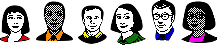
Metal finishing Q&As since 1989
-----
Best way to cool anodizing tanks?
Disambiguation: Please see also --
• Topic 58129, "Cooling of home/D-I-Y anodising baths"
Q. Dear Sirs
What the best way to handle anodizing tank cooling?
We use heat exchanger -- are coils better than heat exchanger?
If we use titanium coils in sulfuric acid tank, do we have any problem?
with thanks to you
KNP - Semnan, Iran
2005
A. Hi Mac. There are several approaches ...
- Some shops put the freon evaporator coils (titanium or lead) directly in the anodizing tank, but I think that's a bit dangerous, although highly efficient.
- Some shops pump the anodizing solution to a remote heat exchanger as you do; there's nothing really wrong with that, and engineered heat exchangers tend to be more efficient than a coil sitting in the anodizing tank, but it introduces an opportunity for an acid leak or spill.
- If the tanks are large enough to accommodate chilled water coils, that's another way, at least with a 68 - 72 °F type II bath, but it may be less practical with a 28 - 32 °F hardcoat anodizing tank.
Titanium is resistant to sulfuric acid, but having said that, I've seen many titanium heaters, coils, and anode baskets destroyed. It is important to avoid stray currents and to install the coils exactly per manufacturer's specs. Sometimes they specify grounding the coils to the anode to maintain the anodized film, but don't come back to me if you do that and have trouble--follow their instruction, not mine. Titanium can only resist somewhere around 15 volts, depending on specific alloy, so if this is a type III bath or even a relatively high voltage type II bath, connecting the coil to the anode could be trouble.
As I started writing this I was going to say that I prefer the chilled water coil approach. But as I read what I wrote, I guess I'll go with the external exchanger myself next time :-)
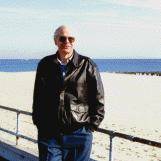
Ted Mooney, P.E.
Striving to live Aloha
finishing.com - Pine Beach, New Jersey
2005
A. Hi Mac,
Being plastics oriented, I'd opt for a plastic coil type heat exchanger.
There are, apart from very expensive fluorocarbon-teflon types, two materials made ... Polypropylene and PVDF ... both are very sulfuric resistant but PP has temperature limitations whereas PVDF is supposed to be good to 140 °C.
The heat transfer is not as good as metal ones ... but looking on the bright side, if one increases the area of the plastic ones (i.e., the length of the pipes) you'd probably get the same efficiency.
Food for thought, anyhow.
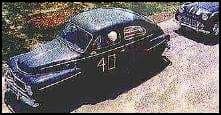
Freeman Newton [deceased]
(It is our sad duty to advise that Freeman passed away
April 21, 2012. R.I.P. old friend).
2005
Anodizing chiller system leaks
Q. We have four 1000 gallon anodizing tanks running on a common chiller system. Two are type II and two are type III. We were advised to insulate each cooling coil (titanium) from the balance of the system. We have tried PVC, CPVC, and, most successfully, 2 1/2 inch diameter teflon machined to accept threaded pipe adaptors and retained with hose clamps. However, Teflon is soft, and we still get leaks.
What is the rest of the anodizing world doing, or not doing, about this?
This is rather urgent. I'm getting into EPA area with the amount of freon we are losing.
Thanks,
Peter F [last name deleted for privacy by Editor]- Oxnard, California
2001
A. Peter,
Goest thou to a reputable purveyor of fluorocarbons .,.. and get some glass reinforced teflon for your tank adaptors... there are other teflon formulations but as you need some strength and less deforming, that's the way to go.
Why doesn't PVC work for you? Strange. Heck, you could have used phenolics but I'm partial to PVC, wherever possible. But don't use nylon.
In Canada we have suppliers like Johnson Industrial and Cadillac plastics ... maybe Cadillac has U.S. operations. Try them.
I'd imagine that you've used teflon tape ... the rule of thumb was to go 1/2 to 1 turn more than a dry fit - otherwise you can stress the female threads and land up, in time, with leaks.
Cheers!
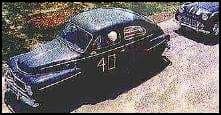
Freeman Newton [deceased]
(It is our sad duty to advise that Freeman passed away
April 21, 2012. R.I.P. old friend).
2001
A. I think you actually have two problems Peter: while the first is the dielectric problem, the second is that you are running refrigerant instead of chilled water/glycol to the anodizing tanks. Personally, I think you really should be cooling water/glycol with the freon, and then running only the water/glycol to the coils in the tank. Then you can use dielectric unions or just high pressure radiator hose on the connections to the coils. Unfortunately your existing coils may not be big enough to cool the tanks with water/glycol running through them instead of freon.
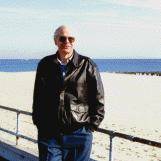
Ted Mooney, P.E.
Striving to live Aloha
finishing.com - Pine Beach, New Jersey
2001
A. Peter,
Here's an addendum ... why is it that ideas often spring up later on?
Re. your loss problem, I have a gut feeling that you are overtorquing, perhaps, the adaptors. Heck, I remember TFE taping a 1/2" PVC nipple and BREAKING the moulded PVC socket by just turning and twisting with my hands! This was an experiment to show the lubricity of the TFE and the stress on the female threaded connector. Hence the suggestion of dry 'tight' fit + TFE tape + 1-1/2 turns and NOT MORE is a practical solution when using thermoplastic socket fittings.
Technically you might be better off to use a metallic threaded socket!
But there is another way to solve your problem! That's to use an 0-ring approach. Get some PVC bar. Drill it with it having a small internal ledge. Machine a straight thread, not a pipe thread. Locate 0-ring onto ledge. Then (with some TFE tape) thread in the male connector.
Anyhow I'm sure that any local thermoplastic fabricator could have solved your problem.
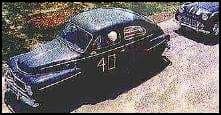
Freeman Newton [deceased]
(It is our sad duty to advise that Freeman passed away
April 21, 2012. R.I.P. old friend).
2001
Material selection for anodizing heat exchanger
Q. I have a customer who requested a cooling system for his anodizing tank. I have calculated the load [Ed. note: letter 2647 addresses how to calculate the cooling load] but need to find a suitable heat transfer medium that I can immerse. He does not want to use the lead system that is in place for heating the tank.
Any help would be appreciated
Contractor - Scotch Plains, New Jersey
2007
2007
A. Hi Mike,
There are a number of options ... probably a PVDF heat exchanger is the best ... there's teflon but that costs an arm and a leg
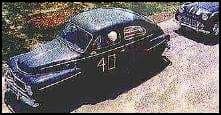
Freeman Newton [deceased]
(It is our sad duty to advise that Freeman passed away
April 21, 2012. R.I.P. old friend).
A. 316L will last several years IF the tank temperature never gets above 75 °F. There is an exotic alloy that can be used, but it costs about double of 316. The drawback with teflon type heat exchangers is the horrible "R" of plastics which requires rather thin or very large heat exchangers.
James Watts- Navarre, Florida
2007
A. Mike
Zirconium will work, but is pricey. It can be used with direct expansion systems or chilled glycol solutions. As James mentioned, the
316L has problems with exposure to higher temperatures. Something to consider if the user is going to make occasional decants.
- Colorado Springs Colorado
2007
A. You can use Teflon or a generic equivalent material. This would be applicable to both chromic and sulfuric acid anodizing.
Gene Packmanprocess supplier - Great Neck, New York
2007
Piping Anodize Electrolyte to the Heat Exchanger
Q. Anodizing electrolyte being circulated to be cooled through a heat exchanger. Electrolyte to be taken from the anodizing tank sent to heat exchanger where it is cooled by cold water and returns back to the anodizing tank. Tank size 1.5 m wide x 3 m high x 8 m long. In order to have a uniform distribution of temperature in the tank, where should be the outlet and inlet openings be placed on the tank? Any schematic or description showing electrolyte circulation?
Timur Ulucak- Turkey
February 27, 2014
A. Hi Timur. Suction and discharge should be at opposite ends of the tank (8 m apart), or even diagonally opposite if that is practical. Ideally, the suction should also be opposite the discharge depth-wise too.
But I dislike the suction being at the bottom of the tank because it places the entire contents of the tank at risk of siphoning out in the event of a leak. I'd prefer to see the suction outlet to be only low enough in the solution to prevent cavitation.
The discharge can then go over the tank rim, and on down to the bottom of the tank as long as there is a check valve, vacuum breaker, and/or some small holes in the discharge pipe to prevent siphoning in the event of a leak. Good luck.
Regards,
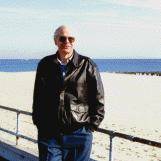
Ted Mooney, P.E.
Striving to live Aloha
finishing.com - Pine Beach, New Jersey
March 2, 2014
Q, A, or Comment on THIS thread -or- Start a NEW Thread