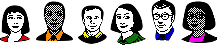
Metal finishing Q&As since 1989
-----
Hard copper over sleeve
I try to do hard copper on soft copper coated Nickel sleeve. If I do hard copper on a roll of Mild steel with Nickel strike and soft copper, I get uniform hardness from hard copper bath. If I put sleeve of Nickel with soft copper on a chrome plated roller, I get variations in hardness. I use same current density, same temperature and dosing of grain refining in both cases. What could be cause of difference in hardness? What can be solution?
Kaushik Magiawalaplating shop employee - Gandhinagar, India
2006
First of two simultaneous responses -- 2006
This is a guess! You are testing with a hardness tester of the rockwell type, rather than using a microhardness tester.
The variability is probably caused by different thickness of nickel, which is probably much harder than even the hard copper. The nickel strike is so thin that it has zero effect on your "hardness" .
I think that you have a variability in the nickel thickness on the same part, with it being thicker on the ends than the middle and the parts in the center of the rack have less nickel than those on the outer edges. Cut and mount a few parts and look for thickness differences.
- Navarre, Florida
Second of two simultaneous responses --
Maybe if you give more details. It's not easy to understand exactly what you are doing. When do you put the roller or sleeve, before or after plating. How are you measuring harness? Is the current and temperature the same?
Guillermo MarrufoMonterrey, NL, Mexico
2006
2006
For James Watts
The Nickel thickness is 178 micron (0.007 inch ) and is uniform. It is verified. The hardness is measured by portable instrument (calibrated) after hard copper plating.
For Marrufo
The C.D. and Temp are same.
The plating is done on a Nickel-copper sleeve which is mounted on a chrome surface.
The recent observation showed pin holes in chrome surface. Could that be high / low current density areas?
If I want to check if chrome is active or not before mounting Nickel sleeve, how would I measure it?
plating shop employee - Gandhinagar, India
Q, A, or Comment on THIS thread -or- Start a NEW Thread