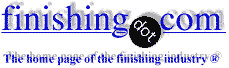
-----
Cold Rust Bluing Methods
A. A couple things here: there are perfectly adequate prepared solutions available from gunsmith suppliers, which are safe, sure, and very economical to use -- so unless you enjoy playing the chemist and have the safety backups and experience, it's not necessary to do the risky and hazardous mixing yourself. If you understand and prepare for safety, with protections in place, hey have at it.
Secondly, it is well known that a well done rust blue is by far the most durable traditional finish for firearms; hot salt bluing, while beautiful in its own right, uses more hazardous substances, has by-products which must be dealt with and gotten rid of, and is far more needful of equipment. And it is nowhere near as durable as rust blue. If you are smart you will substitute steam in place of boiling water to blacken. Done properly you can be up to steam in 15-20 min using 110V household current (U.S.A.) -- no need for distilled water as the steam is obviously distilled. There may a bit of adjustment in costs for a commercial setup, but for me rust blueing has proved considerably cheaper and easier using steam on my small scale hobby.
Hobbyist gunsmith - Huguenot, New York
August 20, 2022
⇩ Related postings, oldest first ⇩
Q. I'M BRIAN AND I AM STARTING A SMALL BUSINESS SPECIALIZING IN THE REFINISHING OF ANTIQUE AND CLASSIC FIREARMS MOST OF WHICH WERE FINISHED USING A COLD RUST BLUING PROCESS.
THE ACID BASED SOLUTION WAS APPLIED TO THE SURFACE ALLOWED TO RUST UNTIL RED IMMERSED IN BOILING WATER THEN WIRE BRUSHED TO PRODUCE A BLUE BLACK FINNISH. THIS FINNISH IS VERY DURABLE AND CAN NOT BE DUPLICATED BY COMMERCIAL COLD INSTANT BLUE PRODUCTS CURRENTLY AVAILABLE IN GUN SHOPS.
DOES ANYONE KNOW FORMULAS FOR THESE EARLY RUST BLUING SOLUTIONS AS WELL AS INFO ON HOW TO USE THEM
BRIAN LOAGUE- OKLAHOMA CITY, OKLAHOMA
2000
A. I am the gunsmith for a company in my hometown and black approximately 60 to 80 sets of barrels and/or rifles annually. I use the following formula, 600 cc's pure nitric acid [affil link to item on Amazon [affil link] , 400 cc's Hydrochloric acid [muriatic acid ⇦ on eBay or Amazon [affil link] ], mix in a suitable container and to this add as many clean degreased iron horse shoe nails as the acid will digest and, when the mix stops fuming and working, dilute using 5 liters of distilled or deionized water and allow to settle for a few days. Decant this liquor into brown chemical bottles making sure that none of the sludge is carried into the bottles. The process as usual of good polishing and scrupulous degreasing must then be carried out on the material to be blacked using either modern chemicals or the old fashioned washing soda ⇦ on eBay or Amazon [affil link] that I use, no hand or skin contact must be allowed after this point. After the degreasing, flush or scrub the metal in very hot water to remove any residual chemicals and allow to cool thoroughly before applying the fist coat of solution with a clean swab, do not swamp it, merely moisten.
After 24 hours in a warm moist atmosphere, boil to fix the coat of rust that has appeared; when cool card off the black loose oxide that will then be visible. I use a very fine wire wheel made by company called Canning from Birmingham, England. This brushing is essential to the final high polished finish required for guns such as the Purdey's Holland and Hollands, etc. which I regularly work on. You may have to use small steel bristle brushes to reach into awkward areas also fine 00 steel wool ⇦ on eBay or Amazon [affil link] .
After you have reached the finish you require or the metal becomes reluctant to take any more rust, it must be boiled again in a soda solution to stop the rusting, given a final carding, and then run up to a high temperature in clean boiling water, allowed to flash dry and placed in a tank containing a 50/50 mix of old engine oil and dewatering oil overnight, removed and allowed to drain to clear rib breather vents, etc.; I then flash off the barrels or whatever by playing them across the flame of a fairly hot gas torch to clear any residual moisture or oil from the rib spaces and then polish them off with a rough paper towel. For a couple of days or so after finishing, coat the work with a film of good gun oil. I do not protect the bores in any way during this process, but give them a serious cleaning and oiling afterwards. Best of luck if you use this method. Yours
John Gellatly- Perth, Scotland, United Kingdom
2003
Ed. note: Ed. note! Readers: These instructions are for experienced smiths or chemists already very familiar with the hazards of strong acids!
The internet is a giant one-room schoolhouse where you may overhear & read instructions appropriate only for people at a reasonably advanced chemistry level & with haz-mat training, working in a proper industrial facility :-)
A. Further to my original post on slow rust blacking, yes the old oil is used engine oil, new oil does not seem to work as well probably due to some of the modern additives although I have used a sample from the same can after an oil change, perfect. The finish, blue, black or somewhere in between depends I think on the quality of the steel and the level of chrome therein. The use of reagent chemistry is a good idea and the use of any of the rust producing sublimates is very sensible when you cannot be sure of the iron content of the horse nails if you use them. Rusting times differ according to where you are in the world and the temperatures and relative humidity levels there, test and test again. The suggestion that silicone content in some modern oils can cause problem with the black taking on is valid and the only way I have found of defeating this is to boil and scrub in a mild caustic soda ⇦liquid caustic soda in bulk on
Amazon [affil link]
solution before coating for the first time with the barrel/s hot and re-coating after maybe 2 hours then follow through the process as usual. The thing we must always have in the back of our minds is that whether it be your weapon or a valued customer's it is someone's pride and joy and we should always err on caution whilst doing our best to achieve the best finish possible.
Yours sincerely and my regards to all our fraternity,
- Perth,Scotland,United Kingdom
October 18, 2009
Q. I'm in the process of learning to rust blue and have done several guns with varying success. Mr John Gallatly's instruction about soaking the parts in old motor oil and a dewatering oil caught my attention and I need to ask if by "old" motor oil, he means used oil?
I'm having trouble getting an even coloring without streaking or blotching especially on the flat surfaces of the receiver. Not getting the parts cleaned well enough? I'm unable to locate washing soda
⇦ on
eBay
or
Amazon [affil link]
locally .
Thanks, Ron
- Roscommon, Michigan
September 9, 2008
Baking soda [in bulk on
eBay
or
Amazon [affil link]
or just real soap for an alkaline water to cook in should do the trick! Modern detergents are neutral; any kind of soda (crystal soda, baking soda, ...) will do the trick; it's just for neutralizing any acidic residues.
The soda mentioned is just the strongest and (bought in big quantities) the cheapest currently on the market, and was used as a detergent for ages.
Soap is alkaline, soda, ashes, ... basically all "the same stuff" as ashes and sodas are used for soap production; soap is the least aggressive.
sr
technician - Austria
November 10, 2021
Multiple threads merged: please forgive chronology errors and repetition 🙂
A. THIS METHOD OF RUST BLUEING IS EASY, AND NOT COMPLICATED AT ALL. POLISH BARREL OR PARTS, AND THEN CLEAN WITH acetone
⇦ on
eBay
or
Amazon
[affil link] Warning! Flammable!
, KEEP HANDS OFF. WHEN DOING BARREL, SWAB A GREASED PATCH DOWN IT AND THEN PLUG BOTH ENDS BY DRIVING IN DOWEL, OR WOOD PLUGS. NOW HANG THE BARREL IN A SMALL CONFINED SPACE, OR MAKE A GARBAGE BAG TENT OVER IT ETC. BUY A JUG OF NITRIC^See ed. note ACID AT YOUR LOCAL PAINT STORE, THE KIND USED TO CLEAN CONCRETE. POUR AN OUNCE IN JAR AND PUT IN WITH PART TO BE BLUED. DO NOT DO THIS IN YOUR SHOP! IN A FEW HOURS THE PARTS, AFTER THE ACID HAS ATTACKED IT, WILL TAKE ON A DULL FINISH. NOW, KEEPING YOUR GREASY MITTS OFF PARTS, HANG LIKE IN GARAGE OR UNDER THE EVES OF SHOP AND LET IT RUST. THIS WILL TAKE 3 OR 4 DAYS HERE IN OREGON, MAYBE LESS ON COAST OR BACK EAST. WHEN THERE IS A GOOD DENSE COAT OF FINE RED RUST ON EVERYTHING, CARD OR BRUSH IT DOWN TO THE BLUE WITH A FAIRLY STIFF MOTOR DRIVEN WIRE WHEEL. THIS BLUE IS REALLY TOUGH, AND ANY AMATEUR CAN DO IT. BUT USE A LITTLE COMMON SENSE WITH THE ACID, AND IF YOU LEAVE A JAR OPEN IN THE SHOP YOU WILL RUST ALL YOUR TOOLs, etc. IF YOU WANT TO BROWN A BARREL JUST 00 steel wool
⇦ on
eBay or
Amazon [affil link] DOWN THE RUST A LITTLE AND OIL.
- MEDFORD, Oregon
2007
Ed. note: We believe that Tom has made a small error in his suggestion, and that he means muriatic acid, not nitric acid. This assumption is based on the fact that it is muriatic acid which is available in paint stores, and which is used to clean concrete, and which is known for the fumes rusting its surroundings. Plus, putting steel into nitric acid is very likely to evolve clouds of yellow NOx-ious choking gasses.
A. Brian, may I add a bit of advice many of the others did not. PLEASE purchase several old Pawn-Shop "clunker" guns or, even better, some scrapped-out pieces of the various types of steel used in firearms. A good selection could be an old "pulled" shot-out Mauser barrel, an old single-barrel shotgun frame, (once case-hardened), maybe a burst repeating shotgun barrel, and, well, you get the picture ... anyway, use these for practice pieces.
I have had a gun shop for 42 years, on and off. I have had some successes, and some failures. However, I am proud to say that I have never had an irreversible failure with "Cold Rust" or "Rust-and-Rub" bluing on a customer's gun. I did have one (an 870 Slug Gun) that I had to end up glass-beading and conventionally bluing, in the early days. It turned out very well, or at least I have been told that. It was mine, and I still have it, and I hunt with it. I keep it as a reminder, as I had other plans for it. About the same thing happened that has occurred with the good Col. from India (see entry below). DO NOT do any real work until you can put out good work on your practice pieces. Blue them, then sandpaper it off (80 Grit). The repolishing will be good practice in keeping the corners square and the round parts round, and the lines straight. Polish to about a 400 grit finish (NOT mirror; just a bit of "cloud" left). Keep the polishing lines straight. Degrease thoroughly. Then, degrease again, and if you still have any doubt, do it again. This cannot be stressed enough. ALL oil and grease must be completely removed from all the nooks, crannies, and metal pores, or the job will be a splotchy mess.
The formula the Scottish Gentleman gave is perfect, except I use "reagent" grade ingredients, distilled water, and I substitute Reagent-Grade iron powder. Add it 'til the mix will not absorb any more. It may take several days. Strain through a paper coffee filter. Repeat the straining process. Use only glass (NO plastic!) containers and funnels, etc. (A good lab supply has the glass funnels. One or two will last forever). That's because horseshoe nails here (I get them from Centeur Forge Blacksmithing Supply) are actually mild steel, and there are trace minerals in them. I use Reagent Grade ingredients as they are very pure and do not introduce any trace materials, which can ruin the job. Same reason for the water, as minerals will affect the outcome in strange ways. The only source will probably be a lab chemical supply house (Google it) in a large city. (The same chemical house will probably have all ingredients). Shipping will be outrageous and obscenely expensive. Pick the closest and be prepared to drive there and pick it up. It'll actually be cheaper, even with gas as it is. Ask the chemical supply house if they can supply glass reagent bottles with a GLASS stopper of a capacity to hold the brew. Buy as many as you can afford. They last forever till dropped.... Use thick rubber gloves ⇦ on eBay or Amazon [affil link] (also avail. from Brownells [ Brownells home page (affil link) ] ) and keep any and all oil far away. Leave the filings out of the mix, and you have a perfect "Browning" solution. Boil all applications when completed in a mild solution of distilled water and soda to "kill" the acid's action.
And, the acid will burn you severely if it gets on you. As another writer said, DO NOT DO THIS ANYWHERE YOU HAVE ANYTHING METAL YOU WANT TO KEEP! It will rust the bejabbers out of all your very expensive tools (and other customer's guns) as well. I have a 10 X 10 pre-fab outbuilding I confine all these operations to. HUGE vent fan, electric heating for winter, I also use a respirator fab'ed out of an old scuba mouthpiece leading through some hose to a location outside (but then, I have lung problems). Anyway, don't breath it; use gloves (degrease them as well EVERY TIME YOU WORK WITH ANY WORKPIECE, and secure eye protection and ventilation. And good luck - it'll be some of the most satisfying gun work you'll ever do!
William WoodWood's Gun Repair - Oxford, Alabama
January 14, 2008
A. MR WILLIAM WOOD YOU HAVE GIVEN A GOOD DETAILED STUDY OF RUST BLUING I BELIEVE THAT THE SOLUTION YOU ARE USING IS THE ONE THAT JOHN GELLATLY HAS DESCRIBED. LOOKING FORWARD TO YOUR REPLY
HAKIMUDDIN F. DAUD- PESHAWAR, PAKISTAN
July 30, 2008
A. To the helpful gentleman that recommended the use of reagent-grade materials, you can obtain these materials from www.carolina.com. How much ferric oxide would be necessary for a mixture using 500 ml of nitric acid?
Thanks,
Dan
- Granville, New York
February 18, 2009
Q. I was trying the cold blueing method on my shot gun and seem to have missed out on some important step in the process, because the parts haven't blued properly and they are still rusty. The process I followed was - First I thoroughly cleaned and polished the metal parts, then I applied a mixture of 1 part Nitric acid 3 parts water. Thereafter I let the metal rust for 4 days. Finally I rinsed the blued parts in boiling water. The result has been disastrous! I would like know to as to how I can undo what I have done or at least blue the metal parts properly once again.I would like to know of a simple remedy that can be done easily at home without any complicated processing.
Lt Col Adeshpal Singh RandhawaIndian Army - Delhi, India
2007
A. Greetings:
You should only let the part rust until there is a fine coating of red rust. Usually in my climate that will occur in 24 hours or less. If you let it go too long, it will pit the metal.
After it rusts, you need to boil the parts in distilled water for 25 to 30 minutes. This will convert the red oxide to black oxide. When you remove them they will look like they are covered in black velvet.
Use de-greased fine 00 steel wool
⇦ on
eBay or
Amazon [affil link] to remove the velvet coating. Underneath you will have a gun metal gray surface. Repeat the above process as required to obtain the blue you want.
After you have the color desired, soak the parts in water displacing oil for 24 hours. After soaking, rub the parts with a paper towel.
Regards:,
- Shawnee, Kansas
Q. I have tried rust bluing using the two-acid / iron filings
[affil link] method for quite some time, but I always get various shades of gray or even a black, but there is no sign of a blue color. I have seen rust blues on older guns and always there is some blue in the color. How do I get that?
thanks, Bill
hobbyist - Chattanooga, Tennessee
February 11, 2009
A. Hi, Bill. I can't tell you for sure what is wrong, but what I can tell you is that you will get a much more blue color on a highly polished substrate than on anything matte. The very same "black oxide" solution which gives a dark black on matte parts gives a jewel blue on mirror polished parts. Try to mirror polish a small item, or part of an item, and see what color it comes out. Good luck.
Regards,
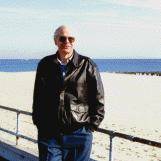
Ted Mooney, P.E.
Striving to live Aloha
(Ted is available for instant or longterm help)
finishing.com - Pine Beach, New Jersey
Q. This is more in connection with my attempts to get a true blue color when rust bluing firearms. I have since read that some of the old rust bluing formulas contained cyanide which have since been discontinued for obvious safety reasons. Also, that these early cyanide formulas, when in contact with iron, resulted in Prussian blue. Does anyone know specifically of any of these formulas and the method of their application?
Thanks,
hobbyist - Chattanooga, Tennessee
A. Hi again.
I am not a gunsmith, but I am from the plating industry where the creation of prussian blue (iron cyanide) is carefully avoided because plating shops are monitored for cyanide, and it is very difficult to destroy the cyanide once it has reacted with iron.
Although there are hazards in working with cyanide, I think it would be reasonably easy to make a prussian blue cyanide solution, since plating shops make it by accident all the time :-)
Regards,
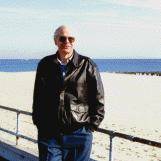
Ted Mooney, P.E.
Striving to live Aloha
(Ted is available for instant or longterm help)
finishing.com - Pine Beach, New Jersey
A. Some advice which I have found to be good.
First go buy a copy of Firearm Blueing and Browning [on
eBay ,
Amazon,
AbeBooks affil links]
by Angier, it explains everything.
Second, don't use any formulas that contain Mercury salts, way too poisonous.
Third, use only distilled water where water is needed.
Fourth, don't touch any part you want a finish on with your skin, no matter how clean you think you are.
Fifth, if modern oils that contain synthetics or silicones have been on the surfaces you will have to clean them more than one time. I have found this out the hard way.
Sixth, the cleaned surfaces must be completely wettable by distilled water, if the last time you rinse the part it is not covered by an absolutely continuous film of water it is not clean yet.
Seventh, don't get greedy, it's better to rust the part only a little and have to put on 6 to 10 treatments than to try to do it in two and wreck your part. After two treatments you may not get rust but rather a very thin dark gray film. Boil it, don't get greedy. It will get black.
Eighth, One of the simplest of formulas in the book works very well, a 2 percent by weight solution in distilled water of Ammonium Chloride. Ammonium Chloride is also known as sal ammoniac
⇦ on
eBay
or
Amazon [affil link]
. It will rust any rustable steel. Don't leave any of it open in your shop, it will cause rust all around, slow but sure.
Nine, there is more art than science to this. I repeat, buy that book and read it.
My best wishes to all who try rust bluing.
- Madison, Wisconsin
September 11, 2009
![]() |
Q. To Bill Dautrich, - Norwich, Norfolk, UK February 6, 2010 A. Hello Trevor: We did in fact correspond years ago about rust bluing. I took a long break from it to earn a living and raise a family. Now that I am retired I thought about getting back to the hobby. As you see, I am still pursuing the elusive blue. I was hoping that with the help of the Internet I could discover the original factory records of DWM and Mauser, but no luck. I am speaking of course of the "new" methods employed by DWM post 1917 and Mauser post 1934. No doubt the color fades over the years and especially when subjected to UV rays. But still it will result in either a light blue or remain a dark blue. The two acid based blues can only give a red rust which always converts to black. There is something more sophisticated in the later formulas of DWM and Mauser in the time frames mentioned above. Good to hear from you again and would enjoy corresponding further. - Chattanooga, Tennessee March 14, 2010 |
I TRIED TOM RICE'S METHOD AND FOLLOWED THE DIRECTIONS TO A T. FINISHED RESULTS PRODUCED A FINISH THAT LOOKS LIKE ANY HIGH QUALITY OR HIGH END BROWNING ON THE MARKET. JUST KEEP IN MIND THAT THE MORE THE STEEL IS POLISHED THE SHINIER THE FINAL FINISH WILL BE. IF YOU WANT A MIRROR FINISH THEN YOU WILL NEED TO DO A GOOD BIT OF POLISHING TO OBTAIN IT. LASTLY KEEP IN MIND THAT EVERYTHING WORTH DOING IS WORTH DOING RIGHT.
HAVE FUN AND ENJOY YOUR WORK.
- EDGEWATER, FLORIDA, USA
March 28, 2010
A. When using reagent grade chemicals or prepared solutions (Brownell's, Pinkington, etc.) 'deionized water' is even better than distilled, though distilled is more available. If there is an analytical laboratory in your area, they are usually willing to supply it (for a price, of course), and many bottled water suppliers are able to, though they may not carry it 'in stock'. If you've ever smelled the 'salt air' near the ocean, you know that salts can also evaporate, especially at distilling temperatures. DI water has had all ionized (dissolved) salts/minerals removed. The 'go slow' advice is also very good. I use steel wool rather than a card or carding wheel, either 'degreased' or soaked in lacquer thinner
⇦ on
eBay
or
Amazon
[affil link] Warning! flammable!
for an hour, then rinsed with spray 'brake cleaner' (non-chlorinated)
⇦ on
eBay
or
Amazon [affil link]
, both quite flammable, but strong degreasers less toxic than acetone.
Salts in the metal (e.g. corrosive priming residual salts) will also make the rust blue 'hard to take', caustic, clean rinse, pickling, clear rinse before final polishing seems to get most of this out (this on a C-96 Mauser with a badly deteriorated bore, the last round of Chinese exports).
If you live in a dry climate, and the parts will fit, hang them from a frame on the upper rack of the oven, set for 150 F, with a pan of water on the lower rack to serve as a poor-man's damp-cabinet, it helps promote even rusting and speeds up that stage of the process.
I've found too fine a polish does not allow the rust blue to penetrate. Even with a 200 grit final polish, the final finish will be close to the equivalent 400 hot-blue finish, as the rust blue builds up and fills the 'scratches' from the polish. It gets more shiny the more cycles you put parts through.
Where possible, wet-or-dry sandpaper (auto supply) or belts work better than polishing compounds, most of which have some organics in the binder that makes post-polish metal cleaning more difficult. Use a water (whet) stone to do the flats on octagonal barrels, it'll preserve the markings and dovetails sharp-edged and the flats flat.
Use of a penetrating, water-displacing oil can't be over-rated (after the soda neutralization and clear rinse). CRC 6-56 is a good stand-by available at NAPA stores everywhere, and is strongly rust-inhibiting. Let it sit on the parts, then apply a heavier (preferably synthetic) oil...I use the old military LSA... and you'll have a finish that'll out-perform hot blue any day.
- Ellensburg, Washington, USA
September 9, 2010
A. Use drinking water that has been treated by the Reverse-Osmosis process. It will be noted on the bottle label.
Had very so-so results and I tried everything from distilled and straight tap water and even spring water from the source until I tried this, and have had excellent results for the past six years (80 + rifles and single barrel pumps, automatic, and even a few bolt action scatterguns and quite a few double barrels sets).
Here at the local big box store RO water is .95 cents per plastic jug. Keep your boiling tub to the needed level. As it boils off, keep it topped up. Use only a tank made of carbon (rusting) steel. NO STAINLESS BOILING TANKS. Something in the stainless (308SS) interferes with the bluing coating.
- Oxford, Alabama
July 21, 2023
Q. With the use of Reagent chemicals, what % strength for the acids would you recommend? My local chem supply has everything I need but the acids come in different strengths. Also for the metal component, ferric oxide red is easily obtainable - do you just add it to the acids until it won't take anymore? Or is their an amount by weight of ferric oxide to a volumetric amount of acids?
Andrew Gibbons- Kendenup, Western Australia
August 15, 2011
Q. Hello to all fellow gunsmiths,
When you boil off your rusted barrels, do you wait for the water to boil and then immerse the barrels or immerse the barrels in the water and then bring to the boil?
Maybe it makes no difference?
I use a solution very similar to John Gellatly's, only I use powdered iron not nails. I have also used staples and steel wool. All with good results. I do not strain and I give it a good shake before use. Again, does any of the above make any difference?
Regards to all,
gunsmith - Florida, Johannesberg, South Africa
March 20, 2012
A. Hey Folks, Here not too long ago I was repairing an antique clock that was badly tarnished. The only thing that seemed to work at getting the green off was Tarn-X tarnish remover ⇦ on eBay or Amazon [affil link] . In the process I got a little on the steel arbors and after rinsing there was a slight film of rust that I removed with 4/0 #0000 steel wool ⇦ on eBay or Amazon [affil link] . When I carried the parts out in the sunlight I noticed that there was a very slight blue tint to those steel parts.
Here recently I've been building a AK-47 from a demilled kit and instead of painting with guncoat I figured I'd try my hand at rust bluing. I read the Scottsman's recipe for Niedner solution and investigated the cost of nitric acid and was blown away by the hazmat fees. I went and got some ⇦ on eBay or Amazon [affil link] and put an old cast iron window weight in the lathe and collected the filings in a clean plastic bowl. I added 'bout a teaspoon of filings to 2 oz of Tarn-X and let' em cook for a couple days then filtered 1 oz of the "soup" back into the remaining Tarn-X.
I took an old piece of barrel and polished it to shiny metal using progressively finer emery cloth until I finished up with 600 grit wet or dry sandpaper. I cleaned the piece of barrel with carb cleaner (mostly acetone anymore, the EPA took all the good stuff out) and applied a thin coating of my Tarn-X soup to the workpiece. Within a few hours it had a thin coating of rust on it and by the next morning a nice thin layer. I boiled some water and the piece turned black within seconds of being immersed, I let it boil for 'bout twenty minutes and removed it and it had that thick black velvet that was described.
I rubbed it off with a paper towel and reapplied my soup. On the second time the rust was lighter and more of a gray haze and after 24 hrs boiled it again. I just did my third boil and wipe and this thing is looking good, black in the shade and deep dark blue in the sunlight. It's still got some thin spots that you've got to look closely to see in direct sunlight but I figure with a few more applications it will look as good as my M91 Carcano. Just thought I'd share.
Jay FortnerRosewood Iron Custom Cycles and Repair - Cedar Key, FloridaUSA
May 23, 2012
⇦ Tip: Readers want to learn from your situation;
so some readers skip abstract questions.
Q. What are the chemicals required and their respective concentration and other temp , pretreatment and post treatment para meters for blueing process and how we can avoid the rusting of it?
Aijazullah Tajir- Al-Ain, UAE
January 6, 2013
Q. I have read a lot on rust blueing, and done a few guns. I have been unable to get a high gloss finish like a English best black. The rusting always seems to cause a satin finish. Does anyone have any suggestions or could post a picture of when to stop rusting? Thanks for the help; good thread.
Justin Oliphant- Neenah, Wisconsin
November 17, 2013
A. You're trying to use a cold rusting process to produce a finish equivalent to the hot black oxide process used by all gun manufacturers. It's not going to happen. You may produce a blue/black finish, but it will never have the durability of hot black oxide.
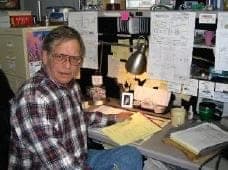
Jeffrey Holmes, CEF
Spartanburg, South Carolina
November 20, 2013
A. Try any recipe for black finish on steel; after that you can use phosphating and then clearcoat it.
You can use black phosphating too (combined with clearcoat).
Modified black oxide process can be used too (there is at least one USA patent on that subject, uspto.gov webpage).
Hope it helps and good luck!
- Cerovski vrh Croatia
November 21, 2013
Q. I just starting brewing the formula of 600 cc's pure Nitric Acid, 400 cc's Hydrochloric acid plus started adding the Reagent-Grade iron powder. I slowly added the powder and wow I was surprised how much yellow smokey fumes came from the bottle --is this quite normal? I did the mix outside in the yard and moved well out of the fumes as they were quite thick.
I have put the bottle in a safe place with a loose lid to expel fumes. I will put more iron in tomorrow. Just wanting to get a feel if I'm going well guys?
sales - auckland city , new zealand
September 10, 2014
A. Hi Brian,
Adding iron to a nitric/hydrochloric mixture has to be done very carefully. The fumes you are seeing are probably nitrogen oxides (nitrogen dioxide is usual).
Professionally this would be done with active extraction to avoid exposure to the fumes, which are toxic and can kill or cause long term illnesses.
The minimum you should be wearing is acid resistant gloves and overalls, safety goggles and, if you do not have an active extraction unit, a face mask fitted with an acid vapour cartridge. Anything less and you are risking your life, even if you are doing it in the yard. Not just that, you may inadvertently expose passers-by, so please be very careful.
Aerospace - Yeovil, Somerset, UK
Thank you for that very important advice. I was looking at the other posts and couldn't identify as much danger as you mention. When the fumes came out I made sure the wind was running away from me; they also dispersed rapidly. What I did wrong was try to tackle a commercial quantity rather than reduce by percentage this mixture to a 10-gun size mixture.
I'm sure it will be less scary and more manageable once I reduce by volume this brew. Cheers for the info.
- auckland, new zealand
A. I second John Gellatly's slow rust bluing formula, i.e., 3 parts nitric acid, 2 parts hydrochloric acid, as much iron as it will dissolve and after cessation of the reaction, dilution with 25 parts distilled water. All amounts volumetric.
I used lab grade 70% nitric acid, lab grade iron filings and hardware store Hydrochloric acid. The safety precautions John G. mentions are not just highly recommended but essential.
The acids/iron reaction is vigorous and your flask should be oversized to minimize boil over. Make small amounts at a time. Add the iron filings a LITTLE AT A TIME. A lot of heat is generated by the reaction. The fumes generated are very toxic and the reaction should be carried out in a safe environment, e.g., fume cupboard. Before adding more iron filings, GENTLE agitation of the flask may initiate further reaction. Wait until there is absolutely no further reaction before adding further iron filings and repeat until addition of iron filings cause no further reaction. When the solution has cooled, dilution with the distilled water can be carried out. After this the solution can be carefully decanted into a dark poisons bottle or filtered. If the solution is left for a fortnight or so any sediment will settle at the bottom of the container when it will be ready for use.
The above is hazardous and should generally be performed in a lab environment by an experienced technician.
- Perth WA Australia
November 16, 2017
Q. How do you use the washing soda
⇦ on
eBay
or
Amazon [affil link]
as a degreaser? I want to try my hand at rust bluing a revolver. Do I boil the frame and slide in a solution of the soda and water or just let it soak? And what about using washing soda and vinegar
⇦in bulk on
eBay
or
Amazon [affil link] ?
Thanks,
Mark
- Ann Arbor, Michigan U.S.A.
November 24, 2018
Q. Hello John Gellatly: I read your post regarding rust bluing formulas. I understand the need for keeping hands off the work and I am assuming it is absolutely necessary to completely clean the work piece after boiling and carding operation.
I came across an article called Mark D's Rust bluing solution and procedures (it is on the web for all to see). He advocates the addition of Sodium Nitrate 20% to the brew which is said to accentuate a deeper blue found in DWM Lugers of the 1917 vintage. I assume that Potassium nitrate may do the same job as I feel it is the nitrate that does the job and it's what I can get. I was also thinking the horseshoe nails being bulky as compared to steel wool for example might slow down the reaction with the acid. I have a 6-acre block and was thinking of conducting the operation in the middle of the paddock I would appreciate your advice.
Yours Faithfully,
- Plainland Queensland Australia
August 4, 2022
Q, A, or Comment on THIS thread -or- Start a NEW Thread