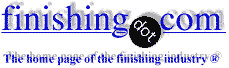
-----
Citric vs. Nitric Acid Passivation of Stainless Steel
Current question and answers:
Q. Can anyone tell me if there would be an effect of passivating parts with nitric acid after they have been through citric acid passivation?
The material is 304SS. I am curious if this would create a film or effect surface roughness?
Background is that these parts get citric acid passivated by the supplier. We then use nitric acid for deburring of our laser cutting process and to remove the oxide created during cutting. Our customer has described the issue as increased friction in the ID of the tubing.
- Dayton Ohio
January 22, 2021
A. Ryan,
There's no problem with passivating multiple times. citric acid passivation removes iron from the surface, nitric acid passivation removes iron from the surface plus a small amount of the chromium, nickel, and other metals.
The "film" created is the iron-depleted chromium layer. The chemical itself is not meant to remain on the surface. Surface finish is generally not affected by passivation, though this can vary depending on the grade of stainless, the type of bath, and the soak time.
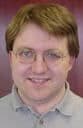
Ray Kremer
Stellar Solutions, Inc.

McHenry, Illinois
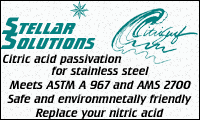
January 26, 2021
A. It is not uncommon to passivate more then once during processing stainless steel parts and you are doing the right thing by re-passivating after laser cutting since you are voiding the passivation once you laser cut the part but if the laser cutting process is leaving any slag behind nitric acid alone wouldn't remove it by it self which may cause the fiction to increase. You may have to go to chemical deburring process that removes material or more aggressive to move the laser slag if it is attached well.
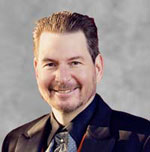
Mark Battles
Plymouth, Minnesota
February 1, 2021
A. Passivation creates a very thin film either you used Citric or Nitric. This film is the passive layer and is very very thin. Both processes don't affect the surface finish of the part.
Why does your supplier perform Citric Passivation if there will be further metal machining?
I would suggest you perform all machining or laser cutting before any finishing processes. Thermal burrs (slag) and oxide layer will sometimes appear after laser cutting. You need to determine which type of burr you have. Thermal burrs can be removed by vibratory deburring while oxide layer can be removed by electro-chemical deburring (ECD). You just need to determine how much burr needs to be removed. After all these processes, perform the passivation. Inspection is recommended between deburring and passivation and also after passivation, concentrating on the surface finish requirement of your customer.
- Moorpark, California
February 11, 2021
⇩ Related postings, oldest first ⇩
Q. My work is considering building its own passivation plant for in house use. We are still doing research on whether to use Nitric or citric acid bath. Your opinions will be be appreciated.
Thanks,
Anthony Samaniego- Edison, New Jersey
2001
A. Anthony,
Nitric acid is far superior to citric acid in relation to introducing a passive film on the surface of stainless steel parts. Nitric acid is so effective because of it's primary mode of action, that is, oxidation of the surface thereby removing iron radicals, etc as present in for example heat generated oxides. This effectively removes risk of corrosion of the part as well as introducing the passive layer. citric acid works more likely by super-cleaning the surface of the steel allowing spontaneous generation of the passive layer. This however will not remove radicals from the surface and therefore the steel is prone to corrosion further down the line. I do not know of any job-shops that condone the use of citric acid in passivation. Chances are you are looking to use citric because it is more environmentally friendly than nitric. However, the quality of the finished part will be far inferior.
John Martyn- Ireland
2001
A. John,
While I agree with you in many circumstances pertaining to nitric acid corrosion results over citric, I have found in my humidity cabinet several cases where certain alloy's resist corrosion is longer with citric passivate than same parts with nitric. Also in special tests requiring confirmation of sulfide removal (303 SS) hands down to citric. While poor at removing heat scales (better addressed in ASTM A380 ) citric passivate has won the merits of an ASTM designation...ASTM A967.
Jon Quirt- Fridley, Minnesota
2001
A. Anthony:
With all due respect to John, he is very wrong. citric acid is being used by MANY job shops and thousands of in house operations due to the INCREASED corrosion resistance obtained. citric acid , when formulated correctly produces higher chrome oxide ratios than nitric acid, and has many other advantages in safety, cost and environmental friendliness. Many customers have data showing the improvement in performance. It is MUCH more than just a cleaner. It removes more iron from the surface than nitric acid.
adv.
Please contact us or go to our web page if you need further information.
Regards,
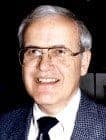

Lee Kremer
Stellar Solutions, Inc.

McHenry, Illinois
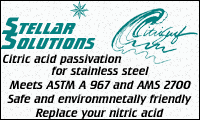
2001
Lee,
I am only knowledgeable of the job-shops in my neck of the woods, i.e. Britain and Ireland. Chemically, I do not see how citric acid could be better than nitric acid. Maybe you could explain the technicalities of the citric passivation process to me, what chemical processes are involved and what real data you have to back up your results. As a chemical engineer, I am very interested in obtaining environmentally friendly chemicals to use in my passivation process so obviously this would be an interesting change.
John Martyn- Ireland
2001
Q. Gentlemen,
Thank you for sharing your views. I am nearly convinced that citric acid would do as good a job as nitric acid. I did some inquiries from other passivation plant and they mentioned something about it not being as easily disposed of as claimed (eg. cannot mixed with regular waste stream). Thanks again for your help.
Anthony Samaniego [returning]- Edison, New Jersey
2001
2001
A. Anthony & John:
citric acid formulations can be very easily disposed of in the waste stream as opposed to nitric acid systems. However, it cannot be put carelessly into a heavy metal precipitation system. There are easy and economical ways to dispose of rinse water by putting it to drain, since it will not normally contain any significant heavy metals.
If you put the waste into a precipitation system it must be treated first. There are simple ways to do this.
citric acid works much better than nitric acid for passivation because it prefers the iron over chromium and nickel. Therefore, it reaches a steady state at a much higher chromium content on the surface, producing an excellent chromium oxide layer.
There is data from hundreds of companies in the U.S. and around the world (in addition to our data) that proves the superiority of citric formulations.
adv.
If you contact me directly I will share some of this data with you. It obviously cannot be done in this forum. Some of the data can be found on our web page.
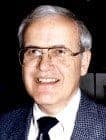

Lee Kremer
Stellar Solutions, Inc.

McHenry, Illinois
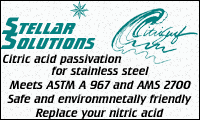
A. The Reduction Potential between CH3CO2H (from the citric acid ) and the Cr3+ is far more powerful when compared to NO3-. Even the dissociation capacity from HNO3 being greater than citric acid , this property of the solution has less effect on the range of the passive layer.
That's my theory...
- Florianópolis, SC, Brazil
October 18, 2009
Multiple threads merged: please forgive chronology errors and repetition 🙂
Q. We have been using both Nitric acid with Sodium Dichromate and citric acid for our passivation process for 440C. It seems that Nitric acid passivation is better than citric acid passivation. We did an EDS and XPS test on samples for both types of passivation. Chrome oxide which is 80% to 90% forms the passive layer is thicker by 25% on samples that undergone Nitric passivation than the samples that undergone Citric passivation. This may be the result of the oxidizing effect of Nitric acid and Sodium Dichromate while on the other hand citric acid can only do removal of free iron on the surface and very minimal oxidizing effect. What we want to do is make citric acid passivation as effective as Nitric acid passivation. Does anybody have any idea how we can improve citric acid passivation?
Leo Monsada- Chatsworth, California, USA
2006
A. I agree that Citric does a fine job of removing the free irons. More than anything, I appreciate working with a safer chemical. However, it does not passivate in the sense of oxidizing the chromium like the Nitric does.
For this reason, I have added a second passivation step when using the citric acid as an added measure. I also rinse with de-ionized water.
What we really need is an oxidizer to help build the chrome oxide film in the absence of the Nitric acid.
My work is field passivation for heavy industry. I frequently work as part of a major construction project. My fear has been the stainless will become contaminated by things in the air before the chromium can react with air to form the chrome oxide film. This contamination could be in the form of free iron from other grinding and welding operations or simply attacked by the corrosive environment.
I've considered adding some other oxidizers to the rinse water such as sodium perborate, sodium persulphate or even a mild hydrogen peroxide. At minimum, I rinse with DI water with the goal of not allowing any chlorides from city water chlorine.
Any suggestions along these lines?
- Monroe, Louisiana
2006
A. Interesting question! What about sulfuric acid with peroxide as an oxidizing agent? Alternately, it certainly seems that it should be possible to electrochemically oxidize the stainless steel with a brush plating unit, but I don't know what acid would be best.
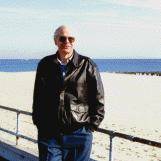
Ted Mooney, P.E.
Striving to live Aloha
finishing.com - Pine Beach, New Jersey
2006
A. Leo:
We routinely use a hydrogen peroxide solution to fully oxidize the stainless steel surface after passivation with citric chelant blends. The oxidation of the surface is the final step which nitric acid completes that the standard citric acid based system does not perform. Oxidation of the surface is important, especially after removal of iron oxide or other surface oxides present on the surface (derouging).
Thanks,
Costa Mesa, California, USA
2006
A. You are correct that straight citric acid is not a total answer to passivation. You need other ingredients to help make the chrome oxide layer deeper and a higher CrO/FeO ratio. This can be accomplished in a number of ways, including adding peroxides to the rinse water, etc.
Typical data that we get with proprietary formulations gives us both higher ratios and DEEPER layers used in semiconductor industry parts. The process of treatment is VERY critical in obtaining the correct depth and content of the passive layer, including the atmosphere in the drying stages.
There is no reason why you should not be able to exceed the % and nitric depth of CrO layer if you use the correct formulation and process.
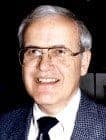

Lee Kremer
Stellar Solutions, Inc.

McHenry, Illinois
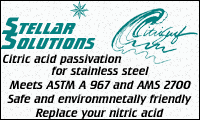
2006
Q. How would an oxygen generator fit into the application to passivate stainless steel.
Jerry Butler- Martinsville, Indiana
2006
Q. We are a small job shop and supplier to the medical industry. We use nitric acid to passivate stainless steel and titanium parts. I have two questions first: According to ASTM A967 -05 there are several different nitric bath solution concentrations and temperatures. The steel supplier as well recommends different processes for different materials say 17-4 or 400 series steels. Being a small shop we do not have the equipment to have several different tanks for each of the process solution concentrations and temperatures. It is not feasible to empty the tank and change solutions every time a part of a different material is processed. Could we use the solution of highest concentration and temperature to cover all the different materials and if not why?
Second: It has been brought to my attention that we should change solutions and not passivate titanium in the same solution that has passivated stainless. What is the reasoning behind not passivating stainless and titanium in the same tank?
- Fort Wayne, Indiana, USA
2006
A. Dear Sirs
Titanium and Stainless steel is not the same material.
Stainless steel 300 series and 400 series have different passivation steps.
Because the alloying is different.
All passivating is to change the corrosion potential for the specific elements in the alloy.
I don't think a citric passivating is the best method to get a high corrosion protection for stainless steel 400 series. I believe the passivating in dichromate and nitric acid because nitric acid will remove iron and other contamination in the alloy and a following step in dichromate passivating will show the best results.
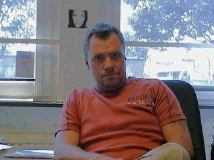
Anders Sundman
4th Generation Surface Engineering
Consultant - Arvika,
Sweden
2006
Q. How about citric acid passivation on 15-5 PH Stainless? This would be a selective passivation process where part of an assembly requires passivation. I'm in the process of testing this right now.
Dan Mitchel- New Haven
2006
Q. Let me be more clear.
Looking for help with a selective passivation issue. The parts are made of 15-5 PH steel and get machined to approximately 1"square in size. They then get sent out for passivation. After machining and passivating the parts get stocked and then assembled with various components as needed. After assembly, the (15-5) parts get laser marked with serial numbers. We require that the laser marking be passivated with a touch up kit. I've been experimenting with the Citric Gel with inconsistent results.
The current process is as follows. Clean the laser marking very well with isopropyl alcohol
⇦ on
eBay or
Amazon [affil links] and a foam swab. Heat assembly to 100° F to raise temp for passivation. Apply room temp Citric Gel to laser marking immediately after baking. Let dry on part for 1 hour. Remove dried gel with distilled water and foam swab. Let dry.
I've been sending treated flanges for a 2 hour salt spray test per AMS2700 and getting inconsistent results in terms of corrosion in the marking. I've also tested parts with no treatment to prove that the marking will corrode. Those results are also inconsistent, some corrode, and some do not.
Can this process be adjusted to work every time without the use of harsh chemicals?
Engineer - New Haven, Connecticut, USA
2006
A. I think sodium dichromate is a good selection for passivation.it is better to use 20 g/lit solution of sodium dichromate and adding chromic acid to adjust PH of bath about 4.
Ali Noroozitinplate specialist - Esfahan, Iran
2006
Q. We just reviewed Auger analysis of nitric and citric acid passivated 316SS test coupons from our own in-house AAA nitric and Citric 3 processes. We also tested identically prepared coupons from another vendor's nitric and Stellar-citric processes for comparison. The CrO/Fe ratios for all four samples were similar, 0.6-0.7, well below what is the acceptable norm of 1.0 for well passivated parts, as reported by the independent test lab. In looking at the general commentary made on this question regarding enhanced CrO layers with additional oxidizing rinses and careful drying, is what we've experienced without the additional CrO layer processing in agreement with other's findings? Is there a technical reference for CrO/Fe ratios based on the different passivation processes being used or is this information proprietary? I would like to hear from others that have experimented with the different processes and conducted their own Auger analysis.
John Buchanan- Attleboro, Massachusetts
2006
2006
A. John,
From the first day I wrote the inquiry, we did a lot of R&D and run a few DOE (design of experiments) concerning citric acid passivation. We were able to come up with a citric acid passivation process that can match nitric and even exceeds nitric acid passivation in terms of CrO/FeO ratio and passive layer thickness measured in angstrom. We used independent test lab to the ESCA and AES analysis. There is no current standard that details passive layer thickness but normal stainless steel will have a natural passivation in air with about 10 to 15 angstrom thickness. Below are just some results we have.I'm sorry I can't give you the formula since it's proprietary and awaiting patent.
ESCA Analysis:
Analyses are based on methods outlined in XPS Sematech Standard 90120403B-STD. The procedure involves measurement of the relative abundance of Cr and Fe as determined from the quantification of high resolution spectra acquired on the Cr 2p3/2 and Fe 2p3/2 photoelectron lines.
Analytical Parameters
Instrument |
Physical Electronics 5500/5600 |
X-ray source |
Monochromated Alk? 1486.6eV |
Take-off angle |
35° |
Analysis area |
2000?m x 800?m |
Neutralization |
Low Energy Electron Source |
Pass Energy |
23.5eV |
Calculation of the elemental Cr/Fe and oxidized Crox/Feox ratios are determined from high resolution data using integrated peak areas determined from nonlinear least squares curve fitting of the individual Cr 2p3/2 and Fe 2p3/2 spectra in conjunction with the appropriately applied sensitivity factors and background corrections. Sample Cr/Fe Crox/Feox
#1, Citric w/ enhancer formula 1 2.7 3.8
#2, Citric w/ enhancer formula 2 2.9 3.9
#3, Nitric with Sodium Dichromate 2.1 2.4
AES Analysis:
This analysis was performed in accordance with SEMATECH Semaspec 91060573B-STD, Feb. 22, 1993 revision. The Auger Electron Spectrometer used was a PHI 660. Each survey provides information from the outermost few molecular layers of the surface. The composition values listed in Table 1 and used in the Atomic Concentration Profiles (ACP) were calculated using sensitivity factors based on pure elements or selected compounds and are expressed as atom percentages for the elements that were detected.
Depth profiles of Fe, Ni, Cr, O and C concentrations were acquired to a depth of 150Å.
Sample Description |
C |
O |
Cr |
Fe |
#1 Citric enhancer formula 1 |
47 |
28 |
13 |
10 |
#2 Citric enhancer formula 2 |
50 |
28 |
12 |
9 |
#3 Nitric with Na2Cr2O7 |
59 |
22 |
9 |
8 |
Sample Passive Layer Thickness(Å) FeO Thickness
#1 Citric enhancer formula 1 24
#2 Citric enhancer formula 2 26
#3 Nitric with Na2Cr2O7 25
- Chatsworth, California, USA
![]() |
! Wow. People working with dichromate and even chrome trioxide. SES Bonn - Huenstetten Germany November 2, 2010
Can you point us to any articles in respected metal finishing journals where caro's acid has been tested against citric acid and/or nitric acid for the passivation of any types of stainless steel? Have any standards been written by respected standards-writing organizations for the use of caroate as a passivation agent for stainless steel? Thanks! Regards, ![]() Ted Mooney, P.E. Striving to live Aloha finishing.com - Pine Beach, New Jersey November 3, 2010 |
Passivation of stainless with 10% dichromate
Q. I am updating a drawing of an aerospace part form the later 50's. It specifies an internal company spec for passivation with just a dichromate (10% solution by weight) solution for 20 to 30 minutes. The material is 440C type stainless steel hardened to Rockwell "C" 55-62.
I believe the reason is because of the ± 0.0001 tolerance. Does anyone know of an industry spec (AMS, ASTM, etc.) that describes this method?
Tom Dalessio- Somerset, New Jersey
January 28, 2014
A. Tom
See section 10 of ASTM A967 for some of the details. ASTM A967
- Colorado Springs, Colorado
January 30, 2014
A. Tom,
Since your part is for aerospace, you may want to refer to AMS2700, but overall either that or ASTM A967 will be fine for you. The SAE crowd decided that aerospace should have their own version rather than use ASTM's replacement for QQ-P-35, but both standards are pretty much the same in the end.
I'm not sure how successful the dichromate alone was in the past for that part, a nitric-dichromate mix would have been the normal treatment. I suppose the tight tolerance might have lead someone to think avoiding the nitric was a good idea. Fortunately these days you can avoid both nitric and dichromate by using citric acid , which if done correctly should give you no problems in maintaining the tolerance.
adv.
Let us know if we can help.
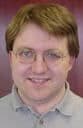
Ray Kremer
Stellar Solutions, Inc.

McHenry, Illinois
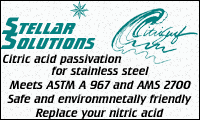
February 27, 2014
Thanks for the information guys
- Somerset New Jersey
February 28, 2014
Q, A, or Comment on THIS thread -or- Start a NEW Thread