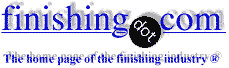
-----
Aluminum vs. Steel for Salt Water Piping
Q. I was given a project to design the piping to carry seawater from the ocean to an RO unit then to a storage tank. We have a length of aluminum pipe and steel of two different diameters. I cannot find a clear answer on which would be more resistant to salt water corrosion. The specific alloys were not mentioned as this is not a materials course, so I would believe that is up to your imagination. I would imagine the steel being something on the order of 316 stainless. I often heard 5140 Aluminum (used in ship hulls) in conjunction with corrosion, but I am not sure if it is actually used in piping. So my question is this: In general, is aluminum piping more resistant to corrosion than steel piping?
William Kenneth SumerfordStudent - Amory, Mississippi
2005
Thank you so much for the feedback. The project was geared around using the available material which was 8" 'aluminum' and 6" and 4" 'steel' pipe. PVC would have been great but it was not an option. The project was set around the scenario of providing 500,000 lbs of water a day to support the troops after the D-day landing at Omaha Beach. RO wasn't around at the time, so that is a bit of an anachronism. It helps a lot knowing that there is a good aluminum alloy that is fairly resistant to corrosion. We were given about 2000 ft of that piping so it was plentiful and with it being the largest diameter available the fluid traveled at a low velocity which means that the pump doesn't have to work too hard. I came up with about a 5 1/2 hp to pump enough seawater. Thanks so much for the information. About how long would this pipe last in constant contact with salt water?
- Starkville Mississippi
2005
A. Re pipe sizing: An 8" pipe diameter is excessive. Figuring 1.25 volumes seawater to produce 1 volume RO water, and allowing for some internal paint thickness, the linear flow rate is only 1/3 ft/second. Trade in the 8" Al pipe for 4" and send me 10% of the refund!
Re pump size: I suggest one 2.5 HP pump for intake and pre-RO treatment, and another 2.5 HP pump for the RO unit.
Anti-corrosion coating. In 1944, there's a good chance that Al & steel piping would have been coated inside and out with a bitumen paint for protection from seawater. Stainless steel piping may have been coated on the outside.
Corrosion rates. With suggested coatings and pipeline burial near shore to avoid sand abrasion, I suggest using these corrosion rates: SS 0.1, aluminum 0.25, and steel 0.6 mm/year/surface. Estimate piping lifetimes from Schedule 40 pipe thicknesses. Corrosion would be mostly of the pitting type, so leakage would be noticed well before any catastrophic failure.
Anyone with marine pipeline (or naval, etc.) knowledge is invited to contribute more accurate numbers.
History lesson: Look up Operation PLUTO (Pipe-Lines Under The Ocean), a World War II operation which constructed and laid undersea oil pipelines under the English Channel between England and France.
- Goleta, California

Rest in peace, Ken. Thank you for your hard work which the finishing world, and we at finishing.com, continue to benefit from.
2005
Q. How to protect carbon steel pipelines from saltwater in a creek environment.The type and severity of corrosion problems that I should expect to arise in service, and alleviation measures.
Lekan Danielstudent - Warri, Delta, Nigeria
October 7, 2008
Q. At oil refinery where I work we have a real problem with sea water fire fighting system specially to fire hydrants, fire monitors, underground carbon steel pipes, and check valves(NRV). Most of fire hydrant valves are butterfly valves and almost all sea water pipes are cement coated internally, but we still have pitting corrosion; pipes are of 4" and 6", rating 150 psi.
Any ideas to improve piping against sea water corrosion?
Thanks
- Kuwait
May 19, 2009
A. Dear Sirs:
RO of seawater will concentrate the salt content up to a factor 2, the regular recovery is 45% the use of 316L is not guaranteed, more exotic alloys like 904L or super duplex is currently used. Please remember that the membranes as well as the piping need regular cleaning with high pH cleaners as well as acid cleaning. In my opinion aluminum cannot be used.
- Windermere, Florida, USA
June 2, 2009
Q. Considering galvanized steel, aluminum, and stainless steel, which has the least amount of corrosion in a high sea salt atmosphere?
Richard MacVeigh- Loveland, Ohio, U.S.A.
November 20, 2012
A. Hi Richard. Surely the better grades of stainless steel are the most corrosion resistant. The 904L mentioned by Hans may be best.
Regards,
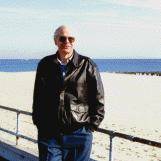
Ted Mooney, P.E.
Striving to live Aloha
finishing.com - Pine Beach, New Jersey
November 24, 2012
Q, A, or Comment on THIS thread -or- Start a NEW Thread