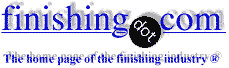
-----
Analysis of metals and acids in Electropolishing Baths for stainless steel
Q. I operate a tightly controlled phosphoric sulfuric stainless steel electropolishing bath. Analysis by titration for sulfuric and phosphoric acid percentages becomes inaccurate as metals content increases. Is there a procedure to provide the true sulfuric and phosphoric acid percentages?
Al Sutton- Canada
1996
A. The presence of hexavalent chromium ion will cause some inaccuracy in titration analysis. In our experience, keeping metal content below 3% via frequent, small decants maintains acid balance, and the inaccuracy of the titration is insignificant. The titration for metal content is usually satisfactory if the bath is not operated as a "full-sludging bath".
Ed BayhaMetal Coating Process Corporation - Charlotte, North Carolina
1996
Q. Given task of setting up an electropolish with 40% sulfuric V/V and 48% phosphoric V/V: Anyone have a simple titration to determine percentage of each acid by %v/v? Would save me a trip to the library and some method development.
Thanks.
Environmental Safety Engineer/Chemist - Phoenix, Arizona, USA
2004
A. After diluting your sample, you can titrate it with NaOH and watch for two end-points: the first, v1 - when both protons of sulfuric acid and the first proton of phosphoric acid have been neutralized (around pH 4.5); and the second, v2 - when the second proton of phosphoric acid has been neutralized (around pH 9.5). You can then calculate the molarity of phosphoric acid from v2 - v1 and the molarity of sulfuric acid from [v1 - (v2 - v1)]/2 = v1 - v2/2 after accounting for proportionality through the known volumes and NaOH concentration.
The end-points are well separated and can best be detected potentiometrically or thermometrically. If you need to rely on indicators (e.g. bromocresol green
⇦ on
eBay &
Amazon [affil links]
for the first end-point and thymolphthalein for the second), you may have to titrate two samples, one for each end-point (unless somebody can think of a combination of indicators that works without mutual interference at these particular pH values).
- Yorktown Heights, New York
2004
Q. Does anyone know of a simple titration for iron concentration in a sulfuric acid/ Phosphoric acid bath for electro polishing operations? I would like to be able to determine the iron level to establish a tank dump schedule.
mukesh guptaChemical engineer - chandigarh, UT, India
2004
A. The iron can be analyzed by AA spectroscopy
⇦ on
eBay
or
Amazon [affil links] . No simple titration exists due to multiple cations: Fe+2, Fe+3, Cr+3, Cr+6, Ni+2.
It is usual to maintain sulfuric and phosphoric acid concentrations, and to estimate total dissolved metals by SG (specific gravity).
- Goleta, California

Rest in peace, Ken. Thank you for your hard work which the finishing world, and we at finishing.com, continue to benefit from.
A. In order to titrate iron in the solution you need to reduce it quantitatively to Fe(2+). A simple way to do that is to pass the sulfuric acid solution through a bismuth column. This is simply a small liquid chromatography column filled with 25-50 (or better, 50-100) mesh high purity Bi particles. I have used a 0.8 or 1.0 cm I.D., 20-25 cm long filled column. My experience has been with dilute (1-2 M) sulfuric acid. I don't think the phosphoric acid would interfere, at least thermodynamically speaking. If you decide to use this method, be sure to keep all the bismuth submerged in acid at all times, to rinse it well with acid before the analysis, to pass the sample solution through it at no more than about 20 ml/min (use a little vacuum in the receiving flask if gravity is not enough), and to rinse the column after the sample into the receiving flask with an amount of dilute sulfuric acid equal to at least 3 times its estimated intergranular empty volume. The solution in the receiving flask is immediately titrated with calibrated KMnO4 solution (watch for stable faint pink).
This technique is similar to the better known Jones (Zn/Hg) and silver reductors, but the column is much easier to prepare (pour Bi particles in; rinse with acid) and to maintain, and selectivity is quite high. I know that Ni, Co, Ti and Sn(4+) do not interfere, and I am sure the same is true of a few additional metals. If Cr is present, a K2Cr2O7 (dichromate) titration may have to be used instead of permanganate because permanganate can oxidize Cr(3+). Unlike permanganate, dichromate requires an end-point indicator or a potentiometric method. For a typical (not necessarily optimal) dichromate procedure see Volumetric Analysis of Metal Finishing Solutions
[on Amazon affil links] by Andrew McFadyen, Finishing Publications Ltd.--, p.
154.
- Yorktown Heights, New York
2004
Q. We currently have an electropolishing bath that is about 5000 gallons in volume. How do we determine the phosphoric and sulfuric acid concentrations and therefore adjust and how critical is the ratio between the two acids relative to productivity?
TY VAN FOSSENmetal finishing - Lake Orion, Michigan
2007
A. The ratio of sulfuric acid to phosphoric acid is not particularly critical, but many electropolishing solutions have other additives in them. I therefore suggest you check the details in the process sheet supplied by your solution's supplier. This will tell you all the analyses you will need to do and what the acceptable ranges will be. Successful electropolishing is dependent on how much metal is dissolved in the solution, its viscosity and operating temperature - detail of these parameters will also be in the process sheet.
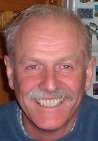
Trevor Crichton
R&D practical scientist
Chesham, Bucks, UK
2007
2007
A. An analytical procedure is in the Metal Finishing Guidebook and Directory; hasn't changed in at least 15 years.
Volumetric Analysis of Metal Finishing Solutions
[on Amazon affil links] by Andrew McFadyen has a very similar procedure under 'Aluminum Electropolishing' (p. 210). Both use colored pH indicators; below is a procedure utilizing a pH meter:
Cool a sample of the well-stirred solution to room temperature.
1. Measure the specific gravity using a narrow-range hydrometer.*
2. Pipette** 2 ml of the solution into a 250 ml beaker [beakers on
eBay
or
Amazon [affil links] and dilute to 100 ml using DI water.
3. Titrate with 1.0N NaOH [1N NaOH on
Amazon [affil links]
to pH = 4.0 and record as 'A' mls.
4. Continue titrating to pH = 8.5 and record the additional mls as 'B.'
H2SO4, wt. % = (A - B) x 2.452/SG
H3PO4, wt. % = B x 4.900/SG
FYI: 'A' is the titration for sulfuric + 1/3 of the phosphoric, 'B' titrates an additional 1/3 of the phosphoric.
*A 1.600-1.800 hydrometer and 300 ml hydrometer (non-graduated) cylinder are usually suitable for measuring SG.
**Use a TC 'to contain' pipette
[pipettes on
eBay or
Amazon [affil links]
; it permits flushing out the sticky sample aliquot using DI water.
Making acid additions requires algebra, as the concentrated acids include water and the total solution volume increases. Agitate or stir very, very well before re-sampling. Excess water can be removed by evaporation (heating).
Productivity of an unspecified EP composition at unspecified temperature for electropolishing parts of unspecified geometry and metal using unspecified racking?
Some general comments (opinions):
High phosphoric baths cost more and may have ~infinite life but require closer anode-cathode spacing.
High sulfuric baths cost less and have better throwing power but are perhaps prone to etching at low current densities.
The acid-to-water ratio varies with phosphoric-sulfuric ratio and is perhaps more important. Some of Charles Faust's original phosphoric-sulfuric recipes for electropolishing stainless steels are given in US Patent 2,334,698 (1938).
Search this site for more electropolishing info. Also, several vendors offer electropolishing seminars.
Hope this helps.
- Goleta, California

Rest in peace, Ken. Thank you for your hard work which the finishing world, and we at finishing.com, continue to benefit from.
Q. Hello,
We use a hygroscopic electropolishing solution consisting of sulfuric and phosphoric acid. Over the course of electropolishing, metals (Ni, Cr, Fe, Mo) get released into the solution. The Fe content plays a critical role in electropolishing. We have been able to determine the Fe content by Redox titration, but since it is a very tedious method (takes about an hour) we are exploring other techniques...like the XRF.
In order to do the measurements by XRF, we first have to develop a calibration standard. Now since the solution is hygroscopic, how will this effect the readings? (the specific gravity of the solution is sometimes manipulated by the additon of more solution or DI water, or a combination of both). If XRF is not the way to go, is there a better technique to determine metal content?
Thanks,
- New York, USA
February 27, 2013
October 16, 2019
Q. Hello everyone in this community!
I would like to know if there exists a titration procedure to determine the amount of the acids - sulfuric acid & phosphoric acid and nickel sulphate in the electropolishing solution.
I used to carry out the titration to determine just the acids in the past, but when the bath gets aged, I believe that the titration results are getting inaccurate due to the formation of Nickel sulphate.
I Electropolish Stainless steel grade 316 and I use a polishing solution comprising of sulfuric acid, Phosphoric acid and water.
This was the titration procedure that I have been using to determine the acids:
Determination of phosphoric acid by methyl orange
⇦ on
eBay or
Amazon [affil links]
indicator
1. 5mL of the concentrated EP solution was diluted to 500mL.
2. 10mL of this diluted solution was taken in a conical and was further diluted by adding 150mL DI water.
3. methyl orange
⇦ on
eBay or
Amazon [affil links]
indicator solution was added to this solution.
4. This solution was titrated with 0.1N NaOH
⇦ on
eBay or
Amazon [affil links]
solution until the colour changed from pink to yellow ->Value A
Determination of sulfuric acid by phenolphthalein indicator
5. phenolphthalein
⇦ on
eBay &
Amazon [affil links]
indicator solution was added to this solution.
6. This solution was titrated with 0.1N NaOH solution until the colour changed from colourless to pink ->Value B
And, I used the following formulas to determine the acids:
Volume % of sulfuric acid = (2A-B) x 2.78
Volume % of Phosphoric acid = (B-A) x 6.22
Remaining % is water.
Now, I would like to see if there is a titration procedure to determine the amount of Nickel sulphate that could be combined with procedure.
I came across a titration procedure for determining the amount of Nickel sulphate by titrating with EDTA against murexide
[affil links].
Would it be possible to combine this procedure with my existing titration procedure of determining the acids?
Any sort of help is highly appreciated!
- Montreal, Quebec, Canada
⇦ Tip: Readers want to learn from your situation;
so some readers skip abstract questions.
Thank you for the information.
Could you please explain more about the calculation? I mean, from where does it take? The source of the calculation.
Thank you,
- Bekasi, West Java
A. Hi cousin Tri. Unfortunately, there are about a dozen individual titration calculations on this page for a number of different acids and metals in electropolishing solutions, ranging over 24 years, with some of the participants having passed away over the decades :-(
I appreciate that English may be your second language and that is causing you to try to be brief, but please introduce who you are, what you do, what individual material you want to analyze for in what kind of processing solution. Then hopefully someone can walk you through it. Thanks!
If you are totally lost rather than stuck on a specific step, googling "what is titration" or youTubing "titration" will help.
Luck & Regards,
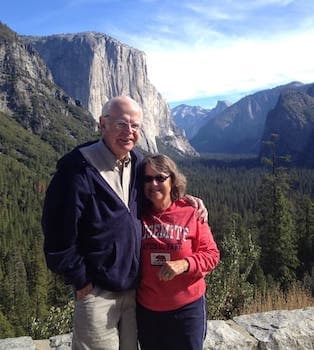
Ted Mooney, P.E. RET
Striving to live Aloha
finishing.com - Pine Beach, New Jersey
November 2020
Q, A, or Comment on THIS thread -or- Start a NEW Thread