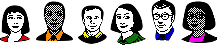
Metal finishing Q&As since 1989
-----
EN over aluminum; corrosion resistance?
2005
Q. I would like to get maximum corrosion resistance of EN applied over 6061T6 aluminum. I'm planning to specify 0.001" ± 0.0002" thick EN. The parts live in jet fuel.
What percentage of phosphorus should I specify?
Will heat treatment affect the corrosion resistance?
The parts have some #4-40 SAE threaded holes; is that a problem?
Is a thicker coating practical?
Is the coating tolerance too tight? How about using 0.001" minimum instead?
Should I specify copper under the EN? Is that electroplated?
How can I confirm the coating thickness?
Can I specify the pores in the plating to insure corrosion resistance?
Thanks!
Alan Kirkpatrickaerospace application - Shelburne, VT, USA
2005
A. What percentage of phosphorus should I specify?
10 to 13% Phosphorous ( Should have an Amorphous layer ).
Will heat treatment affect the corrosion resistance?
Yes it will.
The parts have some #4-40 SAE threaded holes; is that a problem?
The ID will be small by 0.002" in diameter.
Is a thicker coating practical?
If it do not affect the other dimension.
Is the coating tolerance too tight? How about using 0.001" minimum instead?
Not for Electroless Process.
Should I specify copper under the EN? Is that electroplated?
EN can be plated directly on to this grade of Aluminium.
How can I confirm the coating thickness?
XRF equipment for non destructive.
Can I specify the pores in the plating to insure corrosion resistance?
No comments.
- Singapore
2005
A. For most applications, EN coatings containing more than 11%P is significantly more corrosion resistant than any other composition.
Heat treatment at temperatures above 450F degrades corrosion resistance and should be avoided. However, heat treatments at 400F are commonly used to promote adhesion and have no effect on corrosion resistance.
The #4 holes are so small that they will quickly become filled with hydrogen gas and stop plating. The coating will probably only extend 0.1" or 0.2" down into the hole and will not be very thick. Vibrating the parts may help, but probably will not solve the problem. You should find another way to protect the holes.
EN can be plated to just about any thickness (say for salvage). However, practically 0.003" coating are usually the maximum used for corrosion protection. But for jet fuel immersions, 0.001" should be adequate.
Your tolerance is practical, but you can specify 0.001" minimum if you wish. You might review ASTM B733 Service Condition SC3.
Do not use a copper strike prior to EN. It may cause adhesion problems. Either go directly from a double zincate to the high phos EN bath, or go through an alkaline EN strike first. Either will provide adequate adhesion.
To measure the thickness of high phos EN on aluminum you can use the beta backscatter instrument. Again see ASTM B733 or ASTM B567. Also look at the Test Equipment section of this web site for instrument suppliers.
You can specify porosity testing on the finished part to confirm the coatings' freedom. Again see ASTM B733.
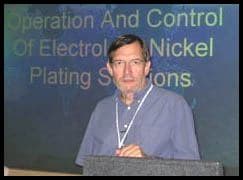
Ron Duncan [deceased]
- LaVergne, Tennessee
It is our sad duty to note Ron's passing on Dec. 15, 2006. A brief obituary opens Episode 13 of our Podcast.

Q, A, or Comment on THIS thread -or- Start a NEW Thread