophotometric ammonia, zinc, and chloride analysis to really have full control of the ACN.
Regards.
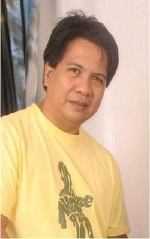
Barlow Campano
galvanizing chemist - Jeddah, KSA
May 25, 2011
A. Barlow:
I have read, with great concern, your last posting several times. In fact I have given your last posting much thought today. You and I are obviously NOT communicating on this website. I have numbered your sentences and I can start to respond as follows:
(1) pH, baumé, HCl, or original formulation are in no way related to ACNV of a process flux solution.
(2)ZnCl2 does not dissociate into HCl. Zinc oxide is insoluble in water. Zinc chloride provides a layer that inhibits rust.
(3)Kindly define your "zinc chloride number." What does "zinc chloride number pulls down the pH," Mean? What is your proof that--"a small portion is believed to be dissociated to ammonium hydroxide?"
I cannot further respond to postings that are contrary to my education and experiences of nearly 40 years working in hot dip galvanizing.
I think I will buy a fishing license and some worms tomorrow and go fishing for walleye and bass :-)
Regards,
Galvanizing Consultant - Hot Springs, South Dakota, USA
![]() |
A. Barlow: Galvanizing Consultant - Hot Springs, South Dakota, USA June 2, 2011 Q. Dear Dr. Cook, ![]() Barlow Campano galvanizing chemist - Jeddah, KSA June 2, 2011 |
A. Barlow:
It occurred to me that you may have tried to get my attention. It is unlikely to happen again. The fishing today was a bit slow but we saw a mother goose and four babies.
The "V" part means using both zinc chloride and iron (II) chloride in the denominator as I previously reported.
I am not able to follow your reasoning in your next few sentences.
In the USA there are some flux companies that use "ratio" which is the inverse of ACN (1/ACN = ratio). This ratio is NOT the OPPOSITE of ACN. Amphoteric means that a material can act as an acid or a base and thus soluble in both.
The "bottom line" on the bake and shake method is that any solid flux when dissolved in water gets colder when the ACNV is higher. Or with sufficiently low ACNV gets hotter (as it is dissolved in water) as the ACNV gets lower.
The method(s) are easy and quite accurate once it is fully calibrated and tables are developed, as I have done.
Now I have other "fish to fry."
Galvanizing Consultant - Hot Springs, South Dakota, USA
Q. Dear Dr. Cook:
On ACN and Ratio, isn't it sir that mathematically the expression: ratio = 1/ACN means that ratio is inversely proportional to ACN where the term inverse is synonymous with opposite? Moreso, by substitution:
Ratio = 1/(wt. NH4Cl/wt. ZnCl2)
multiplying both the numerator and the substituted denominator with the inverse of the substituted denominator will yield the following:
Ratio = 1 x (wt. ZnCl2/wt. NH4Cl) / (wt. NH4Cl/wt. ZnCl2) x (wt. ZnCl2/wt. NH4Cl) where the denominator cancels out and becomes 1 therefore what remains out of the equation will be:
Ratio = (wt. ZnCl2/wt. NH4Cl) / 1, OR simplifying
Ratio = wt. ZnCl2/wt. NH4Cl, which now becomes the exact opposite of ACN.
Whew! I never expected this discussion would end up with algebra and a hot seat.
All the best.
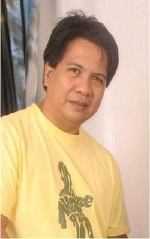
Barlow Campano
galvanizing chemist - Jeddah, KSA
Q. Dear Dr. Cook:
Sir, I just read the second half of your numbered concerns and I can't help but answer your queries to wit:
a) From the respective MSDS's of the flux salts
NH4Cl ZnCl2
Solubility: 29.7 g/100 g water 423 g/100 g water
Density: 1.53 g/ml 2.91 g/ml
pH: 5 (10% aq. sol'n.) about 4 (aq. sol'n.)
Boiling Pt.: 520 732
Melting Pt.: 338 (sublimes) 290
b)Adding ammonium hydroxide to the flux solution
b.1 2NH4OH + FeCl2 (in the flux sol'n. from carryover) = 2NH4Cl + Fe(OH)2
b.2 NH4OH + HCl (in the flux from carryover) = NH4Cl + H2O
I was actually making an analogy from your previous commentary on straight ammonium chloride as pre-flux where you said "Ammonium chloride alone as a hot dip galvanizing flux solution is extremely bad. It is even worse if the molten zinc is high grade. After fluxing in ammonium chloride the steel corrodes badly before it reaches the kettle and the zinc spatter is extreme. With high grade zinc the dross pimples are entrained in the zinc giving many sandpaper pimples on the steel, especially on highway guardrail.". I theorized that because ammonium chloride breaks down into HCl and NH3 in the zinc bath, the reaction simultaneously clean and galvanize the dipped item making the previous (unremoved) iron oxidation from the flux solution very evident on the article when it leaves the molten zinc bath.
Nevertheless, I must agree that nothing much happens to the pickled material when it reaches a flux solution of pure ammonium chloride except however to the formation of a protective layer. I'm also having this idea that the oily characteristic of the protection may be proprietary.
That's how far I got Sir.
Sir, to augment on what seems to me like an oily protective layer on the fluxed material of which I think is proprietary combination, I am now with the belief that it might not be oil after all but trapped moisture by zinc chloride since ZnCl2 itself is hygroscopic and even deliquescent. Ammonium chloride alone dries up to a white powdery material.
Thank you and best regards.
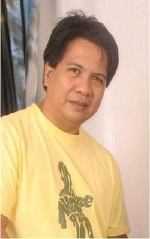
Barlow Campano
galvanizing chemist - Jeddah, KSA
June 5, 2011
Q. Hi My Dear
Please Guide me about "how to remove ferric chloride in flux solution"
My Tank has 80 Ton Capacity and sedimentation has been for a very long time .
happy new year
best regards,
- Tehran, Iran
December 30, 2011
A. Sir:
There are three forms of iron that can be in a galvanizing flux tank:
(1) Metallic iron with oxidation number 0. This would come from workpieces falling into the flux tank or steel shot from "sandblasting". This metallic iron dissolves slowly or moderately fast depending on the pH of the flux. Metallic iron can be removed using a strong magnet.
(2) Ferrous iron with an oxidation number +2 is formed when metallic iron dissolves in a flux solution with a pH lower than 5. This type of iron is titratable using hexavalent chromium. In excess in the flux solution it causes excess ash and in the case of a "wet" kettle causes dross. It also causes thicker zinc on the product. If the ferrous iron is more than about 3% there is no reason to try to purify (remove iron) because the entire tank will turn to solid ferric hydroxide.
(3) Ferric iron with oxidation number +3 is caused by oxidation of ferrous iron by a pH higher than 5 by air or peroxide. Ferric iron precipitates with three hydroxides to form orange, insoluble ferric hydroxide that goes to the bottom of the flux tank.
Nearly forty years ago I went around the USA purifying flux solution (removing iron and sulphate, if sulfuric acid was used as the pickle). When the sulphate was about 1.5% and the iron (+2) was about 0.6%, upon purification the %GZU decreased from about 9% to about 6%. The money yearly savings were usually between $0.5 to $1 million/year from zinc savings and much, much less zinc clean-up. Ahh--The Old Days.
To remove the iron (+3) sludge you get scoop shovels and put the orange sludge into barrels. It's a sweaty job.
Regards,
Galvanizing Consultant - Hot Springs, South Dakota, USA
Q. I am sorry to burst in like this and my presence most likely will be unwelcome to someone...
Any advice for treating skin burns caused by zinc ammonium chlorides and sweat "pooling" in waistline. all other posts and forums simply refer me to MSDS which only has first aid for ingested, inhaled or in eyes. If any of you gentlemen have experience with this I would love to hear from you. Have had burn or rash eight to ten months a year for three years now and just want it gone.
HotDip plant employee - United States
July 15, 2015
A. William,
I'm not sure if what you really need is treatment or just better prevention. I found an MSDS for zinc ammonium chloride that lists first aid for skin contact, of course all it says is the standard rinse the area and seek medical attention. The page
http://www.johnsonmfg.com/temp/HWhtml/ZCFS3p~1.htm ⇩
goes into more detail about it: "ZnC12 absorption through your skin isn't likely, but absorption onto your skin is highly likely. This is due to the desire of ZnC12 to be wet. It will cling to the water molecules in the cracks of your skin, and once there, it holds on tight."
I am not a doctor, but due to the self-renewing nature of skin I rather suspect that any trapped zinc chloride will be cast off on its own eventually as long as you are not continuing to add more zinc chloride to the area. It sounds like you need better protective clothing, and maybe in the meantime some good skin moisturizer. You may want to discuss the matter further with a dermatologist and your plant's safety manager.
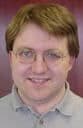
Ray Kremer
Stellar Solutions, Inc.

McHenry, Illinois
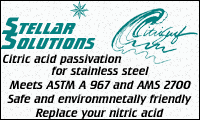
July 16, 2015
[Ed. update: The above link has broken. Thankfully, The Internet Archive preserved a copy

These days information often appears on the internet, then disappears forever. If that bothers or frightens you please consider a donation to The Internet Archive.
? Sir: Do you use nickel in the kettle?
Regards,
Galvanizing Consultant - Hot Springs, South Dakota, USA
⇦ (tip: readers rarely show interest in abstract questions, but people's actual situations usually prompt responses)
Q. What role does ammonium chloride play in zinc ammonium chloride flux?
Anand KumarKriso Enterprise - Howrah, West Bengal, India
September 17, 2018
Q. Dear sirs,
I have read the Kjeldahl method is the most accurate technique to measure the NH+4 content in existing flux --
(i) has anyone really tried it? Also
(ii) existing flux consists of Fe2+ which precipitates when NaOH is added; in view of that, does the method still work efficiently?
As purchasing a set of Kjeldahl equipment costs more than RM30k in Malaysia, so would to have a confirmation from the seniors here.
Thanks,
Prestar Galvanising - Selangor, Malaysia
January 3, 2019
Ed. note: Sorry, this RFQ is old & outdated, so contact info is no longer available. However, if you feel that something technical should be said in reply, please post it; no public commercial suggestions please ( huh? why?)
A. In the 1980's I did many KJ tests on flux and it works just fine, but does take skill. Fertilizer companies normally have good skills in this test and likely is less expensive than getting the glassware to do it yourself. The answer is normally g/L of ammonium chloride.
You have made a mistake thinking you need to add NaOH to take out iron. You need both hydrogen peroxide and ammonium hydroxide and you must add the ammonium hydroxide first. NaOH will destroy your flux.
What is your iron (Fe+2) content? and what is flux tank size?
Regards,
Galvanizing Consultant - Hot Springs, South Dakota, USA
A. The Kjeldahl analysis is not specific for ammonia. It measures total nitrogen content which, of course, includes ammonia.
It can be highly accurate in skilled hands but is slow and tedious.
A far simpler method is to boil a known sample with a known excess of sodium hydroxide until all ammonia is driven off and then titrate the residual hydroxide.
However, you cannot just buy the kit and assume that the knowledge of how to use it comes free. Even the simple method requires some basic knowledge of technique and without it you will get unreliable and misleading results.
You probably have a local college with a chemist who will give you the basics but my best advice would be to speak to your flux supplier.
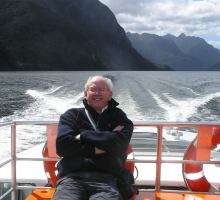
Geoff Smith
Hampshire, England
Q. To Dr. Cook:
(i) The NaOH that I mentioned is for the Kjeldahl's method, which will only be added into a sample volume hence it will not affect the whole pool.
(ii) We do understand NH4OH and H2O2 are used to reduce iron and a filtration system is now incorporated to our flux pool, however, not all iron can be removed which causes precipitation in the sample when NaOH was added for Kjeldahl's method. Hence do I continue to cook the mixture to evaporate NH3 off or will the ppt. cause inaccuracy?
(iii) Our Fe content is kinda high which is 1.4++% as rinsing water is not changed periodically which has caused excessive carryover. We are gonna replace it.
(iv) The capacity is around 30 tonnes of liquid. With a geometry of 7m height x 3m long x 1.5m wide.
(v) As compared to Kjeldahl's method, I have considered using an NH4+ ISE. Issue is that the maximum reading can only be 1M hence was thinking of using serial dilution to make the NH4+ conc. in range and with the measurement, use back calculation to obtain the real conc. Does that make sense?
Q. To Mr. Geoff:
Thanks for the information. I am looking into the time consumption as well. As each round of testing would at least take up to 2-3 hours following the standard Kjeldahl's method; hence I am looking into the NH4+ ISE as we will need to monitor it daily for the moment as the pool is totally off spec now. What do you say?
Prestar Galvanising - Selangor, Malaysia
A. Geoff, KJ works perfectly for ammonium chloride in galvanizing flux. I have used it for many years and have made standard solutions containing zinc chloride, iron chloride, and other chlorides and there are no interferences. I do not share your confidence in flux suppliers testing fluxes properly. 22 years ago I made up a flux solution with a specific composition and sent portions of it to 13 companies for testing. All results were useless. World- wide there are many contaminated galvanizing fluxes. I do not expect your alteration to the KJ to work. What about the OH-1 tied up with iron or zinc at the bottom? Also what about the colors interfering with the end-point detection?
Sir, Iron (III) hydroxide at the bottom of the boil flask does not interfere. If you can find a fertilizer company nearby, that does KJ every day, they may do it for a small fee. Here the cost is $25/sample and I have one client that does testing this way. The specific ion electrode for ammonia is high priced and the flux needs to be well diluted with distilled water. From which country do you buy flux? Is your kettle very deep as you indicate?
I now use my bake and shake method and it is easy with excellent results. I have a number of clients that also use the method to advantage. It is based on "heat of solution." ZnCl2 gets hot when dissolved and ammonium chloride gets cold when dissolved. Also there is a second method using density to get ACN directly.
We are working on a Dynamic test (four steps) for testing flux. The first takes a 2 inch x 2 inch x 1/4 inch angle 5 inches long and pickling it and fluxing it and seeing if it will galvanize in 20 seconds. All of my clients have passed this test. There are three more steps in the dynamic testing. I am considering posting it on this web site.
Regards,
Galvanizing Consultant - Hot Springs, South Dakota, USA
January 7, 2019
Dr Cook: I agree completely that KJ is a perfectly good and accurate method in capable hands.
My point was to question if it is suitable for someone with limited analytical experience; otherwise the question would not have been asked.
The indirect method I suggested is simple, quick and in inexperienced hands probably as accurate as KJ would be.
However, your advice to farm out the work is by far the best option.
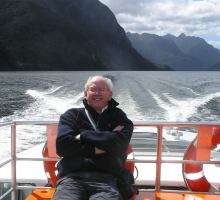
Geoff Smith
Hampshire, England
January 9, 2019
Q. Dear Dr Cook,
Thank you very much for your experienced opinions. I am wondering does the bake and shake method only cater for new flux preparation or can it be used as a method to measure ACN of existing flux. I am wondering this as the temperature of the existing flux is already fixed so how does the heat of solution is used to find out the ACN?
Thanks,
Prestar Galvanising - Selangor, Malaysia
January 9, 2019
Q. Hi
I am a mechanical engineer but work in hot dip galvanized pipe industry in Vietnam. My factory has been in operation for only 1 year and there are some problems related to product quality. Zinc layer after plating does not adhere to the iron layer, but it is inflated when carrying out bending test (%Si and %P in iron not more than 0.02%, zinc oven temperature is 450 °C, time of soaking tube in zinc furnace about 2 minutes). I think it may be because the ratio of ammonium chloride and zinc chloride is not suitable (ammonium chloride = 271 g/L, zinc chloride = 175 g/L). Hope someone will give me the best rate for this flux and explain to me the reason above.
This is my method; I hope it helps someone:
- ZnCl2: take 1 ml of sample solution + 50 ml of water + 25 ml of pH10 buffer (buffer pH10 = 54 g NH4Cl into 500 ml of distilled water, add 350 ml of NH4OH 25% in, determine with 1L of distilled water) + a small amount of substance EBT directive (Mordant Black T). Titrate with EDTA solution 0.2M until it turns green (EDTA 0.2M = 74.45 g C10H14O8Na2.2H2O dissolves in hot water and set 1L of distilled water).
Zn2+ (g/L) = EDTA volume 0.2M x 11.65
ZnCl2 (g/L) = EDTA volume 0.2M x 24.27
- NH4Cl: take 1 ml of sample solution + 75 ml of water + 1 ml K2CrO4 2%. Titrate with 0.1N AgNO3 solution until red.
NH4Cl (g/L) = 5.77 x AgNO3 0.1N volume - 1,924 x Zn2+
(I am not good at english so I use google translate, so readers are hard to understand).
Vina One Steel Manufacturing Corporation - Ho Chi Minh, Vietnam
January 30, 2019
A. Pham, By pipes galvanizing 1 year you are certain to have much Fe+2 carry-over from your HCl pickle into the flux and there may be as much FeCl2 in the flux as there is ZnCl2. The Fe+2 in your flux can be easily titrated with dichromate.
What does "inflated" mean? Does it mean "peeled off"
I prefer P at 0.01% or lower.
Your methods for testing ZnCl2 and NH4Cl, I understand perfectly, but they do not work. Iron interferes with the zinc test and if you are using "hard" well water so does calcium. For NH4Cl you are getting total Cl-1 and doing a subtraction. You cannot get correct NH4Cl from wrong ZnCl2 and total Cl-1.
I recommend that you do the first and fourth tests in my new dynamic flux tests as shown in the on-line library on this website. Then post the results on this website. photo (of 20 second test) and minutes (for cook-off time).
FLUX: What country do you buy your flux? What is your flux density (g/ml)? What is temperature of flux? What is color with 50 ml flux + bromophenol blue
[on
eBay or
Amazon]
? Do you have an effective wetting agent in your flux solution? Are your problems (post photos) mostly on the outside or inside of the pipes? What diameters of pipes do you galvanize?f What is TDS (total dissolved solids) of your tap water? Do you have water softener?
Regards,
Galvanizing Consultant - Hot Springs, South Dakota, USA
January 31, 2019
Q. Hi everyone!
I want to produce ZnCl2.NH4Cl solution with baumé of 30° and ZnCl2 ratio: 34%.
How do I do it? Should I add the chemicals separately or is there any process for this production technique? Is the thing to be done to mix the chemicals in determined amounts?
I researched many books and forums but I didn't find anything for this situation.
Thank you in advance
- Istanbul, Turkey
February 19, 2019
Ed. note: Readers, please always introduce yourself. As Geoff Smith already noted, instructions may be offered which are appropriate for a well-trained chemist or chemical engineer in a properly equipped & regulated chemical manufacturing plant, whereas suggesting the same to a student with limited chemical training might be dangerous :-)
Q, A, or Comment on THIS thread -or- Start a NEW Thread