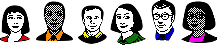
Metal finishing Q&As since 1989
-----
Phosphoric acid anodizing per BAC5555 and ASTM D3933-98, p.2
< Prev. page (You're on the last page of the thread)
November 5, 2011
Hello,
I am working on a Epoxy joint on Aluminium.
I have found some info regarding a Boeing procedure BAC5555 (Boric acid anodizing) on the internet. First tries with a 10 % boric acid solution at room temperature / 20 min / 15 V showed a big improvement. So I am now looking for the BAC 5555 to get more information.
Who can help?
Developer - Husum, SchleswigHolstein, Germany
A. Hi Bernd. I believe that BAC 5555 is Phosphoric Acid Anodizing rather than Boric Acid Anodizing. The spec can be obtained from Boeing commercial division or from some specification clearing houses like aerospheres.com.
Regards,
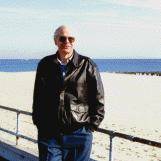
Ted Mooney, P.E.
Striving to live Aloha
finishing.com - Pine Beach, New Jersey
Can sulfuric acid anodizing be substituted for PAA
Q. I am working at a US Air Force base. It uses sulfuric acid anodizing at many sites, and has a phosphoric acid anodizing operation in one building. This operation pre-cleans the thin aluminum aircraft skin/panels (with an alkaline cleaner), DI water rinses, etches (with ferric sulphate and sulfuric acid) and then phosphoric acid anodizes (with 30% HPO3). It is then sealed using DI water in a series of two dip tanks. The phosphoric acid anodized sheets are then pressure bonded.
Can this operation be switch to sulfuric acid anodizing?
We could more easily recycle the waste anodizing solution is we could convert the phosphoric acid anodizing bath to sulfuric. Is there any literature about the advantages and problems associated with switching from phosphoric acid to sulfuric acid anodizing? Will it require a different sealer, such as with sodium chromate?
We have been told that the sulfuric acid process is more temperature sensitive, and we might have to install a chiller and a heat exchanger to control the temperature. Other changes? Thanks, Nick
Nick ConkleBattelle - Columbus, Ohio
2000
1 of 2 simultaneous responses
A. The main office, downtown, used to have one of the finest libraries going. Phosphoric anodizing is well known as being superior to sulfuric acid for bonding purposes. I rather doubt if the gain is waste treatment is worth the reduction in bondability. That is a management decision. since it involves the military, you may die of old age before a change is approved.
James Watts- Navarre, Florida
2000
2 of 2 simultaneous responses
A. Are you sure that the DI water tanks following the PAA are for sealing, versus rinsing? What is the temp of those tanks? Nonetheless, if the PAA is being called out for a pretreatment for a subsequent pressure bonding operation than the answer is no, sulfuric acid anodizing is not the coating of choice for a variety of reasons.
The only other anodize treatment called out for bonding prep work is CAA which now brings Hex Chrome into your facility. The surface morphology of PAA, and coating thicknesses produced are much better suited to bonding operations than SAA.
Ward Barcafer, CEFaerospace - Wichita, Kansas
2000
Thanks you for your input regarding the suitability of sulfuric acid anodizing as a substitute for PAA. Nick
Battelle - Columbus, Ohio
2000
Need an alternative to PAA
Q. I am working on a project to find alternatives to Phosphoric Acid Anodizing to actually try to eliminate the phosphoric acid. I don't think this is possible, but I thought I should at least try to post the question. One option was to eliminate the entire process and propose Ion Beam Assisted Deposition treatment to the components. Any thoughts.
Susan Brandick- Johnstown, Pennsylvania, USA
A. The next best process to PAA would be any method of etching the aluminum surface to roughen the profile. Chromic acid etch, sand blast, bi-fluoride etch, sanding. Basically any of these processes would have to be tested for relative bond strength.
Michael G. Broussardplating and metal finishing shop - Albuqerque, New Mexico
A. You might find the article "An Alternative to Anodization: Sol-Gel solutions for Metal Finishing" published in Metal Finishing, December 1998, to be of interest to you.
Bill ParkSpace Systems/Loral - Palo Alto, California
2000
Bonding aluminum to carbon fiber for race cars
Q. My company is co-molding forged 2014 aluminum inserts into a carbon fibre component for the auto racing industry. We are currently grit blasting, acetone [on eBay or Amazon (adv.)] washing and priming the material with BR127 from Cytec, before laminating with glass/carbon preimpregnated with epoxy based resins. We are researching either chromate surface conversion (CAA) or PAA for better bonding performance, but are getting conflicting information from various anodizing sources. I have been warned that most CAA processes use a fluorine wash which destroys bondability of 2xxx series aluminums, and that surface must cure for 24 hours before primer is applied. Others tell me that PAA requires primer application within 3 hours of anodizing and near clean room surroundings to avoid subsequent damage. Also, PAA anodizers say you can laminate carbon skins directly to the converted surface without galvanic problems, but other coatings still require a glass barrier. This is auto racing, not aerospace, so we have some flexibility, but still cannot tolerate problems.
My basic question is: what is the ideal corrosion inhibitor/bonding preparation for 2014 aluminum (forged) for subsequent bonding to glass/carbon using epoxy resins.
Thanks,
Josh Poertner- Speedway, Indiana, USA
Filtration of PAA solution
2003Hello,
I work for a company that specializes in composite structures. We currently have a small PAA outfit and would like to get it Nadcap approved. Currently, Nadcap does not have a specific PAA spec, but one will be handed down soon after their quarterly meeting this month. We are trying to get BAC5555 compliant since it is going to be used as the "straw man" for the new Nadcap spec. I was hoping someone could suggest a filtration technique for the acid tanks to keep chloride and fluoride levels down to acceptable levels (35 ppm for chloride, 75 ppm for fluoride). Our current system needs to be improved upon. If you are curious about Nadcap, the meeting results should be available on their website at the end of the month.
Thanks for any replies!
Paul Bozzo- Sacramento, California, USA
----
Ed. note: We have a long and interesting but highly charged thread about Nadcap as "Trouble with NAPCAP Audits", letter 27698.
Shop Problem: Is fungus/algae buildup causing white streaking?
Q. We have developed a white residue after our parts are removed from the Phosphoric Acid anodizing Tank which is causing streaking.
Is this the fungus that I have read about or something else?
TTF, LLC - Breaux Bridge, Louisiana, USA
2006
Q. I am looking for any information on the removal and control of algae that is in our Phosphoric Acid Anodizing tank. This solution of a 75% Phosphoric Acid at 16 oz / gallon of water is maintained at 77 F. The use of a Ultra Violet system has been mentioned as one possible cure?
Eddie Roach- Tulsa ,Oklahoma
2001
----
Ed. note: Hello, David and Eddie. We have an excellent thread about Control of Algae in PAA; please see letter 34342.
Shop Problem: Can't remove tape after adhesive bonding
Q. We are using a tape to hold Phosphoric Acid Anodised details together during adhesive bonding (350°F) and the tape we are using is leaving a residue which we can't remove with a solvent. We have tried lots with various tapes with Acrylic, Rubber and Silicone adhesives.
Desperation is setting in. Can anyone recommend a really good high temp tape?
Thanks
Ciaron MurphyAerospace Repair - Blackwood, South Wales, Britain
2004
Shop Problem: Incoming aluminum is too smooth for bonding
Q. Is it possible for an aluminum surface to have too low of a surface roughness for phosphoric acid anodizing? Our PAA plater is getting hardware(no roughness specified) where the surface has a mirror like finish, probably a 2-8 RMS. They state that at this low roughness the plating has problems adhering. I am skeptical-any truth to this? Thanks!
William Pinzon- Greenlawn, New York, USA
2005
A. We have tinkered with PAA over the years typically applying adhesive primer after anodizing, but anodizing is a conversion coating. Specifically, little protruding oxide fingers rise right up out of the aluminum - I'm not sure that a smooth surface or a rough surface would have any difference - a clean and properly deoxidized surface will behave identically given the same electrolyte, current density, etc. Are you sure your anodizer isn't talking about adhesion of the primer to the PAA - this might have some merit - however, with PAA being only a fraction of 1 micrometer in thickness, I'm not sure it matters.

Milt Stevenson, Jr.
Syracuse, New York
2005
Should PAA solution turn yellow after use?
Q. My company has a small phosphoric acid anodize set-up for prepping 5083 Al and 2024 Al. We would like to know if it is it normal for the solution to turn a yellow color after processing. We are using a 10% PA solution in a glass tank with aluminum cathode and aluminum racks, voltage 10-15 v per ASTM D3933-98. We previously had not experienced this yellow color change until we recently improved the electrical contacts and the mechanical contacts holding the parts to the racks. Does the spent solution turn yellow with continued use?
David F [last name deleted for privacy by Editor]- Oakland, California, USA
2002
A. First of all, you probably want to use stainless steel cathodes instead of aluminum for PAA. The aluminum cathodes will be dissolved continually in phosphoric acid, shortening your bath life.
The discoloration could be related to some of the alloying materials dissolved in solution. For alloys with a lot of Chrome, the solution will become a greenish color. I would guess that the copper from the 2024 alloy could be somewhat to blame, along with whatever dissolved out of your cathodes.
I am not an expert, but this would be my guess. I wouldn't be too worried about it until the concentration climbs above what is allowed.
- Zeeland, Michigan, USA
March 29, 2016
Q. Looking at ASTM D3933-98, there are two voltage levels, 10 ± 1 V for a single rack and 15 ± V for a multi-rack. So our racks have 5 bars on them that we hook parts to, but they are electrically all connected. Does this count as a single rack, or a multi-rack. I wasn't sure if they were thinking about a process line where you could put racks into a processing tank independently or if they were thinking about a set up like ours with multiple bars?
Thanks,
-Kirby
Aerospace repair facility - Bristow, Oklahoma, USA
March 26, 2019
Q, A, or Comment on THIS thread -or- Start a NEW Thread