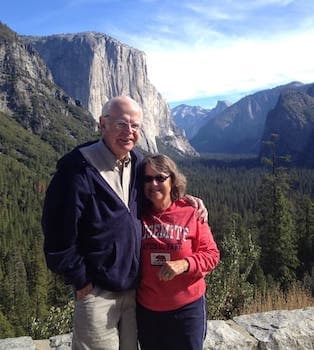
Ted Mooney, P.E. RET
- Pine Beach, NJ
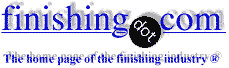
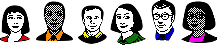
The authoritative public forum
for Metal Finishing since 1989
-----
Chemical Polishing (Bright Dipping) of Aluminum
Q. I have been looking at chemical polishing of aluminum with a phosphoric-nitric mix and was wondering what materials were used to make the baths, and what special requirements would be needed to pump the solution.
Nathan Havercroft- Manhattan, Kansas
2000
A. The typical material of construction for bright dip equipment is 316L stainless steel. Be very careful of the L portion; it stands for extra Low carbon. If you don't use all 316L you will get chromium carbide precipitation in the heat affected areas adjacent to welds, which will corrode quickly.
Lee BranchRichmond, Virginia
2000
A. Hi, Nathan.
An additional aspect to consider is the need for a special ventilation system. This solution evolves clouds of mustard color toxic NOx, and lip-style tank exhaust is probably not adequate. The bright dip tank and the first rinse usually need to be installed in a "garage" ventilation system, and may require a two-stage fume scrubber rather than a conventional one.
Regards,
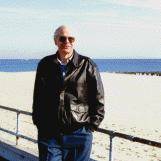
Ted Mooney, P.E.
Striving to live Aloha
finishing.com - Pine Beach, New Jersey
September 23, 2010
A. If you go the route of electropolish instead of bright dipping (its not so extreme in its temperature requirements if that matters, and because of its use of electrical means its more controllable). The problem with the electropolishing being that the only true tank material they've found to hold the electrolyte and maintain a reasonable lifespan is Kynar(tm). Apparently its life is very good, but a sheet of the stuff will set you back 1200-1500 dollars, so you're looking in the neighborhood of 5K+ to put a decent sized tank together. If they could figure out a way around this, they'd have more acceptance I'm sure, but it's a large hurdle to jump for any shop.
Matthew Stiltnerplating company - Toledo, Ohio
2000
RFQ: I am looking for a vendor to perform aluminum bright dip operations. Our annual aluminum bright dip requirements are ~ 1500 pieces ranging from 28" x 1.3" diameter tube to 1" x 1" diameter machined part of alloy 1100 aluminum. If this is something within your capabilities and you are interested, I will need a description of the process and any quality systems you have in-place. I would prefer a vendor in the northeast.
Thank you,
James L [last name deleted for privacy by Editor]- Horseheads, New York
2001
Ed. note: Sorry, this RFQ is old & outdated, so contact info is no longer available. However, if you feel that something technical should be said in reply, please post it; no public commercial suggestions please ( huh? why?)
Q, A, or Comment on THIS thread -or- Start a NEW Thread