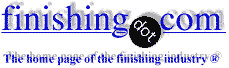
-----
Problems in powder coating of aluminum
Current question and answers:
September 17, 2020Q. Dear Sir,
I recently procured a metal fabricator to manufacture an aluminium staircase, balustrades and railings. The railings and balustrades were finished with Dulux Flouroset Powdercoating, which comes with a 35 year anti-corrosion warranty.
After the work was done, it later emerged that, prior to the Powdercoating treatment, the aluminium substrate had been sitting in the yard of the manufacturing plant for nearly a month and was delivered to the Powdercoaters in an oxidised state.
The Dulux approved Powedercoater whip blasted the metal prior to pretreatment and removed all of the visible signs of oxidisation, but no guarantee can be given that they were able to remove all traces of oxidisation. The Dulux warranty will not apply to the extent that any future corrosion is due to oxidisation or other contamination of the metal prior to Powdercoating.
I am now in discussions with the manufacturer about what is fair compensation for the risk of premature corrosion of the metal during the life of the warranty period due to these pre-treatment defects. The powdercoater estimates the risk at 20% to 30%.
Is is possible to get an expert to provide a more reasoned estimate of the risk without doing invasive testing?
- Hong Kong
A. Hi Christopher. Although readers are encouraged to contribute any thoughts they wish, a free expert opinion is an oxymoron, and no court or arbitrator would give it credence. An 'expert opinion' is one that has been offered by someone who has studied all available facts in detail and who has survived, to the judge's satisfaction, witness stand challenges by the other side as to their education, experience, reputation, and the applicability of their knowledge.
From my own experience as an expert in a number of cases in bygone days, I doubt that an expert would take this one on.
I would suggest documenting all available facts, taking any offered discount from any of those three parties, hoping for the best ... and then going back to Dulux 10, 20 or 30 years from now, if and when a problem develops. The odds of any given company even being in business 35 years from now seem very low to me anyway.
Luck & Regards,
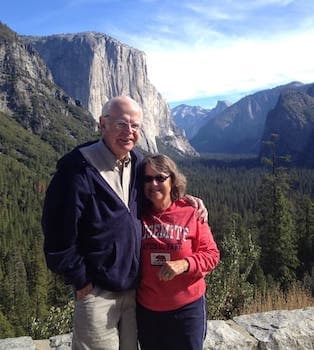
Ted Mooney, P.E. RET
Striving to live Aloha
finishing.com - Pine Beach, New Jersey
September 2020
⇩ Related postings, oldest first ⇩
Q. We do lots of aluminum work around salt water. Everything we do gets sandblasted and powder coated. We now are seeing corrosion forming under the powdercoat , blistering , and peeling .
We do use stainless steel hardware (screws , etc.)and we know that this is a bad mix but the only alternative is steel hardware which rust almost overnight. The blisters are not just around the screw areas though,it is all over.
Spots that are total covered will start to bubble leading me to believe this is a pre-finishing problem .I would appreciate any input on this .
Thanks,
Michael Calandroornamental fabricator - Alva, Florida, US
2004
A. We went through the same thing. Have now switched to electrostatic polyurethane top coat over primer and sandblast prep. We also had chalking problems after only a couple of years.
John Gambill- St. Petersburg, Florida, USA
2004
A. Your problem is definitely pretreatment, at least the bubbling and lack of adhesion. Aluminum must be chemically treated prior to powder coating to get any kind of outdoor performance at all. Look to a good chemical company to provide you with a fluoride bearing treatment and a reactive non-chrome final rinse. Then get clean rinse water and you're all set. If you don't have all the equipment for that consider jobbing the powder coating out to someone who does. It'll be cheaper in the long run.
As for the stainless fasteners, you're probably OK once you take care of the other problems. Hope that helps.
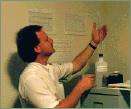
Jeff Watson
- Pearland, Texas
2004
A. I do agree with a friend that advises you to treat chemically the aluminium surface prior coating with powder coating, as you might believe that the surface of aluminium are very difficult to stick without opening/doing the pre treatment. might be you can try with a solution mix of hydrofluoric acid/55%, with comparison 2-4 kg of HF into 20 kg of water. fyi, I had been trying to eliminate galvanized aluminium with 5 to 20/HF to water,but be careful, ok
Daniel Herman S Suhendra,drs- Jakarta, Dki, Indonesia
2004
Q. Sir I have a powder coating plant and I regularly paint mild steel sheets. Now a job is to color on aluminum, and that comes out with bad quality, like edge breaking; please give me some information to develop the quality.
Joseph Vargheseemployee - India
August 2, 2010
Q. We are having a powder coating plant. Mostly we are doing for aluminium channels. While doing light colour, there is cloudy formation over the surface. Please give a solution to avoid this. We have checked water moisture is contaminated in powder, and we are having good branded gun and compressor with air dryer also.
BALA DEEPAKpowder coating plant - Tirupur, Tamilnadu, India
December 20, 2012
A. There's not enough information here to give any meaningful answer.
What is this formation? What does it look like? Is it raised above the coating, or a discolouration only? Is anything else affected? What pretreatment route?
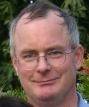
Geoff Crowley
Crithwood Ltd.
Westfield, Scotland, UK
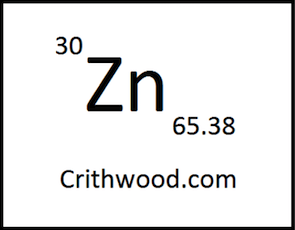
December 21, 2012
Q. Sir we are starting aluminium die-casting auto parts and we face the problem of pin holes and orange peel too. we used Henley's chemical for pretreatment (7 stage process). After PT preheat it for drying up to 150 °C and spray powder. While spraying, job temperature is more than room temperature. My question is: is this the root cause for pin holes and orange peel.
Rajendra Gatkal- Pune, Maharashtra, India.
February 8, 2018
Q. Hello, if I were to import aluminum machined components without any surface treatment at all (mill finish), will the journey over the ocean (approximately 3-4 weeks) for the parts to get to me pose a problem when I go to get them powder coated locally in the US?
James Chen- Seattle, Oregon
May 2, 2019

Q, A, or Comment on THIS thread -or- Start a NEW Thread