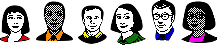
world gathers for metal finishing
Q&As since 1989
-----
Black zinc plating vs. Black oxiding

Q. I need to prime bolts without having to clean off any oil. I need to prime them so I can cover the bolt head with Flock, but our customer wants the bolt to be black in color in case any of the black flock wears off it will still appear black.
I have been told that black oxide means "Black oxide and oil" which makes this not a good option as we are not to clean the oil off.
I have been told that Black Thermal Oxide is the way to go since zinc coatings are not available in black.
My question: Does the Thermal process not include oil? Can I prime these without having to wipe them clean like I can do with a zinc coated bolt?
Any guidance is appreciated.
Thank You.
Darrin June
Engineer - Lapeer, Michigan
November 21, 2022
A. Hi Darren. You replied to thread 14189, "Thermal vs Chemical Black Oxide", but we moved your posting here because we think it fits better. If you have been successful priming zinc plated bolts (which include a clear chromate), you should be equally successful priming zinc plated bolts that have received zinc plating and a black chromate instead. These 'black zinc' bolts should be readily available.
Luck & Regards,
Ted Mooney, P.E. RET
Striving to live Aloha
finishing.com - Pine Beach, New Jersey
⇩ Closely related postings, oldest first ⇩
Q. WHAT IS THE MAJOR DIFFERENCE BETWEEN BLACK OXIDE AND BLACK ZINC?
THANK YOU,
JARED MORIN
Limerick, Maine
2003
A. Hi Jared. Black oxide is an extremely thin (millionths of an inch) oxidation product created on the surface of a steel part; it has almost no corrosion resistance but it is attractive and does not affect the dimensions of parts; so it's used on things like bored sprockets, gears, and couplings, where dimensions are critical, and on things that are lovingly maintained and regularly oiled like rifles and shotguns.
Black zinc is zinc plating (say .0002" thick or more) followed by a black chromate conversion coating. You get the sacrificial corrosion protection of zinc, plus a nice appearance, but it does affect the dimensions enough to be a problem on very tight fitting parts. Luck and regards,
Ted Mooney, P.E.
Striving to live Aloha
finishing.com - Pine Beach, New Jersey
Q. I have a plain carbon steel part that is exposed to a mild corrosive climate. It needs to retain its magnetic properties and must keep the post machining tolerance (0.001 thou). I know that black oxide coating will work well for this application but can I also use a black zinc coating?
I need help fast, thanks
Timothy Vandermeiden
Calgary, AB, Canada
2006
A. Hello Timothy. Black zinc plating is significantly more corrosion resistant but it does add thickness. The minimum thickness would be 2 ten thousandths of an inch and, due to the irregularity of the thickness, it could be 5 or 6 ten thousandths in some areas depending on the shape of the part. But zinc plating is done even on small fine-thread components, and a tolerance of .001" doesn't sound like a problem pending a review of the specific part. Good luck.
Ted Mooney, P.E.
Striving to live Aloha
finishing.com - Pine Beach, New Jersey
Differences between black ox and black zinc trivalent
Q. I have a customer that I am looking to switch from a black oxide coated screw to a black zinc trivalent, but they did to see some sort of data sheet that shows the difference between the 2 finishes. Also, they are asking if black zinc trivalent will react negatively with plastic, as this is the material these screws are being placed into. Can someone point me in the right direction to locate some information?
best regards,
Gary Davis
sales person for a fastener distributor - Norcross, Georgia, USA
2007
A. Black oxide has little if any corrosion resistance and the only protection is provided by the oil that is on it. Black trivalent chrome is in reality black zinc plating so you have lots more corrosion protection and very little chance for reaction with plastic. If anything to watch for it would be the build-up of the zinc plating - it's substantiallly more than black oxide which is nearly nil. Also, my experience with black trivalents products is that by themselves they are blotchy and not very eye appealing. To overcome this applicators of black trivalent typically apply an organic sealer - wax or lacquer based - which if you have electrical requirements (not likely if this is going into plastic) you've now lost conductivity. Bottom line - black trivalent is better and you should charge more! At least make your customer aware of upgrading their value without a cost impact.
Milt Stevenson, Jr.
Syracuse, New York
Q. Hi. As a mechatronics engineer, mainly with electrical background rather than mechanical, I am stuck over a problem of coating. The engineering standards of my company support phosphate & oil coating on screws, but the supplier has been using zinc coating for the same part, saying phosphate coating is not environmentally friendly and the government does not support it. Now, I want to have comparisons drawn round off on a conclusion.
Troy Costa
Pune, Maharstra, India
November 21, 2012
A. Hi Troy. Although the government probably doesn't want excessive phosphates in the effluent water from metal finishing shops, it sounds like an exaggeration for your supplier to claim that "the government does not support phosphate coating". Phosphate coating is just about the only acceptable pretreatment for painting ... and for powder coating ... and for applying secondary coatings on top of galvanizing ... and as a break-in coating for the countless moving parts inside automobile engines ... and as a rust converter [on eBay or Amazon] such that consumers can maintain old equipment rather than throw them away. A government which doesn't support phosphating would be a government with zero respect for sustainability.
But depending on the function of the screws in question, zinc plating may be perfectly satisfactory, and might well be better than phosphate and oil! Probably as a general rule, if part of the screw is painted or it sits in oil or grease, the phosphate and oil is better, whereas if the screw is exposed to the air, the zinc plating may be better. Again, only a very general guideline. Good luck.
Regards,
Ted Mooney, P.E.
Striving to live Aloha
finishing.com - Pine Beach, New Jersey
A. Hi Troy,
We do phosphate coatings on screws, and all the products we use are RoHS compliant. If he does not do phosphate because of environmental concerns, the sealer he can apply may have hexavalent chrome. There are many sealers without hexavalent chrome, environmentally friendly, but they are expensive (but not as expensive as a black zinc trivalent conversion coating as he applies).
If you ask me, if you ask for a zinc phosphate coating, you can have that without any environmental problem. There are many vendors offering these products. Black zinc is (if the conversion coating does not have hexavalent chrome) also environmentally friendly, but also more expensive.
Hope it does answer your question! Regards!
Daniel Montañés
Cañuelas, Buenos Aires, Argentina
![]() |
opinion! Hi Troy. That Chinese shortsightedness is very depressing, but it does explain the shiploads of worthless painted Chinese steel crap for sale in every big box store :-( |
Q. Hi,
I have several questions I want to verify regarding the black oxide. I have a set of front rotors and currently using black oxide. After several days, it starts rusting in comparison to black zinc coating.
I'm testing which coating can last longer. Can you give me any advise for the black oxide if possible? Is there anyway that we can hold up the black oxide to prevent the rust?
Daniel Ip
Toronto, Canada
September 21, 2013
A. Hi Daniel. Your findings verify exactly what this thread tells you. Zinc plating offers sacrificial protection against corrosion and black oxide does not. Black oxide has no rust resistance except its wax or oil. In a somewhat corrosive shop environment I have seen it rust horribly within 45 minutes when the oil was stripped and not replaced in that time period.
Regards,
Ted Mooney, P.E.
Striving to live Aloha
finishing.com - Pine Beach, New Jersey
Q. Hi,
Is it possible to identify the difference among black oxide, black zinc and phosphate coated bolts just by visual inspection?
VIMAL RAJU
- India, TAMILNADU, COIMBATORE
October 19, 2014
A. Hi, Vimal. People are forever hard at work trying to make things look like something else. If you were to review this whole forum you'd find hundreds of threads of this form: "I want my thingamajig to look like it's made of Xxxxxx but I actually want to make it out of Yyyyyy -- how do I make Yyyyyy look like Xxxxxx?". Although the finishes you named might tend to look slightly different, and some experienced platers could probably get the identification right 75 or even 90% of the time, after 50+ years in the finishing industry I personally have zero faith in visual identification of finishes.
Luck and Regards,
Ted Mooney, P.E.
Striving to live Aloha
finishing.com - Pine Beach, New Jersey
Recommended finish for A490M Type 3 bolts?
Q. What is the accurate difference between plain finished and black finished? And what is the recommended finish especially for bolts ASTM A490M TYPE 3?
Farid Nagy
Cairo, Egypt
November 20, 2014
A. Hi Farid. Unfortunately, we can't take a loose, slang term like "plain finished" or "black finished" and tighten it up to something precise. Sorry.
I believe that ASTM A490M says that these high strength structural bolts cannot be galvanized, electroplated or mechanically plated, but you must check the spec. to make sure. That probably limits you to a zinc-rich dip-spin coating. I believe TYPE 3 is Weathering Steel (Corten), which might mean that unfinished is the suggested finish anyway.
Please try your best to explain your own situation, rather than keeping it abstract. Thanks!
Regards,
Ted Mooney, P.E.
Striving to live Aloha
finishing.com - Pine Beach, New Jersey
Inspecting selective black zinc plating?
Q. Hi,
Is there a way to visually check or guidelines for partial plating on steel for incoming inspection on black zinc coating?
Thank you
Andy Rada
September 30, 2015
A. Hi Andy. What exactly does the spec referenced in the purchase order call for in this regard? The plating spec is your primary guideline for incoming inspection, and it often even instructs in fine detail about lot sizes & sample sizes, etc. Trying to inspect from a different starting point will only lead to contract disputes :-)
Good luck!
Regards,
Ted Mooney, P.E. RET
Striving to live Aloha
finishing.com - Pine Beach, New Jersey
Q. I want to ask about the abrasion resistance of Zn Plating? I mean if some heavy thing slides over it, can the protective layer be damaged or otherwise?
FARHAN SIDDIQUI
Islamabad Pakistan
December 16, 2016
A. Hi Farhan. The overwhelming majority of nuts & bolts in the world are zinc plated. The adhesion is fine for this tough service. Further, zinc is cathodic to steel, so it can largely continue to serve its corrosion protection mission even if scratched.
But the black coloration is chromate conversion, which is thinner and less rugged than the zinc plating. I would expect the black finish to be marred from certain heavy things repeatedly sliding over it. Please describe your situation as much as you can because our ability to help with abstract questions is limited :-)
Regards,
Ted Mooney, P.E. RET
Striving to live Aloha
finishing.com - Pine Beach, New Jersey
Aesthetic standards to get matching parts from multiple vendors
Q. Hi, I am working in a small company and we usually ask our vendors to make specific coatings and finishes for the parts that they make for us. For example we just say "Black Zinc" or "Black Oxide". But since we have different vendors the products come in different colors and shapes. So I want to make a standard way to communicate with vendors to have identical finishes. Our parts are usually made of steel or aluminum and right now aesthetic is more important than anything for us.
What sources should I use to make such an internal standard? ASTM or ISO standard or anything else? Is there any general code for colors of these coatings and finishes?
Thanks for your help.
Sam bahremand
Irvine, California, United States
March 30, 2017
A. Hi Sam. Most plating specifications are concerned with the functionality of the plating more than the aesthetic requirements, but check the spec first. If you want consistent appearance from vendor to vendor, the only practical way to do it that I am aware of is with sample boards: "this component is ideal" "this component is satisfactory", "this component is too shiny", "this component is too matte", "this component is too light", "this component is too dark".
But sample boards are something that a lot of professionals scoff at for a few good reasons --
- The samples age over time, and few buyers will undertake the major effort to keep them current.
- How do you get Shop B to agree to let you use Shop A's samples in the sample board instead of theirs?
- Different inspectors will still pass/fail different parts; it's still not 100% objective.
I think I understand what you want, but it honestly doesn't work quite that way :-)
Certainly you can tighten up your purchasing a little by finding ASTM, ISO or other specs, but in the end either you rely on the technical expertise of your plating shop or your own (or your consultant's).
Consistency is possible, Apple achieves it on millions of iPhones. It may be that the best path forward is to pick your favored vendor, work with them on the sample board, and only accept work from other vendors if they agree to live by the sample board. Second opinions welcomed!
Regards,
Ted Mooney, P.E. RET
Striving to live Aloha
finishing.com - Pine Beach, New Jersey
Q. Hi,
I need to specify black oxide coating on a few of my parts but I don't know how much thickness and salt spray life need to be specified on it.
The machine has to run in a muddy and dusty field.
Please support.
Regards
Deepak Bathla
Chandigarh, Punjab, India
June 13, 2017
A. Hi Deepak. Black oxide has very poor corrosion resistance, but if you're sure you want black oxide rather than black zinc plating or black phosphating or black chrome, there are many threads on this site which are more informative about the process details than this one. But you don't specify thickness for black oxide coatings (they are almost indetectably thin, although salt spray testing might be appropriate. Here are some typical specs: ISO 11408, AMS2485, MIL-DTL-13924
[on DLA]. Please pick one and see if it covers your needs.
Are there reasons which make you feel black oxide is appropriate for these parts and this application? Please explain the parts and your situation because in that way can people best help you, and your inquiry will attract the most interest.
Regards,
Ted Mooney, P.E. RET
Striving to live Aloha
finishing.com - Pine Beach, New Jersey
Q. Hi All,
Considering Black Zing plating for a clamp mount design for a task light. Wondering how much control you get over gloss levels with this process? Is it possible to have a semi-matte finish, or are we limited to glossy?
Thanks in advance
sergio silva
Brokklyn, New York, USA
November 27, 2017
A. Hi Sergio,
You don't control the gloss of the zinc plating process, as the only way to get good thickness and adherence is having a glossy zinc layer. The chromate could modify this but not so much to take into account.
If you want a semi-matte finish you could do some dip-spin paint over zinc, a little more expensive but I think far more superior.
Hope you get what you want! Best regards,
Daniel Montañés
Cañuelas, Buenos Aires, Argentina
Q. We are building a wooden bench in our back yard and want a black finish on the bolts/screws we use to hold the bench together. What would you recommend for the type of bolts/screws with what type of black finish to get the longest life?
Tom Murray
Portland, Oregon, USA
January 2, 2018
A. Hi Tom. Hardware stores and the labeling on screw packages don't generally give you enough information to determine the thickness & type of plating and coating, and it's not customary to try to buy hardware for a small home project to your own engineering specifications as the time and cost involved are out of proportion. I'd probably just look for deck screws in a satisfactory shade. I've seen them in olive green, gray, and black -- and they'll be plenty corrosion resistant. Good luck.
Regards,
Ted Mooney, P.E. RET
Striving to live Aloha
finishing.com - Pine Beach, New Jersey
Q. Can someone share with me the differences of zinc black and black oxide?
Catherine Ang
Singapore
February 13, 2018
A. Black zinc is almost always zinc electroplate followed by a black conversion coating. In the old days this was a hexavalent chromate conversion coating incorporating a small amount of silver. Today, with platers leaning toward trivalent passivates, there are a variety of formulations. The word on the street I hear is that they are not as black or reliable as prior art technology. Black conversion coatings over zinc-iron, though, have been successful. Since the underlying coating is zinc, sacrificial protection is provided. And the passivate provides inhibitive protection.
Black oxide is a conversion treatment for iron. (It converts the iron to magnetite (Fe3O4)). It is almost always done by immersing and iron or steel article in a very hot, very alkaline, very strong oxidizing agent. It looks great, but provides no corrosion protection of any kind. Post treatment with a mineral oil (or the equivalent) provides a modicum of corrosion protection and a little gloss. The bottom line is this: if it's going outdoors, go with black zinc; if it's going indoors, black oxide should be fine.
Tom Rochester
CTO - Jackson, Michigan, USA
Plating Systems & Technologies, Inc.
Q. Hello all, I have a part that is currently black oxide for a finish against corrosion. Our supplier has indicated to change to zinc plate for better corrosion resistance, based on this thread that is the correct thing to do. However, some of our units are used in an oxygen environment, is there any concern with compatibility with black zinc plating and oxygen?
Carson Krajco
Denver, Colorado, USA
October 12, 2018
A. Hi Carson. I've never heard of such an issue but, sorry, I've never researched it either.
Luck & Regards,
Ted Mooney, P.E. RET
Striving to live Aloha
finishing.com - Pine Beach, New Jersey
Q. I require a black finish for some small mild steel plate components that will be handled by customers. I require mild corrosion resistance as well as a black finish. I have been recommended a Black oxide finish and a Zinc Blacking process. Black oxiding is cheaper, but does it leave a residue on fingers? This would be undesirable.
Robert Sedgeman
Gloucester, Gloucestershire, UK
April 15, 2019
A. Hi Robert. In my limited experience cold blackening (selenium sulfide based processes) are usually smutty, but real hot black oxide significantly less so. "Small mild steel plate components that will be handled by customers" might be better with black zinc plating though, because it is more corrosion resistant.
Regards,
Ted Mooney, P.E. RET
Striving to live Aloha
finishing.com - Pine Beach, New Jersey
Q. Hello,
My company manufactures off-road truck bumpers and we're looking for a black plating process for ordinary nuts, bolts etc that will be a deep black that is corrosion and UV resistant. I've read that black zinc will change colors over time. Is there a good option for black hardware that is constantly exposed to the elements?
Thanks in advance,
Jake
Jake Holmes
Springdale Arkansas
October 3, 2019
A. Hi Jake. Some black chromates are silver based and will indeed turn green or other colors over time and after UV exposure. It is my understanding, but you would need to back it up by talking to a supplier, that if you do zinc-iron plating and then black chromate conversion coat it, that the iron content makes stable black chromating possible.
Even still, black zinc or black zinc-iron may not be quite what you're looking for if you want a truly decorative long term finish. Black chrome plating is a fully decorative finish but may be prohibitively expensive.
When I picture what "off road" means to me, black zinc-iron sounds fully acceptable, but to some people the tiniest paint scratch on their "Trail Rated" Grand Cherokee would be considered a tragedy, so it may not be decorative enough for them :-)
Regards,
Ted Mooney, P.E. RET
Striving to live Aloha
finishing.com - Pine Beach, New Jersey
Q. Hi all, I am building a low quantity racing motorcycle from scratch. You can find some information at www.cosentinoengineering.com/blog.
As you can imagine, there is a large amount of fasteners of every size (M2-M30) on a motorcycle. Because of this, I have a pile of bolts with a variety of finishes, some yellowish, some silverish, and some black oxide. The majority are alloy steel and some are stainless. Some are purchased new and some are modified from an existing OEM part sourced from a suitable bike.
I would like them all to have a consistent black finish. The bike will be raced in the rain so black zinc sounds like a suitable process. Is this the case? Is it possible to have all of this hardware stripped (if needed) and coated without compromising the fastener strength?
Thanks for any assistance.
Regards,
Chris
Chris Cosentino
Jersey City, New Jersey
October 20, 2020
A. Hi Chris. Yes it is possible to strip all of the existing plating, and yes it is possible to zinc-iron plate it and black chromate it. And if the hardware is properly baked for hydrogen relief at the necessary stages it is possible to do most of it without compromising its strength. But there are some specs for very high strength fasteners (see the reference to ASTM A490M above, for example) that might forbid stripping or plating.
Luck & Regards,
Ted Mooney, P.E. RET
Striving to live Aloha
finishing.com - Pine Beach, New Jersey

Q, A, or Comment on THIS thread -or- Start a NEW Thread