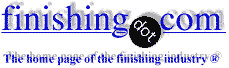
-----
Passivating Stainless Steel with citric acid
Q. What are the risks of using citric acid rather than Nitric acid on Stainless Steel manufactured products? Oxidation was mentioned? Also does citric acid remove less than Nitric Acid? Would a fallout occur because of this?
Ellyce ChrisbaieQC Manager - Westwood, Massachusetts
2007
A. Personal opinion. Citric and nitric are a "wash" on 300 series SS. On 400 series, the citric will blow nitric out of the water. That is assuming that you are using a citric from a good company and not a home brew. The major advertiser of citric at this site has a product that I like, and I am not on their payroll.
James Watts- Navarre, Florida
2007
A. Passivation is the controlled "oxidation" of the nickel on the surface of stainless steel.
citric acid removes free iron, PERIOD.
Nitric Acid (and sometimes with dichromate depending on the alloy) also removes the free iron BUT then control oxidizes the surface to prevent further oxidation (unless exposed to a reducing liquid or chloride).
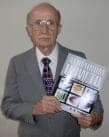
Robert H Probert
Robert H Probert Technical Services

Garner, North Carolina
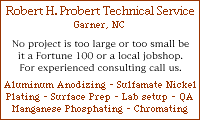
2007
A. Quite the contrary, the risks are in using nitric. Safety risks, risks to surrounding equipment from fumes, risk of etching the surface of your parts.
Citric removes "less" than nitric in the sense that it removes the iron only and leaves behind the chromium and other metals. This is beneficial both from a waste disposal standpoint and from a corrosion resistance standpoint, as the citric leaves a deeper chromium-enriched layer than nitric.
And yes, the chrome oxide layer is formed not in the bath but in the air afterwards. This does not prevent citric from delivering equivalent or even superior corrosion resistance results.
Passivation of stainless steel as defined by ASTM A967 is the removal of the free iron from the surface, which enables the passive chrome oxide layer to form. Though yes, from a general chemist's perspective, the passivation is the formation of the unreactive oxide layer itself.
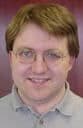
Ray Kremer
Stellar Solutions, Inc.

McHenry, Illinois
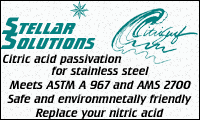
2007
Regarding ASTM A967. In between "free iron from the surface --- and which enables" ALSO appears what was left out, namely "with a mild oxidant". citric acid is not an oxidizing agent, nitric acid at the recommended concentrations for the various alloy IS an oxidizing agent. Let's quote the whole sentence.
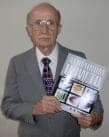
Robert H Probert
Robert H Probert Technical Services

Garner, North Carolina
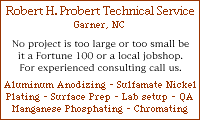
2007
Thanks Robert! You're clearly right to call attention to selective quotation, but after 12 years of countless postings on the subject here, I admit that I too am weary of this "debate" between proponents and opponents of citric acid passivation.
A decade ago we asked for references to independent studies showing that citric acid "worked", and we immediately received them. For me personally, I don't feel the shoe is on their foot anymore, but on the other foot; i.e., that those who remain opposed to citric acid passivation should quote some recent independent studies explaining in what cases or under what circumstances it isn't a satisfactory substitution.
For my own part I've had enough experience with presumably good parts being inexplicably destroyed by nitric acid, plant evacuations caused by steel parts accidentally put into nitric acid passivating tanks and releasing clouds of toxic poisonous NOx, harassment from regulators with their nonsense that a nitric acid passivation tank is a "nitrate factory" which must maintain "nitrate production stats", and pressure from the government against using nitric acid because of its ties to explosives, to want to continue to use nitric acid for passivation unless there is clear and present evidence that in a specific case it remains absolutely necessary.
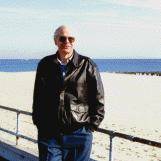
Ted Mooney, P.E.
Striving to live Aloha
finishing.com - Pine Beach, New Jersey
2007
2007
Not to belabor the point with petty bickering, but while the citrate ion is not an oxidizer, hydrogen ions, and by extension every type of acid, are. Iron atoms are oxidized in order to remove them from the metal surface as iron ions, by both citric and nitric acid. The oxidation of the chromium occurs in the air later on, which is also explicitly stated in ASTM A967.
Regardless of the exact mechanism, if it didn't work, people wouldn't be using it.
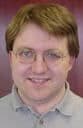
Ray Kremer
Stellar Solutions, Inc.

McHenry, Illinois
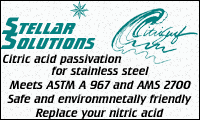
A. citric acid is the reducer and promote de-passivation of the surface. Passive film formed after citric acid treatment is very thin. Further increase in thickness of such passive film take place during rinsing and drying. Such operations are hard to control. Therefore citric acid is very effective in removing free iron, but not sufficient enough in actual passivating. We recommend that after citric acid treatment stainless steel is treated in nitric acid solution or other more environmentally friendly solutions with high redox-potential in order to create thick passivating film. https://en.wikipedia.org/wiki/Reduction_potential. Such film will increase corrosion resistance and reliability of corrosion protection.
adv.
We have developed such passivating solution for 300-steel for food and medical industry. We also have passivating solution for 400-steel which deploys both functions removing of free iron and passivating film formation.
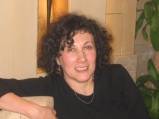
Anna Berkovich
Russamer Lab

Pittsburgh, Pennsylvania
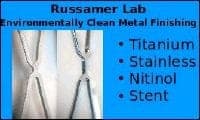
2007
Q. I have been following this thread with quite a bit of interest. As we have been having the perennial problems with 416 and 440C on a very intermittent basis we were advised that citric acid may well be the way to go as the potential for attack was greatly reduced (correct me if I'm wrong).
My problem is that when I read such polar views I am disinclined to investigate too much further.
So, in general, are we for or against passivation with citric acid ? Please give me something to go on instead of the "it works/no it doesn't" arguments.
Looking forward to seeing some reasoned arguments, preferably backed up with some more literature sources.
Aerospace - Yeovil, Somerset, UK
2007
A. From my experience, Anna has presented the most accurate information. Let me just share some personal experience from a non-biased perspective. citric acid indeed behaves differently than nitric acid in the way that it helps achieve passivation. The comparison of the resulting passivation layer thicknesses is key here. The thickness of the layer helps determine corrosion resistance. The one thing that many are overlooking is the application you are using the SS for. For many applications Citric is sufficient and the difference is negligible. However, I have first-hand experience using both citric and nitric for metal injection molded (MIM) parts, as well as some other medical device applications and nitric sometimes out-performs citric. This is especially important if cosmetic finish is a factor. It also depends on how smooth your surface is pre-passivation.
Dwayne Bell- San Jose, California, USA
2007
2007
A. Anna,
The current understanding of passivation here at Stellar Solutions is that iron removal takes place in the bath and oxidation of the non-ferrous metals takes place in the air, and that this is what happens in both the citric and nitric processes. I realize this view is not shared by many old-schoolers.
Stainless steel is etched by nitric acid given enough time, as I'm sure you are all aware. I.e., all the metals present in the alloy including chromium are potentially removed. This is mutually exclusive with the idea that a passive chrome oxide layer is formed in the nitric acid bath.
Testing data we have indicates a BETTER chrome oxide layer with citric passivation, not a thinner one. Citric does a better job of forming a chromium enriched surface because, unlike nitric, it only removes the iron. For this reason, the benefits of a citric passivation would be negated by following it with a nitric bath as you suggest. However, it is true that a post-passivation bath of oxidizer (peroxide, etc.) is likely beneficial, or at least faster than mere air exposure.
Brian:
416 and 440C are difficult to passivate, even with citric, but we have seen many successes in dealing with them. Citric Passivation is accepted by both the ASTM and ASM passivation standards.
adv.
Let us know if we can help you.
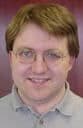
Ray Kremer
Stellar Solutions, Inc.

McHenry, Illinois
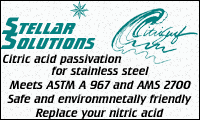
A. We understand why you are not satisfied with the present state of passivation theory. Numerous opinions are caused by differences in theoretical explanations, and mostly by different real conditions of applications. For example:
1. Stainless steel parts have relatively clean surface with no free iron, no areas depleted by chrome, no signs of rust;
2. SS parts have iron on it surface left from previous mechanical treatment, there are visible signs of rust, areas depleted by chrome.
In the first case treatment in citric acid will not enhance passivation quality, moreover it will significantly decrease corrosion resistance, decrease potential of dissolving in corrosion environment ( the only output of such treatment will be decreasing of the thickness of the passivating film and decreasing of Chrome and Fe (III) in such passivating layer).
In the second case it is opposite -citric acid will remove iron from the surface, remove areas depleted in chrome, remove rust. Thin uniform passivating film will be formatted on cleaned surface. Corrosion potential will be similar as in case 1, but significantly higher than if no citric treatment is conducted (since without treatment metal part will behave as steel, not as stainless steel).
That is why there are various opinions on citric acid passivation. Russamer Lab Group opinion: in each particular case decision on which passivation method to use should be based on corrosion tests before and after passivation (for example test in Copper sulphate, or test on potential reduction).
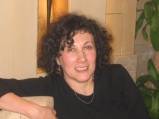
Anna Berkovich
Russamer Lab

Pittsburgh, Pennsylvania
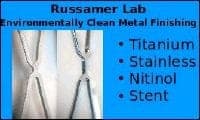
2007
"It doesn't matter how beautiful your theory is, it doesn't matter how smart you are. If it doesn't agree with experiment, it's wrong."
- Richard Feynman
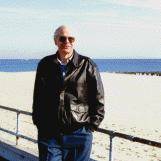
Ted Mooney, P.E.
Striving to live Aloha
finishing.com - Pine Beach, New Jersey
A. All of us are tired of the back and forth opinions of citric vs nitric passivation.
The simple fact is that dozens of independent laboratories, universities and Fortune 500 companies have run exhaustive studies on this and, in all cases that we know of, these have proven that citric acid when formulated properly will out-perform nitric acid in almost every situation.
We would be happy to post in a public forum those studies which we are permitted to divulge. Anyone desiring to contact the universities, testing agencies or companies can do so.
We can also supply public data directly to interested parties.
Regardless of which opinion one is of, the metallurgical mechanism (lots of opinions worldwide) the fact is that citric formulations DO yield not only a higher chrome oxide to iron oxide ratio, but also a THICKER oxide layer when the proper process is used.
All of this is verified by the thousands of companies around the world who have tested and are using these formulations. We can all debate the theory-- that is good and educational for all of us. But the test data showing improvements in corrosion resistance are in the end the only thing that really matters, because that is WHY we passivate.
None of us would ever say that nitric acid does not work, because it has been the workhorse for many years. But there is even independent university data indicating that nitric acid is harmful to the surface. So you can find data to prove probably whatever you want to prove.
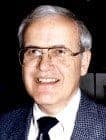

Lee Kremer
Stellar Solutions, Inc.

McHenry, Illinois
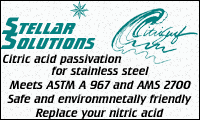
2007
2007
A. Ted,
sorry to come in late in this interesting debate though I am a regular in our "electroplating and forming" section.
I am of opinion that Ray and Lee Kremer are talking about the latest in citric passivations and Anna is referring about her initial studies in the lab. Debatably I would go with the Kremers as it seems they are ahead in their studies.
As we all know, Stainless steel is comprised of a mixture of materials, primarily iron, chromium, nickel (in some cases molybdenum and manganese) along with other materials in small ratios. Nitric or citric formulated passivation solutions cause the formation of an effective outer protective layer consists of only oxides of chromium, iron or nickel, in different ratios which are highly resistant to corrosion. Though both Nitric and citric removes free iron from the surface it is very important to to apply good surface cleaning technique to remove the entire free iron from the surface to allow formation of good passive layer.
Nitric method tends to "re-deposit" contaminant iron back on the surface and some times it leaves behind a reddish-yellow rusty look. it is considered rust. If the dip time is extended for any reason,there is a chance of acid attack on the surface used in surgical/electrical usage.
One thing I want to make clear is that I am not in the pay roll of the Kremer's but I am confident that they have mastered the citric technology, may be by formulating an additive that immobilizes removed metal ions which will not redeposit back on the surface as in the case with nitric solution.
Nitric passivation was developed at a time when the chemistry of passivation was little understood.With current technologies available for the study of the surface chemistry of stainless steel, I think we should be ready to listen and try out Kremer's finding of "higher chrome oxide to iron oxide ratio,and a THICKER oxide layer" when using citric passivation solutions.
May be that is the reason that the beer now- a days tastes better as I presume these industries have already stated citric solutions (which restricts re-deposit) to passivate beer containers in place of nitric passivation solutions!
Regards,
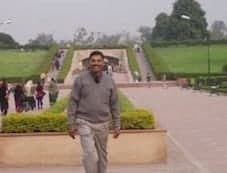
T.K. Mohan
plating process supplier - Mumbai, India
You know, I'm liking TK's comment about using beer tasting as a means of testing passivation effectiveness. There's got to be some way we can work that into ASTM A967 or AMS2700 instead of those boring humidity or copper sulphate ⇦ on eBay or Amazon [affil links] tests...

Lee Gearhart
metallurgist - E. Aurora, New York
2007
A. Beer taste is one of the original passivation tests! It was the work by Coors in Germany decades ago that originally identified citric acid as an alternative passivation chemical.
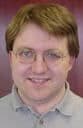
Ray Kremer
Stellar Solutions, Inc.

McHenry, Illinois
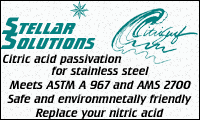
2007
Q. I was interested to read T.K Mohan's following comment "Nitric method tends to "re-deposit" contaminant iron back on the surface and some times it leaves behind a reddish-yellow rusty look". We have sometimes observed it. Is there a solution to it?
Jari Hyvarinen- Sydney, Australia
April 9, 2008
June 14, 2009
A. Hi,
I'm just a newbie here.
Something I learned a long time ago: There is always a better way. Don't close your eyes on the future. Citrisurf makes perfect sense. Someone approved it so it must be an effective replacement. I bought some to use on prints calling out the ASTM standard.
However, when my major customer found out I was going to use orange juice on their parts all of a sudden all the ASTM points were changed to AMSQQP35
[canceled] spec. This company obviously don't believe in the times are a changing.
tyvm
Hope I have a chance to put my 2 cents in again.
Bob
dry lube and passivate shop - Nevada, USA
Q. How important is it to prevent evaporation to dryness of the citric acid solution on 304SS, prior to washing it off, and subsequent peroxide passivation? I have sometimes observed a "sticky" residue if the citric solution dries on the SS surface prematurely. The deposit appears to be removed with warm water washing.
I guess my question is, "What is downside of intermittent evaporation of the citric acid on the 304 SS surface if subsequent water wash appears to remove the "sticky film" prior to peroxide passivation?
Jack
- Richmond, Virginia, USA
December 28, 2010
A. Jack,
Yes, is it important with passivation to have a complete rinsing of the surface. This ensures full access of the surface to oxygen in the air which creates the chrome oxide layer.
Does it hurt anything if you let some citric solution dry on there as long as you rinse it off later on? Probably not. You're certainly a lot safer with residual citric than you are with residual nitric acid, which can cause bad localized etching and pitting.
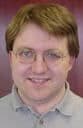
Ray Kremer
Stellar Solutions, Inc.

McHenry, Illinois
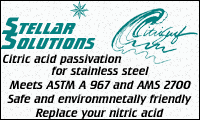
February 14, 2011
![]() |
This is a highly technical discussion. It seems that for the purpose that I intended to use a tested-n-tried solution that remove rust from stainless steel safely, I will stick with what I have been using safely and successfully, Barkeepers Friend ⇦ on eBay or Amazon [affil links] in powder. Monty Betancour- Coconut Creek, Florida April 30, 2011 May 2, 2011 Thanks, Monty. You are right that this discussion has been about how manufacturers should process their materials to reduce or eliminate the likelihood of their stainless steel rusting; it is not about what a consumer should do when they encounter a rusty stainless steel surface. Readers in a similar suggestion will probably appreciate your advice! Regards, ![]() Ted Mooney, P.E. Striving to live Aloha finishing.com - Pine Beach, New Jersey |
Q. We operate a set of chemical tankers and have recently carried out passivation onboard one of our ships using citric acid Solution.
Can this be disposed out at sea after suitably diluting it to around ph 6.5.
Is there any regulation prohibiting discharge in open seas?
Is the product harmful to marine life in any way?
thanks for your quick response.
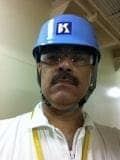
Gurcharan Sachdeva
shipping - Singapore
September 19, 2012
A. Gurcharan,
citric acid is most certainly safe for marine disposal and not harmful to wildlife. As for the regulations, we've been trying to figure that out lately. There seem to be a lot of regulations from several different organizations and it's difficult to figure out which takes precedence.
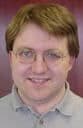
Ray Kremer
Stellar Solutions, Inc.

McHenry, Illinois
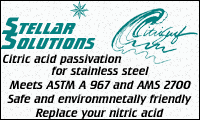
RFQ: G'day
I would like to give some Stellar Solutions or equivalent a test. I make products out of 304 and 316 stainless. It sounds like I will still have to use another method to remove weld scale but I want to be able to safely and effectively submerse my parts to remove possible steel contamination. I currently use hydrofluoric paste on weld scale but I would need far too much to submerse whole parts. Can you get citric acid for this purpose in Australia?
Any Advice would be great
Regards
owner operator - Charters Towers, QLD, Australia
March 12, 2013
Ed. note: This RFQ is outdated, but technical replies are welcome, and readers are encouraged to post their own RFQs. But no public commercial suggestions please ( huh? why?).
A. adv.
Timothy,
please contact us directly regarding distributors of our products in your area of the world. Our contact information is available in the supplier directory here on finishing.com, or we are easy to find with your favorite internet search engine.
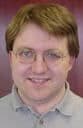
Ray Kremer
Stellar Solutions, Inc.

McHenry, Illinois
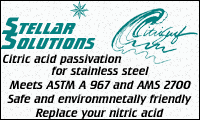
March 13, 2013
Q. We recently switched our stainless steel passivate solution from nitric to citric. The citric solution grows an algae or bacteria, which we have to keep filtering out. Is there any way of preventing the growth, that doesn't affect the solution?
Dave Foot- Weymouth, Dorset, UK
May 20, 2013
May 30, 2013
A. Dave,
A small amount of hydrogen peroxide should be ok. I know some folks passivate with citric and kill bacteria with hydrogen peroxide. I would think 1/2% of a 35% solution would be more than enough. This however will have to be trial and error like all metal finishing applications. You may want to do a beaker test to verify and you could get some at the drugstore, but note that it's already diluted for the most part. Also note that hydrogen peroxide doesn't stay around. If it works, you might only need to do a visual to see the need for more H2O2.
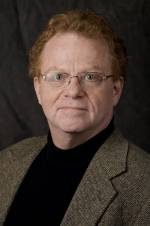
Bob Adams CEF
Tijuana, Mexico
A. Hello Bob
Exactly my thoughts, Right now I investigate this substitution, and the only reason I can find not to do this substitution, is that the NO released from the nitric acid is known to kill bacteria.
This effect should be possible to obtain by say 1% hydrogen peroxide in mild sulfuric acid, as a byproduct you ensure that nickel/chrome is oxidized.
Any reason this might not work?
- Aalborg, Denmark
June 5, 2013
June 10, 2013
A. That's not a bad idea Bob, and peroxide can be helpful for passivation as well.
A commercially available biocide should also be fine to prevent growth in your bath. Citric is an organic molecule, so this can happen. However I've also noticed that it seems to happen mostly when the bath sits stagnant. If the bath is in daily use or agitated daily, it may also help prevent growth.
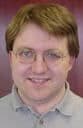
Ray Kremer
Stellar Solutions, Inc.

McHenry, Illinois
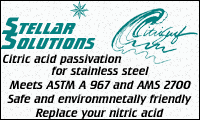
Sorry for the slow reply, but I've been away. Thanks to all for your input, very helpful. I've been asked to enquire about the best method to check the strength of the citric acid in the bath.
Thanks
- Weymouth, Dorset, UK
June 28, 2013
July 30, 2013
A. Dave,
The traditional methods are usually best. For a straight citric acid bath you can track the pH. If the citric is pH buffered at all, monitoring that way won't work, so instead something like specific gravity, conductivity, or refractive index. Most of these presume you filter the bath to keep it clean of other materials.
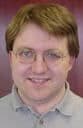
Ray Kremer
Stellar Solutions, Inc.

McHenry, Illinois
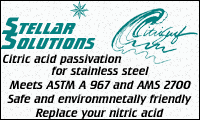
citric acid passivation of an assembly of two different types of stainless steel
Q. Can you citric passivate an assembly that consists of 17-4SS and 304SS parts? I thought that different materials would react off of each other -- or is that with the Nitric only?
dawn hoke- dayton, ohio
August 13, 2014
August 25, 2014
Dawn,
In theory, any pair of dissimilar metals or alloys that are touching each other while immersed in water or acid can undergo a galvanic reaction. However, I've never heard of this actually being a problem for multiple grades of stainless during passivation. I suspect that different grades of stainless are similar enough to each other that the effect is negligible. Always run some trials before going into production, but if things look okay you should be fine.
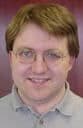
Ray Kremer
Stellar Solutions, Inc.

McHenry, Illinois
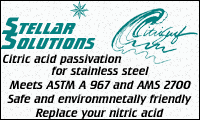
Q. When using a hand applied passivation of citric acid , I have not seen any mention of rinsing, thus risking mineral deposits from the water.
Please advise.
Tool & Engineering - Romeoville, Illinois USA
August 13, 2014
A. Hi Karen. Demineralized water can be purchased if only a small quantity is needed, or easily and cheaply made on site ("Call your Culligan man") ... perhaps I don't quite understand the question?
Regards,
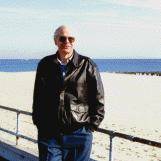
Ted Mooney, P.E.
Striving to live Aloha
finishing.com - Pine Beach, New Jersey
August 2014
Q. So after the hand application of citric acid is applied, I am guessing it needs to be rinsed? My engineer is stating the product he is using in a hand application for passivation is some type of paste consistency. He states if he rinses it off, iron may be left on the surface since our water is hard and has a lot of iron in it.
I want to know if there is a product (citric acid is nothing more than fruit juice) that does not have to be rinsed and the part still be passivated?
Karen
- Wesley Chapel, Illinois USA
August 13, 2014
A. Karen,
All passivation, be it parts dipped in a bath, a spray-on product, or a gel, must be rinsed clean with water afterwards. All that the acid (nitric or citric) does is remove iron from the surface. The passivation process is not complete until the chromium in that iron-depleted surface is exposed to air to enable chromium oxide to form. I am sure that the manufacturer's directions for the passivation product you are using must state that rinsing is required.
You are correct in saying that water with unusually high levels of iron can leave some of that iron on the surface, which can lead to minor surface rusting later on. The surface is only as clean as the water used to rinse it. If the only water available to you is high enough in iron to be a problem, you should do as Ted suggested and invest in a water filtration system or bring in clean water from elsewhere.
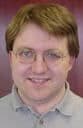
Ray Kremer
Stellar Solutions, Inc.

McHenry, Illinois
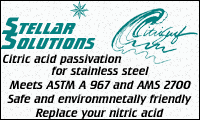
August 25, 2014
Can I passivate stainless steel with orange juice?
Q. So what's the difference between citric acid and using orange juice to passivate 316SS for my sailboat chainplates (one time, not in production)? I am going to polish the production finish for looks on the exposed portion of the chainplate. Thanks
Thomas Erk- Oakland, California USA
September 3, 2014
A. Because orange juice is a complex mixture that contains many things besides citric acid. citric acid is cheap - why reinvent the wheel?
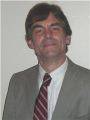
Dave Wichern
Consultant - The Bronx, New York
September 10, 2014
A. Thomas,
Freshly squeezed or something from the grocery store? Just kidding :-)
Ready-to-use citric acid based passivation products are readily available in small quantities. Save the orange juice for drinking. :)
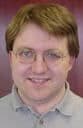
Ray Kremer
Stellar Solutions, Inc.

McHenry, Illinois
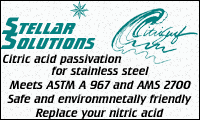
September 19, 2014
Q. The A967 has a table to describe the nitric acid passivation treatments for different grades of stainless steel. Does anyone has any smilar table with recommended citric acid passivation treatments (per ASTM967) for different grades of stainless steel?
Carlos Lopez- Caguas, Puerto Rico
October 16, 2014
A. citric acid passivation is allowed by ASTM 380 and ASTM 967.
You can get a copy here:
https://www.astm.org/Standards/A967.htm
However, note the parts must pass the relevant testing.
Some say citric passivation is marginal to pass, others disagree.
Your money, your choice.
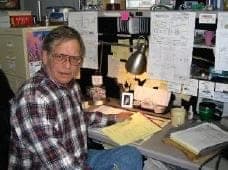
Jeffrey Holmes, CEF
Spartanburg, South Carolina
October 17, 2014
A. Carlos,
The chart is important for the nitric baths because there are several distinct nitric formulations listed in the standards. However, on the citric side there is only one formulation given. You'll note the various options on the citric side relate only to time vs. temperature choices. If A967 had a grade per bath type table for citric, every column in every row would be checked, so there's really no point to it.
However, if you are using a commercially available citric acid passivation blend, the manufacturer may have such a table to choose between the different variations of their product.
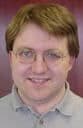
Ray Kremer
Stellar Solutions, Inc.

McHenry, Illinois
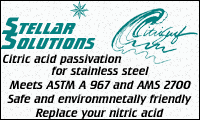
November 10, 2014
December 19, 2014
Q. Can Alloy 88 be passivated along with 316SS in a food grade piping and equipment system? Thanks.
Here is its makeup:
Alloy 88 corrosion resistance is equal to AISI 300 series Stainless Steel and has the following chemical composition by percent:
(Nickel Balance)
Tin 3-5, Manganese < 1.5, Phosphorous < .03
Chromium 11-14, Molybdenum 2-3.5, Silicon < .5 Sulfur < .03
Bismuth 3-5, Iron < 2.0, Carbon < .05
- Howes Cave, New York USA
January 6, 2015
A. Jeremy,
Should be fine, but you may want to run a bench test first to make sure the 88 won't have any etching from the process you are planning.
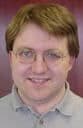
Ray Kremer
Stellar Solutions, Inc.

McHenry, Illinois
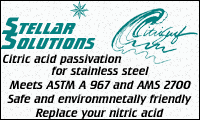
Q. How is the bath life of a citric passivation bath determined -- what criteria is used to determine the activity of the bath? We have noticed very little chemical additions in a 5-week period based on holding concentration levels; however, I find it hard to believe that no additions of "fresh" chemical is needed. Please help! Thanks.
Gary Raihl- Wernersville, Pennsylvania
March 13, 2015
Q. I'd like to piggy back my own questions on to this post. We use citric acid recirculation for the cleaning/passivation of 316/316L SST. Are there any guidelines for the reuse of the weak acid cleaning vs that of a strong acid such as nitric acid? Are there any chemical methods to essentially "clean" the recirculation solution for reuse?
Shawn Way, PE- Stafford, Texas USA
March 13, 2015
A. Gary & Shawn,
If you are purchasing a citric acid based product, the manufacturer should be able to provide you with a bath maintenance procedure with recommendations on this, no doubt based on a few common-sense things that I shall describe here.
Running a filter on the tank will help keep the bath clean in general.
As for the acid concentration, you can check it the same way you do any other acid, typically pH or titration. To be compliant with industry standards you are looking for a range of 4-10 wt% acid.
The key exception to this is if the acid has been buffered to an elevated pH, in which case the easy relationship between the acidity of the solution and the wt% of citric present is severed. In which case alternative measuring methods such as specific gravity are often employed.
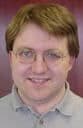
Ray Kremer
Stellar Solutions, Inc.

McHenry, Illinois
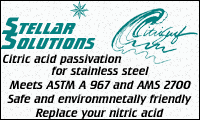
March 16, 2015
Q. Thank you very much. We are using a citric acid solution with an ammoniated EDTA complex, so I think we're going to need to come up with something along the lines of the specific gravity.
Shawn Way, PE [returning]- Stafford, Texas USA
March 17, 2015
March 26, 2015
A. Shawn,
For 316 I doubt that's necessary. EDTA as a complexing agent is redundant to the citric acid itself, and 316 holds up fine in a low-pH citric bath so the ammonia
⇦ on
eBay or
Amazon [affil links] isn't needed either. But yes, if that's what you are being required to use, then monitor with specific gravity.
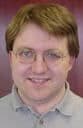
Ray Kremer
Stellar Solutions, Inc.

McHenry, Illinois
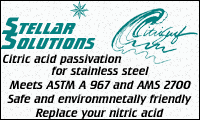
1 2
Q, A, or Comment on THIS thread -or- Start a NEW Thread