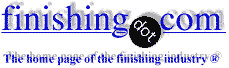
-----
Sodium hypochlorite (bleach) piping problems
Q. Hi. We are converting our water plants to bleach from Cl gas.
The problem we are having is on our threaded connections. Currently we use the dope & tape method on our PVC connections, but we are constantly chasing the same drips. Is there a tape or pipe thread sealant or combo that works better? Thanks.
- Orlando Florida
April 12, 2021
A. We've had problems over the past 20 years with a hypochlorite system. Depending on how your system is used/pumped ...
Teflon tape only holds until you get some off gassing; then it'll start leaking.
We used #2 non-hardening Permatex form a gasket for a few years and it would hold up ⇨
We've found that Tuf-set brand
⇦ on
eBay or
Amazon [affil links]
works pretty well as long as you have dry (no hypo) and clean threads.
If this is a new system, just a heads up: after about 5-10 years your PVC will become brittle -- not to the point of failure but where hairline stress cracks may be found during walk-thrus.
Hope this was some help.
- Maryland
May 18, 2022
⇩ Related postings, oldest first ⇩
Q. This question may appear as a multiple part question, but it really addresses a single problem we are having with PVC glue / welded joints in a series of sodium hypochlorite PVC pipes.
1. Is it recommended to use regular Teflon tape to secure threaded PVC pipe and fittings or is there a similar product that can withstand the high acidity^alkalinity and corrosiveness of sodium hypochlorite ?
2. For glue welded connections, is PVC primer and glue, that is typically used for PVC pipes to carry water and waste water, strong enough to withstand the corrosiveness of sodium hypochlorite ?
We have noticed that many of our leaks are occurring at the glued joints and sometimes at the threaded joints. Any one in a similar industry ? How do you weld PVC pipe together? We use Sch. 80 PVC
2004
![]() |
A. Hi Dan! ![]() Freeman Newton [dec.] R.I.P. old friend (It is our sad duty to advise that Freeman passed away 4/21/12) A. Check this link out. It might help. www.finishing.com/library/newton/cementingPVC.html ![]() Trent Kaufman electroplater - Galva, Illinois A. PVC, and the glue used to make joints, can fail after long exposure to highly alkaline chemicals (like hypochlorite, which is alkaline, not acid). You can use polypropylene pipe or tubing, or stainless steel. ![]() Jeffrey Holmes, CEF Spartanburg, South Carolina |
A. Hi again Dan,
What Jeffrey says may be true ... I don't know ... but I do know that PROFESSIONALS, such as we, as top notch thermoplastic fabricators were, never to my knowledge had this problem.
But when we encountered a 'nasty' condition, such as 93% sulfuric or strongish nitric, we would add a weld bead to the joint.
Particularly on larger pipe & fittings, when you cement them, there is a minuscule gap which the cement is supposed to fill. If, after one year, you were to cut open a cemented 10" dia fitting in half, you could see the cemented line ... and with your finger nail, you could indent it very slightly, too ... but that's with large fittings.
The proper PVC cement will fill up the gap successfully.
But Jeffrey, you said use stainless for alkalies. Yuck. Yes, PP would be OK but the cost of buying it and the cost of installing it would be much higher ... and unless UV pigmented, then outdoors it would be nbg.
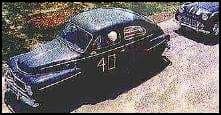
Freeman Newton [dec.]
R.I.P. old friend (It is our sad duty to
advise that Freeman passed away 4/21/12)
A. I've been wrestling with this problem for many years, mostly in trying to fix problems created before I became involved.
The only product I have ever found to be suitable for use with the hypochlorites is IPS Weld-On 724 [←affil link]. Last summer I spoke with the folks at Oatey to see if they had anything suitable and they offered 31113, 31114, & 31115. Later, I downloaded the MSD sheet and that document specifically states that the Oatey product is incompatible with "Acids, oxidizing materials, alkalis, chlorinated inorganics (potassium, calcium and sodium hypochlorite), copper or copper alloys."
My understanding is that the problem becomes more apparent on larger diameter pipes because the glues for larger diameter pipes have "inert" filler materials that are intended to fill the (larger) gap on these fittings. Apparently, the chlorinated compounds attack the filler materials leading to joint failure. However, I've seen 1/2" thru 2" pipe fail due to incorrect cement as well.
Last summer, I worked with a contractor to salvage a rework project on which they used Oatey 31015, specifically not approved for this service. A contact of mine with a company that makes sodium hypochlorite generation systems steered me to 3M Scotch-Weld Acrylic Structural Plastic, Part Number DP8005 ⇨
After the joint is made with the wrong sealant, you can place this over the top of the joint and it is supposed to make the joint leak tight. You just clean off the excess primer & glue before applying the 3M product. I haven't checked back with that client to glean how well things are performing, but since they are not calling me, I'd say that bodes well.
I happen to be looking for alternatives to the IPS product I noted above and this thread caught my eye. I have another project kicking off and I like to have more than one alternative in the specs. If any of you know of anything, please let me know.
Damien Stella- Anchorage, Alaska
A. In my opinion, uPVC Pipe with EPDM rubber ring joint for straight connection and k-Type socket PU coated Ductile Iron Fitting for Bends will solve the problem.
I welcome your opinion on this solution. Classical Solvent Cement Joint cannot easily react with heat expansion and other vibration factors.
Cheers~
- KL, Malaysia
2007
A. When dealing with bleach (sodium hypochlorite) of 9-15% concentration its always best practice to follow the manufacturers specific instructions to the letter while making the solvent welded joints to include cure times. When pressurizing the bleach, don't get excessive or you can expect to have many leaks as it will eventually eat the glue. Also, avoid threaded connections like a heart attack! Teflon tape will hold on a no/low pressure threaded connection, but I have found that a simple hobby glue called E-6000 ⇨
works best on mid to high pressure systems but also needs 24-48 hours cure time for best results.
Also, stainless steel and ductile iron are not a cost effective choice due to the fact that the bleach will eat the pipe extremely quickly, try to stick with thermoplastics as much as possible.
hope this helps:)
- Burlington, Kansas
February 26, 2008
Q. To Chris Smith in Kansas: Can you provide examples of where you have you used the E6000 adhesive [←affil link] in a 12% hypochlorite application? How long have these systems been in service without leaks? I have a project coming along that will involve trade solution product and I'd like to have some evidence to offer the client before I propose using a product not generally considered for use in this industry.
Damien Stella [returning]- Anchorage, Alaska
April 10, 2009
A. Damien Stella, I work with 10% and 12.5% Bleach solutions on a daily basis doing water treatment for Wolf Creek Nuclear Power Plant. We routinely used E-6000 [←affil link] on all threaded PVC and plastic pipe joints in our old Bromination system as the pressure that we had to over come was approximately 150 PSI. we saw far fewer leaks from the threaded joints using this hobby adhesive than any other thread sealing compound that we could get on the market. we have a newer system installed now that is a low pressure Neat feed system that injects chemical at less than 5 psi and the E-6000 [←affil link] is still in use as we have found it to be the proven to not leak. we also no longer use diaphragm pumps as they would literally hammer the system to a point where it would leak. our new pumps are gear driven PULSAFEEDER Eclipse series pumps.
Also, if money is not an issue with your upcoming project, you might check into socket thermo welded Kynar plastics, the Kynar (PVDF) pipe is currently used on our system for the delivery piping and when thermally welded correctly will not leak because the plastic for both the male and female parts of the joint are melted and then pressed together bonding them permanently. hope this helps
Chris Smith [returning]- Burlington, Kansas
Q. Chris Smith, have you actually installed the PVDF systems and placed them in service? A couple of years ago, I read good things about PVDF, then more recently learned of severe failures.
Would appreciate knowing your experience with that.
- Anchorage, Alaska, USA
November 1, 2010
A. Here is my 2 cents worth, my company has been involved with the installation of any number of chemical systems requiring piping fabrication and can advise the following.
If you pipe a Hypochlorite system in metal it is only short term compatible with either Titanium or Tantalum anything else will just dissolve very quickly.
With regards to making a long term strong Solvent Welded joint on PVC-U use a product made by Tangit called Dytex using both the Solvent and Adhesive. We have done many strong Acid & Alkaline systems with excellent results.
The trick is to ensure you follow the process to the letter for the best long term results, we have found that the US grade of schedule 80 pipe and fittings gives the best results over the metric equivalent as this has proven to have some issues.
Hope this helps.
In answer to your query about PVD-F material we use this material extensively and have found it to be utterly reliable. The last major project involved Hydrofluoric acid at 95% concentration to a 10 kl storage tank and then to a distribution mixing tank farm.
This system has been in approximately 5 years with a continuous vacuum alarm system as all the piping runs outside the decanting room are in Double containment.
We perform yearly pressure tests on the outer containment system +GF+ Contain-It Plus and no issues have been detected, this system is in daily use.
We have also just recently completed an UltraPure water system at a NANO facility that uses heat sanitization fully IR Welded fabrication and Triclover joints without any issues.
Again the trick is to follow the process to the letter for the best results, with failures I have been asked to investigate over the years 98% of the time it is Installer error without doubt.
The smallest seemingly insignificant oversight can mean a complete failure of the system as a result; think twice act once is what I always tell my guys.
- Melbourne, Australia
November 10, 2011
![]() |
Q. Good day to all... can help me to know if possible to glue the PVDF materials. Thank you. Freddie Andico- Manila, Philippines March 3, 2012 A. Hi Freddie. I think the implication of Chris Smith's posting was that thermal socket welding is possible but gluing isn't. Regards, ![]() Ted Mooney, P.E. Striving to live Aloha finishing.com - Pine Beach, New Jersey March 6, 2012 |
A. Responding to many of the questions posed about PVC and PVDF used in transport or storage of sodium hypochlorite.
PVC as a material is in fact resistant to high concentrations of NaOCl. Leaks occur at the joints where glue is used. The industry has developed special formulations of glue for use with bleach, but the lifetime expectancy is still low.
Tank fabricators typically do not use glued joints since they are making open top or vented storage tanks out of sheet (like plywood) for bulk storage. The fabricators heat weld the joints using an extrusion gun which is similar to a glue gun; it heats up PVC rod which is fed into the gun, then extruded over the two joining pieces. The thermally fused bond is now resistant. This is not recommended for pipe installations because the cooling time of PVC is too quick and the chlorine gasses that are put off can be hazardous to your health.
PVDF is also a temporary (and costly) solution for transportation of bleach, as the material is broken down by the bleach.
Polyethylene (PE) can be used for such transport. My company manufacturers a PE piping system for transport of high concentrations of sodium hypo. The product is called Chem Proline. Not all PE can be used for NaOCl. Certain resin advances have allowed us to engineer this product specifically for use in bleaching applications. PE pipe is joined similar to PVDF, using heat and not glue.
Thermally fused PE is a fairly inexpensive product. Mechanical joints (threads) should be avoided as well. PVC or PVDF or PE will all tend to leak at the mechanical connections, regardless of how much PTFE tape you use. Permanent installation methods such as heat fusing should be used whenever possible to keep the integrity of the piping system.
- Malden, Mass, USA
June 11, 2012
Q. In reading your responses, do you have a recommendation for a thread sealant. I have a 1" kynar water educator that is connected to a domestic water line. When the domestic line is opened it will suction a 93% sulfuric acid solution into the system to control the ph level. The suction fitting is a Sch. 80 PVC male adapter. We have tried different teflon tapes to wrap the threads, but as soon as the system shuts down a leak occurs at the threaded connection. Any advice?
Thanks.
- Texas USA
March 5, 2013
A. I installed a T-Chlor system with schedule 80 PVC and called Oatey to ask about what type of cement to use for sodium hypochlorite. They told me to use EP42 (Oatey # O30329 Lovoc Gray Cement).
As a side note I bought a stick of CPVC pipe to use because the plumbing supply place didn't have any schedule 80 PVC. They said it would work with the schedule 80 fittings. I mentioned that to Oatey and they said definitely do not use it with schedule 80 PVC fittings.
- Elk Mountain, Wyoming, USA
April 10, 2013
A. I keep reading all of the answers and can't believe that nobody has really recommended CPVC. Corzan has a special formulation of CPVC that works perfect for sodium hypochlorite. There was one response that said he used IPS weldon 724 [←affil link]. Again that's the perfect cement. This was specially formulated for waste water and water treatment plants for chemical applications such as sodium hypochlorite.
Most of the time pipe fitters and plumbers use the wrong installation practices when solvent welding joints together.
There is a code ASME B31.3 that certifies pipe fitters and plumbers to install plastic pipe and fittings. The procedure tests 4" PVC schedule 80 pipe to 750 PSI. More than twice the recommended pressure rating for 4" schedule 80 pipe. Some cities and companies will not let pipe fitters and plumbers install plastic piping in their facilities unless they have an ASME B31.3 certification card. I myself have taught over 1000 people on these same procedures.
Corzan CPVC with IPS 724 cement [←affil link] is the only way to go.
industrial plastics - charlotte North Carolina, united state of america
April 16, 2014
Q. Thank you, Chris Smith!
I am hoping you can lend me some expertise.
Am trying to convert a 58 gallon water tank to use for Sodium Hypochlorite or Calcium Hypochlorite bleach.
Have a polypropylene Banjo bulkhead at the base of the tank that is going to be plugged. Have heard that is bad idea, the SH will eat away the EPDM gasket, etc., and cause it to leak. Inadvisable to have any holes in tank other than on top, but I have a good tank, otherwise. Just has the hole near the bottom.
Will E6000 [←affil link] seal it? Will it last forever? <grin> The tank is for a low pressure roof and exterior cleaning delivery system (5 GPM).
It says on the E6000 package [←affil link] that it is not for polypropylene. Bulkhead and plug are threaded, too.
I apologize if this is not on subject, but this thread is where I got the idea of using this glue.
Any ideas?
Thank you for your time, hope you don't mind,
- Kennewick, Washington USA
March 7, 2015
Q. What is the cost of PVDF in general vs. cast iron?
If similar, this will be an easy sell for a difficult client who is having to replace their cast iron now.
- Atlanta Georgia
August 5, 2020
A. Hi Joe. There's no substitute for specifying exactly what you need and getting quotes for it, but PVDF is an 'exotic' plastic, far more expensive than PVC or CPVC. Even taking labor and handling costs for the much lighter materials into account, my bet is that the cost of PVDF isn't even in the same ballpark as cast iron. One chart I quickly perused suggests that the installed cost of 6" PVDF pipe is 11.33X that of CPVC.
Luck & Regards,
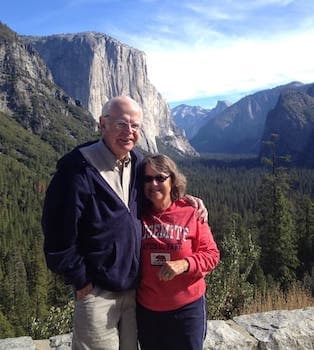
Ted Mooney, P.E. RET
Striving to live Aloha
finishing.com - Pine Beach, New Jersey
Q, A, or Comment on THIS thread -or- Start a NEW Thread