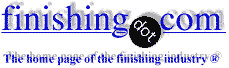
-----
Brown oxide vs. black oxide, immersion tin processes for PCBs / PWBs
Q. We are experiencing oxide 'smearing' on circuit boards after the black oxide plating process. Does anyone know if the reason is due to something in the plating line or if processes post-plating of the boards causes this?
Thank you,
- Tempe, Arizona, USA
2001
A. I'm not sure what you mean by smearing of black oxide. Does this occur before or after lamination? I've seen some interesting things happen to oxides on some complex boards, but I would not know if what you're seeing is the same thing. What I saw was really part number specific.
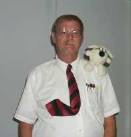
James Totter, CEF
- Tallahassee, Florida
2001
Q. Thank you for your response James.
The problem occurs after the oxide process during lamination. The oxide appears to 'run', resembling paint that smears if it's rewetted.
I've noticed some particulate matter in our oxide module and have requested the filters be changed on a weekly basis. Might this be the source of this problem?
- Tempe, Arizona
2001
A. What I saw could be traced to an interaction with moisture which apparently formed acids during the press cycle. Make sure your cores are dry and check your press cycle, especially the ramp. You might try a low temperature vacuum bake just prior to applying pressure.
James Totter- Largo, Florida
2001
Immersion tin vs. black oxide
Q. Does anybody have a study or experience in using immersion white tin to take the place of brown oxide for inner layers?
Frank Yijun Lan- ShenZhen, Guangdong, China mainland
2001
A. I have no experience but heard that it works fine.
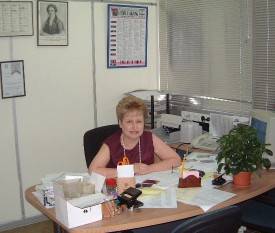

Sara Michaeli
Tel-Aviv-Yafo, Israel
2001
A. Immersion tin is an excellent treatment for inner layers. It can eliminate several problems with conventional oxide treatments. The only concerns are: Ionic contamination of exposed substrate needs to be removed and the tin layer should be quite thin but solid.
John EddyElectronics Manufacturing - Canada
2004
Difference between black oxide process and natural oxidation of copper
Q. I am a trainee in a PCB manufacturing company. I will be having my presentation regarding the purpose of the black oxide (Cupric Oxide) in the lamination process. My question is "What's the difference of the having the natural oxidation of copper and the black oxide process?" "Why do we need a crystalline structure?"
Rodjel CuebillasTechnical Specialist (trainee) in PCB industry - Manila, Philippines
2003
A. The purpose of black oxide on Cu in the PCB process is to provide a rough surface in preparation for the lamination process. If you peel-back the foil copper on a PCB you will find that the underside of the copper foil is rougher than the top side. Under a microscope or SEM you will see that there is a rough or dendritic surface. Black oxide coatings create much the same roughness on a smooth copper surface. This enables the PCB layer to laminate more effectively. Black oxide also comes in brown and red.
Bill Watson- Santa Clara, California, USA
2003
A. The response above is appropriate for normal or "Shiny" foil.
FR-4 Laminate is also sold with Reverse-Treat (RSTF) or Double-Treat (DSTF) foils which have the rough/tooth side out, making the black oxide finish unnecessary. Peel strengths are higher than when black oxide is used, and much higher than those obtained using the newer oxide replacements (which have a bad name among some OEMs).
If your management is open to it, suggest a side-by-side comparison using the reverse-treat vs the black oxide treated layers. You may be able to get rid of the black oxide finish altogether. Several PCB manufacturers have switched over from BO to RSTF/DSTF and have yield increased by 50% or more.
PCBs - Salt Lake City, Utah, USA
2003
A. The simple answer is the black oxide creates a rough topography that allows better grip or adhesion between the layers of the PCB when pressed. I'm not an engineer and don't play one on TV but it is basically the same principal of sanding PVC piping on the connecting ends before gluing them together. Better topography better adhesion. Best of luck.
JB
- Portland, Oregon
August 18, 2010
Remove copper from a brown oxide bath
Q. Dear all,
I would like to know any existing method that can precipitate or plate out the copper ion in a brown oxide bath. The copper ion concentration is around 5000 ppm. I try to apply the current directly to the bath but only gas bubbles are evolved. I believe it is the decomposition of hydrogen peroxide. When I try to get rid of all the peroxide and apply the current again, only Ni, Fe & Cr are plated out. Any comments?
Samuel
Plate shop - HK
2007
Difference between black oxide and brown oxide treatments for printed circuit boards?
Q. What is the difference between black and brown oxide chemical treatments? Many manufacturers are moving away from black oxide because of the hazardous waste.
Russell HaeberleConsultant - Auburn Hills Michigan
February 27, 2015
Q, A, or Comment on THIS thread -or- Start a NEW Thread