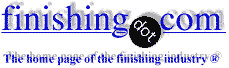
-----
Melonite, Tenifer Salt-bath nitriding for Glock & firearms
Q. I have a Kimber Super Match with the Kim Pro finish on the slide. It is horrible to me; I holstered it once in a dirty holster and scratched the finish. Now every time I take it out to the range I get marks on the slide from shell casings at the ejection port and other mix and chips I can't even explain.
I have a Springfield XD in hard Chrome and it seems to be indestructible. But I do want a black finish on the Kimber slide. I hear different things about Cerakote being so durable but I don't believe painted finishes are durable at all. And I am not sure about PVD or DLC so I'm sold on hard Chrome.
My understanding is that black hard Chrome is not quite as hard as white hard Chrome . I have to say that whatever black finish Smith and Wesson used on their MNP pistols was very durable until I carried the gun for 6 years and the corner of the slide started to rust a little due to skin and sweat contact, but I don't find this to be unreasonable.
Can you let me know your thoughts on black finishes for scratch resistance?
- Lake Forest California
December 26, 2022
A. Hi Michael. We added your posting to a thread about salt bath nitride finishes because I think this is probably what you are looking for. It's as much a heat treatment as a finish, so the question becomes what material are the parts you are speaking of made of? If the slide is steel, salt bath nitriding sounds good.
Luck & Regards,
Ted Mooney, P.E. RET
Striving to live Aloha
finishing.com - Pine Beach, New Jersey
⇩ Related postings, oldest first ⇩
Q. Where would I find a Side by side comparison of Burlington's Melonite Process vs. the German Tenifer Process? I am often involved in arguments regarding the these two finishes on Smith & Wesson and Walther forums. Both Companies produce a version of the same Walther Designed 99 pistol (Walther Tenifer over Steel and Smith amp;& Wesson Melonite over Stainless steel.)
Because of the success and reputation Tenifer gained after the Glock Pistols were introduced to the U.S. market some years ago, Tenifer seems to have gained the reputation of an indestructible miracle finish unable to be duplicated in America. I say this attitude is wrong and American finishers know just about as much about super hard firearms finishes as the Germans on their best day. Smith & Wesson didn't just pull Melonite out of a hat. The Engineers at Smith & Wesson knew that Melonite over Stainless was a pretty advanced finish for Firearms slides. So help me out guys. I may be right. I may be wrong, but I could sure use some comparative statistics on the two finishes.
hobbyist - Enid, Oklahoma
2004
A. Hi, Jim. Tenifer and Melonite are trade names for firearm finishing processes that involve salt bath nitriding. The heart of the matter is probably licensing rights rather than technology. I do not have any special inside information, but I believe that Glock will not let the supplier license the Tenifer name to any other firearms manufacturer; therefore, other firearms manufacturers are using a similar finish but from other chemical suppliers or under different trade names.
Historically, firearm parts were black oxided ('blued' is another name for the process), which is an oxidation process which produces black rust, but is only a few millionths of an inch thick, does not offer much corrosion resistance, and doesn't alter the underlying steel. Salt bath nitriding is a case hardening process that leaves a thick, corrosion resistant, hard surface. We have an article on line here which explains it (under a 3rd trade name), the "Kolene Q-P-Q Process".
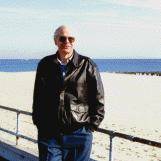
Ted Mooney, P.E.
Striving to live Aloha
finishing.com - Pine Beach, New Jersey
Q. What happens to a Melonite pistol slide that later has to be re-blued. Do the Melonite properties remain in the metal or do they disappear? In other words, is it (the Melonite) a permanent part of the metal. I have a Melonite slide that I would like to refinish so I am curious. Thanks.
Richard Kay- Port Washington, New York
2006
A. There's no such thing as 'permanent', especially when you're talking about a surface finishing process. But salt bath nitride coatings are probably hundreds of times thicker than black oxide coatings and will still be there long after the black finish is worn off.
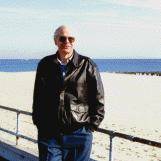
Ted Mooney, P.E.
Striving to live Aloha
finishing.com - Pine Beach, New Jersey
A. From what I understand - Tenifer can't be applied in the US because the EPA won't allow it.
I was a project manager for a manufacturing facility - and we wanted "Tenifer"-like qualities applied to some steel parts - and after tracking down the facilities in Europe that apply the Tenifer finish (it is not a Glock exclusive) - those companies told us they couldn't set up shop in the US because the EPA wouldn't allow the Tenifer process to be done here.
So - that would make the "Melonite" process different - as it can be done in the US. How different - I have no idea. More importantly - if there is any *practical* difference between the finishes? That is the $64,000 dollar question...that I don't know the answer to.
- Ogden, Utah
I have seen a lot of postings to that effect on gun forums, Jones, but I really don't think it's an EPA issue because salt bath nitriding is widely practiced in this country; plus in a lifetime working in the finishing industry I have never heard of any finishing process being banned by the EPA (although there a few real or de facto bans of chrome plating in some local jurisdictions). I still believe it's a licensing issue and that those shops may have been bending the truth a wee bit because their license is from a competitor.
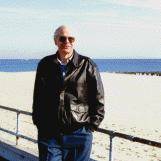
Ted Mooney, P.E.
Striving to live Aloha
finishing.com - Pine Beach, New Jersey
A. MELONITE IS ANOTHER WORD FOR Tenifer. THEY ARE THE SAME EXACT THING! YOU CAN DOUBLE CHECK MY ANSWER BY SIMPLY TYPING "MELONITE ENCYCLOPEDIA" ON THE GOOGLE SEARCH AND BE ABLE TO LOOK IT UP YOURSELF FOR VERIFICATION.
Christopher Deleon- Palm Beach, Florida
2007
Thanks, Christopher
At www.durferrit.com/en/unternehmen/firmengeschichte.htm, Houghton Durferrit -- formerly part of DeGusa, but now a division of H.E.F. -- claims both trademarks and says they are the same thing. If they own the trade names as they claim, they are free to use them as they choose, just as Ford has been free to say a "Thunderbird" is a 2-seat sports car, a 4-seat luxury car, or a 6-seat family sedan to suit changing times.
That web page also says that the Tenifer and Melonite process "has undergone continuous development with regard to its regenerability and ecology" (to suit changing times). So neither process is quite the same process as it was in the past. They are only trade names, not process descriptions, and they've already declared that they've changed them and will continue to change them as they choose.
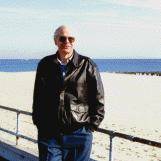
Ted Mooney, P.E.
Striving to live Aloha
finishing.com - Pine Beach, New Jersey
A. The only difference in the "Tenifer" process and "Melonite" is the brand name.
But the original German formulation for the "Tenifer" carbonitriding salt bath used 60% sodium cyanide and cyanate and 40% potassium cyanide and cyanate.... That's why the EPA wouldn't let anyone do it here.
The process has to be cyanide-free here.
As far as I can find out, some places in Europe are still using cyanide salts.
Mmmmm....smell the vapor coming from that vat of molten sodium cyani..i...... thud!
- Birmingham, Alabama
A. Thanks, Edward, but can you quote an EPA reg that says this? I'm not saying you are wrong, but I am saying that we've received countless postings saying "the EPA doesn't allow ..." that have been in error. Although people are continuously working to reduce cyanide use, virtually all silver plating and brass plating (for example) is done from cyanide solutions.
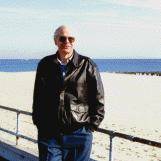
Ted Mooney, P.E.
Striving to live Aloha
finishing.com - Pine Beach, New Jersey
A. Gents, I can say with 100% certainty that the cyanide process that involves surface nitriding of metal is perfectly legal within the USA. I know this because I currently regulate 2 such processes right here in Springfield, Ohio. They both use a molten cyanide bath to introduce the nitrogen into the structure of the metal part being nitrided. Please see
www.hefusa.com and www.trutecind.comwww.parkertrutec.com
Jeff
gov't - Springfield, Ohio
January 8, 2010
Ed. note November 2022: www.trutecind.com no longer loads, but is now apparently www.parkertrutec.com
A. The Tenifer process is not exclusive to Glock. In fact SAAB of Sweden once used the same process for its cam and crankshafts. The main difference between the Tenifer and Melonite processes is a matter of splitting hairs. I believe that it is simply an EPA issue, in two separate processes, each having the same end result.
Jeremy Shank- Atlanta, Georgia
Q. Okay, so if these two processes are the same, how come I've seen Smith & Wesson firearms that are Melonite treated rust/corrode, but Tenifer doesn't? A friend of mine has carried both guns concealed and his Glock 26 never rusted, but his M&P 9 compact did? Through practical experience, I have to disagree that they are the same. They react differently when they are placed in the same environment.
Todd Heimann- Cincinnati, Ohio
2007
A. Just because they are the same finish doesn't mean they are applied the same way. Company X might have done a bad job of applying the product. Perhaps they had a bad batch of the product?
Levi Gresser- Baltimore, Maryland
A. Thanks, Levi. I believe you are right there at the heart of the matter.
Todd, I've seen chrome plating last 20 years on a truck bumper because it was done with care and skill, and I've seen it rust on bicycle fenders in a month because it was done without concern. Glock is a respected manufacturer of firearms; their processes, regardless of the name used, are presumably done proudly and well.
Regards,
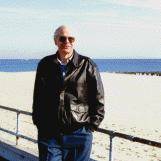
Ted Mooney, P.E.
Striving to live Aloha
finishing.com - Pine Beach, New Jersey
Q. Thanks in advance,
My question regards the Melonite/Tenifer debate and actually is quite simple. My understanding of this salt nitriding acid bath process is that it doesn't translate well to stainless alloys, that it actually weakens their ability to withstand corrosion? Would this perhaps explain why we're seeing the S&W product developing oxidation?
- Roseville, Minnesota
February 17, 2008
A. Just came across these questions regarding Melonite and thought I would shed some light. As the former engineering Manager of S & W I can tell you that we chose Melonite for several reasons, one being durability and the other that it could be used on both 4140 and 416 stainless. However, I don't recommend it for the latter because it actually removes some of the properties of the material, which ultimately could allow for rust/corrosion.
The facility we selected is located in the Mid West (no secret there) and let's not give Gaston Glock too much credit, the Tenifer finish has been used by the German automotive industry for years, including BMW and Mercedes.
I will give him credit for taking a very traditional industry and introducing a great product using simplicity and light weight materials (Original patents for many of Glock's design were filed in the 40's, years ahead of its time).
Hope this helps.
- Coral Springs, Florida
David,
Like Crazy Einar I give Gaston Glock kudos because when he put down his ideas for gun designs he didn't know anything about it ... so he didn't have any preconceived and "traditional" notions of what goes into it. Therefore he looked around and added the best technology available to do the best job.
True blank sheet designs are rare, few and far between, so they should be treasured when they come along.
- Greensboro, North Carolina
A. Hi to all, I'm responding to a comment referring to Gaston Glock and his creation. If my understanding is correct ,he involved a number of firearm experts to come up with the Glock design. It wasn't something he came upon all by himself.
Regards,
Frank....tool and die trade
- Mocksville, North Carolina USA
July 6, 2011
Q. Is anyone here familiar with austempered ductile iron (ADI)? this process uses a salt-bath process, too. The material is used for crankshafts, suspension parts and whatnot--exposed to stresses not unlike guns. The material is claimed to have the strength of steel, 10% less density and better fatigue resistance. It's easier to machine than steel. Is this used in any handgun, to anyone's knowledge?
Adam C. Sieracki- Calgary, Alberta, Canada
February 2, 2009
Q. Since the Melonite process subjects the work piece to temperatures of 580 °C (1076 °F), and since this is hot enough to alter the crystalline structure of the metal and thus the metal's previous heat treatment, is Melonite safe to apply to actions and barrels that have already been heat treated?
I have a barreled action for a bolt rifle that I'd like to have Melonited, but I'm concerned that doing so will compromise its properties.
Recommendations?
- Oakland, California
September 29, 2009
? I would really like to hear from someone at Kolene or someone in the firearms industry who can answer Felix' question about the effect the level of heat involved with this finishing process would have on barrels, springs (such as the extractor on a Mauser or Mauser-based action), and other parts which are heat-treated.
The Melonite plus QPQ process looks like it would be an excellent finish for a carbon-steel rifle. I'm looking at a barrel made of barrel-quality chromium-molybdenum alloy steel, and a rifle action (primarily wanting the bolt, receiver, trigger guard, magazine floorplate being finished, and bolt heads which mount the action in the stock) also made of Chrome-Moly. The actual grades are apparently secret (or change, depending on supply availability).
- Peoria, Illinois
A. I would never subject a rifle barrel to that high a temperature if the barrel were of the button rifled or hammer forged variety. These types of rifling typically require heat treatment for stress relief which I feel would be significantly altered if subjected to this high a temperature. A cut rifled barrel of high quality chrome moly steel might make a good experiment for someone to try, however, as an experienced gun smith, I would not want to be the first to pull the trigger in an unprotected environment. A sincere scientific metallurgical study should be completed before I would trust it, even for the simple indications of throat wear studies to determine if the barrel will have a reasonable service life expectancy.
Andy Hooker- Tyler, Texas
March 11, 2010
A. With regard to not using salt bath nitrating, on hammer or button rifled barrels - GLOCK uses salt bath nitrating on hammer forged barrels.
It is anecdotal, but where I've seen a barrel where a round was fired into an obstructed barrel (the shot after the squibb) - the GLOCK OEM barrel has never split - only bulged; while stainless steel aftermarket barrels (of the same dimensions) usually split.
- Memphis, Tennessee, USA
September 20, 2010
A. Thanks, Philip. But I don't see a real contradiction there. Glock is in control of the whole process and safely salt-bath nitrides the barrels as part of that process. That doesn't mean that it is necessarily safe to take a barrel and nitride it in the aftermarket. Sorry, I don't know whether it is or isn't.
Regards,
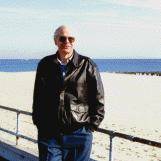
Ted Mooney, P.E.
Striving to live Aloha
finishing.com - Pine Beach, New Jersey
A. I am a technical adviser for firearms industry work, and full time weapons designer and custom rifle builder, and I can assure you that the process can be used on both Button and Hammer Forged barrels. I have personally done over 100 barrels and receivers of all three types of rifling -- cut, button and hammer forged. I have experienced no issues with any of them. My employers plant does a lot of rifle barrels for major OEM contracts so if it were a problem we would know. I have done stainless, and chrome moly, one thing I have noticed is that the process will allow to use Chrome Moly where manufacturers would ordinarily use stainless. Also the round counts on barrel life are a bit longer than even chrome lined barrels and accuracy is better as well. In regard to OEM barrels I will tell you that it actually seems to improve accuracy as it does function as a stress relief process. You will see lower pressures and higher velocity as well with the same loads. It usually allows for more powder to be loaded to get back to max pressure which in turn increases velocity even more.
It's a great boon to rifle building and should be considered for all who want a custom rifle built. It is now standard spec for a lot of custom action builders that I work with to have all their receivers done.
Let me know if I can be of further help
- Delaware, Ohio, USA
October 17, 2010
A. I can confirm 100% the statement of Mark L.
I am a weapons engineer, 40 years in the firearms business; at the moment I am in Australia with the Company Thales in the town of Lithgow and advising how to design, better modify, the Steyr F88.
11 years with Mauser, 6 with Walther, 3 with Steyr, and owner of the company BOCK known as "Bock mounts" in the US
In the last years I have made several custom made rifles and the company FEINWERKBAU in Oberndorf is doing for me the Tenifer QPQ.
The Company H&K is also bringing all their pistol slides to Feinwerkbau.
Regards,
- Oberndorf, Germany
A. More to add to the mix. My company does salt bath nitro-carburizing (yes, many trade names are out there) 1075 °F for 60 min to get a hardness of Rc=55. Many gun mfgrs. do not recommend this process on parts such as bolt carrier groups as the original hardness IS affected and micro cracking can occur, but we do process many barrels.
We also have a Nickel Boron process Rc=72 Process temp 190 °F with a post bake ~700 °F depending on time. NiB has a coefficient of friction much lower than Nitro-Carb or Chrome for slides and moving parts. Fabulous for bolt carrier groups, actions, and slides. My personal Belgian-made Browning High Power is fully coated. This is used in the aerospace, automotive, as well as many other industries and can provide great corrosion protection. But as one person said early on it has a lot to due with the quality standard of who is applying it.
- Warren, Michigan USA
![]() |
Q. Mark L & Michael V (especially, but thanks to the other responders as well), I wish this forum allowed us to publish e-mail addresses. I would like to reach both of you about doing some finish work... Perhaps a hint about where you work, so we could track you down by phone? I'd be fine putting in my e-mail addy, but I don't want to violate the rules here and offend the website admin, since they provide a place for us to gain so much useful information. Michael Arlington- Peoria, Illinois, USA February 16, 2011 A. Thanks, Michael. We've survived 23 years while countless free newsgroups, websites, and Facebook groups went defunct or became worthless spamfests because we make it hard for posters to commercially benefit from "comment spam". ![]() Ted Mooney, P.E. Striving to live Aloha finishing.com - Pine Beach, New Jersey
- Peoria, Illinois A. If people want a good free technical forum we can't have the people who are making it available for us called onto the carpet by their bosses for spending the company's advertising dollars on a site which sends potential customers to their competitors who pay nothing :-( Regards, ![]() Ted Mooney, P.E. Striving to live Aloha finishing.com - Pine Beach, New Jersey |
Q. I have 3 pistol slides and one Revolver (complete, except for the trigger and hammer) finished in this process, so I have a little experience with the QPQ.
My question is related to this:
I'm building a custom rifle (6.5 x 55 s) with a Mexican Short Action Mauser model 98. I want to know if the action (DWM) can be put through this process with out harm to it.
Thanks in advance.
- Naucalpan, Edo de Mex, Mexico
February 25, 2012
Q. What is the depth of the nitrocarburized layer in the barrel's bore?
Thank you
Filippo
- rolo,re,italy
February 25, 2012
A. Hi Filippo.
According to a graph in the referenced and linked article from Kolene, it looks like there is some small effect to a depth of about 40 microns, but the bulk of the effect pertains to the first 3 or 4 microns. I think some people use the rule of thumb that it's about 5 microns thick.
Regards,
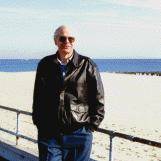
Ted Mooney, P.E.
Striving to live Aloha
finishing.com - Pine Beach, New Jersey
Q. Does the rust proofing resistance of the Tenifer or Melonite treatment process result from the fact the Fe is tied up with N and C as an ironcarbonitride and therefore not available to react with O2 to form rust FExOx?
Gary Hoff- Middletown, Ohio
April 16, 2012
A. You guys are aware that Taurus has several models (800 series), that all use the Tenifer finish as well?
Eric Hensen- Tampa, Florida, USA
Q. The Tenifer type finish seems to have great protective properties. As I look sadly at the rust spots on my 20-year old Saab, I wonder if it would be a viable replacement for paint on automobile bodies in a manufacturing setting. Have any auto makers considered it as an alternative to paint?
Bob Newton- Warren, Rhode Island, USA
September 5, 2012
A. Hi Bob. Salt bath nitriding is a great finish but we shouldn't take it out of context, and thereby attribute almost mystical power to it. Remember that the alternative to salt bath nitriding for firearms is black oxiding, which offers virtually zero corrosion resistance, yet is acceptable to some gun owners who lovingly clean, care for, and oil their guns. Firearms have it pretty easy!
Salt bath nitriding is far better than black oxide, but that doesn't make it better than auto paint. Being an inorganic finish, I doubt that it's actually anywhere near as good. One place on autos where salt bath nitriding is often used is on the piston of those little air springs that hold up hoods and hatchback windows. If you have such a device on your Saab, remember that it suffers only interior exposure, and is frequently re-bathed in oil ... and even then it may not be still perfect after 20 years.
Regards,
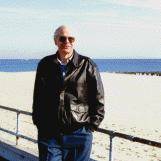
Ted Mooney, P.E.
Striving to live Aloha
finishing.com - Pine Beach, New Jersey
! Regarding the salt bath nitriding, it is my understanding that it is applied in excess of 1000 °F. Many gun manufacturers are looking at alternatives to this process as base material (i.e 4140) core hardness drops to an unacceptable level 36HRc. Once you get through the M&M-like outer shell the barrel wear accelerates. I have been told by one manufacturer that the bores go out of round. There goes your accuracy.
Lou Lechner- Chicago, Illinois, USA
November 8, 2012
What is the Glock slide/barrel finish ?
Q. There seems to be much debate on what Glock uses to finish their slides with. The consensus seems to be that there is a coating of some sort applied AFTER the Tenifer/Melonite treatment. I believe the Tenifer/Melonite is the resulting finish.
Can anyone help shed some light on what process Glock uses for the final finish on the slide and barrel ?
Thanks !!!
Bill
Gun nut - Canton, Michigan, USA
November 28, 2013
A. Hi Bill. I believe it is possible to apply a dry film lubricant coating on top of a salt-bath nitrided coating; such dry film coatings have been applied to firearm components, so that's my best guess. I hope that's enough info, because we sometimes walk a fine line here in trying to offer as much technical content as we can, while also carefully avoiding crowd sourcing of industrial espionage. If someone knew the fine details of what some company did, we probably couldn't post it anyway :-)
Regards,
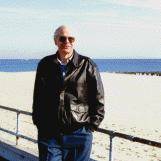
Ted Mooney, P.E.
Striving to live Aloha
finishing.com - Pine Beach, New Jersey
Q. Ted, thanks for the info !
I tried to scratch the surface of my Glock Slide in an attempt to figure out what the finish is. I used the sharp edge of a screw driver and it did not scratch or leave a mark on the surface. Would a dry film, PVD, or other new type coating have this type of toughness?
Bill
- canton, Michigan, usa
December 14, 2013
Q. I plan on having a Glock slide milled for a RMR Red dot sight.
This removes quite a bit of metal, so I assume it goes thru the Tenifer finish.
What might be a viable treatment for the exposed metal?
- Carlinville, Illinois, USA
December 15, 2013
I was looking on this site for info about Glock's replacement for Tenifer. Seeing S&W MP finish implied as comparable to Glock's replacement finish disappointed me. I had a .40 M&P on the slide it said "stainless steel." I sometimes like to keep a pistol in my trunk. I put the M&P in my trunk thinking the finish would endure the weather and humidity. Two or three weeks later I checked it out to find several patches of rust on the slide. I sold that gun and put my Glock 34 in my trunk. I check on it about every two or three months. No rust on the slide or barrel. Ever. Nothing beats Tenifer.
- Shawnee Kansas USA
December 5, 2014
A. Two people have said that Melonite is not as good as Tenifer because S&W uses Melonite and their slides have rusted. Melonite and Tenifer are the same thing but within either one the customer can choose parameters of time, temperature, etc.
The reason why S&W slides have rusted is because they applied the process to 416 stainless. 416 stainless can have reduced corrosion resistance when certain types of nitriding are applied. There are ways to fix this, and it seems like S&W did.
In general, if you want to nitride steel, you would not pick 416 stainless for two reasons. One is that it costs more than 4140 with no benefit. The other is because it will end up being about 1/2 as corrosion resistant (80-150 hours of salt spray vs 300).
Glock applies a spray-on finish over the nitrided steel. I assume they do this both for an even look and for additional corrosion protection. I have seen many people call this a Parkerized finish. It is paint, not phosphate.
- Boston, Massachusetts, USA
July 1, 2015
RFQ: I recently purchased a S&W 696-1 revolver manufactured around 1998.
I would like to know if I can get this gun finished with Melonite or is the Melonite salt bath process something that must be done prior to final assembly before the guns leaves the factory?
If it can be refinished, what is the best way to find a reputable company that will do a good job? A fair amount of internet searching have not helped in finding people with experience in having guns refinished with Melonite.
- Boston, Massachusetts
January 2, 2018
Ed. note: This RFQ is outdated, but technical replies are welcome, and readers are encouraged to post their own RFQs. But no public commercial suggestions please ( huh? why?).
A. Hi David. We appended your inquiry to a thread which offers a lot of insight into your first question.
Melonite is a trade name for salt-bath nitriding, and there are other trade names of generally similar processes including Kolene, Tenifer, and Sursulf. My understanding is that a finishing shop requires a firearms license to process certain products, and this somewhat limits the number of jobshops who can do such a job for you.
Regards,
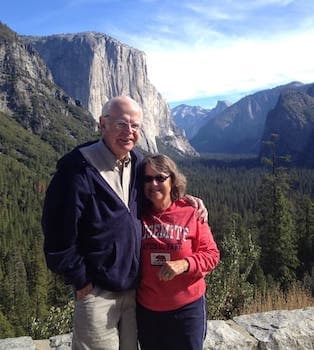
Ted Mooney, P.E. RET
Striving to live Aloha
finishing.com - Pine Beach, New Jersey
Q, A, or Comment on THIS thread -or- Start a NEW Thread