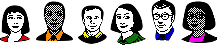
Metal finishing Q&As since 1989
-----
E-coating vs. Powder Coating vs. E-coating Plus Powder Coating
Q. I am a paint technologist and wanted to know the difference between An electrodeposition coat vis-a-vis powder coatings. Which one is superior in terms of following.
1. Impact Resistance.
2. Salt Spray Resistance (ASTM B117)
3. QUV Testings :- 313 Nm lamp , UVB light 300 Hrs. total test duration having 4 Hrs. of UV AND 4 Hrs. of the condensation cycles at regular intervals. Any specific cost saving due to the process.
Regards,
VAIBHAV KULKARNI- MUMBAI, MAHARASHTRA, INDIA
2003
2003
A. Theoretically, they are both electrodepositions. Both achieve the same end - an organic coating on a metal substrate. Only the method of transferring the organic layer is different. In powder coating the powder particles are charged. In E-coat the liquid is charged and an electrochemical reaction deposits a film. Both have to be baked for crosslinking. Both are available in epoxies and PUs. Both have their own advantages and disadvantages.
To compare the parameters you will need to match the technologies. Epoxy or PU. That is fairly complex to be answered here.
Gurvin SinghMohali, Punjab, India
Multiple threads merged: please forgive chronology errors :-)
Powder coater losing huge contract to e-coating
Q. We are faced with losing 30 million dollars in sales due to competitor quoting finishing the components in lower cost e-coat vs. our current powder coating. We manufacture and install commercial vehicle cargo interiors. Our components will be used in everything from Telecommunication to heavy construction and the finish needs to stand up to the equipment being placed on and off our powder coated shelves and components. We feel by powder coating our components vs. e-coating it gives a more durable surface and longer finish life. Does anyone have any test or study information where e-coat has been tested against powder coating? We are using a non UV-resistant polyester-epoxy powder coating.
J. Michael C [last name deleted for privacy by Editor]1st tier automotive, point of purchase displays - Atlanta, Georgia
2003
2003
A. Hopefully, you will get some help here ... and you can contact the Powder Coating Institute and vendors such as Tiger Drylac and Martex to see what literature they can offer, Michael.
But personally if I had 30 million dollars in sales at risk in these circumstances, I wouldn't consider those options for a heartbeat until I hadn't already retained a world-class powder coating consultant to prepare a report tailored to my exact product line. Best of luck.
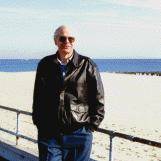
Ted Mooney, P.E.
Striving to live Aloha
finishing.com - Pine Beach, New Jersey
by Electrocoat Association
on AbeBooks
or eBay
or
Amazon
(affil links)
Q. What is "e-coating" as mentioned in your mail ... thanks.
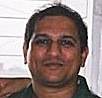
Atul Bhide
jobshop / applicator - Mumbai, India
2003
May , 2007
A. Hello, Atul. E-coating means electrocoating -- sometimes alternately called electropainting, electrophoretic lacquering, CED (cathodic electrodeposition) and so on. The parts are immersed in an electrified tank with a special cationic or anionic paint which deposits on the parts as a result of electrochemical oxidation or reduction analogous to electroplating.
An advantage is full and even coverage -- the deposited paint becomes an insulator, diverting the electrical current to spots where paint hasn't yet deposited). Another advantage is that the coating is quite thin compared to other organic coatings. But that thinness might be a mark against it for durability and corrosion resistance. The two processes can be combined, i.e., electrocoating followed by powder coating.
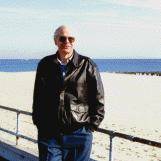
Ted Mooney, P.E.
Striving to live Aloha
finishing.com - Pine Beach, New Jersey
Q. Advantages of electrocoating over powder coating.
praveen kumaremployee - Chennai,Tamil nadu, India
May 6, 2009
August 31, 2010
A. Hi, Praveen. We appended your inquiry to a thread which may offer some general insights. If you provide a couple of paragraphs of additional detail about your components and their application, readers may be able to provide additional info tailored to your particular situation. Some of our readers tell us they will not attempt to answer abstract questions, and they refuse to spend more time/words on an answer than the inquirer spent on their question ... so your 6-word dependent clause won't be a promising start. Please get back to us with a few paragraphs describing your situation. Thanks! :-)
Regards,
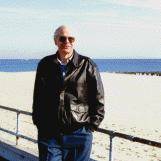
Ted Mooney, P.E.
Striving to live Aloha
finishing.com - Pine Beach, New Jersey
Best finish for aluminum outdoor luminaire
Q. Hello all,
E-coat vs. powder coat for an outdoor luminaire? Trying to address the finish on a diecast aluminum outdoor luminaire. Current finish is anodize with powder coat over the top. VERY expensive. Any suggestions on a finish that will withstand weathering (looking for 10 year warranty)?
Consultant to OEM - Wauwatosa, Wisconsin
January 24, 2012
A. Hi David.
Anodizing diecast aluminum and following it with powder coating sounds like a good but fairly unusual and (as you mention) expensive finish. I suspect that e-coat PLUS powder coat will be less expensive and more robust. Please remember, however, that pretreatment is a major part of finishing, so it's not just an issue of specifying the final finish, but either specifying the pretreatment or finding competent applicators who supply good pretreatment as a matter of course. Good luck.
Regards,
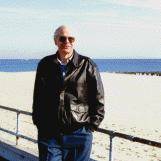
Ted Mooney, P.E.
Striving to live Aloha
finishing.com - Pine Beach, New Jersey
January 24, 2012
A. A possible even cheaper process whilst still retaining 10 years protection would be zirconium phosphate followed by architectural polyester powder top coat.
Terry HicklingBirmingham, United Kingdom
January 25, 2012
July 2014
I like Terry's suggestion providing that the geometry of the luminaire is sufficiently simple that full coverage can be guaranteed. An advantage of your present anodizing process, which will be maintained when switching to electrocoating, is complete coverage because both processes are insulative, driving the current to any thin or uncoated area.
Regards,
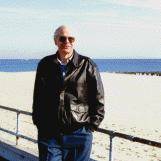
Ted Mooney, P.E.
Striving to live Aloha
finishing.com - Pine Beach, New Jersey
E-coating for swimming pool filters
Q. Hi all,
We need to protect some tubular heaters that are going to be used in a swimming pool environment (fitted at high level) and have suggested the use of e-coat. The tubular heaters are manufactured from mild steel.
Our client has asked for some data to support the choice of e-coat. Can anyone point me in the right direction?
regards
Gary
- Daventry, UK
February 15, 2012
A. Hi, Gary. We can tell you that all automobiles around the world are e-coated before painting, so that should be some evidence of its value. PPG may have case studies. But I think you will find that most E-coating is not UV resistant, so it must be followed with something. A polyurethane top coat is common, but I think polyester powder coating would be better.
Again, the primary thing that E-coating offers, that painting and powder coating don't, is thinness and 100 percent coverage. Good luck.
Regards,
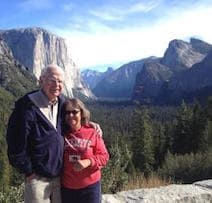
Ted Mooney, P.E. RET
Striving to live Aloha
finishing.com - Pine Beach, New Jersey
February 14, 2012
Q. I am in the beginning stages of restoring an old pick up truck. I'm having the frame repaired and reinforced, being a midwestern truck, from the Salt n' Rust Belt... I want to take whatever steps I can to prevent the frame from being ruined again. From what I have been reading, it would appear that having the frame cleaned, then e-coated, then powder coated is the way to go? I want the best protection possible - whatever method it might entail. Comments saying E-coating is able to offer 100% coverage, but is thin... tend to concern me. Powder coating is a thicker more durable process correct? But is not able to offer 100% coverage... but the two together - would that be good enough? Opinion, thoughts, suggestions?
Thank you!
- Stevens Point, Wisconsin, USA
February 15, 2012
February 16, 2012
A. Hi Tom. Yes, the two coatings are compatible, and electrocoating followed by powder coating is a common and very robust system.
Regards,
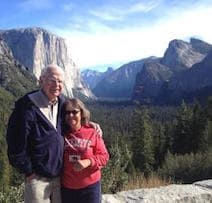
Ted Mooney, P.E. RET
Striving to live Aloha
finishing.com - Pine Beach, New Jersey
Need 1300-1400 hours salt spray resistance with powder coating
Q. Sir, can we increase Salt Spray resistance by using super quality (durable) powder? We have requirement of 1300 to 1400 Hrs SST. Another system, CED coating, is available but can we use only powder to increase SST hrs?
Jeetendra Borse- Ahmednagar, Maharashtra, India
July 8, 2014
A. Hi Jeetendra. If the shape of the parts is simple enough that you can be assured of full coverage, with no pinholes or thin spots, and you have a robust pretreatment system like zinc phosphate, I think you should be able to get those hours from powder coating.
Regards,
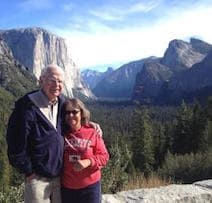
Ted Mooney, P.E. RET
Striving to live Aloha
finishing.com - Pine Beach, New Jersey
July 2014
Powder Coating over CED Coating Fails Impact Test
Q. Hi
I would like to know the reasons why a component would fail in the Impact test for powder coating done over CED coating.
We have been doing CED for more than a decade and are facing this problem just lately for only one of our customers who get their jobs powder coated after CED.
All other parameters for CED like SST, Adhesion, etc. are Okay and there is no change in the process but we are getting this problem only after the powder coating is done over CED.
Please help any suggestion/comment will be extremely useful to pin-point the exact problem.
Thanks,
plating shop owner - PUNE, MAHARASHTRA, India
February 25, 2015
A. Check the cure schedule of the powdercoater.
Perhaps there is an over-bake issue?
Hope this helps,
Bill
Trainer - Newcastle, NSW Australia
March 12, 2015
A. Bake your E D coated coated parts at higher temperature than powder coating. This will solve your problem for sure.
Avinash Vidhate- Naik, Maharashtra, India
April 1, 2015
(you are on the 1st page of the thread) Next page >
Q, A, or Comment on THIS thread -or- Start a NEW Thread