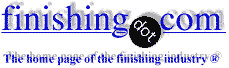
-----
Confusion over hexavalent vs. trivalent chromating on zinc plating
2005
We are a supplier of switches using Zinc Die cast housings to the automotive industry. Over the past year we have been changing from Yellow Hexavalent chromate conversion to a clear Trivalent Chromate conversion on the Zinc housings. I recently change a housing to the Trivalent Chromate on a switch which is grounded through the Zinc housing. Aside from the Trivalent Vs Hexavalent change, our supplier is now using a Zinc preplate under the Trivalent conversion to improve corrosion resistance. The switches using the new Trivalent conversion appear to have a higher resistivity than the old yellow Hexavalent conversion without the Zinc preplate. Is there a difference in the conductivity of the Hexavalent chromate vs. the Trivalent Chromate?
QUICKSTART:
July 2017: Zinc and zinc alloy electroplating invariably require & receive chromate conversion coating to deter white rust. Until about 20 years ago this was almost always hexavalent chromate because it delivered corrosion resistance that was far superior to what was available from trivalent chromating. But in the last two decades, because of increased concern over the toxicity of hexavalent chrome, much research has gone into improving trivalent chromates, and many codes (RoHS, EOLV, Reach) and many standards (Automotive especially) demand it.
Many of the new trivalent chromates employ "sealers" or "topcoats", although our understanding is that the "thick film" trivalent chromates do not. Some cautions that are in order when reading these dialogs are:
- trivalent chromating is now much better than it was some years ago, so it can be necessary to dismiss some very old postings which claim inferior corrosion resistance;
- the biggest concern for the new generation of trivalent chromates was corrosion resistance, and they may not be the equal of hexavalent chromating in all regards;
- trivalent chromates are highly proprietary, and what may be said of one may not hold for all.
Thank you for your time and assistance in this matter.
Raymond V Dart Jr
Low voltage automotive switch and sensor supplier - Canton, Massachusetts, USA
A. You need to specify your needs carefully, Raymond. In general, trivalent chromate per se does not offer the corrosion resistance that hexavalent chromate offers. So there is a tendency for shops, if left to their own devices, to apply a silicate or other topcoat or a water soluble lacquer on top of the chromate. In many applications, this has no downside ... but in some it does.
Ted Mooney, P.E.
Striving to live Aloha
finishing.com - Pine Beach, New Jersey
2005
2005
A. Bingo Ted! Sealers are becoming too widespread without OEM's and specification organizations taking this into account. While the auto world loves them, they create fits for anyone in the electronics field that believes they're getting the same old surface conductivity. Platers could use common sense too, but then how is the plater supposed to know that increased resistivity might be a concern?
Platers have trouble even getting steel hardness out of manufacturers despite baking guidelines that clearly require them. It all comes down to communications and clearly defined expectations.
Milt Stevenson, Jr.
Syracuse, New York
2006
Q. Due to the European directive we are having to change the plating on our automotive parts.
Parts are currently Hexavalent (dull yellow).The proposed alternative is Trivalent.
On a typical EN1A union what would be the typical salt spray resistance for the two plating methods?
Josh Smith
Auto parts Ltd - England
2006
A. Trivalent chromate conversion coating has been around for decades, Josh, but in the old days it had very poor corrosion resistance. What has happened in the last few years is that highly corrosion-resistant trivalent chromating processes have been developed which allow compliance with RoHS without a big performance hit. So the answer is that you should demand of your new trivalent chromate the same performance that you received from hexavalent.
There is no "typical" though. All of these chromates are highly proprietary. Some generate thick films; some are thin films with a topcoat, and so on. Specify the required salt spray resistance and any other requirements, and the plating shop will have to meet those specs. Good luck.
Ted Mooney, P.E.
Striving to live Aloha
finishing.com - Pine Beach, New Jersey
2006
A. Josh
It is not clear from your question if you are a user or a plater.
The deposit on parts is chrome metal. It contains neither trivalent nor hexavalent chrome. If you are a user, you are only interested in the physical properties of the deposit, not how it got there.
The EH has finally found out that when chromium trioxide is dissolved in a plating bath, it does not necessarily produce hexavalent chrome ions. Once again, the EU is legislation on matters it does not understand but sounds good to most people and makes them look 'greener'. (They look pretty green to me)
In UK, the Institute of Metal Finishing will keep you up to date on the current state of this and similar legislation.
I suggest that you do not rush into changing a well established finish for one with no track record, particularly where there may be real issues of safety involved.
Geoff Smith
Hampshire, England
2006
Once again, Geoff, we are into that confusing question of ...
whether we are talking about chrome electroplating, which is valence 0 regardless of whether the bath was hexavalent or trivalent or
...
whether we are talking about a chromate conversion coating on zinc plating (or other metal), which is a hexavalent gel if deposited from a traditional hexavalent bath.
I took it from Josh's question, where he described the color as dull yellow, that he was talking about chromate conversion coating rather than chrome plating, but I may have misread.
Ted Mooney, P.E.
Striving to live Aloha
finishing.com - Pine Beach, New Jersey
2006
A. Hi,
Ted, Josh mentioned about automotive parts and European union directive. I think he is referring to ELV (End of life Vehicle) not RoHS. RoHS refers to the European union directive for electrical and electronic industry.
SK Cheah
- Penang, Malaysia
Thanks Cheah, you're doubtless correct. I tend to be too careless about whether it's RoHS or ELV or REACH or automotive standards or whatever that is precluding hexavalent chromating in a particular sector ... but the end result is that it is rapidly becoming precluded in all sectors :-)
Regards,
Ted Mooney, P.E.
Striving to live Aloha
finishing.com - Pine Beach, New Jersey
Q. I am in the automotive industry and a new Quality Engineer so therefore I am rather new to plating but willing to learn. There seems to be quite a bit of confusion at the plant that I work at as to the proper callout between hexavalent and trivalent. The callout that is in question is MFZn8-C. I know that one of our suppliers is claiming MFZn8-C to be a trivalent coating. But yet another customer is claiming MFZn5-C to be a hexavalent coating. The only difference between the two callouts that I know is the 5 and 8 which to my understanding is the difference of the coating thickness. Can this coating callout be for both hexavalent and trivalent? If so is there a specific book that would explain the breakdown of the coating callout so that I can understand it better? Or what is the proper callout for trivalent coating? If you could shed any light on these questions it would be greatly appreciated.
Thank you.
Jeff Marshall
- Columbia, Missouri, USA
2006
2006
A. Although this is probably the umpteenth time for regular readers, newbies are always very welcome, Jeff!
Traditionally, trivalent chromates exhibited far less corrosion resistance than hexavalent chromates; so although they have existed for many decades, they were rarely specified. Chromates were "de facto" hexavalent and most people didn't even bother specifying it.
But in response to RoHS & EoLV pressures and other requirements to get hexavalent coatings off of parts, new generations of trivalent chromates were developed in the last few years which can often, but at somewhat greater cost, approximately match the corrosion resistance of hexavalent chromates. Consequently there has been an industry-wide switch over the last few years to the point where trivalent chromating is by now probably more popular than hexavalent chromating.
To keep up with the curve, and stay ahead of it, you should specify trivalent chromating unless there is a compelling (but temporary) reason not to. Some specs don't yet incorporate the distinction, so you must add as a note the requirement that the coating be "trivalent and RoHS-compliant".
If you don't move to trivalents, I would be fearful of being caught at "musical chairs". In the not too distant future, as less and less hexavalent chromate is used, it will suddenly become socially unacceptable to use hexavalent chromates -- and the people still using it may receive much more attention than they want :-)
What do you call the people still using it when he music stops? As Julia Roberts says in 'Erin Brockovich', "They're called boobs, Ed" :-)
Ted Mooney, P.E.
Striving to live Aloha
finishing.com - Pine Beach, New Jersey
A. MFZn5-C or MFZn8-C are codes that come from a Japanese specification, likely Nissan M4040 from the coding, but it could be from others. You need to find out from the drawing or the customer what specification the code is taken from. The specification should then tell you whether hexavalent chromates are allowed, for the most part they are not. As it happens, M4040 has grandfathered older codes for hexavalent materials with newer codes that are specific for trivalent chromates. MFZn5-TC is an example where the T means trivalent. Practically, I would not recommend using a hexavalent chromate on an automotive part without a clear understanding from the customer that they will accept a non-RoHS compliant finish.
Don Troy
- Monee, Illinois, USA
May 8, 2012
Q. Good day:
I would like to know the next information regarding the Trivalent vs. Hexavalent process, please:
1.- How many hours are the standard to corrosion for Trivalent CR+3? 36, 48 hrs, etc?
2.- How many hours are the standard to corrosion for Hexavalent CR+6? 36, 48 hrs, etc?
Regards
Raul Garcia
- Apodaca Mexico
September 27, 2012
A. Hi Raul. Different automobile companies have different standards calling for different hours. And trivalent chromates are proprietary and use different approaches, with different results. Some vendors claim up to 300 hours to white rust.
But the most general generic answer is probably that traditional iridescent yellow hexavalent chromates were expected to survive 96 hours to white rust in an ASTM B117 test, and trivalent substitutes must achieve the same.
Nabil Zaki's article "Trivalent Chrome Conversion Coating for Zinc and Zinc Alloys" in the Metal Finishing Guidebook is outstanding and will answer nearly any question about trivalent chromating. Good luck.
Regards,
Ted Mooney, P.E.
Striving to live Aloha
finishing.com - Pine Beach, New Jersey
September 28, 2012
Q. I'm curious about Hexavalent versus Trivalent. I have done the usual internet research but opinion seems to be divided, some claim that trivalent has better corrosion and wear properties and some claim it doesn't? Can someone point me in the right direction?
Oliver Gwynne
Bronte - united kingdom
June 28, 2017
A. Hi Oliver. I would say the trivalent chromates exhibit corrosion resistance equivalent to hexavalent chromate. All trivalent chromates are proprietary, so they differ one from another. A given vendor is certainly welcome to claim superior corrosion resistance, higher temperature resistance, or greater hardness and it may even be true rather than just sales blather -- but that doesn't make other unspecified trivalents superior.
And the other point, of course, is that hexavalent no longer has a champion to supply a balanced perspective. For example, a vendor may say "our trivalent offers 192 hours to white rust whereas hexavalent chromates only offered 96", but it is not necessarily true that no platers exceeded the 96 hour minimum requirement with hexavalent chromates. Further, most trivalents employ sealers or topcoats to achieve their corrosion resistance, but some hexavalent chromate platers also used water soluble lacquers or other topcoats on their hexavalents to increase their corrosion resistance -- so it's not entirely fair to offer a comparison of trivalents with a topcoat against hexavalents without one :-)
Regards,
Ted Mooney, P.E. RET
Striving to live Aloha
finishing.com - Pine Beach, New Jersey
July 2017
July 11, 2017
A. Prior to the introduction of trivalent passivates, hexavalent chromates provided salt spray protection from 24 hours (blue-bright chromates), more or less, up to 96 hours, more or less (yellow and olive drab chromates). The amount of corrosion protection was largely a function of the amount of chromium (actually, both hexavalent and trivalent) in the conversion coating.
I see the same characteristics in the trivalent passivates. Keeping in mind that trivalent passivates function by generating hexavalent chromium in the corrosion process, those trivalent passivates with small amounts of trivalent chromium might give you 24 hours - or maybe not. But the 'thick film' passivates (say 900nm or so) have a lot of trivalent chromium capable of being oxidized to hex. The same is true of dry-in-place trivalent passivates. These perform as well or better than hex yellows - mainly because they have more chromium.
The silicated sealers that Ted mention are themselves corrosion inhibitors. But not excellent corrosion inhibitors like hex chrome. But they function synergistically with hex chrome from either kind of passivate and can give upwards of 500 hours of neutral salt spray.
Tom Rochester
CTO - Jackson, Michigan, USA
Plating Systems & Technologies, Inc.
Q. Can anyone tell me what the disadvantages are (if any) of performing hydrogen-embrittlement baking after a trivalent passivate film has been applied to a zinc-plated part? We have been doing this for years, with no issues, but many plating specs still state that baking is to be performed "prior to the chromate step", which mainly used to apply to hexavalent chromates. Any input would be appreciated.
I need some expert clarification. When trivalent passivates first hit the zinc industry, one of the advantages (I was told) was that plated parts could be baked for hydrogen-embrittlement after the passivate film was applied, and not only would the passivate withstand the oven temperature (375 °F), it's corrosion protection would/could slightly improve. I have tested some Type VI yellow parts and found this to be generally true, although the heat does alter the color slightly. I remember this being a huge selling point, as this meant we no longer had to tie up the plating line twice, first for plating, then again to apply the color, like with hexavalent chromates.
Recently, however, I was told you cannot bake trivalent passivate films, as this converts them back to hexavalent chrome. Is this true? If not, are there any other legitimate reasons NOT to bake parts after the trivalent passivate is applied?
Bruce Brady
- Lincoln, Nebraska, USA
September 13, 2017
A. Hi Bruce. You have been doing this for years, but have you been doing salt-spray testing after it? I'd be happy to be disabused of obsolete thinking, but I've always believed that hydrogen-embrittlement relief baking temperatures were unsafe for any chromate -- not because of conversion to hexavalent but because dehydration of the film spoils its corrosion resistance. But perhaps your sealer keeps that from happening (baking of powder coated chromated parts seems to not be a problem, as sort of a parallel).
Regards,
Ted Mooney, P.E. RET
Striving to live Aloha
finishing.com - Pine Beach, New Jersey
September 2017
Q. Thank you very much for your response, Ted. Yes, we have performed some NSS testing after bake. Our baked trivalent yellow (no seal) surpassed 240 hours (no white corrosion) before we finally decided to end the test. The trivalent clear products seemed to test about the same with or without bake, no significant improvement, but no discernible harm, either.
Again, as I was taught years ago, this is because the trivalent passivate films are not gelatinous like hex chromates, therefore they do not dry out and degrade in the heat.
Thanks again, and any input is welcome!
Bruce Brady [returning]
- Lincoln, Nebraska USA
September 19, 2017
September 21, 2017
A. Hi Bruce!
We do it as you, and we can say NOT ALL CHROMATES withstand baking after them.
Fluoride-based trivalent chromates lose its corrosion protection properties after baked, so all cheap ones can't.
Medium and high performance chromates can withstand baking without losing much (or none) corrosion resistance performance. There are many formulations that are prepared just for that use.
It is true that heat (no more than 140 °C, 285 °F) improves corrosion resistance in all trivalent chromates, and they contain less humidity than hex chromates. In hex chromate conversion coatings heat would disturb its structure mostly because of the hex chrome present in them. Both are layers of trivalent chrome oxide over zinc!
For thick trivalent chromates, there is no risk for baking (no more than a couple of hours, though) after applying them. BUT you must test them for salt spray and embrittlement as it could drop a day or two its resistance if the chromate isn't in perfect condition, and chromate film makes a little more difficult for hydrogen to get out of the part.
Conclusion: In my experience, it can be done with the adequate controls, we do it since 2010 with really good results as you :)
Daniel Montañés
TEL - N FERRARIS - Cañuelas, Buenos Aires, Argentina
Q, A, or Comment on THIS thread -or- Start a NEW Thread