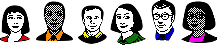
Metal finishing Q&As since 1989
-----
Alternatives to Phosphating

Q. Dear Sir,
We are an automotive clutch manufacturer and do zinc phosphating as anti-rust coating for hardened CR steel parts used therein.
As Zinc phosphating is dull in appearance, we need to know alternate to the same.
Employee - Nashik, Maharashtra
May 27, 2022
⇩ Related postings, oldest first ⇩
Q. Sir,
We are dealing with INJECTION MOULDING MACHINE manufacturing & we have our own paint shops in which we carry out painting -mainly Poly Urethane based.We would like to know about the alternate methods of degreasing process/phosphoric coating prior before primering on our product.
Quality Assurance engineer - Chennai, Tamilnadu, INDIA
2006
"Phosphating & Metal Pretreatment"
by D.B. Freeman
on
AbeBooks
or
eBay
or
Amazon
(affil links)
A. This is at least the fourth request from India this month asking how parts can be painted without a phosphate pretreatment--but no one is saying why everyone suddenly wants to do that. Is there a new restriction on phosphates in wastewater? Is someone making the rounds claiming that phosphating isn't necessary?
Please tell us why you would want to get away from the pretreatment that has proven itself around the world for decades as by far the most cost-effective & robust treatment in tens of thousands of applications, Rejith. Thanks!
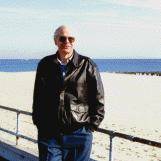
Ted Mooney, P.E.
Striving to live Aloha
finishing.com - Pine Beach, New Jersey
![]() |
2006 Dear sir, - Chennai, Tamilnadu, India A. There are lots of alternative treatments, many of which are used by my employer. Most are OK but none are as good as Zinc Phosphate. If you use no treatment count on having adhesion problems. Ronald ZeemanCoil Coating - Brampton, ON, Canada 2006 2006 A. Dear Mr. Rejith, - CHENNAI, TAMIL NADU, INDIA |
"Phosphating of Metals"
by Werner Rausch
on
AbeBooks
or
eBay
or
Amazon
(affil links)
A. Rejith,
1). If you are painting and plating, you might consider doing the painting first. The painting will act as a mask, and the chrome plating will be shiny because it will follow phosphating rather than preceding it.
2). Phosphating is a pre-paint treatment, not usually meant to be a final finish; I don't really understand the corrosion problems you are mentioning.
3). Please describe this 'suffocating'. I am not aware of any health related problems for phosphating when the usual common sense safety measures are in effect. Similarly, I know of no environmental problems associated with phosphating except perhaps the release of phosphate-rich rinse water; and even in that case, dry-in-place phosphate coating systems exist. Good luck.
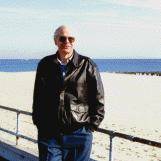
Ted Mooney, P.E.
Striving to live Aloha
finishing.com - Pine Beach, New Jersey
2006
A. Nanoceramic
One of the best surface technologies that can replace phosphating.
Best Regards,
specialist - Serbia, Belgarde
2006
2006
Dear Sir,
There are water borne polymers ranging from epoxies to polyurethanes with which you could eliminate phosphating process. However, you need to remove grease and rust(in case the component is rusted), rinse twice in DM water, dip in water borne polymer bath(from 3% to 5% concentration. Allow an interval of 20 minutes. Then, proceed for further top coat by powder coating or liquid top coat. If not you can leave the component at least for a week.
HOPE THIS WOULD RESOLVE YOU ISSUE.
Thanks,
- Bangalore, Karnataka, India
Q. We are currently processing cold forging slugs with Zinc Phosphate and due to its cumbersome process and hazards to environment, we wish to upgrade our system.
Can anyone suggest or be of a help in providing information of an alternative to the Zinc Phosphate process? Is Zirconisation the appropriate process? If so, please can you refer any supplier in India?
Please guide with any other suggestion.
Regards.
- Belgavi, Karnataka, India.
July 16, 2016
Picture taken July 2012: Outside on my saltwater lagoon, 365 days a year, after 13 years of zero maintenance. And it's still outside, still being used in September 2016.
"Phosphating of Metals"
by Guy Lorin
on
AbeBooks
or
Amazon
(affil links)
opinion! Hi Vijay. I remember reading Rachel Carson's "Silent Spring" decades ago and thinking "How could we all have been so blithely unaware?". But as I continue to see the penny wise/pound foolish "environmentalism" of trying to eliminate phosphating, with the lack of sustainability which its elimination has brought, the feeling of deja vu is overwhelming :-)
I bought an expanded metal patio set 17+ years ago that stayed outdoors year 'round on our saltwater lagoon for 13+ years, then was submerged under Superstorm Sandy for a few weeks, and has now been outdoors at my new home for 4+ more years. We're still using it because it was zinc phosphated, electrocoated, and powder coated. In the intervening years I have bought countless outdoor metal items, replacing them time & again & again, with the consequent need for re-mining ore, re-smelting steel, re-fabricating, re-finishing, re-packaging, re-shipping, re-retailing, and re-landfilling, and all the transportation between each of those steps :-)
What on earth is wrong with society that we focus on the ounce of phosphate not the tons of unsustainable waste which eliminating the phosphating is directly producing? By all means look into recent advances in transition metals coating [TMC] processes, but consider them only if they offer proven 20-year+ performance, and only if you know every material in the effluent and you are completely convinced that these materials have absolutely no effect on the environment. We may be better off with the devil we know :-)
Luck and Regards,
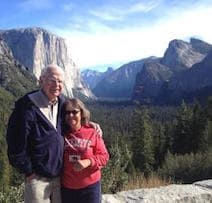
Ted Mooney, P.E. RET
Striving to live Aloha
finishing.com - Pine Beach, New Jersey
September 2016
P.S. Our expanded metal outdoor table and chairs are still going strong here in 2022 after 23 years of the most corrosive environmental conditions imaginable. And I still say that trying to eliminate phosphating is an environmental travesty :-)
Q, A, or Comment on THIS thread -or- Start a NEW Thread