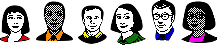
Metal finishing Q&As since 1989
-----
Discolorations on Inconel 718 -- Vacuum Furnace Discoloration?
Q. We vacuum braze and vacuum heat treat high temperature nickel based alloys. We perform frequent burnouts and perform weekly leak rates. We monitor argon quench gas for low dew points. Despite all our efforts to maintain sound vacuum systems, Inconel [Inco] 718 will frequently come out of heat treatments with blue to purple discoloration. Everyone outside of the furnace department swears we have a furnace problem but we know better. We have no ammunition to defend our position other than to show the heat treat cycle parameters and the furnace calibrations are within specification. Why is this material so susceptible to oxidation and what can we do to minimize the discoloration?
Jim T [last name deleted for privacy by Editor]aerospace repair engineer - Indianapolis, Indiana, USA
2004
A. Try to do the following:
1) Check whether parts are clean prior to loading into furnace. A clean white rag soaked with acetone
[on
eBay or
Amazon] can be used for a solvent wipe test on the parts. Any indication of discoloration due presence of contaminants / black smut / oily layer require cleaning parts.
2) You can run one test piece of Inco 718 wrapped in 321 stainless steel foil. Leave a few holes so that vacuum can escape from the bag. Check whether you get good results.
3) Your vacuum furnace bake out cycle, TUS, SAT and calibration might be good. What about Leak Rate Test at Elevated Temperature, say at 1000 °F? Make sure your leak rate is no more than 15 mTorr/Hr.
aerospace - Winnipeg, Manitoba
2004
A. The clean part is a must. Next, when is the last time you did a prescribed "oven burnout"?
James Watts- Navarre, Florida
2004
2007
Q. We have heat treated Inconel [Inco] 718 tubing; three sets of tubing from three sources, all heat treated together. Upon return, one set of tubing is dark bluish to maroonish in color while the balance remain gray.
The tubes were formed and EBW [Electron Beam Welded] prior to heat treating and ultrasonically cleaned in a vapor degreaser using AK225 prior to being sent out for heat treat. All tubes looked similar in color prior to going out for heat treat.
Any assistance in determining the source of the color differences would be greatly appreciated.
Mfg. engineer - Redmond, Washington
A. Insufficient info. Some possibilities:
1) Pre-existing oxide affected subsequent oxidation during heat treatment.
2) Local differences in heat treat furnace atmosphere. The tubing nearest the oxygen leakage 'gettered' it from the atmosphere, turning dark blue while protecting the remaining tubes.
What was the initial condition of the purchased material, maybe solution annealed + water quenched? Perhaps some was also pickled + skin rolled.
What was the heat treatment after welding, maybe aging 8 hr at 1325 °F in ? atmospheres?
- Goleta, California

Rest in peace, Ken. Thank you for your hard work which the finishing world, and we at finishing.com, continue to benefit from.
2007
Q. The .063" diameter tubing was purchased per the AMS5589 rev. D (Nickel Alloy, Corrosion and Heat Resistant, Seamless Tubing).
The specification calls for a solution heat treatment. Pickling, bright annealing, etc., are allowed, for surface finish effects.
Our receiving records only have the chemical composition of the material and that they were annealed the standard stated above. We do not know what other variants within the spec may have been applied to the tubing.
The tubes that were heat treated concurrently, were located within the same fixture, only a couple of inches apart.
- Redmond, Washington, USA
2007
A. I don't have AMS5589 but note its title includes '1775 °F (968 °C) Solution Heat Treated.' Also, SAE shows that revision E (July 2007) eliminates the requirement for passivation after polishing. Does AMS5589 D require polishing?
The proximity of the tubes within the furnace indicates a difference in material. The discoloration is almost certainly oxidation. The amount of oxidation depends upon the initial surface. Any residual high-temperature oxide [possibly (Ni,Fe)Cr2O4] will be less protective than an oxide (mostly Cr2O3) formed on a polished surface while aging at 1325 °F, and a polished + nitric acid passivated surface (enriched-Cr2O3) will be more protective.
It is possible to make some judgement regarding the presence and thickness of an oxide film using a passivation tester (basically, a VOM with a flat probe); see threads 11772 "Testing for Passivation" and 33579 "Are passivation test kits gimmicks?".
If necessary to remove high temperature oxide, formulas for pickling Inconel alloys are given in 'Fabricating' available from Special Metals Corporation: www.specialmetals.com
Is your post-fabrication heat treatment merely the age-hardening (e.g., 8 hrs at 1325°F + 10 hours at 1150°F, often conducted in air) or the entire heat treatment [solutionizing (in protective atmosphere?), air cooling and aging]?
A brief article 'Heat Treating of Nickel and Nickel Alloys' is available at http://www.key-to-metals.com/Article32.htm
- Goleta, California

Rest in peace, Ken. Thank you for your hard work which the finishing world, and we at finishing.com, continue to benefit from.
2007
A. Some contaminants in a vacuum furnace come from sublimation of metals which coalesce onto the first cooler area of the furnace they meet which is usually a few layers into the hot face insulation or quench nozzles. Some of these metallics can be easily oxidized by water vapor even at room temperature. When the cycle is run the oxide is at a low enough temperature to be stable, but when the backfill and quench cycle occurs the heat is driven into the area where the oxide resides and some materials (such as manganese) will give up their oxygen and revert back too a lesser oxide or pure ... this free oxygen is then absorbed by the nearest getter which is usually the part.
A good way to test for this is to run samples with a preheat to around 1400 - 1500 °F for an hour - forced cool and then pump down without opening furnace, then proceed with your standard cycle.. This extra step forces any contaminant to release any retained oxygen which is then pumped out leaving a cleaner system for the actual process.
The only cure to this is a very, very intrusive rebuild of the hot zone ... all parts must be grit blasted clean or replaced and the vessel thoroughly cleaned, then a maximum temperature burnout after rebuild. You must also determine where the contaminant came from and either eliminate it from the run list or run with a partial pressure of at least 800 - 1000 mics (.8 - 1.0 T)
Good Luck
Vacuum Furnace Troubleshooting and Repair - Vernon, Connecticut, United States
May 27, 2013
Q. I have an Inconel 718 aircraft engine rotating part that is turning dark purple/blue following the vacuum age process. Other than it being a cosmetic issue, is there any reason I should be concerned about this discoloration?
Alan Yost- Havelock, North Carolina USA
October 25, 2017
Discoloring of Rene 125 during vacuum heat treatment
November 30, 2017Rene 125 is a nickel based superalloy for turbine blades
Q. What can be reason for black surface of the part made from Rene 125 if heat department saying that vacuum process and furnace is OK? Parts are ultrasonic cleaned.
Bedrich Dolezalproduct designer - Prague, Czech Republic
Q. Jim, did you ever find out the exact cause of the discoloration? I have a similar case and know it is not the furnace.
Rich Grossman- Massachusetts, USA
March 11, 2019
Hi Rich. Jim's posting was from 2004; we are unable to reach him to alert him 15 years later, and I doubt that he checks in frequently if at all. But if your problem is the same as his, the answers offered to him should have validity. Can you try those suggestions and/or comment on them? Thanks!
Regards,
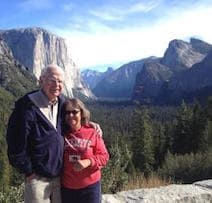
Ted Mooney, P.E. RET
Striving to live Aloha
finishing.com - Pine Beach, New Jersey
March 2019
May 31, 2020
A. The likely culprit here is aluminum and titanium oxides. Even with good pre-cleaning, a clean furnace, and low leak rate on the furnace, these oxides can still form in a vacuum atmosphere if additional measures are not taken to prevent it; especially with the long age cycle.
See metal-metal oxide equilibrium curve for TiO and AlO here:
https://vacaero.com/information-resources/vacuum-brazing-with-dan-kay/168697-reducing-metal-oxides-in-brazing.html
the partial pressure of water on the vertical axis on the right of graph closely approximates vacuum pressure (if standard pump down is used); for each oxide curve shown, reduction of that oxide begins to the right of the curve.
Measures that can be taken to prevent this are:
1) Pump furnace down, purge with inert gas, then pump back down (so remaining atmosphere in furnace is largely inert)
2) use a "getter" material in the furnace to scavenge unwanted contaminants (stainless steel/titanium foil enclosures around parts with no line of sight to heating elements work well though there are many approaches)
- Orange County, California
Q, A, or Comment on THIS thread -or- Start a NEW Thread