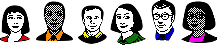
Metal finishing Q&As since 1989
-----
Electrodeposition of Tungsten or other Very Hard Material
Q. I am a researcher in Microsystems and am looking for a material which is hard and conductive which can be electroplated. Particularly I would be interested in tungsten if it is possible. Can anyone offer any input on this?
Also if anyone knows how to increase the stress in nickel electroplating the info would be gratefully received.
Michael CookeR&D - Durham, UK
2004
A. Hi Michael. Tungsten cannot be electroplated from a conventional aqueous bath, but that is not the only coating technology available. Chromium is probably one of the hardest electroplateable materials but maybe you already considered that one. Composite plating with diamond or other particles may be useful to you. Rhodium is hard, but extraordinarily expensive and perhaps not thick enough.
Chlorides should drive the stress in nickel electroplating through the roof.
Please tell us what you are trying to do. Thanks!
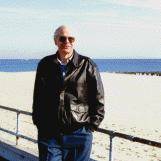
Ted Mooney, P.E.
Striving to live Aloha
finishing.com - Pine Beach, New Jersey
2004
2004
A. Stress in nickel can be induced by almost anything, but one surefire way of doing it is to add chloride. Sulphamate nickel has been designed to offer low stress deposits, but you can always use high sulphate and/or high chloride baths.
For hard materials, probably the hardest is hard chromium, although you can also get hard electroless nickel with a high phosphorus content. You certainly cannot electrodeposit pure tungsten, (although there are some claims you can) but you can deposit binary systems using tungsten and (say) chromium or other metals. If you want to deposit pure tungsten, try vacuum technology; this will also let you put down tungsten nitride, which has a hardness well in excess of 2,000 Hv. Perhaps you would like to tell a bit more about what you are doing?
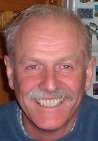
Trevor Crichton
R&D practical scientist
Chesham, Bucks, UK
A. I think that he is looking for sodium tungstannate, which is added to nickel plating solutions to increase the hardness. Twenty years ago, there were several articles and formulas in print. I am fairly sure that it is still being used in some brush plating solutions, with a very limited build up possible -- i.e., a cap coat.
James Watts- Navarre, Florida
2004
![]() ![]() ![]() |
September 13, 2013
A. Electroplating of Tungsten is quite simple actually. Ideally, the material should be bead blasted. - New Gloucester, Maine USA
Trevor, James, and myself assumed that Michael was inquiring about electroplating of tungsten onto a substrate of something else, whereas you have assumed he was inquiring about electroplating of something else onto a tungsten substrate :-) Regards, ![]() Ted Mooney, P.E. Striving to live Aloha finishing.com - Pine Beach, New Jersey September 2013 A. Ok Ted. My mistake. Sorry. ;-) Jeff Mills- New Gloucester, Maine, USA September 15, 2013 A. Hi, - Perth, WA Australia September 20, 2013 September 26, 2013
Regards, ![]() Ted Mooney, P.E. Striving to live Aloha finishing.com - Pine Beach, New Jersey |
A. Tungsten can be plated from a melt of sodium tungstate with a small addition of sodium pyrosulphate. Temperature 1650 °F
Bill Zweig- Vancouver, BC, Canada
September 23, 2013
Q. Hi All
I have a problem that would be solved if I could electrodeposit W on Copper.
But perhaps someone could guide me to an alternative solution please?
I need to have a small bead of mercury spinning in a channel made of copper with a coating of some metal that won't form an amalgam or degrade the mercury and have similar electrical properties to Tungsten and Copper.
Any ideas perhaps?
Kind Regards
- Pretoria, Gauteng, South Africa
January 30, 2014
A. The electrical properties of nickel are not too far from tungsten. Nickel can be easily plated on copper, and, I believe, will not amalgamate with mercury at ambient temperatures.
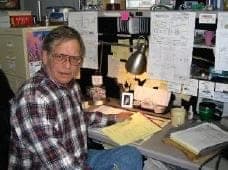
Jeffrey Holmes, CEF
Spartanburg, South Carolina
January 30, 2014
Would an electrodeposit of Ni-P-W on Cu prevent the formation of an amalgam if in permanent contact with Mercury?
February 10, 2014Q. Hi All
I need to have a bead of Hg spinning in a Cu channel plated with some material that has similar electrical resistivity to Cu [ (20 °C) 16.78 (ed. note: units unintelligible) ] but that will not form an amalgam with, or degrade the Mercury.
Tungsten is a candidate (52.8 [ed. note: units unintelligible]) but it's difficult to deposit on its own in a complicated molten salt process beyond my cost target. Therefore co-deposit appears the only viable option, but I'm worried about the Ni in the alloy being amalgamated over time.
If so, would the P-W keep its structure? If it does, would it be possible to "pickle" the Ni-P-W and then use fresh Hg for the rest of the application?
The Hg and plated Cu channel can be operated in an inert gas environment if needed and I'm looking for a 10 year operational life.
Possible answers are pay-walled to me.
Thanks
- Pretoria, Gauteng, South Africa
"Electroless Plating"
by Mallory & Hajdu
on
AbeBooks
or
eBay
or
Amazon
(affil links)
A. Hi Trenton. Access to Finishing.com is free, but if you have found papers on another site which require payment to view, we can't help with that.
You can do an electroless deposit of Ni-P-W alloy with up to 20% tungsten according to Mallory & Hajdu .
Gawrilov's Gawrilov's Chemical (Electroless) Nickel Plating
[affil link
on Amazon,
...
on AbeBooks] very briefly mentions electroless Ni-P-W alloys. Brenner's "Electrodeposition of Alloys" has a whole chapter on tungsten alloys, but that 1400-page tome is so exhaustive that I don't have the necessary several hours to study it and summarize :-(
Iron is notable for not forming amalgams with mercury. Could the copper be plated with iron, kept in an inert gas environment, and maintain low enough resistance to convey the electricity to the copper channel?
Regards,
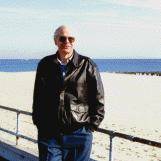
Ted Mooney, P.E.
Striving to live Aloha
finishing.com - Pine Beach, New Jersey
February 2014
February 11, 2014
Hi Jeffrey
I've been advised that only Iron and Tungsten are not amalgamated, thank you for your reply.
Hi Ted
Paywalled not by finishing.com but by other technical paper repositories, and I'm not asking for help to circumvent that, but perhaps for a solution to my problem from someone with that knowledge.
I'm going to try Ni-P-W on Cu and pickle that in Hg to see if the Ni is amalgamated out the alloy. The process is cheap. Might also try some Moly.
The resistivity of Iron is too high.
Another option for me (and by the look of things, the best) is to try CVD Graphene on Cu, but once more, I cannot find any info on the interaction between the two.
Thank you for your reply.
Kind Regards
- Pretoria, Gauteng, South Africa
A. I believe nickel and or its salts are capable of amalgamation with Hg. Especially as it is very similar and closely related to noble metals it is highly likely that it will amalgamate. I seem to remember that some noble metals will not amalgamate. Perhaps palladium, rhodium or platinum but I don't have a reference.
David BeleskiFormer machinist - Gainesville Florida
April 9, 2022
Electroless plating of tungsten onto alumina
Q. Can tungsten be plated on alumina? Electroless or other means.
Thank you!
- Montreal, Qc, Canada
July 22, 2015
A. Hi Jean. I think a PVD vacuum process would be necessary. I'm not aware of electroless tungsten and strongly doubt that it is possible (but see the earlier entries about alloys). Good luck.
Regards,
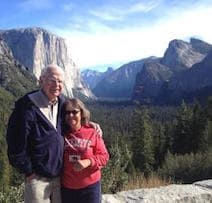
Ted Mooney, P.E. RET
Striving to live Aloha
finishing.com - Pine Beach, New Jersey
July 2015
Q. We have a China supplier who is plating 4140 steel with tungsten. They seem to struggle with achieving hardness levels (750) we desire. Please comment on the process.
Jerry priestb.k. thorpe co - long beach, California
December 30, 2016
December 2016
? Hi Jerry. Can you tell us anything about what they are doing -- like thickness, purity, method of application? What the component is so we can visualize whether line of sight methods are useable, the criticality of thickness distribution, etc.? Maybe it would be ideal if the shop doing the work described the problem? Thanks.
Regards,
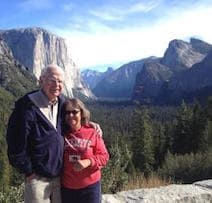
Ted Mooney, P.E. RET
Striving to live Aloha
finishing.com - Pine Beach, New Jersey
![]() |
A. Hi Jerry ![]() Geoff Smith Hampshire, England January 1, 2017 A. Jean, ![]() Blake Kneedler Feather Hollow Eng. - Stockton, California January 1, 2017 Q. As comment this is our second supplier of tungsten coated rods. First supplier is limited on size range hence we move to a new supplier. You do not get "straight" answers from the Chinese suppliers. Perhaps language or simply they figure you do not need the detail or information. They struggle with achieving thickness and tensile. Previous supplier polished the tungsten surface and this seemed to work harden the material to acceptable level.
b.k. thorpe co - long beach, California December 30, 2016 |
Q. Picking again the interesting second question of Michael Cooke made in 2004, this may sound like an odd request but if I wanted (within the restriction of commonly/easily available materials) not only to maximize stresses and hardness in an otherwise standard nickel plating as originally asked, but also roughness and microporosity (or preferably nanoporosity) what would I generally have to do? I realize this would be almost the exact opposite of what a good electroplating would normally be. Actually I want a "bad", but durable plating.
Since it was asked before, what I plan to do is obtaining a material that will be able to trap microbubbles of hydrogen without deforming in electrolytic experiments, not really just a surface finish. For disclosure, I'm still in the planning stages and I'm very new to the subject of electroplating.
Regards,
- Rome, Italy
February 24, 2017
A. Hi Bill. Easiest would probably be to just plate at too high a current density, generating a "burnt" deposit. Good luck.
Regards,
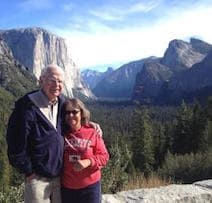
Ted Mooney, P.E. RET
Striving to live Aloha
finishing.com - Pine Beach, New Jersey
Q. Why tungsten cannot be electrodeposited alone?
Lava KumarARCI - Hyderabad,Telangana, India
August 19, 2017
Q. Why is it difficult to electrodeposit tungsten alone? Why a codeposit of tungsten is preferred with Ni and other metals but not alone?
Thanks,
Ron
- Beawar, Rajasthan, India
August 20, 2017
"Electrodeposition of alloys: principles & Practice"
by Abner Brenner
on
AbeBooks
or
eBay
or
Amazon
(affil links)
A. Hi Lava. Hi Ron. Brenner's "Electrodeposition of Alloys".
has a 66-page chapter on tungsten alloy deposition, including about 10 pages just addressing a number of hypotheses about why tungsten cannot be plated from an aqueous or organic bath but alloys can, especially with nickel or iron. It's an unsolved mystery so far.
Regards,
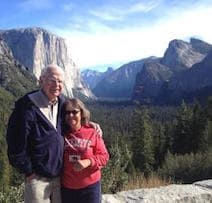
Ted Mooney, P.E. RET
Striving to live Aloha
finishing.com - Pine Beach, New Jersey
August 2017
A. Electroplating of tungsten from water bath:
https://sci-hub.tw/10.1149/1.3497829
Fink, C. G., & Jones, F. L. (1931). The Electrodeposition of Tungsten from Aqueous Solutions. Transactions of The Electrochemical Society, 59(1), 461. doi:10.1149/1.3497829
CEITEC VUT - Brno, CZ
November 12, 2019
Hi Pavel. Thanks for the reference, but it was discredited. Fink & Jones were unable to plate any thicker than a fraction of a micron, and later researchers have repeatedly confirmed that it was a tungsten-iron alloy rather than tungsten.
Brenner's "Electrodeposition of Alloys" has the very interesting story of this paper, and does credit them with the first progress towards tungsten alloy plating .
Regards,
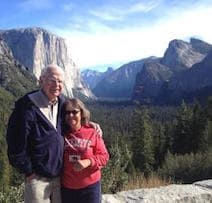
Ted Mooney, P.E. RET
Striving to live Aloha
finishing.com - Pine Beach, New Jersey
November 2019
A. Hello Ted,
I read this paper in fast way, noticed the problem of thickness and pits. Maybe there is some new paper with improved method, like addition of some surfactant or other stuff like PEG which can help, not sure.
I got a copy of the plating of alloys book, it was very useful and inspired me to my last publication (Co-deposition of gold amalgam; DOI: 10.1016/j.snb.2018.11.127)
Have a nice day!
CEITEC VUT - Brno CZ
November 12, 2019
November 2019
Hi again, Pavel. There may have been progress since Brenner (pub. 1963). Maybe try searching scholar.google.com and surfacequery.com
Luck & Regards,
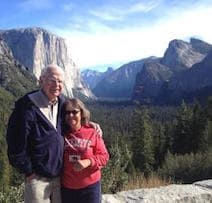
Ted Mooney, P.E. RET
Striving to live Aloha
finishing.com - Pine Beach, New Jersey
Q, A, or Comment on THIS thread -or- Start a NEW Thread