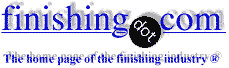
-----
How to make gold plating last longer?
Current questions and answers:
January 1, 2022 Hi Ted / Everybody - Happy 2022!
Firstly may I just comment on what a veritable wealth of knowledge here Ted.
- Read a few answers and was blown away at the in-depth answers.
Q. Right, so, I would like your opinion please on how best to go about preserving the shelf life of Jewellery I produce which is mainly copper/brass based & mixed Alloy based, i.e., copper/nickel + lead.
Jewellery is then all Silver + Gold plated, but of course does not stand the test of time in various climates I ship to.
Therefore, have been looking into this "e-coating /electro coating", etc.
Any advice / opinion you could provide would be greatly appreciated / very welcomed.
Thank You.
Jewellery Manufacturer - London, England
A. Hi Raj. Thanks for the kind preface, but it prompts me to add a preface as well ... There was a time long long ago when gold plating might be as much as 20 microns thick. It gradually got much thinner. When I was a young man 2-1/2 microns was considered high quality plating and 1 microns was the "cheap" plating you'd find on costume jewelry a high school boy might give to his steady. Then it became a half micron, and a quarter, and even a tenth of a micron ... to the point where some people today nervily call one tenth micron plating "high quality" :-)
The point being that no matter how thin the plating, people will naturally always want it both thinner and longer lasting. But there may be a point at which the gold plating is already so thin and the actual cost of the gold so low, that it's questionable whether money can be saved by reducing the gold plating thickness but adding the cost of additional more exotic topcoats.
I'm told that inexpensive, easy to apply 2-component automotive clearcoats are reasonably good.; I'm told that UV-cured topcoats (fingernail lacquer) are reasonably good and inexpensive to apply. Although I have seen electrocoating a few times; I have not personally seen an electrocoating line for jewelry, but imagine it to be rather expensive capital equipment.
The suppliers of electrophoretic lacquer can do samples for you and you can compare them to what you get from automotive clear coats or UV-cured clearcoats before committing to actually installing an e-coating line, but I suspect that focusing on proper undercoats like high quality white bronze plating, plus making sure your gold or silver is thick enough to be pore-free, followed by the simple clearcoats will be fine for low and medium volume. If you are into really high volume that justifies large capital expense, I suspect you will be happier with titanium nitride PVD hardcoating than with electrocoating ... but all I know is what I read -- I don't have hands-on experience with such comparisons.
Luck & Regards,
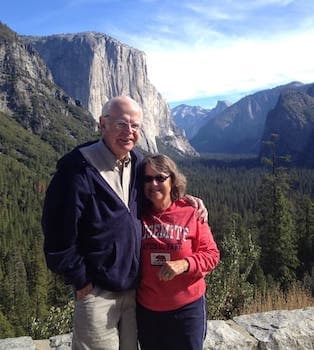
Ted Mooney, P.E. RET
Striving to live Aloha
finishing.com - Pine Beach, New Jersey
January 2022
February 8, 2022
Q. Hello there Ted,
Big thanks for your time & effort, and of course wonderfully insightful & mighty helpful suggestions.
I wish I could afford PVD hardcoating than with electrocoating, but not viable as not enough volume.
But will certainly be upping the Silver levels, come what may, because I cannot stand for customers being short changed for any reason.
In addition, like you kindly suggested / and a lot of people here agree, to apply electrophoretic lacquer, simple one's as mentioned : 2-component automotive clearcoats / UV-cured topcoats.
My follow up here would be, again to try & mitigate any nefarious activity / sub standard application of these top coats , + additional silver plating content.
Is to perhaps, reverse engineer the items. In the sense, I order them as they are, - And in effect, apply a further coating of Silver (say 1 Micron) , and then go for the Topcoat.
This way , for me, I am in control of the most crucial aspect here in London.
You think that can be done Ted ? Without breaking the bank?
I mean could / would actually be willing to spend probably up to £5 per piece to try and have these Jewellery items meet a better standard.
Will look forward to your reply, and thank you again for your time. Appreciate it a great deal.
- London
A. Thanks again for the kind words, Raj. I can't help you further but hopefully another reader will.
While I understand metal finishing and how to retard corrosion, tarnish, and other problems, I have no actual experience with jewelry manufacturers, distribution methods, industry practices, etc., so I don't know what options are available to you, so can't offer practical advice on how you can best fulfill your requirements :-(
Luck & Regards,
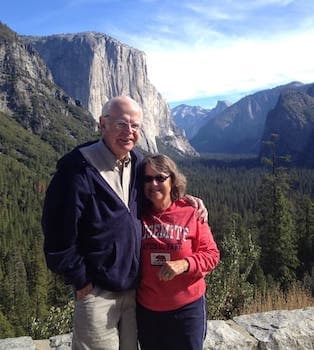
Ted Mooney, P.E. RET
Striving to live Aloha
finishing.com - Pine Beach, New Jersey
February 2022
February 9, 2022
Q. Hi Ted,
Glad you're well & many thanks at least for the reply.
If anyone else please, perhaps has an opinion to share on this approach? - It'd be very welcome.
I.E-
To retrospectively apply a further coating of silver plating on the silver plated jewellery, and then adding a topcoat on that too.
In truth I don't see why it would be problematic for any reason, but just wanted to make sure.
- Yes, probably not as cost effective as getting it done at manufacturing stage, but with the way thing's stand, and my inability to travel over to India to oversee thing's which I count on always doing, . . .I'm reticent to give a whole new spec order without me there, if that makes sense - that's all.
So please if anyone does have an opinion on this, or a better suggestion, then I'd be very grateful. / will give me peace of mind.
Thanks all.
- London, England
⇩ Related postings, oldest first ⇩
Q. Hello,
We import gold plated jewelry from various different countries including, China, India.
The gold plated jewelry usually doesn't last long and will tarnish within 12 months, Usually using 1 micron gold plating.
We want our jewelry to last longer, for at least 3 years wearing it everyday. I have heard about PVD process and using titanium nitrides, I have asked many manufactures about PVD on jewelry and they tell me its not suitable for jewelry as it doesn't give the right gold color for jewelry, they tell me its too bright and mainly used on door handles etc but not for jewelry.
Is this correct? Does anyone know of a manufacture that can do PVD Titanium nitrides over brass/copper for jewelry or any other suggestions for increasing the wearability/durability without a too heavy price tag?
Mat JohnsonJewelry - Australia
2006
by Steve Borichevsky
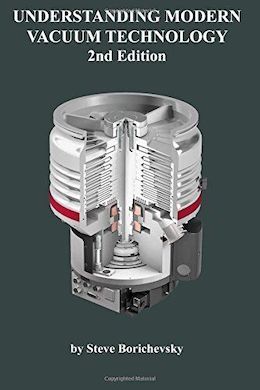
on eBay or Amazon
or AbeBooks
(affil link)
by John F. O'Hanlon
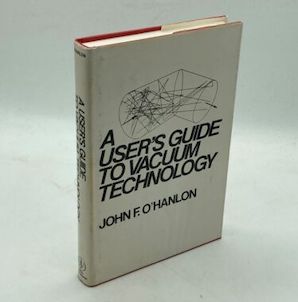
on eBay or Amazon
or AbeBooks
(affil link)
A. Hello, Mat. Actually, I think it is a fairly well developed technology to combine titanium nitriding PVD processing and gold plating to provide a good gold color and a wear resistant surface. The thing is, it is rather inexpensive for a very small shop to do gold plating (especially if they don't have environmental regulators monitoring them), but a PVD vacuum chamber is major capital equipment. So you won't often find tiny operations offering titanium nitride assisted gold plating.
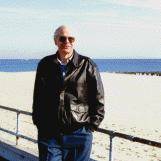
Ted Mooney, P.E.
Striving to live Aloha
finishing.com - Pine Beach, New Jersey
2006
A. Ted is exactly right. The technology for using titanium nitride and gold is well tried and tested. The titanium nitride is put down first as a "rough" deposit and then gold electrodeposited into the valleys of the rough surface. This gives a very high amount of gold on the surface, but it is protected by the "peaks" of TiN, so it doesn't wear away too fast.
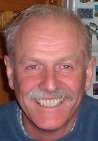
Trevor Crichton
R&D practical scientist
Chesham, Bucks, UK
2006
A. Gold is soft, so it wears fairly fast. 1 micron is about enough to give it color. It also depends on what it is plated on. Copper and zinc will migrate thru a coating that thin in a few weeks.
You get what you pay for sometimes. Cheap will be cheap in most countries.
- Navarre, Florida
2006
Q. Thanks for your reply, I wonder where I can find a suitable manufacturer to do the PVD Titanium Nitrides combined with gold electroplating?
Best Regards,
Jewellery - Australia
2006
Ed. note: This RFQ is outdated, but technical replies are welcome, and readers are encouraged to post their own RFQs. But no public commercial suggestions please ( huh? why?).
Although gold electroplating onto a TiN surface may be possible, our understanding is that the usual technology is to vacuum deposit the gold layer as well as the TiN layer.
A. One micron of gold should give a reasonable life for costume jewelry. Most costume jewelry is plated with a 'flash' of gold which is much less than a micron. Check the thickness; are you getting what you paid for?
Tarnish of thin gold deposits is associated with porosity or diffusion of the base coat. It is usual to apply an intermediate layer. In industrial applications this is usually nickel but some people are sensitive and can develop a form of dermatitis (do they never take their jewelry off?). Palladium/nickel is commonly used. Your supplier should know this.
P.S. 1 micron of gold cannot be accurately measured by microsection. You will need XRF - talk to a local plating house.
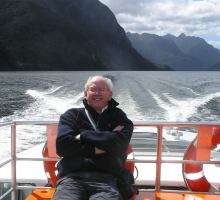
Geoff Smith
Hampshire, England
2006
Q. I am very curious about the use of titanium nitride underneath gold plating for costume jewelry. I have customers who are using anywhere from 3-5 mils to 6-8 mils gold, often with e-coating on top.
Anyone familiar with the cost of e-coating and titanium nitride who can provide me with a comparison in cost? would replacing e-coat with titanium nitride be cost neutral? would it be a more effective option?
Also, does the color of titanium nitride work only with a shiny gold finish? Some of our customers use an oxidized or even matte gold. If the gold plating were to wear off, would the titanium nitride beneath be very obviously different in color?
Thank you in advance!
- New York, New York, USA
May 4, 2011
Unique Colors for Gold
June 21, 2011by Reid & Goldie
-- hard to find & expensive; if you see a copy cheap, act fast!
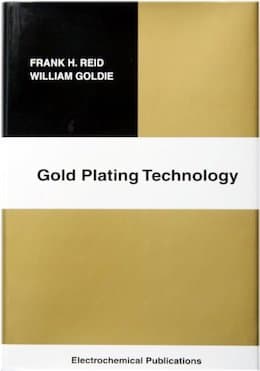
on eBay or Amazon
or AbeBooks
(affil link)
by C W Zanariah Ngah
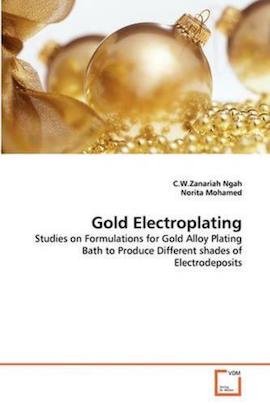
on eBay or Amazon
or AbeBooks
(affil link)
Q. Yeah, I have the same question. My jewelry coming from many sources, so I want to have a unique color of 18k jewelry in my show room. Could you please to share with me where I could buy the tools and material to do that?
Thank you very much!
- HCMC, Vietnam
A. As per the series of experiments conducted by our company, the durability of depositing gold over titanium nitride would be as much as that of 1 micron. Sometimes the life term of the product can be 6 months also. To obtain a durability of nearly 3 years, it is recommended to do electrophoretic lacquer.
Amit Jain- Mumbai, Maharashtra, India
November 8, 2011
A. Hi Rebecca. Ideally, the titanium nitride is, as Trevor tells us, a rough surface with mountain peaks that protect the gold in the valleys from wearing off. Cost comparisons are difficult because non precious materials like TiN and e-coating lacquer are inexpensive, so you're usually looking at capital costs vs. labor costs. The capital cost of gold plating can be very low; jewellers can do it in a beaker [beakers on eBay or Amazon [affil links] with a stirrer on a hotplate. E-coating systems might cost $100,000 for a small setup to $1 million for a large one, and PVD systems cost something like $1 million and more. I believe it is relatively easy to incorporate 'contaminants' into PVD deposits to give a darker look.
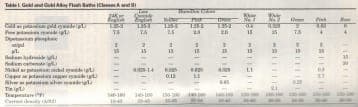
Hi Huan. The coloring of gold is an art more than a science, but Al Weisburg's "Gold Plating" chapter in the Metal Finishing Guidebook includes a "Table 1 "that will give you a start on formulations and operating conditions for different colors.
Regards,
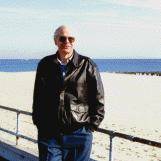
Ted Mooney, P.E.
Striving to live Aloha
finishing.com - Pine Beach, New Jersey
October 2013
Q. I'm a watch case manufacturer and also plater. We own PVD plant to coat ss 304 straps and brass watch cases using arc for TiN plating up to 0.5 or more micron and then followed by sputter 24k Gold plating (0.05 micron) to get gold finish.
I want to reduce the cost of PVD plating due to very high price in GOLD!
My question is can we do electroplating followed by TiN ? Or can we do gold electroplating after TiN and very thin layer or gold or nickel layer in PVD?
Any other suggestions are welcome
Thanks
Bhavin
Owner - Rajkot, Gujarat, India
February 23, 2012
A. Hi cousin Bhavin. It is possible to electroplate gold before TiN deposition by PVD. I think, but do not know for sure, that is is also possible to electroplate gold plating on top of a thin TiN layer. But it is probably more customary to apply the gold via PVD as you say you are doing.
Surely there is something wrong with your figures? 0.05 microns of gold cannot possibly be costly as it is incredibly thin. Light gauge aluminum foil is 320X thicker :-)
Regards,
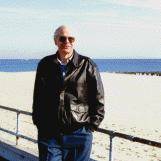
Ted Mooney, P.E.
Striving to live Aloha
finishing.com - Pine Beach, New Jersey
October 2013
Q. I'm an independent jewelry designer in NYC used to working with gold/silver. I've now created a line of costume jewelry in brass and would like to have them gold plated but have been quoted cost prohibitive prices for "micron plating". What I understand is called "flash plating" is at my price point (~$5-10 per piece) but doesn't last long.
Is there a coating I can apply that will extend the life of the gold plating (to at least 1 year but hopefully more) while maintaining a matte finish?
Hopefully either something I can apply myself (as a layman) or can be inexpensively be done by a professional in the NYC area?
Thanks and regards,
Jon
- New York
May 1, 2012
A. Hello Jon,
The jewelry industry has their own jargon especially when it comes to electroplating. Micron plating is not a considered a flash plate in Au plating. A micron is about 40 microinches give or take. Flash plating is conventionally anywhere from 3 to 10 microinches. You would be lucky to get 10 from most decorative Au platers. If the Au plating thickness was 1 micron and was alloyed for some hardness your products would last a year and even more. If you can't find a plater to put down that much Au, coatings are available that will not change the appearance of the final finish. Obviously your price to have the items plated / coated will be more expensive. Good Luck.
Engineering - Mesa, Arizona, USA
May 4, 2012
Q. I would like to know about the gold micron plating which can last at least one year. Can anybody suggest for the same? Thanking you.
Rohan
- Mumbai, India
July 25, 2012
Q. We are importing sterling jewelry charms and would like to offer gold plated silver charms as well. I have been discussing the plating with suppliers but it is difficult to get an actionable answer. I am looking for a suggestion to point me in the right direction with regard to wearability. There is obviously some body contact with the charms. I'd like to offer pieces that will not wear through to the silver - at least for several years of occasional wear. 1 micron of 24k gold has been suggested and that's affordable, the charms are small, but I have not been able to determine what I should buy. Any suggestions will be greatly appreciated. Thanks.
John Anthony- Phoenix, Arizona, USA
August 2, 2012
A. Hi, Rohan; Hi, John.
I'm not a jeweler, but since no answers have come so far, I'll provide my understanding, albeit not definitive answers.
Gold has been valued throughout history for its beauty, one aspect of which is that it doesn't tarnish or corrode. For that reason, no lacquer or topcoat is required to keep it bright, as is needed for copper or silver and other non-precious metals. So it has been customary to not topcoat gold or gold plating. That doesn't mean you can't put a clear topcoat on it; but it does mean that it may not be as well received, so you decide whether you will or you won't as a business decision depending upon how you want your jewelry perceived.
If you do topcoat it, with an electrophoretic lacquer for example, the thickness of the gold doesn't matter from a wear standpoint because it is underneath the clearcoat. If you don't clearcoat it, the gold itself will wear and must be thick enough to resist that wear for what you consider an acceptable life. 1 micron is probably sufficient to offer sufficient life for moderately priced jewelry if it sees little wear and no body contact. A ring would receive tremendous wear and body contact, a pin or brooch virtually no wear or body contact, a charm would probably depend on the exact design of the bracelet. Until I learn better myself, I don't think I'd do 1 micron without a clearcoat though if I wanted it to last several years.
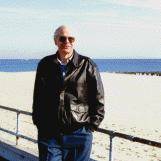
Ted Mooney, P.E.
Striving to live Aloha
finishing.com - Pine Beach, New Jersey
August 7, 2012
A. A trick used by some jewellers is to coat the articles with titanium nitride and then put down a thin coating of gold. The TiN is relatively rough, and the gold fills the cavities (or valleys) as well as the peaks. However, as the gold wears off the peaks, the TiN offers a hard and wear resistant point that protects the gold further down the valley.
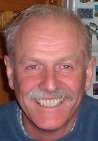
Trevor Crichton
R&D practical scientist
Chesham, Bucks, UK
August 29, 2012
Q1. In respect to jewellery items, what is the common understanding of the meaning of the term HARD GOLD PLATING (HGP)? What does HARD actually refer to?
Q2. Also, what are the recommendations for achieving HGP with very strong bonding (that is, won't wear off), when plating silver (925) and brass jewellery items? It seems that a barrier layer is required between the base material and the HGP layer, what is the consensus as to what layers be applied to each of 925 and brass items?
Q3. Does anyone have opinions on the use of Enthone additives and solutions? They seems a reputable supplier, or any other specific brands you have tried and have faith in?
Q4. Any views on the use of e-coating, as a final protective coat over the HGP? Is this necessary and recommended?
Many thanks for anyone sharing their views and experience.
Jewellery manufacturer employee - Brisbane, Queensland, Australia
January 31, 2013
A. Hello Robert,
Hard gold plating is a gold plating process whereas the plating solution contains gold salts (Potassium Gold Aurocyanide, conducting salts, buffer salts, and an alloy or brightener. Potassium citrate versions have been common for many years. The gold plating thickness is normally higher than standard "color gold flashes". Whatever the alloy is in conjunction with the gold metal concentration in the bath, determines the color and hardness of the plating deposit. pH and bath temperature play a role as well. Diffusion barrier coatings (between the substrate and the gold plating) vary. White bronze has become popular, palladium is also a good option, but more expensive. As you probably know, nickel had been the most widely used barrier plate in jewelry plating, but over the past 15 - 20 years usage of Nickel has been on a steep decline because of consumer allergies. There are reputable gold plating suppliers out there. This website can satisfy your search for a good supplier. Because jewelry is gold plated you have to expect the deposit to wear off over the years. The wear life will of course be dependent on the piece. Are you plating rings that will be worn daily, or necklaces that will be worn a few times a month. E-coating is an option to extend the wear life, but I am not familiar with possible drawbacks. Good Luck.
Process Engineer - Mesa, Arizona, USA
February 9, 2013
Q. Hello, please please I need some help!
I'm doing the hardware metal for my handbags (logo, tags, o rings, metal plate) in China. I got the samples on Friday and they looked pretty good to my surprise. The only problem I have is the gold color. I asked them to do a 14k gold plating (they say they use IP plating which is better and more durable than micron plating, is this true?) and when I compared the pieces to the metal hardware that were done here in the USA, the gold color is a little bit lighter then the ones made in USA. I wonder why could this be?
Also, another thing that got to my attention. When I did the metal hardware here in the USA, the people that did it told me that to have the engraving on the metal (like the name of my brand that is engraved on the metal) to polished inside is really hard, so that's why it looked rough on the inside, not polished. But the hardware from China looks amazing on the inside! is completely polished and clean. Does anybody knows why is there such a difference? if there is something that this people in China might be doing differently? And if this is the case will that be compromising the quality of my metal hardware?
Thanks so much
- Snowmass Village, Colorado, USA
February 6, 2013
A. Hi Isabella. 14K gold is 10/24 non-gold, and the color depends on those other 10 parts. "Gold coloring" is both an art form and a trade secret for the fastidious: it's not easy to get consistent color, and quite difficult to specify it -- but you can study that topic in plating textbooks. "Gold Plating Technology" has quite a bit of info on gold coloring.
I didn't understand your engraving description and problem, sorry; but is it possible that the engraving was done after the plating here, and before the plating there? Also, your Chinese supplier is doing "ion plating" -- but that's a method, like "electroplating" is a method; it may be gold plating but it may not be. Are you sure you specified "gold plating" rather than just "gold color"? Micron plating is neither a method nor a material; it's a gold plating thickness of one micron. I don't think you are getting from China what you thought you were asking for; but if what you actually want is only the appearance, and you're happy with the appearance, that's probably okay.
This is a forum of international camaraderie, so we naturally try to not stand in judgement of anyone's outsourcing choices. Still, a problem is that we receive hacking attempts every hour of every day from China, and so many thousands of pieces of spam from China every week, that we often must block large swaths of IP addresses from China, and in so doing we may inadvertently block a helpful response from China. So you probably can't expect much help from China. And you really can't expect domestic and other platers to spend their time for free here helping you cut them out of the loop. That would be like going to a Chevy dealer and expecting the salesperson to patiently spend her time helping you choose between a Honda and a Toyota. That's probably why you've received no responses in a couple of months. But best of luck.
Regards,
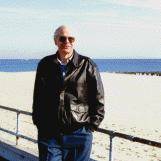
Ted Mooney, P.E.
Striving to live Aloha
finishing.com - Pine Beach, New Jersey
April 25, 2013
April 25, 2013
Q. Regarding Plating Cost and Plating Thickness recommendation
Hello,
I am talking to manufacturers in China about fashion jewelry, mainly ear studs, chains, pendants and rings. My market is very price sensitive and I need to consider cost versus benefit closely.
I understand ear studs have less exposure to sweat than rings.
Can anybody give a recommendation for each of those categories - chains worn around the neck, ear studs, pendants and rings - how many microns or fractions thereof you would recommend so that the plating holds for 0.5/1/1.5/2 years under normal usage in a table format for gold, rhodium and black colour plating ?
In addition, I was wondering what the actual cost differential for the plating factory is. The issue I have that I do not know how big the square centimeter surface of a ear stud (sizes 3 to 10 mm), ring, chain etc is depending on common sizes.
For example a table that would tell me that the average 4 mm/5 mm/6 mm ear stud costs x US$ per 0.1 micron of gold/rhodium plating.
I would like to use this when negotiating prices with my manufacturers.
Any help would be highly appreciated.
Another question I am pondering with is whether there are health concerns if the plating wears off and brass or zinc alloy is revealed and gets direct skin contact. Firstly, I cannot even find what exactly "zinc alloy" is versus brass. Are there any EU rules under REACH that mandate a specific minimum plating thickness in microns?
Many thanks again,
Daniel
- Guangzhou, China
A. It isn't necessary to know all the costs involved in the manufacturing of the jewelry you are seeking to buy in order to get the best possible price but you will need detailed designs and exact specifications that you can give to multiple manufacturers for quotes. Based on some of your questions I'm guessing you have little experience and you should hire a consultant to help you write up the specifications you will want to use. A word of caution: we regularly receive jewelry items through our customers that have been gold plated in China and do not meet the specifications.
Neil BellAlbuquerque, New Mexico
April 30, 2013
(You're on the 1st page of this topic) Next page >
Q, A, or Comment on THIS thread -or- Start a NEW Thread