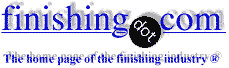
-----
Electrical resistance of Class 3 chromate conversion coating
To make stuff easier to find we've moved Q&A's about how to do the testing, what labs offer it, and where to buy or how to make the test equipment to:
• Topic #0012 "MIL-C-5541 / MIL-DTL-5541 Chromate / Chemfilm / Iridite / Alodine Conductivity Testing"
Q. Electrically conductive spec for chromate finish?
Gerry Cafferty- Erie Pennsylvania
October 26, 2022
⇩ Related postings, oldest first ⇩
Q. We plate aluminum pads for electronics. As part of the process flow, the aluminum is chromated with a solution consisting of a Cr (III) compound, a fluoride and a tin (4) compound. The chromate is conductive. We find occasional corrosion that we suspect may be due to high levels of fluoride and chloride in the chromate solution. Is anyone aware of any commercial or non-commercial chromate formulations that provide both corrosion protection (without the use of significant amounts of fluorides or chlorides) and a conductive surface?
Charles Rosenstein- Jerusalem, ISRAEL
2001
by Raj & Ali
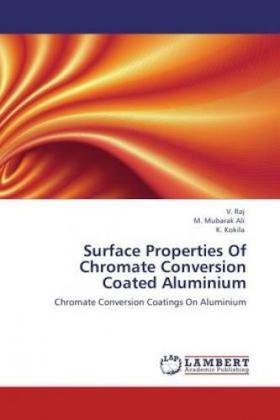
on eBay or Amazon
or AbeBooks
(affil link)
A. I'm not really sure if this will work as base for plating on aluminum but if you're looking for chrome-based corrosion protection, you might try Alodine or Iridite process.
Dado Macapagal- Toronto, Ontario, Canada
A. Hi Charles. Dado has mentioned two tradenames for proprietary chromate conversion coating chemistry. MIL-C-5541 covers the topic of corrosion resistant chromate conversion coating, and specifically addresses conductivity as well. It's actually a pretty well established technology.
If you wish to plate the aluminum, though, the conventional approach is not to chromate it, but to zincate it first and then electroplate it; alternately if the plating will be tin plating, there are processes like Atotech's Alstan, which start with a stannate immersion rather than the zincate immersion. Good luck!
Regards,
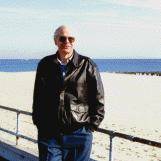
Ted Mooney, P.E.
Striving to live Aloha
(Ted can offer longterm or instant help)
finishing.com - Pine Beach, New Jersey
Multiple threads merged: please forgive chronology errors and repetition 🙂
Alodine electrical conductivity issue
I understand that Alodine is an electrically conductive coating, which does not affect grounding. Is it true?
Lev J. Balanovsky- Feasterville, Pennsylvania, USA
2001
Yes, a thin coat to Mil-C-5541 class 3 is often used in grounding areas. See MIL-C-5541 and there are some numbers for this.
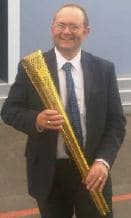
Martin Trigg-Hogarth
surface treatment shop - Stroud, Glos, England
Calling the chromate conversions "electrically conductive" is really a misnomer. The Class 3 coatings are so thin that when put under pressure, they short through and those shorts conduct, the coating is not in itself conductive.
The variables involved are both the thickness of the coating, and the surface finish of both mating surfaces. If you had a highly polished pair of surfaces, it would be difficult at best to cause the necessary "punctures" through the surface thus allowing electrical conductivity. Conversely, extremely rough finishes would allow conductivity with very little pressure.
Bob Denneyavionics Tampa, Florida
Hello,
I am trying to find value (number) for relative conductivity of Alodined aluminum.
- Port Moody, BC, Canada
2006
Ed. note: We've merged several threads, so the answer is now on this page :-)
Multiple threads merged: please forgive chronology errors and repetition 🙂
Q. I would like to know the electrical properties of ALODINE 1200. We are using it as protection on our metallic housing of Door Control Unit. Is it necessary to protect the ground stud from ALODINE 1200 ?
Emmanuel SEREZATtransport - FRANCE
2005
A. Alodine 1200 is one of chromate chemical conversion coating that meets requirements of MIL-C-5541 (you can find a lot of other processes). MIL-C-5541 Class 3 requires maximum 5000 µOhm per sq. inch electrical resistance. Actually, electrical resistance for properly performed Class 3 is usually 1000-2000 µOhm per sq. inch. MIL-C-5541 Class 1A does not require electrical conductivity. Most chemical conversion coatings from QPL (including Alodine 1200) can be performed as both Class 1A and Class 3. Therefore you should check which class is processed on your parts.
Ilya OstrovskyGermany/Israel
Q. Could you please explain about the electrical resistance on Alodine surface. Do I understand correctly that Alodine surface itself gives some resistance on aluminium. And what is the standard for the resistance on the Alodine surface and how to measure the resistance? From MIL-C-5541, the resistance needs to be less than 5,000 micro-Ohms/sq. inch. But current supplier cannot achieve that figure, 1-4 Ohms is the best they can do. I did experiment as below.
Measuring 100 of bare aluminium. I also did chromating evaluation by dipping bare aluminium for 10 different times in chromating bath. (Alchrom 713:AM713, 10 each at 40, 60, 80, 120, 130, 140, 150, 160, 180 and 200 seconds.) Below are summarized my findings:
1. Base on my evaluation, I found that the Alodine surface would create some resistance to aluminium. The average resistance of bare aluminium are around 0.2-0.5 Ohm. But the resistance of the aluminium after chromating are around 1-4 Ohms.
2. According to my investigation, thicker Alodine surface will give the same resistance to Aluminium. (1-4 Ohms) I asked my supplier to do chromating by 10 different dipping times in chromate bath. (40, 60, 80, 120, 130, 140, 150, 160, 180 and 200 seconds (my assumption is longer dipping time gives thicker Alodine surface).
3. The current dipping time in Chromate bath is 130 seconds.
P.S. If I need lower resistance on Alodine surface, what should I do? Change the chemical? Or process?
Regards,
York - Bangkok, Thailand
2006
A. First, 'Alchrom 713' is not listed in QPL-81706
[⇦ this spec on DLA]-16. Does the manufacturer indicate it will meet MIL-C-5541, Class 3 requirements?
Second, is the resistance measured as described in MIL-DTL-81706
[⇦ this spec on DLA]
B?
"The average resistance of bare aluminium are around 0.2-0.5 Ohm" -- Should be much lower. Maybe on raw material, prior to any pretreatment (or pretreated material aged in air)? Rinse a sample after desmutting, dry with a lint-free cloth & measure resistance.
Unfortunately, your findings did not appear above. Does the yellow coloration & resistance increase with increasing immersion time and then level off? An even shorter time may be necessary for a Class 3 coating, which may be a pale, iridescent gold or yellow (or even colorless).
General info for low resistance: The starting material should be a clean wrought alloy, smoothly rolled or finely machined, free of corrosion. Clean in a non-etching detergent, alkaline etch the minimum time for uniform bubbles, desmut in 50 vol% nitric acid, and rinse in DI water prior to chem-film (additional rinsing not listed). The chem-film pH & conc. should be maintained per mfr. The surface must not be noticeably roughened by etching, nor allowed to dry between steps. Sometimes, the alkaline etch is omitted, although it is preferable to do the same procedure as for production.
Shorter chem-film times give lower electrical resistances, but a compromise is necessary to maintain the 168 hours salt spray corrosion resistance.
In summary, proper pretreatment and shorter chem-film immersion time will probably help.
- Goleta, California

Rest in peace, Ken. Thank you for your hard work which the finishing world, and we at finishing.com, continue to benefit from.
Q. The aluminium my supplier is using is 6063T5 and they are performing the pre-treatment process before chromating as following.
Start
Degreasing
Water Rinse 1
Water Rinse 2
Strong Base
Water Rinse 3
Water Rinse 4
Strong Acid
Water Rinse 5
Water Rinse 6
Alodine (Alchom 713)
Water Rinse 7
DI Water Rinse
End
I did measure the electrical resistance after Water Rinse 6 and found that the avg. resistance was exactly the same as bare aluminium before pre treatment process. (0.3 Ohms) Therefore I can conclude that the resistance came from chromating process. Does anyone here know about what kind of chemical I should use if I need the lower resistance to my aluminium and I still need to have the yellow color?
Regards,
York - Bangkok, Thailand
A. In the aircraft fabrication and maintenance industries process, Alodine 1000 is used for low resistance and better conductivity (e.g. used for connector assembly on aluminium parts that need electrical bonding or grounding). Compared to Alodine 1200s, the 1000 has better conductive properties and creates a thinner film coating (the yellow color will also look lighter and almost transparent). You should try testing the 1000 solution for a change. Both solutions are mentioned in MIL-C-5541.
Syvan Chartyaaerospace - st-hubert, Quebec, Canada
![]() |
Q. Dears, - Semarang, Jawa tengah, Indonesia April 15, 2011 A. Hi, Francois. Yes, Cr+6 is considered hazardous in most jurisdictions today. But Alchrom seems to be a trade name of Nihon Parkerizing*, just as Thunderbird is a trade name of Ford. A Thunderbird was a 2-seat sports car, a 4-seat luxury car, and a 6-seat family sedan depending on what Ford decided at a given time. Similarly, the composition of a chromate conversion product can be hexavalent, trivalent, or whatever the trade name owner decides at any given time. Please get an MSDS from Nihon, as they alone decide.
* -- Further complicating things is that there are several different but similar-sounding trade names for chromate conversion coatings. Alchrom is one trade name, Alchrome is another, and Alocrom is a third, whereas the words Alochrom, Alochrome, and a few others are very widely used according to Google ... but I don't have the energy to track them all down and determine whether they are actual trade names or just pervasive misspellings :-) Regards, ![]() Ted Mooney, P.E. RET Striving to live Aloha (Ted can offer longterm or instant help) finishing.com - Pine Beach, New Jersey |
Multiple threads merged: please forgive chronology errors and repetition 🙂
Q. I would like to ask if someone has a value table with the results of measurement of electrical results of Alodine 1200S class 3? I would like to see the behavior of the alodine class 3 when measured according to MIL-DTL-81706.
Leandro reis- Lorena SP, Brazil
July 21, 2021
A. Hi Leandro. We appended your inquiry to an existing thread on the subject, and highlighted Ilya Ostrovsky's earlier response to a similar question. The test is sufficiently complex, and thus subject to error, that pass or fail Mil-C-5541 may be a better way to answer your question than numerically :-)
Luck & Regards,
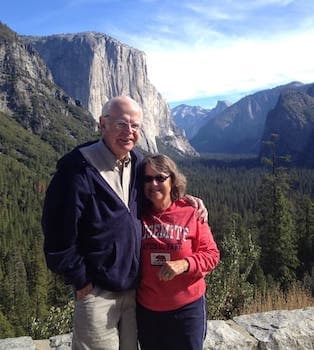
Ted Mooney, P.E. RET
Striving to live Aloha
(Ted can offer longterm or instant help)
finishing.com - Pine Beach, New Jersey
Q. Regarding the conductivity of Chemical Conversion coatings on Aluminum (MIL-DTL-5541) what does it mean that so many coatings are double qualified on the QPL to both 1A and 3?
For example we use T5900 and have an electrical contact resistance requirement. Our typical values post treatment pre salt spray are in the 1-2000 µohm range. Per the spec we also test to 168 hours salt spray where we still have contact resistance within spec, typically about double the original 1-2000 µohm range. To me, that seems to indicate these coatings are conforming to both class 1A and 3.
I think the typical thinking and a quick reading of MIL-DTL-5541 says that if you want low contact resistance use class 3 and if you want the best protection against corrosion use 1A. However, seems to me that you actually get both maximum corrosion protection and low contact resistance with these new double qualified chem conversion coatings.
Thoughts?
- Salt Lake City, Utah
July 29, 2021
A. Is it just a semantic expression to say "double qualified"?
The product used for application may be QPL listed and capable of Classes 1A AND 3, but each "coatings" are different because the concentration, time and pH are different in each of two tanks containing the same product.
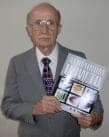
Robert H Probert
Robert H Probert Technical Services

Garner, North Carolina
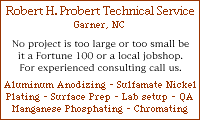
t The phrase "Double Qualified" is of my own making. I'm just saying it seems to be qualified to both. From my research it seems that there are two major differences between 1A and 3: 1) Contact resistance and 2) qualification corrosion resistance of 336 hours for class 1A (per Table 1 in MIL-DTL-81706). Conformance for both class 1A and 3 is still 168 hours per both 81706 and 5541.
I guess I'm trying to wrap my head around the fact that if a coating both meets the 168 hours salt spray and the contact resistance testing, how is it not both a class 1A and 3 coating?
- Salt Lake City, Utah
August 2, 2021
----
Ed. note: Readers may also be interested in
thread 13808, "Achieving Class 3 Chromate Conversion Coatings" and
letter 38755, "Aluminum conductivity, chromate coating, oxidation"
Q, A, or Comment on THIS thread -or- Start a NEW Thread