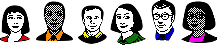
Metal finishing Q&As since 1989
-----
Titanium nitride coating thicknesses
Was curious about Titanium Nitride coatings on consumer cutting products, scissors, etc...
I was told that .2 micron is decorative, .4-.5 has some friction reducing benefits but wears quickly. 1.0 has good friction reducing, wear properties and over 2 is getting into heavy use/industrial coating. Is this accurate?
conair - Stamford, Connecticut, USA
2005
Your numbers are pretty much correct. I would be a bit wary of putting on too thick of a coating. The coating can be deposited by both chemical and physical vapor deposition (CVD or PVD). If deposited by CVD, the coating has little residual stress, and a coating thickness of around 10 microns are common. The PVD process adds considerable compressive stress to the coating, limiting coating thickness to around 5 microns. I would also be wary of claims regarding the frictional properties of TiN as well. While it may give you a lower coefficient than steel, it is not regarded as a low friction coating, and other related PVD coatings are better suited for applications where friction is an issue.
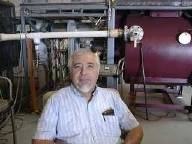
Jim Treglio - scwineryreview.com
PVD Consultant & Wine Lover - San Diego,
California
2005
2006
In the past many of the reasons for spalling or flaking off of these types of coatings have been due to the poor cleaning of the substrate, another element has been the low hardness of the substrate and hence the coating cracks in a similar way to "Ice on Mud" under loading.
The PVD coatings also have a high level of stresses in them and some coating methods are micro porous. The high stresses will add to any problems of poor cleanliness of the substrate material in causing the spalling off of the coating.
Decorative coatings may be thinner by choice of the applicator- since they do not have to really do anything apart from look good.
On the frictional properties there are a large number of papers indicating good low friction properties, and PVD TiN verses PVD TiN does exhibit good low friction properties, in some instances
<0.1.
The variation in frictional properties may be more related to the ability of the TiN coating to minimise pick up, but there will be an element of surface roughness.
High surface roughness with a Hard coating will act well as an abrasive surface and hence higher frictional properties.
A lot of information on this was produced by a UK DTI funded project called PACT- Plasma Assisted Coating Technology project.
- Sandbach, Cheshire, UK
Q, A, or Comment on THIS thread -or- Start a NEW Thread