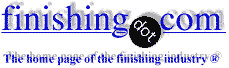
-----
What exactly is Mill Scale?
Q. I am currently working on a hot rolling facility. We are experiencing scale formation in the furnace. I know that is a natural situation, but time to time scale pits turn into mug like environment and closes the exit way of the scale. Do you have any suggestions such as chemicals or burning regime?
mertcan ylmaz- istanbul turkey
September 12, 2023
⇩ Related postings, oldest first ⇩
Q. My name is Frank Rea. I am a coatings consultant, predominately for steel structures. Arguments with contractors about mill scale are common. In order to discuss this issue knowledgeably I would like to know:
What is the chemical composition of mill scale?
Does it vary by process?
Are there primary constituents that must be present for a substance to be classified as mill scale.
thank you
Consultant - Gainesville, Florida
2005
A. Mill scale consists primarily of magnetite, Fe3O4, of characteristic blue-gray "steely" color.
An extremely thin outer film of hematite, Fe2O3, is invisible to the naked eye.
The inner portion of the magnetite contains fine metal grains and sometimes, residual black FeO (see below), which contribute to the roughness of descaled metal. Mill scale is found on all hot-rolled steel products unless processed in a protective atmosphere or descaled (e.g., for galvanizing).
At hot rolling temperatures, an inner layer of wüstite, FeO, exists between the steel and magnetite.
"At elevated temperatures, FeO constitutes about 85% of the scale thickness, Fe3O4 about 10 to 15% and Fe2O3 about 0.5 to 2%. During slow cooling [below 1040 °F] of hot-rolled coils of hot-rolled strip [and heavy shapes], most of the FeO is transformed to Fe and Fe3O4, and the latter oxide is predominant after cooling."
---
The Making, Shaping and Treating of Steel, 10th Edn., p. 1083 (1985). ISBN 0930767004.
The alloying metals form cations within the mill scale at about the alloying proportions* due to the almost instantaneous oxidation of freshly exposed metal at high temperature. Fe3O4 contains both Fe+2 and Fe+3, and is sometimes written FeO·Fe2O3. Ni+2 substitutes for Fe+2, Al+3 and Cr+3 substitute for Fe+3. Thus, (Fe,Ni)O·(Fe,Al,Cr)2O3. Cations of other valences, e.g., Si+4 and Ti+4, are accompanied by cation vacancies to maintain overall electrical neutrality. With very slow cooling, small grains of Si- and Ti-containing oxides may precipitate within the scale.
*unlike general heating or heat treatment scale, where Al, Cr, etc. preferentially oxidize.
Steel mills descale sheet and plate by passage through scalebreaker rolls, which flexes the metal enough to fracture the scale. This allows pickling acid (HCl) to attack the more soluble (partially transformed) inner wüstite layer.
- Goleta, California

Rest in peace, Ken. Thank you for your hard work which the finishing world, and we at finishing.com, continue to benefit from.
Q. My name is Dr P K Maitra, (formerly G M, Q/A & head R&D, BALCO), in past I have communicated & interacted through Finishing.com.
I have read the posting No 38657 of Mr KEN VLACH Dec 20-2005, & appreciated the efforts being done by Finishing.com & through this platform I want to ask & reply or propagate the information for future compilation for valuable readers.
- Chhattisgarh, INDIA
2007
----
Ed. note: Thanks for the kind words, Dr. Maitra! You are welcome to attributed fair use, of course, but unless Ken Vlach and individual responders reply to your offer, we can't speak for them or give their permission to use their name in a different forum or media.
A It is easy to understand why the oxides form in a specific sequence in a mill scale. The highest oxide (the one with maximum proportion of oxygen) forms on the surface as it is directly exposed to air (the source of oxygen) and the lowest oxide forms next to the base metal (the source of Fe). However, the lowest oxide, FeO, is said to form only above 570 °C. Therefore, its presence could be indicative of the scale being mill scale, which might be easy to confirm if FeO is retained at room temperature, without further oxidation to a higher oxide, for sufficiently long time.
If only mill scale was dense, adherent and continuous it could have provided necessary protection against corrosion but unfortunately it is not. Moreover, it is cathodic (and not anodic like zinc) to iron and hence will corrode much faster at locations of discontinuity due to unfavorably large area ratio of cathode to anode. In such a case, a bare metal surface might be better than a discontinuous mill scale (or any other cathodic coating) as the former will corrode more uniformly as against the possible severe localised corrosion of the latter.
- Sydney, NSW, Australia
May 18, 2010
Q. I am particularly concerned about the effects of Mill Scale if left in place and painted over. Does it have any long term negative effects on the steel or subsequent paint or coating surfaces. Secondly if left in place and painted how can in be removed in the field.
Gary Kopp- Barrie, Ontario, Canada
April 20, 2008
A. In response to the question on whether or not mill scale on hot rolled steel is detrimental, I would submit that is very much so as it is anodic to the steel. Meaning that once moisture enter the picture the steel corrode (rust) and not the mill scale. Which is why the most protective coating products designed for immersion and other tough environments require an SSPC SP-5 white metal degree of cleaning as this process removes all mill scale.
Burt OlhiserFebruary 10, 2009
- Middletown, California
A. When you are applying a coating to a steel surfaces in order to produce sufficient adhesion against corrosion it is necessary to remove all contaminants off the surface. Mill scale is porous and poorly adherent scale of magnetite, it will only give limited short term protection to steel against corrosion. If you are coating any steel surface against corrosion it is necessary to blast clean (with garnet or similar) to a finish of Sa2.5 blast standard before coating.
Regards
- Adelaide, South Australia, Australia
February 16, 2009
![]() |
Q. As per some friends, the mill scale can be used in production of steel production, put in the trench when steel liquid get out, thus it will automatically smelt in the liquid, and no wastage, steel still proper, want to know if it is the best way to use mill scale? Howard Limineral resources development - Tianjin, P.R China July 14, 2008 Ed. note: We already have several threads on the topic of how to gainfully use mill scale. Please see thread 14057, "Mill Scale Uses and Applications" and thread 20037, "Recycling or disposing of Mill scale", or search the site for still more. Q. Is there any free iron available in typical Mill scales. Dr. Zubair AlamChemist - Al Khobar, Eastern Province, Saudi Arabia October 25, 2008 Q. Hello: I want to briquette Mill Scale Dust removed from a Shot Blasting Operation. Can these briquettes be used as material to be remelted for Industrial Steel Manufacturing in EAF type of process? What are the pros and cons? Brian Lehane- Ramos Arizpe, Coahuila, Mexico December 19, 2012 Q. Hi All, The Smart Cube - Noida, India March 21, 2016 Ed. note: Please see thread 14057, "Mill Scale Uses and Applications" and thread 20037, "Recycling or disposing of Mill scale", or search the site for still more. Please take discussions about potential uses of mill scale there because if threads wander everywhere it can be difficult to find anything :-) |
Q. If you are installing heavy, rotating equipment what are the policies for the base plates, regarding mill scale. I have been taught that it is poor engineering practice to install equipment on a mill scale surface. Can anyone corroborate my thinking.
Les PulmanEngineering - U.K.
May 14, 2010
A. Hi, Les. It may depend on what type of equipment, but to the limits of my experience base plates are always painted, and to properly paint them requires removal of mill scale anyway.
Regards,
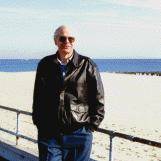
Ted Mooney, P.E.
Striving to live Aloha
finishing.com - Pine Beach, New Jersey
Q. Ted,
The base plates support a Gas Turbine weighing 370 tonnes. If the Mill Scale is on the plates, under vibration, the scale breaks down to dust and effectively leaves a void. The underside of the plate is coated with scale also and sits on a cementitious grout. The grout is water based which could result in the Mill Scale separating from the plate.
Engineering - Wales U.K.
A. Hi, Les. I've never designed in that field and can't comment on codes or standard practices for heavy gas turbines, but I do agree with you in general that steel structures require removal of mill scales, and that same opinion is also offered here by Burt Olhiser and Vijay Vijayaraghavan. Good luck!
Regards,
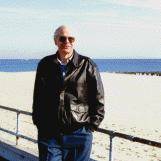
Ted Mooney, P.E.
Striving to live Aloha
finishing.com - Pine Beach, New Jersey
Q. Comments on applying finishes over mill scale gave me a sculptor's idea. I don't fight Mother Nature, I leave my outdoor steel sculptures to develop a handsome rust finish. So, if I was to remove some of the mill scale selectively, in a decorative pattern, the finished piece might develop a pattern as parts rust differently. However, would the mill scale and non-mill scale rust soon catch up with each other and soon look the same?
I posted an earlier question with no response - whether applying a rust converter
⇦ on
eBay
or
Amazon [affil links]
in a selected pattern on a rusted surface would also allow you to add visual interests or does the rust margin creep under and push off the converted rust?
- Plymouth Massachusetts US
June 11, 2011
Q. I want to remove the oil from the mill scale; does anybody have an approved process which can cost less than 10 dollars/ton?
Vk MurarkaEngineering Company - Marion, Ohio, USA
May 18, 2012
A. Hi Vk. Murarka,
Just some ideas to your question for de-oiling mill scale:
There are really many different processes. One method is using water to separate the oil content from the solid by high shear agitation. I refer you to the following US patent for details: US Patent 5047083, "Process for de-oiling mill scale".
Another patent suggests a mixing the mill scale with calcined lime followed by a burning process to form pellets. Please see US patent 4326883.
Regards,
engineering - Sydney, Australia
July 10, 2012
Q. What is the effect of steel mill scale on shear blade if the steel plate is sheared without pickling or shotblasting.
Mohankrishna G- Jamshedpur, India
October 4, 2012
All about mill scale . . .
Mill scale immediately starts at the steel making stage of casting hot metal steel grades and steel alloys when the metal is in a liquid stage. The mill scale chemistry will be the exact makeup of the steel and/or steel alloys being made. It is the outer skin of the casting and is formed by the rusting of the iron as it is exposed to the humidity and Oxygen of the air. Steel makers allow this to occur as it will form a protective coating from further rusting to occur for a period, normally 1 mm per year under normal ambient conditions. Sometimes it is forced to occur by a light spray of moisture. As indicated it will slow the development of further rusting but will not stop it and an additional 1mm per year will be expected on normal high carbon steel. Any crack or hole in the mill scale to reach the base metal will continue the rusting effect. Salt air will hasten rusting.
----
I am continuing my response on mill scale, if I may . . . In addition to the explanation on where mill scale comes from and how it forms -- mill scale is sold on the commercial and international exchange mainly to the Chinese steel makers that use low quality iron ores either domestically mined or purchased. The Chinese steel makers then mix the mill scale with the low quality iron ore and prepare it for feed to a sinter plant, whereas the iron ore is mostly less than 60% Fe and the mill scale is around 70% Fe. How much they add is dependent on their steel making processes. Mill scale can be used in other iron ore preparation for steel making but it may require crushing and grinding it to very specific sizes and too expensive or it can be briquetted and used directly. If it is used directly the further preparation and processes to use it would have to be scrutinized to ensure that it would be efficient and economic to do so. It would be beneficial to use it as it is the highest quality iron oxide available. Mill scale production is equal to 1% of all cast steel in the world. Today on an annual basis with1.4 billion tons of steel cast worldwide, that means there is produced around 10 million tons of mill scale per year. Today only about 1/2 million to 1 million tons or so are commercially exchanged. It should be noted to remember that all mill scale will include the exact makeup of the cast metal or steel and alloys. Meaning that if there are any other ingredients in the steel, carbon, any alloy or additive it will also be in the mill scale. Another question I noted was about finishing: it absolutely must be removed prior to any use of the steel and/or finishing. As it starts out to be a protectant it is also the beginning of rusting and over time the steel must be protected from itself. From the casting metal it is removed before further processing, rolling or drawing as the mill scale will damage other equipment in the processes and can cause early failure of any component.
----
Further to my previous 2 blogs on mill scale, I seem to find more information in my aged brain, therefore, I wish to explain what it looks like after it is removed from the steel and what to do with it. In a rolling mill where the steel will be stretched and squished the mill scale will first be removed mostly by water jets, or by sand blasting in some shops or by vibrating rolls in others and the mill scale will fall into a pit below the equipment where it will also be joined by rolling mill lubricants and bearing oils and water. From there it will be pumped to a holding pond, where companies like Harsco will be paid by the steel mill to clean out the pond once in awhile and get rid of the mill scale. In the U.S. in the past, and only a few short years ago it was dredged up and let drip dry and sold to a bidder, normally a cement plant who bought it for a very low amount and processed it to use in cement making since they require a little amount of iron in their processing and mill scale hit the mark. However a few years ago the EPA found that some of the ingredients, mostly from the lubricants from the rolling mill oils, caused the mill scale to be a hazardous material. The cement plants looked for other sources of the iron and mill scale became a personna non-grata. As the international market place for mill scale was taking off with China purchasing it as previously indicated, it is now an out to send the hazardous waste there and let them deal with it. This is not very neighborly, to say the least, so a few companies have come up with alternatives. One is to compress the mill scale into giving up the oils and lubricants and water to an acceptable level for the feed to the sinter plant where the mill scale is mixed with other iron ores and hydrocarbons from coke plants and bake it at 2500 °F. The squished out oils and lubricants by the way are recycled to be used once again. As far as recycling it to make other steel, the answer is yes it is being done at steel mills that employ a sinter plant. There are 7 in the U.S. and almost all steel mills in Europe, China and other places like India employ them with the use of the blast furnace to make steel. Other plants that use the EAF (electric arc furnace) cannot use them as it would take an ungodly amount of energy to extract the iron from the mill scale unless it were put through a major amount of preparation and chemical reduction first. There is also the consideration of what are the elements that are in the mill scale. Remember, I indicated that every bit of mill scale represents the product being made at the steel mill whether it is construction grades of steel like rebar or high quality alloys and stainless for example. Therefore if a steel mill wants to make rebar and they buy mill scale from the open market and it comes from an alloy shop what do they do with the other elements and how do they get it out? That costs money and lots of it for the procedures and the equipment and the chemicals to eliminate the unwanted stuff. So, further processing and experimentation and trials and tribulations must be done to be able to recycle and use all of the 10 million tons per year and growing.
Thomas J Coyne jrT.C.Inc. - Estacada, Oregon, USA
July 3, 2014
Wow, Thomas! Finishing.com has received thousands of helpful postings, but this is one of the most thorough and exhaustive ever. Thanks!
Regards,
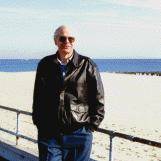
Ted Mooney, P.E.
Striving to live Aloha
finishing.com - Pine Beach, New Jersey
July 2014
Q. How can you mimic a finish that resembles mill scale on sheets of hot rolled material that has been de-scaled?
I would like to first say that I am very impressed with the knowledge here! I am an architect and builder in Las Vegas. I also have a background in metal working and have studied metallurgy fairly in depth. I have never seen such concise (and correct) descriptions and explanation about mill scale and "what it is" before reading these entries! Great job!
Anyways, as for my question:
Here in the Southwestern United States, a trend in architectural aesthetics is a heavy industrial look using hot rolled steel where the mill scale is left intact and you can see the heat marks left by the rollers in the factory. One reason this is popular is because the extremely low humidity in our dry desert climates allows for these types of finishes to be left without a sealer and will never oxidize (rust) further. So the project gets an industrial aesthetic that requires no maintenance or upkeep and the cost for these types of looks is very low. You just put up sheets of hot rolled material and you're done.
These architectural details are often full sheets of hot rolled steel used as wall paneling, fireplaces, bar-dies, etc. If anyone is interested, I can direct you to some photos on our website or social media pages to show you examples of this.
My question is this: What is the best way to fake or apply a finish that closely resembles black mill scale on a hot rolled sheet?
I am currently working on a project for an architect client who is using hot rolled sheets on a residential project. I ordered sheets of hot rolled steel from a large company in the midwest to be perforated (punched) in such a way where the different sized perforations make an image in the steel. The problem is that they ordered a "clean" hot rolled material where the mill scale has been removed. We are out of time on this project so I can't wait for them to receive the correct material and start over. I am hoping I can have them proceed with the punching and when I receive the material, just apply a chemical or something that would closely resemble mill scale.
Thank you in advanced for your time and effort!
October 26, 2016
Make Studios - Las Vegas , Nevada - USA
A. Nathan,
There are a few things you can try on a few small samples to see which you like best. You can apply a faux finish such as paint but it's tricky and the paint could stand out over time. Some people take used motor oil, spread or spray it thinly over the material and light it on fire. After it cools off you can clean and scrub. Don't try this at home kids!
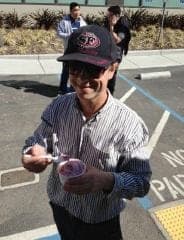
Blake Kneedler
Feather Hollow Eng. - Stockton, California
February 5, 2017
Q. Hi, I am researching ways to measure the thickness of mill scale formed on hot rolled steel coils. Can anyone suggest a way to make a Bakelite mold without disturbing the oxide scale so that I can use the mold to measure the thickness of oxide scale? In addition to the above problem, can you also suggest a way to cut the steel to the size of the molding machine without disturbing the oxide scale? "Disturbing" here is defined as breakage of oxide scale or reduction in thickness of scale due to mechanical vibration or by heat.
Dinakaran Murugadass- Chennai, Tamilnadu and India
May 4, 2017
I have a substantial restoration business in NYC restoring old "wrought iron" doors, windows, and architectural metal work. We are constantly refinishing old Fenestra-style windows and doors, chemically stripping them, and repainting. From our experience stripping thousands of windows and hundreds of doors, the mill finish is generally intact, and protects the steel. The only time it is not, is when the caulking fails and traps moisture, or air conditioners drip steadily on hot rolled steel causing it to fail. Without question in my mind, the mill finish is more durable than the typical oil alkyd paints made since lead paint was banned. We always leave it intact, unless the client doesn't want it.
The blue black finish can be imitated with nigrosene powder and top coated with acrylic lacquer, but that will be more susceptible to rusting than the mill finish.
Olek, Inc. - historic metal restoration - Newark, New Jersey, US
June 1, 2017
Effect of mill scale on refractories
Q. Hi I am Muhammad Bilal, working in a steel-making industry as a refractory trainee engineer. I just want to know that what are the effects of mill scale on refractories either acidic or basic, and what effects it may cause useful or adverse, on all refractories, monolithic and bricked ones, too.
Thank You. Please give me a detailed answer.
Agha Steel Industries - Karachi, Pakistan
November 1, 2018
Q, A, or Comment on THIS thread -or- Start a NEW Thread