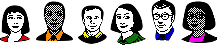
Metal finishing Q&As since 1989
-----
Electroless Nickel Plating with Silicon Carbide Particles
Q. Hi,
I am presently doing the Postgraduate project on this topic. I have some difficulties in that I am using the acid hypophosphite bath containing 30 g Nickel Sulphate, 10 g sodium hypophosphite, 10 g sodium acetate, 5 g SiC particles -- and substrate for coating is of mild steel.
I am not getting any coating on the substrate. I want to know why this is happening? I am using the nital etchant to observe the coating, is it an appropriate etchant?
Mahajan Devendra AshokStudent - Pune
2005
A. You left out the most important parameter -- Temperature! Also what kind of agitation are you using? How are you activating the steel?
James Watts- Navarre, Florida
2005
Q. Hi,
As far as mild steel activation is concerned, I first do surface polishing until I have the mirror-like appearance; then secondly I hold it in 10% NaOH solution which is at 60 °C; after that I wash it with distilled water; then activate with dilute HCl solution; then wash again with distilled water; and then hold it in the bath. Also for SiC particles I washed them with acetone
[on
eBay or
Amazon] then with distilled water and then cleaned with 34% HCl solution. The temperature of bath is 90 °C, and speed of agitation is 150 RPM. I am not getting any coating on the substrate. I want to know why this is happening? Also I want to know how much coating thickness should I get if I hold the substrate for 3 hr in that bath?
student - Pune, Maharashtra, India
2005
A. Have you narrowed the problem to:
a) the bath not plating or
b) the metal surface not activating?
Has your bath successfully plated visible amounts of nickel on some other kind of metal other than steel, such as copper wire? If your rinse water was stagnant and became alkaline with drag-over from the NaOH, the rinse after the acid might de-activate the surface. Use new water for that last rinse, and don't rinse very long.
- Los Angeles, California
2005
A. You don't mention the bath pH? Commercial electroless solutions usually work in the range of 4.7-4.8
Also you have to agitate SiC powder before adding particles to plating bath. I've done a similar project, personally I am adding my particles to 200 cc bath solution and ultrasonic it for 2 hr before using particles in bath.
The mechanism for deposition Ni-P coatings is pure mechanical so use abrasive paper 800 for entrapping particles and coating.
The rate of deposition depends on Temp, pH and chemical composition of the bath. deposition rate of commercial Ni-P solutions is about 18-25 µm/hr. You are using SiC particles in bath it results lower deposition rate.
- Iran - Tehran
November 18, 2009
Particle percentage increases to a point, then decreases
Q. Hi
In electroless composite coatings for example Ni-P-SiC, the volume percentage of particles in coating such as SiC or Al2O3 after a maximum value decreases. I want to know why this decreasing occurs.
thanks,
university - Iran
2006
A. Two reasons. The grit gets an organic slime on it that is hydrophobic and becomes difficult to occlude onto the part in the electroplated metal. Periodic cleaning in a similar acid with peroxide is sometimes used.
The second reason is that the smallest particles are easiest to plate out, so the plate out rapidly. As their % diminishes, the amount of particles in the plated metal steadily decreases.
- Navarre, Florida
2006
2006
A. In electroless co-deposition process, the particle flux at the interface available for impingement at the surface and the holding time of the particles at the surface determines their level of incorporation rather than the type and nature of second phase particles added to the electroless plating bath. The impingement of the particle on the substrate is determined by the flux of the particle at the interface. The particle flux at the interface, in turn, is determined by the concentration, size and density of the particle. The holding time is a function of mode of agitation, speed, and particle shape.
The observed increase in the level of incorporation of particles in the electroless Ni-P or Ni-B matrix up to a certain concentration can be ascribed to the increased flux of the particles adjacent to the electrode surface. However, beyond this concentration, there is a possibility of grouping or agglomeration of the particles due to the decrease in the mean distance between them, resulting in settlement of these particles. Such an effect will lead to a leveling off in the flux of the particles that are available at the interface for incorporation in the deposit, causing either a saturation or slight decrease in the level of incorporation.
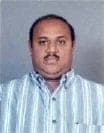
T.S.N. Sankara Narayanan
- Chennai, Tamilnadu, India
(ed.note Nov. 2017: The good doctor has a fascinating blog at https://advancementinscience.wordpress.com)
Our electroplating is soft compared to Japanese electroless plating
Q. Hi, could anyone give me advise on hardening the nickel silicon carbide coating? is there an alternative to nickel carrier? reason I ask is that we recently ran a test on a standard Japanese motorcycle cylinder vs. the plating we do, and the results were astonishing. The "factory" cylinder measure in at 849 - 973 HV and ours at 366 - 471 HV. I'm to add more of the Kermet that we import as it contains more silicon particles. we are electroplating and as far as I know the "japanese factory" is plating Electrolessly. Advice would be much appreciated.
Didier Bartholomeplating shop - Johannesburg, Gauteng, South Africa
August 16, 2011
A. You fail to say what kind of nickel you are using to co-deposit the carbide.
Electroless nickel is quite a bit harder than electrolytic nickel. Heat treating makes it even harder.
Co-deposition out of an electroless bath is a lot more difficult than from a normal tank.
Nickel sulfamate is rather soft. Nickel sulphate is quite a bit harder. Hardeners (organics) can be added, but they can be a bit of a problem to control in a co-deposition tank.
Adding sodium tungstanate will also harden the plate, but is another thing to control.
Cobalt sulphate could be used as it is a bit harder than nickel sulphate plating, but it is normally a lot more expensive.
- Navarre, Florida
August 17, 2011
A. The deposit consists of more or less pure nickel with particles of silicon carbide embedded.
The hardness you measure depends on whether your indenter hits a particle of silicon carbide or not.
I would have no confidence in hardness measurements on this type of material.
In any case, hardness is not a reliable predictor of wear, although they are related.
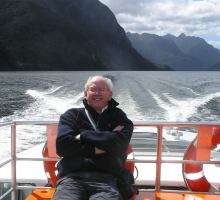
Geoff Smith
Hampshire, England
August 18, 2011
Q. What Chemical Manufacturer Companies sell the electroless nickel carbide solutions in the USA? What is the viscosity of the solution?
Thanks
Consultant - Arlington Texas,USA
March 19, 2019
March 2019
A. Hi Jim. To minimize lost motion please tell us your situation because there may be problems such as regional exclusives, licensing fees, etc. And I assume you want to build a plant to apply this coating yourself, rather than sending parts out for plating.
Probably the best known brand name of nickel plus silicon carbide is "Nikasil" (this was originally electrolytic nickel and may still be, but Mahle may offers electroless nickel with silicon carbide particles as well); Surface technology in Trenton NJ offers every possible particle type in electroless nickel composites.
Elnisil, Kanisil, and Alusil are earlier tradenames for processes that may lead you to manufacturers.
Readers are very welcome to mention other suppliers if they know any, but no testimonials or slams please (why?)
Regards,
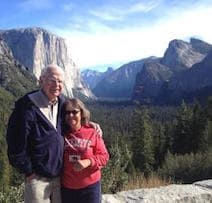
Ted Mooney, P.E. RET
Striving to live Aloha
finishing.com - Pine Beach, New Jersey
June 15, 2019
A. You left out one,
I call mine DynaSil !
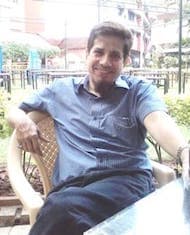
Khozem Vahaanwala
Saify Ind

Bengaluru, India
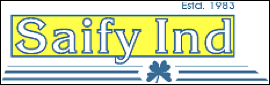
Q, A, or Comment on THIS thread -or- Start a NEW Thread