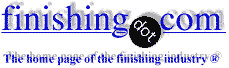
-----
4130 Chromoly -- what are its properties (and meaning)?

Q. I am generating the bill of material and fabrication process for a large "modern, organic-shaped" Chandelier.
There is a limit to how much the ceiling can hold. We are considering using Chromoly due to its strengths.
My only concern is how does Chromoly polish and how well does it hold its polish.
- Brooklyn New York
October 28, 2022
A. Hi Rob. Chromoly should polish just fine (even plain carbon steel polishes fine). But Chromoly is not stainless steel, it's just a low alloy higher strength carbon steel, which means it is not much better at resisting corrosion and rust than plain steel.
It's probably not going to be well maintained, so I'd strongly consider lacquering or clearcoating it.
Luck & Regards,
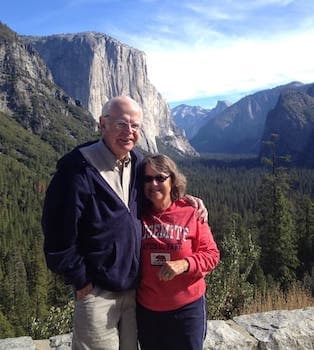
Ted Mooney, P.E. RET
Striving to live Aloha
finishing.com - Pine Beach, New Jersey
⇩ Related postings, oldest first ⇩
Q. Any idea where I can find out properties on AISI 4130 chromoly, I have been looking on the net for ages and had no luck...help! Thank you.
Richard T Andrews- Lancashire
2002
A. Richard, remember that 4130 is a chromium-molybdenum steel. Roughly 1% Cr, and 0.2% Mo. So if you look in Matweb or Efunda under "steels" or search under "4130 steel", your efforts will likely be more fruitful.
Enjoy!

Lee Gearhart
metallurgist - E. Aurora, New York
A. Properties of 4130 vary according to their process routine; the method by which the item was produced. If it is tubing you are referring to the typical properties I can provide you: they are easily obtained by looking at ASTM A519 - Seamless Mechanical Steel Tubing (American Society for Testing and Materials)
Mark L. Jones- Valparaiso, Indiana,USA
2004
Multiple threads merged: please forgive chronology errors and repetition 🙂
Q. I am taking fab/weld here at Lane Community College in Eugene, OR, USA, and I need to know (because of a friendly debate on a message board, and for general knowledge) what do the numbers stand for in "4130 ". I have been riding BMX bikes (yeah, the "little kids' bikes") for a few years, but the kind I ride are super expensive hehe. Now, go to K-Mart or Wal-Mart, and most of the BMX bikes there are made of 1020 high tensile steel (which is what most of us use here in the shop). But, you purchase the good stuff, the stuff you can actually use and abuse hehe you will find that most of the stuff is made of 4130 steel, so in other words, when it comes to BMX, 1020 is bad, and 4130 is good.
Now I know that both materials are derivatives of steel, and "" is chromium, molybdenum, and the rest is steel, correct? SO, the thing that I want to know, and it helps in the discussion on the message board, is what do the numbers "4130" stand for? And really, the main question on the message board, is what is the difference between "100% " and "4130 "?
Jimmy SpoorStudent - Eugene, Oregon
2004
A. 4130 is a designation for a steel alloy that contains chromium and molybdenum among other elements. The exact composition range is defined in the standard SAE J404 "Chemical Compositions of SAE Alloy Steels".
1020 is another steel alloy, but since it does not contain appreciable amounts of alloying elements other than carbon, silicon, & manganese, it is called a carbon steel, not an alloy steel, and its composition range is defined in the standard SAE J403 "Chemical Compositions of SAE Carbon Steels".
So, to answer your question, there is no difference between "100% " and "4130 " except that one description refers to an industry standard and the other one is pretty much meaningless.
Toby PadfieldAutomotive module supplier - Michigan
A. The 4130 is a code of the American Iron & Steel Institute and defines the approximate chemical composition of the steel.
The "41" denotes a low alloy steel containing nominally 1 percent chromium and 0.2 percent molybdenum (hence the nickname ""). The "30" denotes a carbon content of 0.30 percent. In addition, as normal constituents of plain carbon and low alloy steels, there will be around 0.2-0.5 percent silicon, 0.5-1.0 percent manganese, and well under 0.1 percent of each of a dozen or so other elements whose presence is unavoidable, in a few cases deliberate, and generally not harmful. The remaining 97-98 percent is iron (Fe).
There are many tens, perhaps hundreds, of different steels defined by that AISI 4-digit code system. The code does not specify any particular mechanical properties, only approximate chemical composition. For any particular grade (composition) (AISI number) of steel, the mechanical properties depend on what heat treatment has been applied, and what (if any) cold work has subsequently been done.
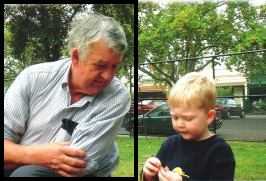
Bill Reynolds [deceased]
consultant metallurgist - Ballarat, Victoria, Australia
We sadly relate the news that Bill passed away on Jan. 29, 2010.
A. The chromium content is approximately 0.8-1.1%. The carbon content is nominally 0.30% and with this relatively low carbon content the alloy is excellent from the fusion carbon content the alloy is excellent from the fusion heat treatment. The actual breakdown of 4130 alloy steel is as follows:
Carbon 0.28 - 0.33
Chromium 0.8 - 1.1
Manganese 0.7 - 0.9
Molybdenum 0.15 - 0.25
Phosphorus 0.035 max
Silicon 0.15 - 0.35
sulfur 0.04 max
Some other facts regarding this material:
Applications
Typical applications for 4130 low alloy steel include structural use such as aircraft engine mounts and welded tubing applications.
Machinability
This alloy is readily machined by conventional methods.
Machinability is best with the alloy in the normalized and tempered condition. Although the alloy may be machined in the fully heat treated condition, machinability becomes more difficult with increasing strength (hardness) of the alloy.
Forming
Formability is best in the annealed condition for which the ductility is very good, Bend radii of 1t on annealed sheet material may be made.
Corrosion Resistance
4130 is a steel and as such is not corrosion resistant. In corrosive environment the alloy should be given a protective coating.
Welding
4130 alloy is noted for its weldability by all of the commercial methods.
Heat Treatment
Heating at 1600 °F followed by an oil quench will harden the 4130 alloy. For best results a normalizing pre-hardening heat treatment may be used at 1650 to 1700 °F followed by the 1600 °F soak and oil quench.
Forging
Forge at 2200 °F maximum down to 1750 °F.
Hot Working
4130 in the annealed condition has excellent ductility.
Thus it is usually not necessary to do hot working to form parts. If hot working is needed it can be done in the range of 2000 °F to 1500 °F.
Cold Working
Cold working by conventional methods is readily accomplished on this alloy.
Annealing
4130 (and most of the other low alloy steels) may be annealed at 1550 °F for a time long enough to allow through heating of the section size. It should then be cooled in the furnace at a rate of less than 50 °F per hour down to 900 °F, followed by air cooling from 900 °F.
Tempering
Tempering is done to restore some of the ductility that may be lost after the hardening heat treatment and quench. Alloy 4130 is tempered at between 750 °F and 1050 °F, depending upon the strength level desired. The lower the tempering temperature the greater the strength.
Other Comments
The 4130 alloy is a through hardening alloy and should not be case hardened.
If you have any other questions or comments regarding steels of any type, I will try to answer you -- a bored Tool and Die / Toolmaker that has worked with many different materials and applications over the years.
- Webster, New York
I just want to respond to the reply from Jack Demcovich. That was a very excellent answer. Thanks.
The tensile strengths, annealed, quenched, and tempered would be nice to know. Otherwise, I think you covered it all.
project engineer - Franklin, Tennessee
February 19, 2009
by Chimonas & Wang
on AbeBooks
or Amazon
(affil link)
Q. Wow! You guys are amazing! Great information Mr. Demcovich. Some guys here are debating whether or not powder coating will effect the steel on a bicycle. They claim a frame broke after being powder coated. Can we powder coat a 4130 bicycle frame without the oven temperature (350 °F to 400 °F for 10 min to 30 min) adversely affecting the steel? What about a cheaper brand bike with 1020 steel? I see the tempering process is twice the temperature as the powder coating oven, but could it have any ill affect? My guess is, No. A manufacturer doesn't re-temper a frame after it is welded do they? Certainly the welding would affect the steel's strength before the oven. I think, simply, their paint cracked and not the steel. Maybe I'm wrong. Please advise.
Steve Seagravescommercial painter - Buildings - Douglasville, Georgia
May 9, 2009
A. They powder coat 4130 aircraft fuselages with no other heat treatment so I'd have to say "yes".
Dan
- Olympia Washington
Multiple threads merged: please forgive chronology errors and repetition 🙂
Help with 4130 info for bicycle manufacturing
Q. Hey guys I have been reading your posts and I can tell that they are full of information and I need serious help.
In 2 months or so I am going to start my own bicycle manufacturing company in Mexico and I really have to know everything about and especially its tempering process so I could process it the best way possible.
Also I have to know which welding process is the best and the cheapest, also I have to know if the tempering process involves any oils for hardening the metal.
Thanks
- Mexico
October 16, 2009
A. Hello Abraham,
In my opinion you absolutely need a consultant in steel fabrication, heat treatment, automated welding, etc. This forum is basically dedicated to finishing questions. Should you have any problems later on when painting your bicycles, post them here. [The] Mostly Metallurgy [category on the index] is for specific and rather simple questions.
Monterrey, NL, Mexico
Q. Can anyone suggest which Reynolds' cycle tubing would be the closest equivalent to 4130? Or are they all? I read somewhere that Reynolds 531 is the same, but my understanding is that Reynolds 531 was always used in lugged tubing only and could not be welded.
Thanks,
- London, UK
November 5, 2009
Q. How about blasting the 4130 to remove paint? What type of medium is best? Will steel shot damage the 4130 tubing?
Jason Doscher- Benson Minnesota USA
December 9, 2010
Q. As long as we're on the 4130 topic ... I have been considering making a knife. It seems to me that 4130, an old friend, would be a good choice, yet none of the knife makers I've read about use it. Any thoughts on why?
I have already formed a blade and I'm ready to harden and temper it. Additionally, any thoughts on that in the context of a knife blade would also be greatly appreciated.
Thanks.
PS great post Dan! Hope you're still around!
- Eugene, Oregon, USA
June 19, 2011
A. Hi, George.
A. Please search our site for "knife making" for several very interesting threads which include great info about what makes for a good knife blade. If you are not finding any info about making blades from 4130 (we have none here), I suspect that it is because it doesn't make a great blade, rather than that no one ever tried it. Some pretty special properties are required of great knife blades -- like a combination of hardness (to hold a good edge), and toughness (to bend and not snap), and most metals lack that combination.
Regards,
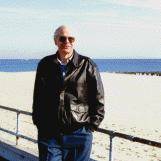
Ted Mooney, P.E.
Striving to live Aloha
finishing.com - Pine Beach, New Jersey
⇦ Tip: Readers want to learn from your situation;
so some readers skip abstract questions.
Q. Hello, I would like to know if Steel 4130 and 4140 could be affected by Alkaline cleaners.
Thank you,
Bita - Montreal, Quebec, Canada
March 26, 2012
A. Hi Martine.
That's pretty vague, so you probably won't get definitive answers. But I'd say that in general alkaline cleaners have very little effect on low alloy steels like 4130.
Regards,
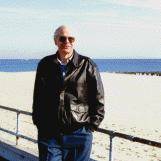
Ted Mooney, P.E.
Striving to live Aloha
finishing.com - Pine Beach, New Jersey
Q. Hallo,
Another question regarding 4130. I am bending 1 3/8" .065" wall tubing into a long bend with about a 25" radius, over about a 5' length, and this I am doing cold.
There is a fair bit of stress as only one end is fixed, and the curved piece does flex. So my question is as follows:
Should I do some sort of heat treatment, post bending, to retain the strength to ensure it always returns to my initial radius? Or is it better to just leave as is as I did, bend it cold? I have been advised to heat it up to red heat and then let it air cool, but I would like more opinions.
Many thanks,
Jonathan
- London, England
June 13, 2012
A. Hi Jonathan.
Steels are elastic up to a point. So if you try to bend them a little while cold, they spring back. But if you exceed the "elastic limit", they stay deformed. It can be tricky to exceed the elastic limit (or yield point) without exceeding the ultimate strength and causing any breakage/cracking though. But you are not going to be able to get it to take this "set", cold, without a "fair bit of stress" (exceeding the yield point). Typical figures for annealed 4130 are probably about 52,000 PSI yield strength, 28% elongation (meaning it will definitely break before it stretches that much), 81,000 PSI ultimate strength. You are probably okay with your 25" radius if you are using a proper tubing bender that discourages kinks on the inside of the bend ... but I have no actual experience in this and have done no calculations; it just "sounds" okay. Note that you haven't told us what you are doing! It's one thing to say "it'll probably be okay" if you're using it as as a handle for your own lawn mower, but it's quite another thing if it's a vital aircraft component :-)
If you bend it hot, it will not spring back at all. But you should probably research the annealing of 4130 to make sure you are following the right protocol, which involves slow cooling in still air, and no quenching.
The third approach is to cold bend it, then heat it and anneal it. This probably leads to a somewhat safer component because it will now be able to bend, i.e., it will now have the cold working stresses relieved and some ductility restored. But my experience is in finishing, not in bending and heat treatment, so take this as an intro to theory, not as an expert opinion on your design :-)
Regards,
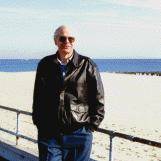
Ted Mooney, P.E.
Striving to live Aloha
finishing.com - Pine Beach, New Jersey
Sizing the tubing for a Rickshaw
Q. Hi I have a question... I am trying to build a human pulled Rickshaw and was wondering what size tubing I would need to hold up to 1000 lbs capacity? Another question: if this tubing is so very strong how would I go about bending it? I am trying to build this with my 15 year old son for an experiment at school and I am his mother, so easy and specific information would be so helpful:) Thanks so much for your time.
Evone Kent- show Low, Arizona, united states
December 29, 2014
A. Hi Evone. I read "In Search of Excellence" so many years ago that my memory has distilled it down almost to what I considered it's most important single lesson, which ran something like this: "If your restaurant wants to offer good salads while meeting a low price point, search for the crispest lettuce, not for the cheapest artichokes". The relevance is that a science project that is within his educational level can turn out great even if it seems a bity trivial at first, because we can always go deeper on any aspect that we find interesting. But a project which is beyond what he has the engineering background to tackle might turn out more like a child's review of rickshaws than a science-based project. Unfortunately he's not ready to size that tubing for the 1000 lb. loading, and won't be before completing more years of high school and then the first 2 years of engineering college :-(
The required calculations are too far beyond his skills, so all you could do instead is look at similar devices like other rickshaws and try to duplicate their elements. But a large diameter but thin walled tube, like Jonathan's 1-3/8" dia. x .06" wall tubing will give a great "strength-to-weight ratio", which is what you'll want for a human powered rickshaw.
Please look at my recently updated response to Jonathan, above, for an explanation of how you bend something that strong: you either heat it red hot so that it's soft, or you impose very high stresses on it that exceed the yield point of the steel. Sorry that I don't have easy answers.
Best of luck, and please tell us more about the rickshaw project if you stick with it!
Regards,
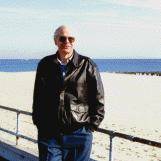
Ted Mooney, P.E.
Striving to live Aloha
finishing.com - Pine Beach, New Jersey
What is the strongest most flexible steel?
Q. Hello, which is better chromium or molybdenum?
Jeff SanchezBike rider - L.A. California
May 15, 2015
A. Hi Jeff. Bicycle frames are not made either of chrome nor molybdenum. They are made out of steel with various but small amounts of chrome and/or molybdenum and other alloying ingredients (although they can also be made of aluminum, carbon fibre, or titanium instead). We appended your inquiry to a thread about Chromoly to give you a basic understanding of it, but the strongest steel will not be the most flexible, and it's very difficult to figure which of two materials is best by starting from the sales pap offered by a bicycle manufacturer :-(
Spend a few paragraphs explaining in some detail what is on your mind, and your actual situation, and we can probably help. Good luck.
Regards,
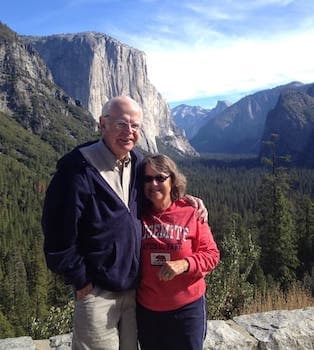
Ted Mooney, P.E. RET
Striving to live Aloha
finishing.com - Pine Beach, New Jersey
Q. I wanted to understand how .01 of chrome and .002 of molybdenum could make such a difference in the way the bike rides.
My hunch is that it has something to do with the flexibility not the weight. Do they use 4130 for railroads?
My main question is which metal will give me the propulsion for my pedal power.
Bike rider - L.A. California
A. Hi again Jeff. Small amounts of alloying material can make a big difference. Low carbon steel (<0.2%) isn't hardenable, but add a smidgen more and you have hardenable medium carbon high strength steels because the whole crystal structure can be different. Yes, chromium and molybdenum allow some properties of flexibility and toughness that probably can't be obtained from a carbon steel, and I do believe that railroad tracks sometimes are chromoly or similar steels, but there are literally thousands of carbon and low alloy steels.
Although I'm neither a metallurgist nor a mountain biker, I probably can't agree with you that those small amounts of chrome and molybdenum are the main parameter controlling the flexibility of the bike though. It probably has more to do with the thickness of the tubing, the heat treatment regimen, whether the frame is constructed of tubing mitered and welded together vs. with tube & lug design, etc. I think the actual situation is more like this:
Renoir and Van Gogh were so skilled that they probably could have done impressive art by drawing with crayons on brown paper lunch bags, but they chose instead to use the best materials available to them. Similarly, bike designers could probably make a pretty competitive bike with carbon steel instead of tubing but they don't because they want to make the best bike they can within the cost range.
I think the way to pick a good frame material is to pick a respected brand bike with lots of good reviews, and trust that their engineers will pick materials well. It would be difficult for an expert metallurgist to predict what frame material would perform better. If you read a couple of books about bike frames, a couple about steel metallurgy, and acquire a lot of trail miles, you might try to figure out what steels are good from first principles -- although I don't think it will work. Trying to pick a frame material based on the manufacturer's sales pap ... impossible. Best of luck.
Regards,
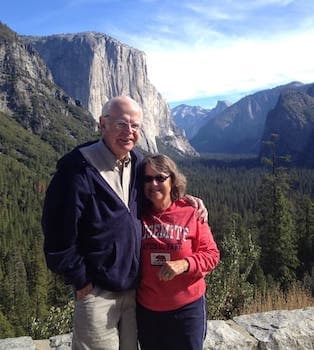
Ted Mooney, P.E. RET
Striving to live Aloha
finishing.com - Pine Beach, New Jersey
A. For 4130 Steel, I think you could check this link: www.astmsteel.com/product/4130-steel-aisi-25crmo4-7218-scm430/, you have detailed 4130 alloy steel's properties. And you could also refer to ASTM A29 standard, which 4130 steel belongs to.
Jeremy HeOtai Special Steel Co Ltd - DongGuan City,
----
Ed. note October 2020: Jeremy's link is now broken.
Q. I need metal tubing that won't crack when hammered almost all the way flat yet is tough enough to handle being pulled through eighth inch cuts in concrete to apply hot tar sealant. Is it ? If not ... ideas ?
Michael longshaw- Salt Lake City, Utah, Usa
December 22, 2015
Forming the ends of a tube of 4130
Q. I'm looking for information on forming the ends of 4130 tubing. Is it necessary to heat the tube ends prior to flattening or forming, see pictures attached. What temperatures are recommended to prevent cracking? What type of unit could be used to form the ends?
- Grand Rapids Michigan
September 7, 2016
Q, A, or Comment on THIS thread -or- Start a NEW Thread