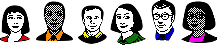
Metal finishing Q&As since 1989
-----
Material of construction for Nitric Acid Passivation Tanks
Q. I have been asked to provide the proper equipment for Passivating of 300 series Stainless Steel. The passivate solution is Nitric acid and run at 150 °F. We would like to bulk passivate and was wondering what material of construction you would recommend for the bulk processing of these parts. I thought there might be a possible problem having two dissimilar metals in the Passivate. Do you have any suggestions? Thanks.
N. Corriere1995
A. Hi Nick. Like they say, coupon testing is the only way to know for sure, because there can always be some little idiosyncrasy you missed. But I'd be very surprised if 316SS didn't fill the bill perfectly in all regards.
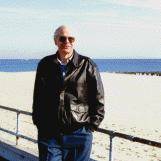
Ted Mooney, P.E.
Striving to live Aloha
finishing.com - Pine Beach, New Jersey
1995
A. We always used polypropylene for tanks and baskets. Thanks,
Ron Landretteplating equipment supplier - Bristol, Connecticut
1995
You could be right, Ron, but I don't feel it's the best stuff for the tanks because the passivating solution is a very strong oxidizing agent; I'm still pretty sure that 316 stainless steel is best. A third opinion would be really welcome here!
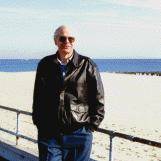
Ted Mooney, P.E.
Striving to live Aloha
finishing.com - Pine Beach, New Jersey
1995
Multiple threads merged: please forgive chronology errors :-)
Q. We've picked our passivation process. We will be performing Nitric Acid passivation. We have some spare tanks. One is a stainless steel and one is a lead lined mild steel. Plus a Deionized water rinse tank. Would we be best off inserting a plastic liner? My ancient chemistry tells me all nitrates are soluble therefore all metal tanks would have a finite life. Am I getting close? Lip extraction is already fitted. Is there anything really obvious I am missing.
Ciaron Murphyaerospace repair - Blackwood, Gwent, UK
2003
A. Your old chemistry knowledge is correct as far as all nitrates being soluble in water, but that fact has nothing to do with the life expectancy of a tank containing nitric acid. You need to use stainless steel, but not all SS is created equal. If you do not know the exact grade and method of manufacture of your existing tank, I would not risk using it. Contact a reputable tank manufacturer and have a new one made. I think that they will tell you that the best choice is 316L (3/16" thick would be good). The tank should be welded inside and out (w/316L rod) and should be equipped with appropriate girth supports.

Jon Barrows, MSF, EHSSC
GOAD Company

Independence, Missouri

2003
Q. I realize this is a very old thread, but I came upon it as I was researching another question related to nitric acid.
I, too, would recommend 316L stainless steel with full penetration welds. I agree with Mr. Mooney, though, that the use of coupon testing (when the opportunity exists) is best.
Have PP tanks in this application, as stated in the comment above, been proven to be acceptable? The information that I have indicates that PP would not be an acceptable long term tank material in this application.
Thanks!
- Kansas City, Missouri USA
August 12, 2016
A. Long term, PP is not a good material for nitric acid.
My choice for endurance and cost is rotationally molded PE. It is more flexible than PP, so it needs good reinforcing. I have used oil based painted 2x4s for several applications.
- Navarre, Florida
August 12, 2016
A. Angela
We have used polypropylene with success for 20-25% nitric at 120-130 °F. 316L for all other solutions (those with sodium dichromate or at higher concentrations).
- Green Mountain Falls, Colorado
August 12, 2016
Q. If 316 stainless is used to create a passivation tank, is it necessary to ground the tank if there is no heat or movement involved. The tank contains nitric at 20% and sodium dichromate at 2%.
Sincerely,
- Rincon, Georgia USA
October 3, 2016
A. Hi Micheline. I first entered this industry in the days when the practice was to electrically insulate tanks from the ground with PVC tank lining material. But I'm thinking that that old practice was because of one rectifier used on multiple tanks, or the tank itself used as anode or cathode for electrocleaning or anodizing, etc.
Although it may not be "necessary", it seems to me that for safety all large metallic objects should be at least casually grounded when practical. Picture what could happen if an extension cord with a cut in the insulation was draped over a metal tank. Further, while you may not have earthquake regulations where you are, such codes require bolting the tanks down anyway (such codes are not primarily about what happens should the earth split open right under your shop, but what happens if the powerful vibrations from a quake even miles away are able to shake the tanks off their supports).
Regards,
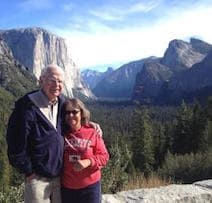
Ted Mooney, P.E. RET
Striving to live Aloha
finishing.com - Pine Beach, New Jersey
April 2017
Q, A, or Comment on THIS thread -or- Start a NEW Thread